How to Optimize 3D Printing
How to Optimize 3D Printing
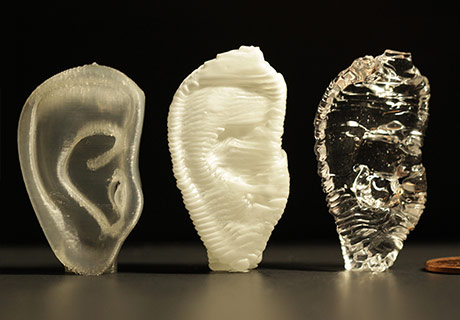
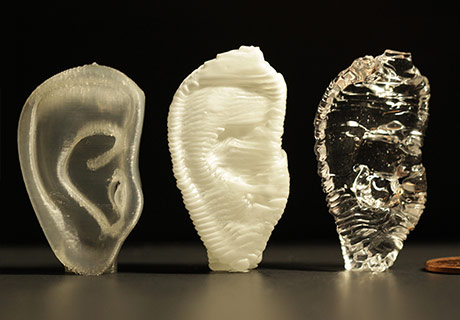
Additive manufacturing and 3D printing are not always as easy as they sound. One of the biggest challenges in the 3D-printing of complex or high-performance parts is optimizing the large number of process parameters that are required for a successful printing. This is especially true when using soft, deformable materials or liquid-like resins that require experimental printing methods.
For example, standard materials typically have five to ten main print parameters. Exploring five levels for each parameter can result in millions of possible combinations of settings to print. The combinations are even more challenging when exploring an experimental material whose print characteristics are unknown. For example, if the experimental material has 20 print parameters explored to five levels, the researchers can have trillions of combinations of print settings to consider.
To ease some of this burden, researchers at Carnegie Mellon University have developed what they call their “expert-guided optimization (EGO) strategy.” It combines expert judgment with an optimization algorithm to find the best combination of parameters to 3D-print a part, saving time and reducing the number of iterations needed.
For You: Top 6 Innovations in 3D Printing
How EGO Works
Sara Abdollahi, an engineering student and Ph.D. candidate, was trying to 3D-print a patient-specific, soft sensor for a wearable pulse oximeter as part of her research project. She wanted to find a way to track the many parameters that she was manipulating until she produced a quality print. Abdollahi built a spreadsheet and recorded the changes she made to all the parameters, eventually resulting in a detailed data set.
“Even though many of the prints had low-quality or were just plain failures, I could refer back to the parameters I had used to avoid making the same mistakes in subsequent iterations,” she says.
Abdollahi collaborated with Alex Davis, assistant professor of engineering and public policy, to figure out a way to use the data to make smarter decisions regarding parameters for 3D printing soft material. They ultimately developed the EGO strategy that factors “expert judgement” into the decision-making process.
"The purpose of EGO is to create an effective search algorithm that explicitly combines both expert knowledge and traditional search algorithms," Davis says. "Typically we think of machine learning being useful for big data, but EGO works in situations when we have little or no data and need to rely on expert judgment, then through a combination of search algorithms and the expert's knowledge, effectively transition from small to big data."
“Perhaps the most innovative aspect of this work for an engineer is the incorporation of expert intervention, a concept borrowed from the field of decision science, in optimizing a manufacturing process,” Abdollahi adds. “In some sense, the approach is akin to using Bayesian statistics to solve an optimization problem with the expert information serving as the prior distribution.”
EGO was developed for streamlining and optimizing the 3D printing of liquid polydimethylsiloxane elastomer resin. PDMS is often used in wearable sensors and medical devices. For this work, the researchers used a printing method called freeform reversible embedding (FRE), in which soft, delicate materials are printed within a supportive gel bath.
EGO consists of three steps:
- Expert screening to select the initial parameter space, factors, and factor levels, and create the boundaries for the algorithm search.
- Activating a hill-climbing algorithm to search within those boundaries, resulting in a "local optimum" combination of the best parameters.
- More expert decision-making to try new factors or new parameters within the boundaries to improve on the “local optimum solution. The process iterates until an improved solution is found.
The team applied the algorithm to two calibration objects, a hollow cylinder and a five-sided hollow cube, that were evaluated based on a multi-factor scoring system. The optimum print settings were then used to print complex PDMS and epoxy 3D objects, including a twisted vase, water drop, toe, and ear, at a level of detail and fidelity previously not obtained.
Future Possibilities
EGO is well-suited to optimize 3D printing across a wide variety of techniques, including fused deposition modeling, stereolithography, and powder bed-based AM processes. It also has potential as a systematic for discovering the key parameters that yield reproducible, high-quality, novel materials.
“For example, for the five-sided cube, we identified print orientation to be critically important and it enabled an increase in the score from 15 to 20,” Abdollahi says.“In addition, it shows how leveraging the expert to jump to a new parameter space is unique to EGO as compared to other optimization methods, and can provide major improvements to the fidelity of 3D-printed parts.”
Although Abdollahi won’t make any predictions about how EGO will be used in the future, she hopes to “see it in areas that I had not considered before because, in a broad sense, EGO embraces the interweaving of human and machine input to reach a common goal. I would like to see EGO applied to other manufacturing processes altogether and to help optimize systems that are not yet well understood, and for which little information is available.”
Mark Crawford is an independent writer.
Read More:
Safety and Efficiency, Brick by Brick
Ultrasound Patch Monitors Critical Components
3D Printing Trains Bomb-Sniffing Dogs
The purpose of EGO is to create an effective search algorithm that explicitly combines both expert knowledge and traditional search algorithms. Prof. Alex Davis, Carnegie Mellon University
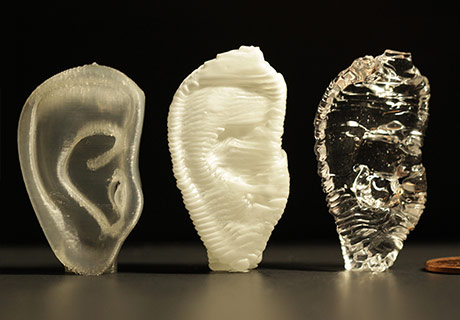
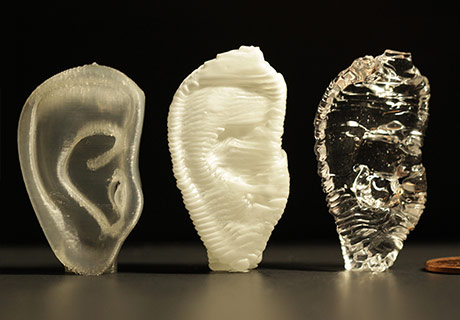