Innovative 3D Printer Could Solve Big Problem
Innovative 3D Printer Could Solve Big Problem
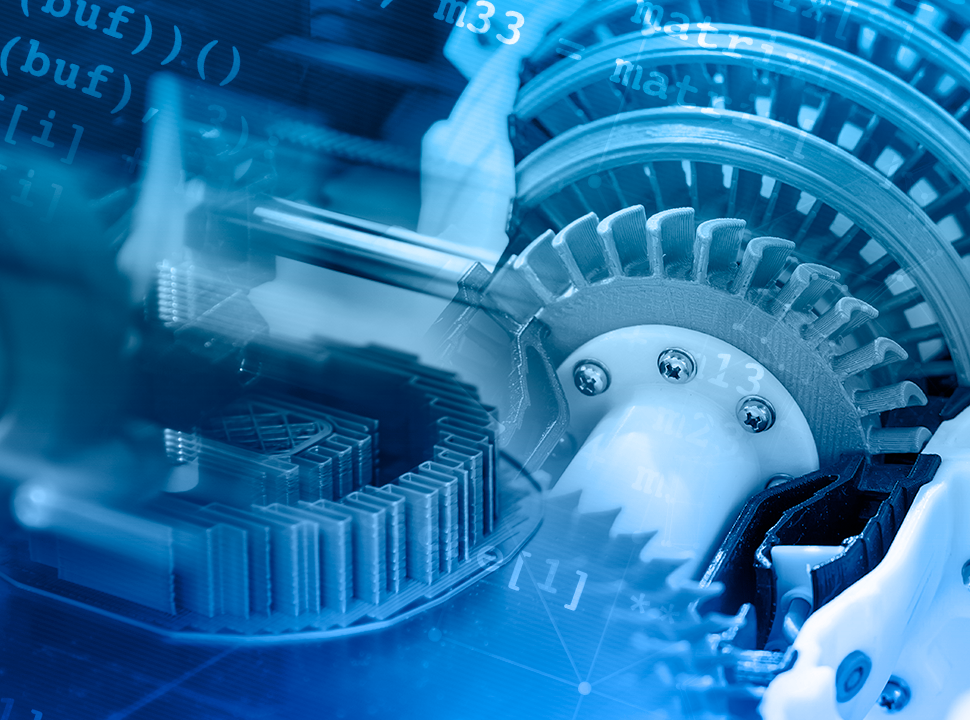
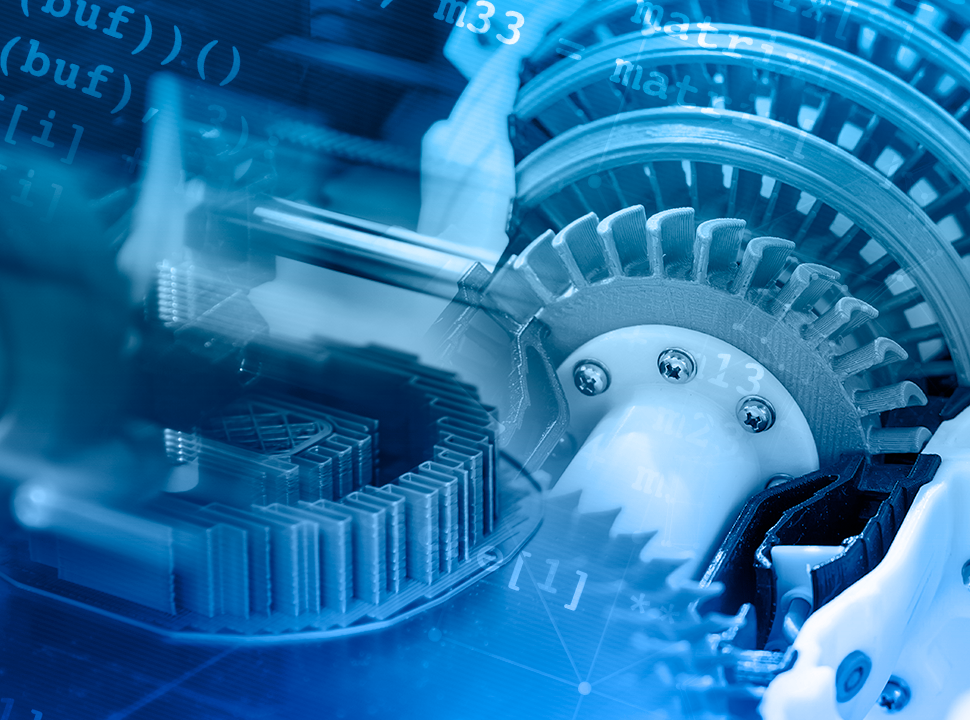
Small-diameter extruder nozzles typically print objects with much higher resolution than the bigger nozzles; however, they deposit material too slowly to be cost-effective – until now.
Large-format 3D printers continue to pump out bigger objects—boats, jet airplane wings, huge molds, even houses—at faster speeds. But size and speed have their drawbacks. The bigger the 3D-printer nozzle, the more ridges and other defects that must be removed from the object during post-production, a costly problem called throughput resolution tradeoff.
Students at Rutgers School of Engineering have come up with a new system they say will decrease those imperfections and pave the way for 3D printing big, complex parts made from thermoplastics at a fraction of the cost of current large-format methods. The researchers outline their new approach, called multiplex fused filament fabrication (MF3), in the August edition of Additive Manufacturing.
Small-diameter extruder nozzles typically print objects with much higher resolution than the bigger nozzles used on large format printers. Small nozzles, however, deposit material too slowly to cost-effectively print big objects. But what if a series of those smaller nozzles replaced the large single nozzle to quickly deposit the molten plastic at high resolution?
Read On: Advancing Additive Manufacturing in Aerospace
That’s the concept behind the new research. MF3 uses a single gantry (the frame or arm that supports the printer head as it moves around) to print single or multiple parts simultaneously using several extruders. To achieve high resolution and efficiency, the researchers custom designed slicer software (made up of the code that maps an object into the slices or layers to be printed) to control the material deposition of each nozzle. They can turn the deposition from each nozzle on or off at any time. That allows each nozzle to print distinct 3D geometries or its own individual part.
“This saves time because when you use multiple smaller nozzles you can accumulate the same throughput as one very large nozzle but get the high resolution,” said Jeremy Cleeman, a mechanical engineer, graduate student researcher, and lead author of the study. “You save a lot of time on the backend, which is where you’d have to do all of that machining.”
The time saved varies with each printed part. But from its research, the team found the area of material that does not have to be machined from the finished object is the difference between the nozzle diameters squared. In the case of an 8-mm nozzle compared to a 2-mm nozzle, the difference would be 36. “It’s a significant factor,” Cleeman said.
Recommended for You: Is 3D Printing the Future of Manufacturing?
The goal of the MF3 system is not to print faster than today’s large-format printers, since they are already very fast, but to save time on the machining side. Based on a series of simple throughput calculations, the researchers determined that 36 2-mm nozzles attached to the gantry can equal the speed of one 8-mm nozzle. “We can keep up with the big-area machines at a much better resolution,” Cleeman said.
Another challenge was trying to better understand and improve filament retraction and redeposition. With most 3D printers, the gantry stops moving, the material is retracted, and the printer head then moves to its next position.
To save time, the researchers program the heads to keep moving while retracting and redepositing the material. The challenge is to minimize or eliminate the thin strings of material left after retraction, which would need to be removed in post-production. The team spent a lot of time analyzing video images and data to explore the effects the different printing parameters (speed, as well as the amount and length of the deposited filaments) to minimize errors. The researchers were able to decrease the errors to about one percent, Cleeman said.
The students used an MF3 machine, which they built almost entirely with off-the shelf parts, with three nozzles for their research. They plan to build one with 36 nozzles by March and begin the next round of tests, which will focus on improving the geometry and strength of the printed parts. They will also continue conducting thermal simulation tests. Since MF3 prints objects in sections, hot filaments of material are often deposited next to cold filaments, which can create stress concentrators depending on the orientation of deposited material.
More Like This: Novel 3D-Printing Technique Could Hasten Bone-Graft Recovery
“We want to get a better understanding of that unique thermal history,” Cleeman said. “In the future, when we start to perform these strength tests, we can use this thermal simulation to try and overcome that obstacle by either changing the number of nozzles or their array.”
The current research took nearly two years to complete, with a good chunk of that time spent perfecting the software, which Cleeman learned to do by watching YouTube videos and other online research.
“I think it's important to be a Jack of all trades,” he said about the need for young engineers to learn additional skills that will make them more valuable in the lab and on the job. “You don't have to be an expert, but the skills are all out there to be learned. The other thing is that it's very important to be up to date with the literature that exists. The reason we came up with this project is because everybody was sort of complaining about throughput resolution trade-off.
We saw an opportunity because we were keeping up to date with the additive manufacturing literature.”
Jeff O’Heir is a science and technology writer based in Huntington, NY.
Students at Rutgers School of Engineering have come up with a new system they say will decrease those imperfections and pave the way for 3D printing big, complex parts made from thermoplastics at a fraction of the cost of current large-format methods. The researchers outline their new approach, called multiplex fused filament fabrication (MF3), in the August edition of Additive Manufacturing.
Small-diameter extruder nozzles typically print objects with much higher resolution than the bigger nozzles used on large format printers. Small nozzles, however, deposit material too slowly to cost-effectively print big objects. But what if a series of those smaller nozzles replaced the large single nozzle to quickly deposit the molten plastic at high resolution?
Read On: Advancing Additive Manufacturing in Aerospace
That’s the concept behind the new research. MF3 uses a single gantry (the frame or arm that supports the printer head as it moves around) to print single or multiple parts simultaneously using several extruders. To achieve high resolution and efficiency, the researchers custom designed slicer software (made up of the code that maps an object into the slices or layers to be printed) to control the material deposition of each nozzle. They can turn the deposition from each nozzle on or off at any time. That allows each nozzle to print distinct 3D geometries or its own individual part.
“This saves time because when you use multiple smaller nozzles you can accumulate the same throughput as one very large nozzle but get the high resolution,” said Jeremy Cleeman, a mechanical engineer, graduate student researcher, and lead author of the study. “You save a lot of time on the backend, which is where you’d have to do all of that machining.”
The time saved varies with each printed part. But from its research, the team found the area of material that does not have to be machined from the finished object is the difference between the nozzle diameters squared. In the case of an 8-mm nozzle compared to a 2-mm nozzle, the difference would be 36. “It’s a significant factor,” Cleeman said.
Recommended for You: Is 3D Printing the Future of Manufacturing?
The goal of the MF3 system is not to print faster than today’s large-format printers, since they are already very fast, but to save time on the machining side. Based on a series of simple throughput calculations, the researchers determined that 36 2-mm nozzles attached to the gantry can equal the speed of one 8-mm nozzle. “We can keep up with the big-area machines at a much better resolution,” Cleeman said.
Another challenge was trying to better understand and improve filament retraction and redeposition. With most 3D printers, the gantry stops moving, the material is retracted, and the printer head then moves to its next position.
To save time, the researchers program the heads to keep moving while retracting and redepositing the material. The challenge is to minimize or eliminate the thin strings of material left after retraction, which would need to be removed in post-production. The team spent a lot of time analyzing video images and data to explore the effects the different printing parameters (speed, as well as the amount and length of the deposited filaments) to minimize errors. The researchers were able to decrease the errors to about one percent, Cleeman said.
The students used an MF3 machine, which they built almost entirely with off-the shelf parts, with three nozzles for their research. They plan to build one with 36 nozzles by March and begin the next round of tests, which will focus on improving the geometry and strength of the printed parts. They will also continue conducting thermal simulation tests. Since MF3 prints objects in sections, hot filaments of material are often deposited next to cold filaments, which can create stress concentrators depending on the orientation of deposited material.
More Like This: Novel 3D-Printing Technique Could Hasten Bone-Graft Recovery
“We want to get a better understanding of that unique thermal history,” Cleeman said. “In the future, when we start to perform these strength tests, we can use this thermal simulation to try and overcome that obstacle by either changing the number of nozzles or their array.”
The current research took nearly two years to complete, with a good chunk of that time spent perfecting the software, which Cleeman learned to do by watching YouTube videos and other online research.
“I think it's important to be a Jack of all trades,” he said about the need for young engineers to learn additional skills that will make them more valuable in the lab and on the job. “You don't have to be an expert, but the skills are all out there to be learned. The other thing is that it's very important to be up to date with the literature that exists. The reason we came up with this project is because everybody was sort of complaining about throughput resolution trade-off.
We saw an opportunity because we were keeping up to date with the additive manufacturing literature.”
Jeff O’Heir is a science and technology writer based in Huntington, NY.
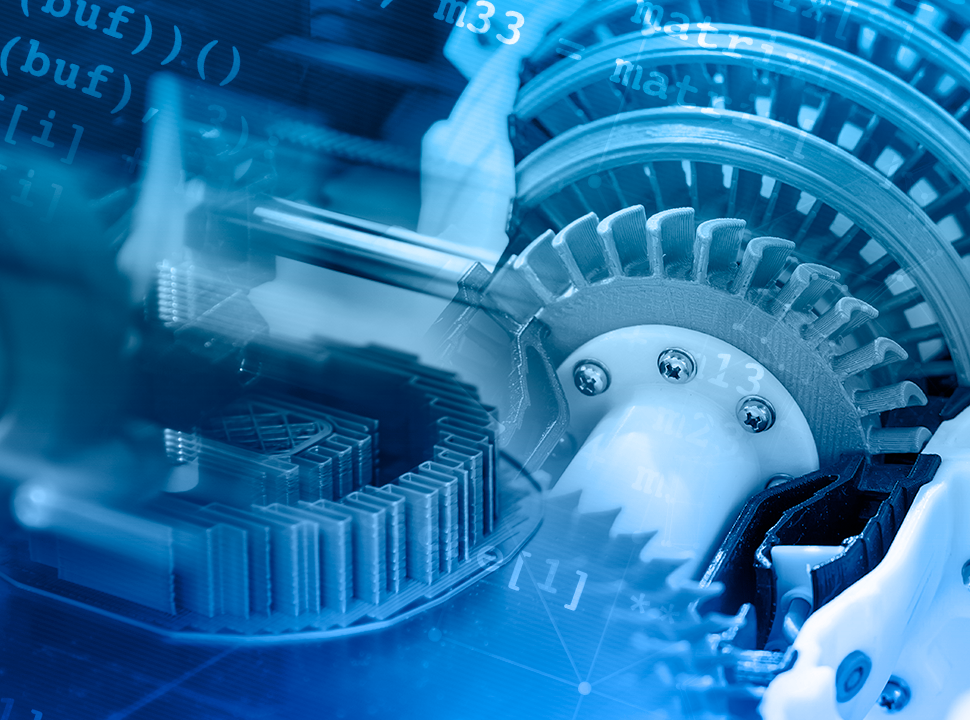
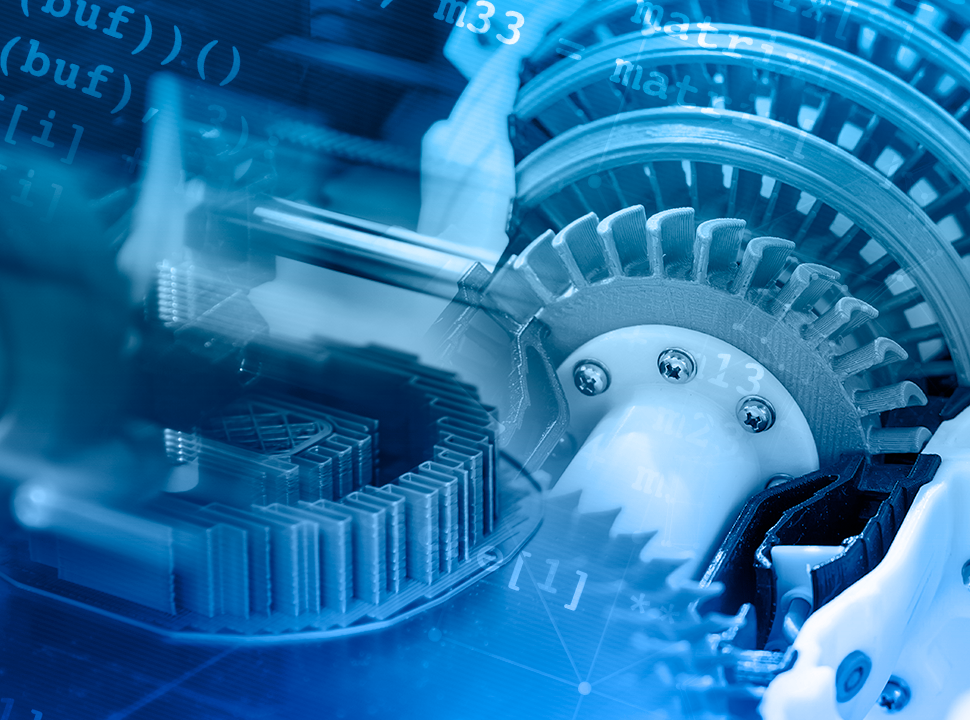