A Linear Motor to Cut Cooling Costs
A Linear Motor to Cut Cooling Costs
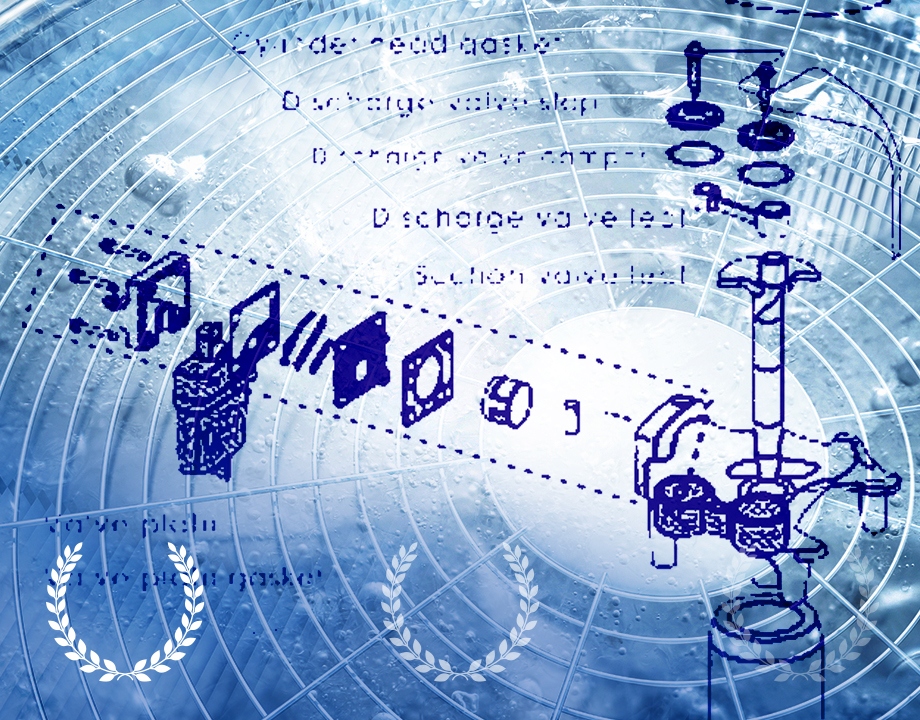
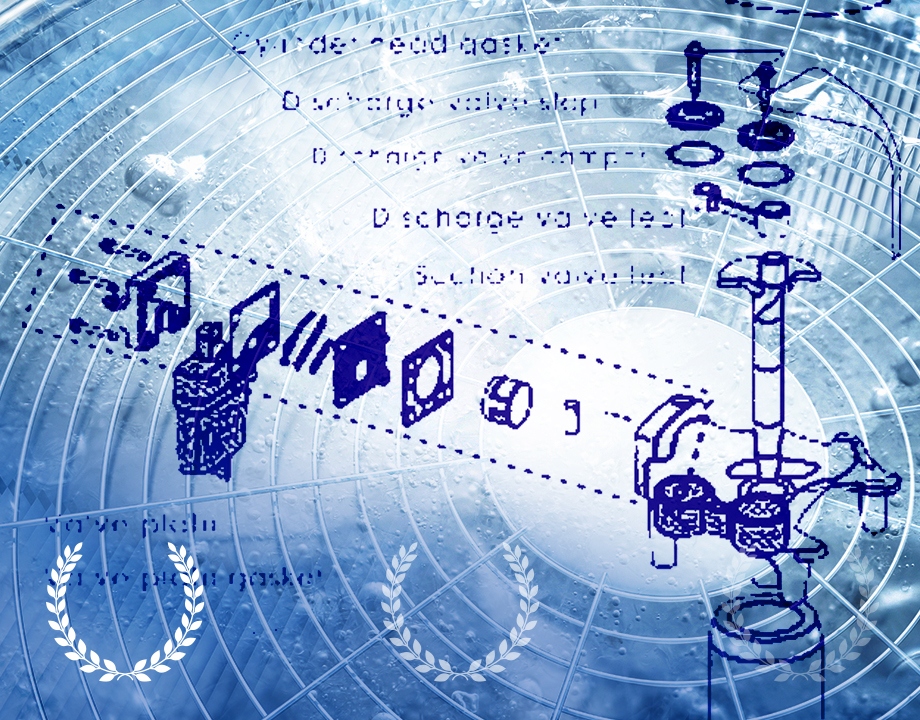
Magtor motor increases compressor efficiencies by 30 percent.
A massive chunk of the world’s energy use goes to cooling homes and refrigerating food. In the coming decades more and more of the world will cool air for comfort and convenience, to the tune of some half a billion cooling units sold each year. All those air conditioners and refrigerators are dependent on their compressors, and a tiny increase in compressor efficiency could have a huge effect on reducing energy use worldwide.
And yet, compressors have hardly evolved in a century.
But now Magtor Ltd., a small European company headquartered in Malta, has chucked out the rotary drive at the heart of compressors as we know them and replaced it with a linear motor. The result is a compressor that is more than 30 percent more efficient than its traditional competitors, according to company officials.
The inventors of the new motor weren’t thinking of compression and cooling when they first created their motor. “Initially, we did not intend to be disruptive in the compressor area,” said Jeremy Hein, Magtor’s co-founder and chief technology officer. “Our intention was to design an electromagnetic piston that converts electricity to linear mechanical motion in both directions.”
More for You: What Termites Can Teach Engineers
When they created their first prototype, they immediately connected it to a crank shaft. “It doesn’t make that much sense to convert a linear motion back to a rotary motion, while everyone else is doing the opposite,” said Hein. Eventually, though, Hein and his team noticed that the force profile of their motor was a perfect match for a compressor.
That profile is the result of a clever, and deceptively simple, arrangement of magnets, shaft, and stator. Two magnetic plates, aligned and facing each other, are connected by a shaft. A stator at the center switches the plates between attraction and repulsion.
“The core principles of our systems are not new,” said Hein. “Any kid playing with magnets could understand the basic principles. But to achieve repulsive interaction between an electromagnet and a permanent magnet requires a lot of electricity. That’s why these devices were not explored much. They’re inefficient from the start.”
Reader's Choice: A Tunable Material for Capturing and Releasing Heat
The Magtor motor also needs no lubrication and the only contact points are found within the compression chambers. So not only is it more efficient than what’s currently available, it’s also likely to have much greater longevity.
Having a target compressor in mind, the Magtor team developed their own valves and pumps to connect to both sides of the Magtor linear motor. “We had absolutely no experience on the compression side, and we had to learn the hard way by mimicking or mirroring what was available on the market,” said Hein. “There was a lot of frustration, and trial and error, but we eventually delivered a “Magtopressor” capable of delivering the same job as the target compressor while consuming less electricity.”
They updated their design to use off-the-shelf components, which offered equal or greater performance. For instance, when thd team came across suitable valves, the resulting compressor worked faster while using less electricity.
The Magtor motor uses a double-cylinder geometry with the magnetic interactions occurring only at the edges of the magnetic plates. These are always kept in alignment with the edges of the electromagnet. This gives the unit a precise flux guidance, and an incredibly tight magnetic field, so the motor needs no shielding.
Editor's Pick: A Pressure Sensor that's Sensitive to Pressure
“When we started, we used titanium tools and made sure not to wear our watches,” said Hein. “Now there’s no need for that due to this geometrical feature.”
Already industry members have been calling the Magtor offices, hoping to use the motor in the next generation of cooling products. But there’s still work to be done. The linear compressor is, at the moment, not enclosed within a shell and mufflers or silencers are not incorporated into the pumps, so it’s loud. But the volume is not likely to remain a significant issue and Hein puts their technology readiness level at six out of nine.
When the motor is produced on a larger scale, it’s likely to get even more efficient. “It will be even better tomorrow, when it’s produced industrially,” said Magtor co-founder and chairman, Martin Marschner von Helmreich. “We are only just beginning to scratch the surface of the potential of our motor.”
Michael Abrams is an engineering and technology writer in Westfield, N.J.
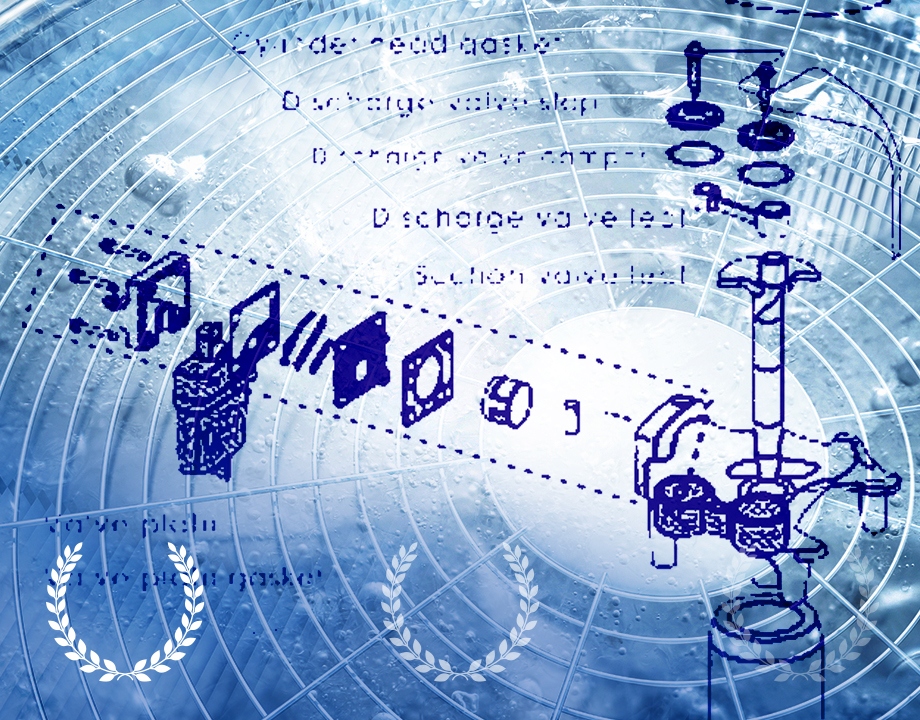
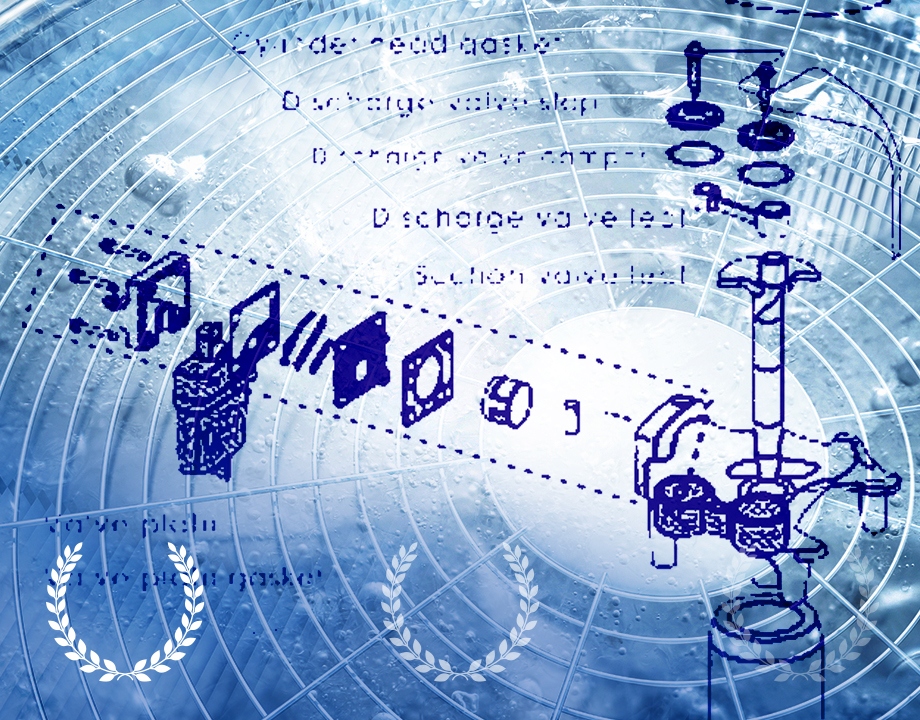