Using Fluids to Control Energy Use in Buildings
Using Fluids to Control Energy Use in Buildings
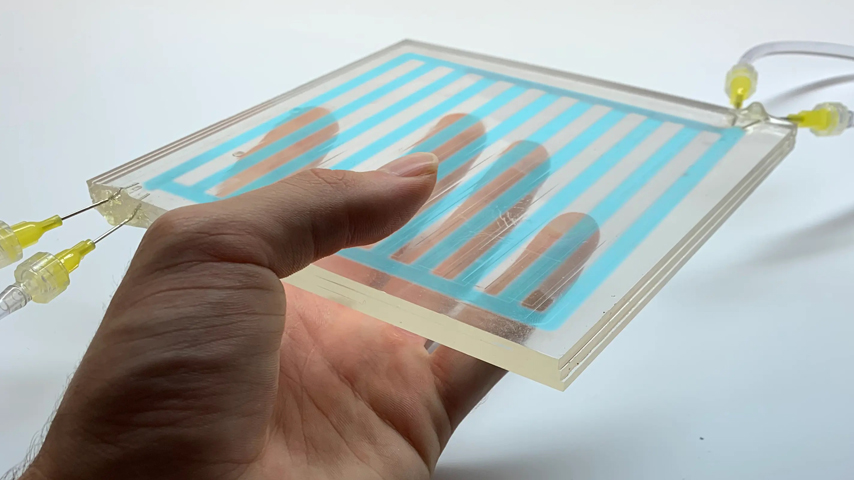
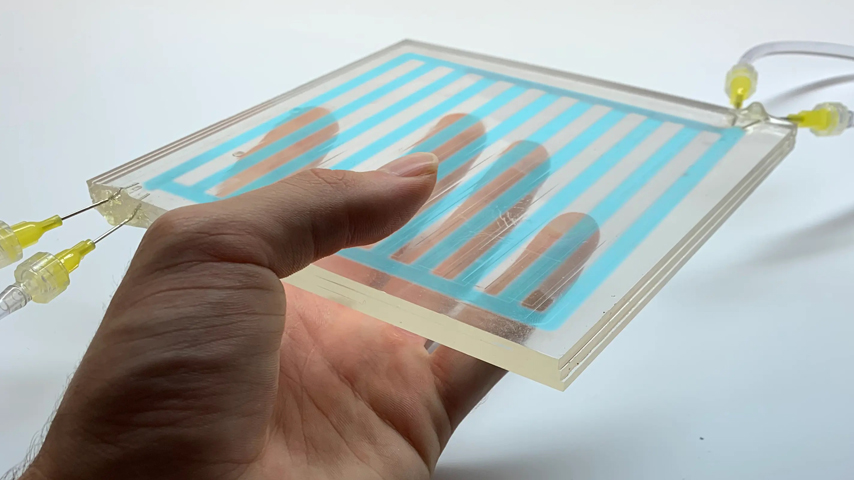
A prototype using channels filled with fluid shows promise in mitigating heating and cooling costs in buildings.
With so much focus on developing and improving renewable energy sources, a team of researchers at the University of Toronto is looking at ways to use less energy. Raphael Kay, a graduate research student, now a research fellow at Harvard University, is mixing his architecture undergraduate degree with the bio inspired engineering lab to apply useful strategies in nature to the built environment.
“Certain mammals regulate their temperature by switching blood flow between surface capillaries and deep veins nearer to the body core. As flow increases within capillaries closer to the body surface, the organisms shed more heat,” he said.
Using this mechanism as inspiration, the team developed a prototype using fluids to control how much light and solar energy can pass through a pane of glass, creating a multilayered optofluidic effect, enabling buildings to conserve energy, reduce artificial lighting, and mitigate heat loss. It pulls inspiration from heating and cooling control mechanisms in nature to reduce the overall energy consumed by the built environment.
Become a Member: How to Join ASME
According to the International Energy Agency’s 2022 Buildings Report, buildings consume 30 percent of our global energy supply and 27 percent of our total energy sector emissions. Global air conditioning demand is expected to triple by 2050. Reducing the amount of energy each building uses could have a significant impact on the global energy sector and greatly reduce consumption.
However, present building systems do not have this capability. In a traditional building, the heating and cooling systems design is based on the performance of the envelope, the barrier between the inside and outside. This includes R-values of each material, the location of windows, how much solar energy can pass through the glass, and thermal bridging where heat loss can occur at the connection points between the envelope system and the building structure.
Current construction methods and materials offer different shading, glass, and insulation performance, but these static solutions do not adjust their configuration or performance as the weather conditions outside change.
“Existing facades cannot achieve selective, reconfigurable responses to their solar environment,” said Kay. “No window, sunshade, or colour film technology can independently tune the amount (intensity), wavelength, and dispersion of sunlight as solar conditions change.”
More for You: Glowing Worms Detect Foul Air
The multilayered optofluidic prototype layers sheets of plastic in a stack, with each layer containing milli-scale channels for fluid movement. It is a 15 x 15 x 2 cubic centimeter bilayer/trilayer device made of polymer sheets with millimeter scale channels. Various fluid compositions pump through the channels in each layer to control the sunlight penetration.
Buildings experience microclimates across their various facades depending on whether the building face is in direct sunlight or shade, the temperature outside, wind speed, and the heating and cooling needs inside. The prototype contains multiple layers, enabling different fluids to pump simultaneously through sequential layers, creating a dynamic system to control light and solar energy automatically for each segment of window.
For implementation in cold climate regions, glycol can be added to the fluids flowing through each layer to reduce the freeze point. This would enable buildings to benefit from solar energy gains and mitigate heat loss at the building envelope in the winter without the risk of freezing the system.
The research team is currently working with industry experts to better understand the prototype implementation in building construction.
“What is the simplest, most scalable way to implement this prototype? How many channels? What types of channels? How thick or how thin are the fluid channels? What types of liquids? What does our pumping system look like? Where do we put the pumps?” are just some of the problems the researchers hope to solve, said Kay.
With so many existing buildings already standing, the team is also hoping to develop a version of their prototype that will act as an add-on to an existing window system. While perhaps not as effective as installing the milli-scale channels in a new glass system, the add-on would still have a significant impact on heating and cooling requirements for existing buildings and facilitate easier implementation to help owners meet energy targets sooner and more effectively.
Reader's Choice: Window Film Reduces Energy Costs
The simulated results from the research project showed 25 percent annual savings on heating, cooling, and light energy with just one layer of fluid, and an increase of up to 50 percent savings with a second layer, said Kay.
Early simulations and modeling show the system can accomplish savings up to 75 percent on heating energy, 20 percent on artificial lighting, and 43 percent on operational energy. This will have a huge impact on the built environment, the size and capacity of heating and cooling systems, and the energy consumed each year by buildings.
The cost to operate the prototype is roughly $100 per cubic meter of glass, which represents a fraction of the potential savings of this system from an operational standpoint, he said. The multilayered optofluidic system can lower the heating and cooling loads by half, reducing not just the capital cost of HVAC systems during construction, but also the space allotted for them leading to more usable floor space throughout the building.
Application of the prototype, which Kay developed for his master’s thesis, is continuing in Toronto, while Kay works toward a Ph.D. at Harvard’s Biomineralization and Biomimetics Laboratory. Kay is hopeful a larger prototype will be available in about a year that can be tested on actual buildings.
Nicole Imeson is an engineer and writer in Calgary, Alberta.
“Certain mammals regulate their temperature by switching blood flow between surface capillaries and deep veins nearer to the body core. As flow increases within capillaries closer to the body surface, the organisms shed more heat,” he said.
Using this mechanism as inspiration, the team developed a prototype using fluids to control how much light and solar energy can pass through a pane of glass, creating a multilayered optofluidic effect, enabling buildings to conserve energy, reduce artificial lighting, and mitigate heat loss. It pulls inspiration from heating and cooling control mechanisms in nature to reduce the overall energy consumed by the built environment.
Become a Member: How to Join ASME
According to the International Energy Agency’s 2022 Buildings Report, buildings consume 30 percent of our global energy supply and 27 percent of our total energy sector emissions. Global air conditioning demand is expected to triple by 2050. Reducing the amount of energy each building uses could have a significant impact on the global energy sector and greatly reduce consumption.
However, present building systems do not have this capability. In a traditional building, the heating and cooling systems design is based on the performance of the envelope, the barrier between the inside and outside. This includes R-values of each material, the location of windows, how much solar energy can pass through the glass, and thermal bridging where heat loss can occur at the connection points between the envelope system and the building structure.
Current construction methods and materials offer different shading, glass, and insulation performance, but these static solutions do not adjust their configuration or performance as the weather conditions outside change.
“Existing facades cannot achieve selective, reconfigurable responses to their solar environment,” said Kay. “No window, sunshade, or colour film technology can independently tune the amount (intensity), wavelength, and dispersion of sunlight as solar conditions change.”
More for You: Glowing Worms Detect Foul Air
The multilayered optofluidic prototype layers sheets of plastic in a stack, with each layer containing milli-scale channels for fluid movement. It is a 15 x 15 x 2 cubic centimeter bilayer/trilayer device made of polymer sheets with millimeter scale channels. Various fluid compositions pump through the channels in each layer to control the sunlight penetration.
Buildings experience microclimates across their various facades depending on whether the building face is in direct sunlight or shade, the temperature outside, wind speed, and the heating and cooling needs inside. The prototype contains multiple layers, enabling different fluids to pump simultaneously through sequential layers, creating a dynamic system to control light and solar energy automatically for each segment of window.
For implementation in cold climate regions, glycol can be added to the fluids flowing through each layer to reduce the freeze point. This would enable buildings to benefit from solar energy gains and mitigate heat loss at the building envelope in the winter without the risk of freezing the system.
The research team is currently working with industry experts to better understand the prototype implementation in building construction.
“What is the simplest, most scalable way to implement this prototype? How many channels? What types of channels? How thick or how thin are the fluid channels? What types of liquids? What does our pumping system look like? Where do we put the pumps?” are just some of the problems the researchers hope to solve, said Kay.
With so many existing buildings already standing, the team is also hoping to develop a version of their prototype that will act as an add-on to an existing window system. While perhaps not as effective as installing the milli-scale channels in a new glass system, the add-on would still have a significant impact on heating and cooling requirements for existing buildings and facilitate easier implementation to help owners meet energy targets sooner and more effectively.
Reader's Choice: Window Film Reduces Energy Costs
The simulated results from the research project showed 25 percent annual savings on heating, cooling, and light energy with just one layer of fluid, and an increase of up to 50 percent savings with a second layer, said Kay.
Early simulations and modeling show the system can accomplish savings up to 75 percent on heating energy, 20 percent on artificial lighting, and 43 percent on operational energy. This will have a huge impact on the built environment, the size and capacity of heating and cooling systems, and the energy consumed each year by buildings.
The cost to operate the prototype is roughly $100 per cubic meter of glass, which represents a fraction of the potential savings of this system from an operational standpoint, he said. The multilayered optofluidic system can lower the heating and cooling loads by half, reducing not just the capital cost of HVAC systems during construction, but also the space allotted for them leading to more usable floor space throughout the building.
Application of the prototype, which Kay developed for his master’s thesis, is continuing in Toronto, while Kay works toward a Ph.D. at Harvard’s Biomineralization and Biomimetics Laboratory. Kay is hopeful a larger prototype will be available in about a year that can be tested on actual buildings.
Nicole Imeson is an engineer and writer in Calgary, Alberta.
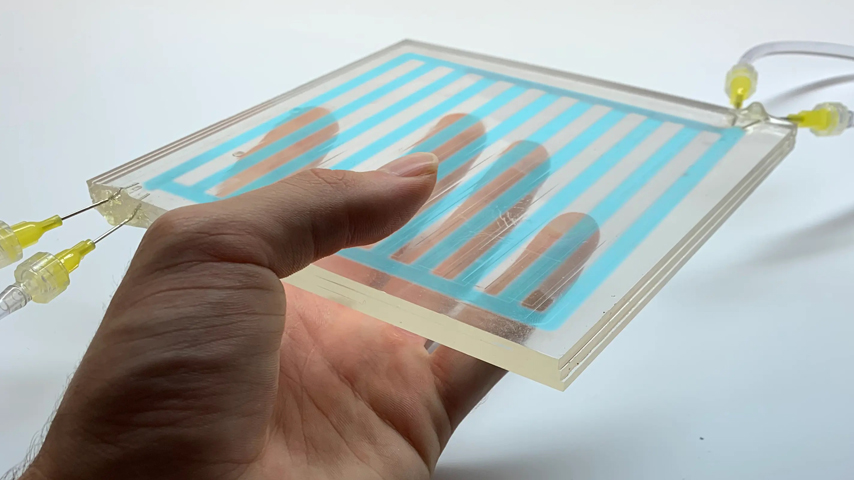
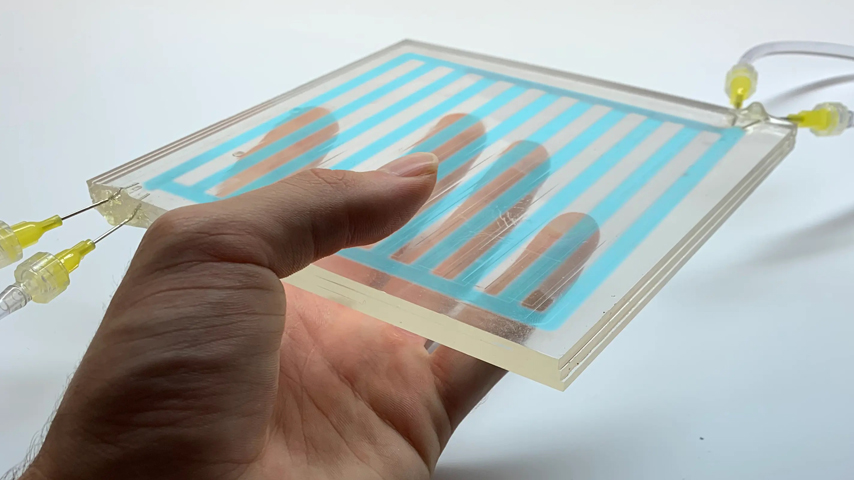