A New Enzyme Eats Plastics
A New Enzyme Eats Plastics
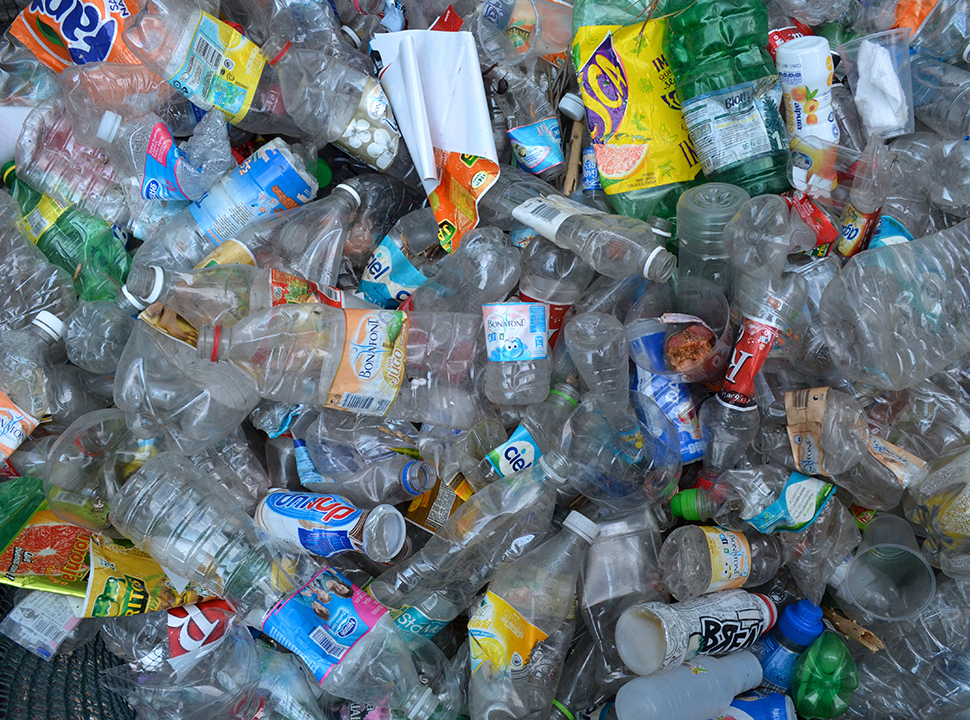
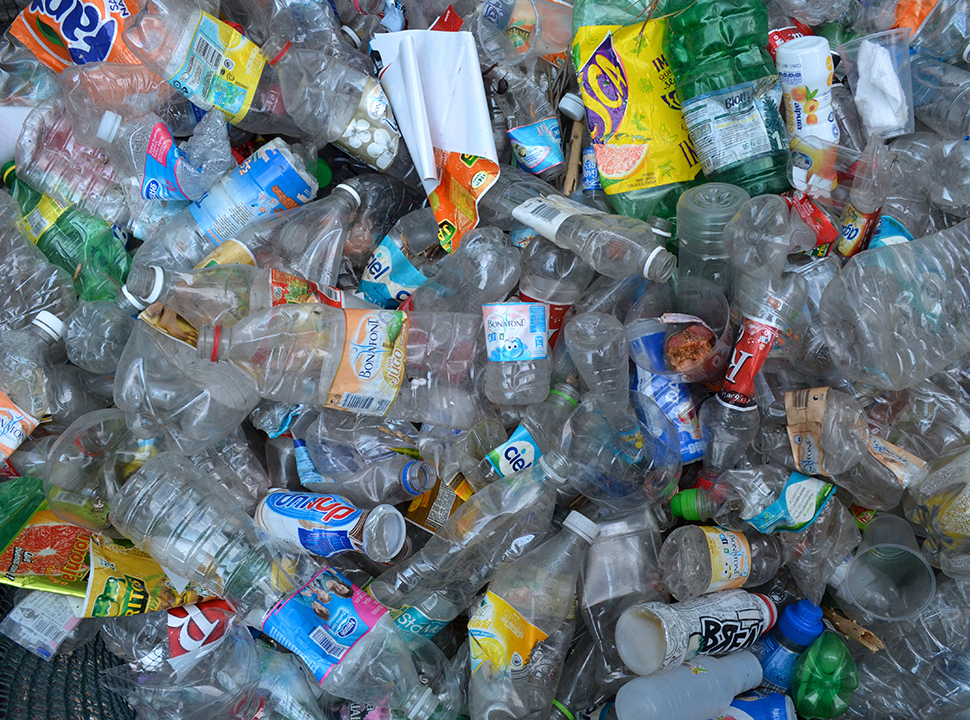
Plastic waste is a global problem, but a new enzyme that breaks PET down could drive a circular plastics economy.
Last updated: October 31, 2024
Plastic is all around us. That’s no secret to anyone who has purchased a bottle of water or grabbed a prepackaged salad after work. It’s really no secret to everyone. Today’s plastics may take many different forms but they seem to be ubiquitous.
The problem is that it takes all forms of plastic hundreds of years to degrade.
Recycling can help reduce plastic waste, but it’s far from an actual solution—and it comes with drawbacks. The process requires a lot of energy and it’s not available everywhere. So far, plastics make up more than 7 billion tons of waste around the world. And less than 10 percent of it has been recycled, according to the United Nations and its UN Environment Programme.
However, another recycling tool is quickly evolving. Researchers around the globe are studying enzymes that can break down plastic polymers. Much of that research stems from the 2016 study by a team of Japanese researchers about the plastic-consuming bacteria Ideonella sakaiensis they found in samples from a plastic recycling plant.
One major leap forward, published in their 2022 study, was made by researchers at the University of Texas at Austin. The researchers, with the help of a machine-learning algorithm, designed an enzyme that slashed the time it takes to degrade plastics from centuries to days, according to Hal Alper, a professor of chemical engineering at the university, who helped lead the research program.
More for You: AI Can Use Infrared Signature to Sort Plastics
In some cases, the enzyme fully broke down plastics to the molecular level in 24 hours, he explained.
Alper envisions a day—hopefully soon—when industries large and small use enzymes to break down plastics and then build them up again: a circular recycling process.
Researchers used a machine-learning algorithm to unlock the biological combination for an enzyme that could quickly eat through plastic at the low temperatures needed to make them portable and affordable. The algorithm generated novel mutations to a natural enzyme called PETase, which has been shown to degrade polyethylene terephthalate (PET) plastics.
The model predicted five enzyme mutations that could meet researchers’ goals, Alper said.
The project focuses on PET, an “everyday plastic” found in most of the packaging you touch: soda bottles and fruit and salad packaging to name only a few. Some fibers and textiles also contain PET. It makes up 12 percent of all global waste.
After running the machine-learning program, researchers created a new enzyme variant, which they dubbed FAST-PETase. Functional, active, stable and tolerant, PETase quickly breaks plastic down into smaller parts, a process called depolymerization. It can also put those parts back together again—through repolymerization—to create an entirely new product.
Biological solutions like enzymes that break down plastic use much less energy than classic disposal methods, like burning plastics at waste treatment sites. That process generates a lot of pollution
Editor’s Pick: How Robots Are Helping Us to Recycle Better
While research on enzymes for plastic recycling has advanced during the past 15 years, no one had been able to figure out how to make these enzymes work at low temperatures, Alper said.
Until the advent of FAST-PETase.
“When considering environmental cleanup applications, you need an enzyme that can work in the environment at ambient temperature. This requirement is where our tech has a huge advantage in the future,” Alper said.
With its mutations, the FAST-PETase can perform the process at less than 50 degrees Celsius and within a range of pH levels, he added.
And it takes only days or weeks to degrade plastic. In some cases it can split plastics to the molecular level within 24 hours.
In tests, it took FAST-PeTase only one week to break down PET from 51 different thermoformed products into monomers. The enzyme also depolymerized untreated parts of a commercial water bottle at 50 degrees C. At the same temperature, it turned a thermally pretreated water bottle into mere molecules.
But the researchers didn’t stop at depolymerizing. They found the same enzyme could build polymers back up—repolymerization—in about the same amount of time it took to break them down.
Reader’s Choice: Intercepting Water Plastic Pollution
With that in mind, they created a closed-loop PET recycling process in which FAST-PETase breaks down PET into monomers and then resynthesizes them into a new material that could be used in consumer products.
“Collectively, our results demonstrate a viable route for enzymatic plastic recycling at the industrial scale,” Alper said.
IIndustries could greatly reduce their environmental impact by recovering and reusing plastics at the molecular level, Alper added.
“The possibilities are endless across industries,” Alper said. “This provides corporations from every sector the opportunity to take a lead in recycling their products. Through these more sustainable enzyme approaches, we can begin to envision a true circular plastics economy.”
Jean Thilmany is a science and technology writer in Saint Paul, Minn.
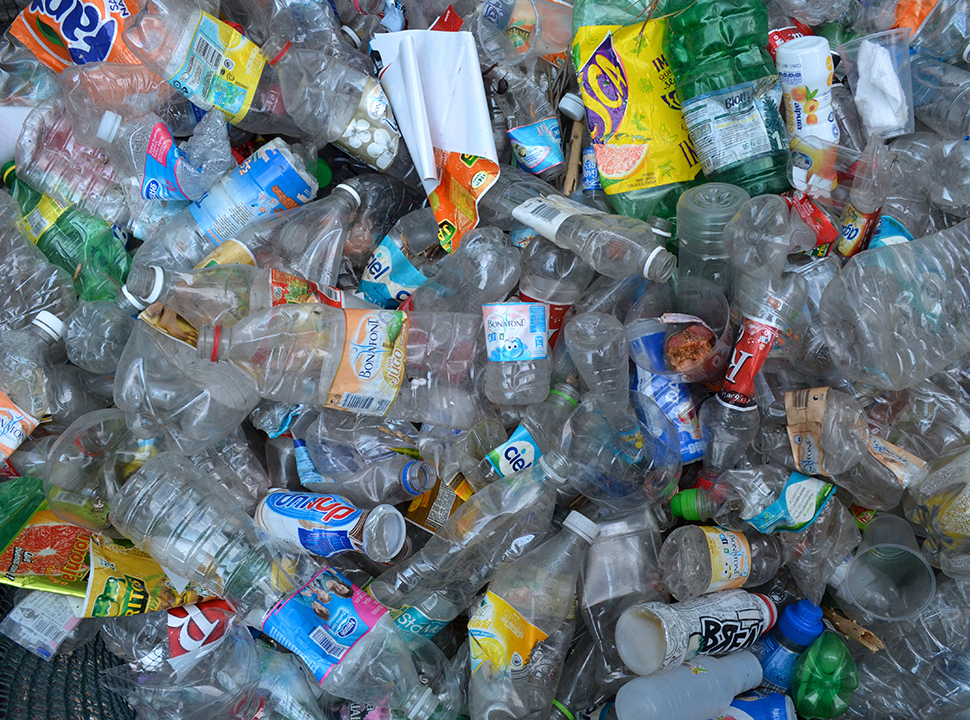
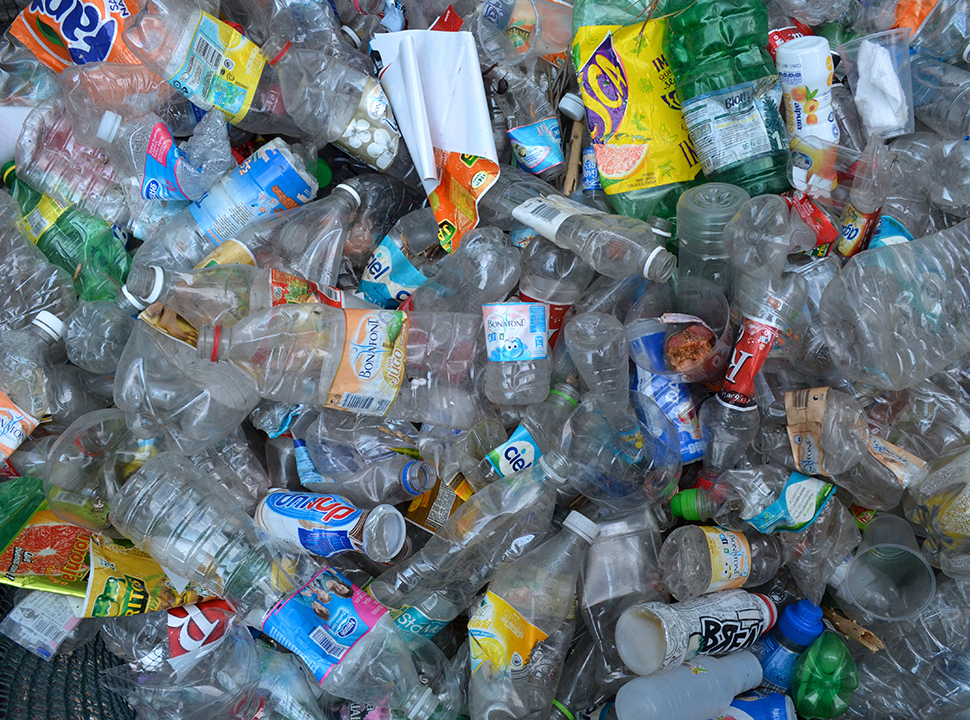