Additive Manufacturing Trends: Looking Back at 2021 and Ahead on 2022
Additive Manufacturing Trends: Looking Back at 2021 and Ahead on 2022
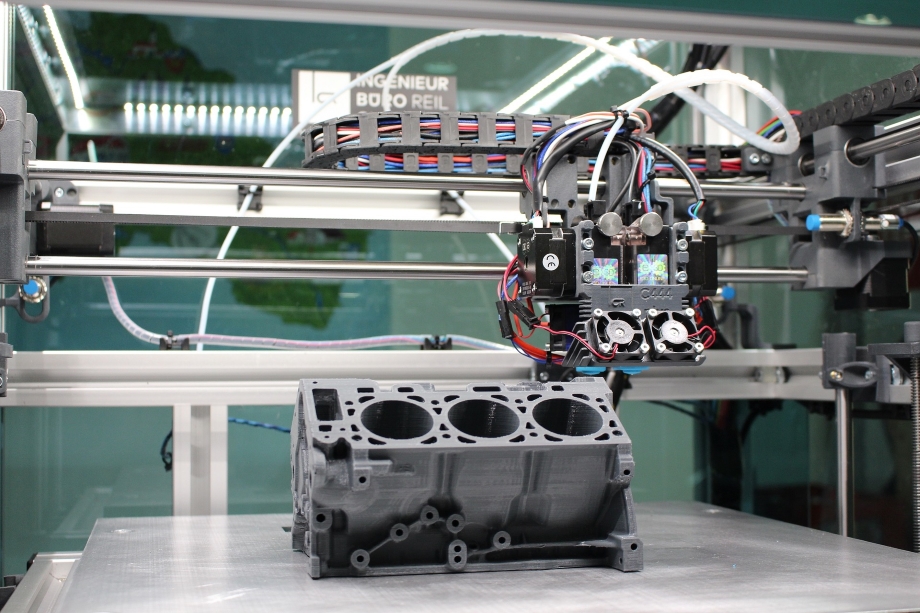
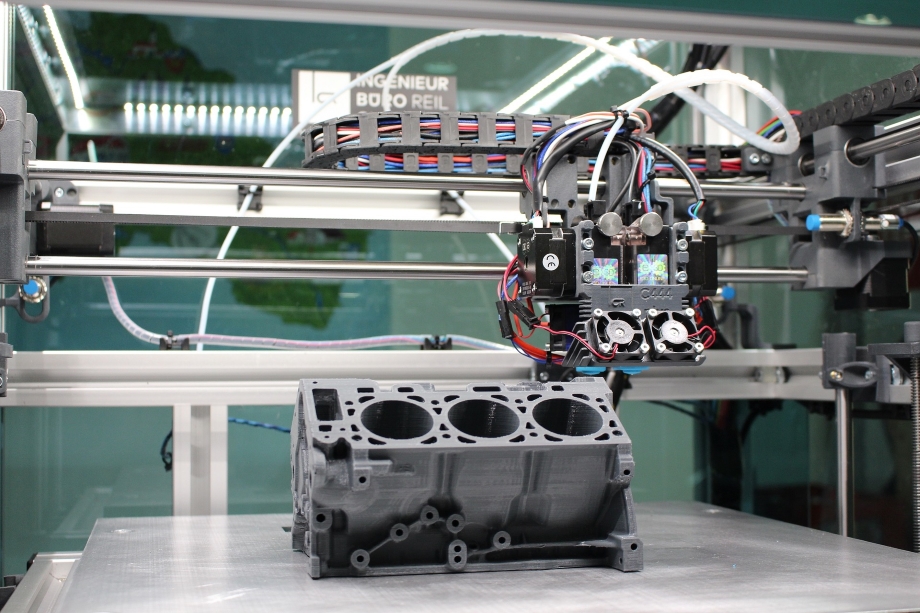
Additive manufacturing and 3D printing made a strong comeback in 2021. The new year looks just as promising.
The global COVID-19 pandemic hit the additive manufacturing industry hard. According to SmarTech Analysis, the AM market was increasing steadily until the end of 2019. In 2020, the sector decreased in all respects as revenue from hardware, materials, and services dipped. However, the spotlight placed on additive manufacturing during the pandemic as a tool to overcome supply chain hardships propelled it to a significant comeback in 2021. Let’s explore some of the top trends of the AM market from 2021 and where the industry may go in 2022.
Across all additive manufacturing companies, there was a significant loss of revenue due to the pandemic. According to IDTechEx’s report “The 3D Printing World After COVID: A Pandemic Post-Mortem”, companies like Desktop Metal, GE Aviation, and 3D Systems reported revenue losses of 38 percent, 32 percent, and 12 percent, respectively, from 2019 to 2020. The primary reason was a decreased demand for 3D printers and materials from industries that were also significantly impacted, such as aerospace, automotive, and manufacturing.
Watch our Video: The Journey of Additive Manufacturing and Artificial Intelligence
In 2021, as the year progressed, companies were able to turn it around and start to perform better than in previous years. In the third quarter, most top companies, including Stratasys, Proto Labs, 3D Systems, ExOne, and Xi’an BLT, were able to report positive revenue recovery. Leading the pack was ExOne, acquired by Desktop Metal, with an almost 75 percent revenue increase over 2019 performance.
According to SmarTech Analysis, metal additives saw significant growth in the third quarter, and companies are now moving toward AM as a source of product development. Sculpteo reported that 36 percent of AM users would use AM for production, 20 percent for customization, and 12 percent would use 3D printing for production flexibility. This coincides with the trends that appeared during the pandemic as companies transitioned to AM for its flexibility and on-demand production capabilities.
The materials driving the AM industry forward in 2021 were a mix of polymers, metal, and ceramics.
To help promote sustainability within AM, 3D printing material suppliers released polymers with renewable characteristics. These new polymers are recyclable and reusable. Chemical company Braskem, for example, partnered with Vartega, a recycling company, to create a polypropylene filament made of 100 percent recycled carbon fiber. Also, in 2021, Materialise released Bluesint PA 12, a 3D printing powder made from 100 percent re-used powder to decrease the wastage of powder in selective laser sintering.
Last year, suppliers introduced novel ceramic materials to the AM market. A primary focus was on micro 3D printing. For example, Boston Micro Fabrication released a high-temperature alumina resin for micro-ceramic components. AGC Chemicals and voxeljet created Brightorb, a ceramic powder mainly for casting modeling and shells. According to IDTechEx, this could increase the use of ceramic 3D printing for the new year.
Recommended for You: Is 3D Printing the Future of Manufacturing?
Lastly, the increased momentum of metal will continue to dominate in 2022. IDTechEx reported on the rise of fused filament fabrication (FFF) among metal materials. FFF technology allows companies to produce parts in three stages: printing, debinding, and sintering. This lowers the costs compared to powder bed fusion. Companies like Desktop Metal and Markforged are investing in FFF systems to advance metal printing systems.
Along with increases in metal and ceramics, continued growth will occur within healthcare and aerospace.
“There are two main markets seeing growth: aerospace and medical. So, there are not only implantable
devices using AM but also components of a hospital bed or other handles/fixtures used in the hospital room in equipment. These products are not necessarily related directly to patients but are used within the medical setting,” said Greg Hayes, senior vice president of applied technology at EOS.
Several industry experts also recognize the need for software growth within AM production. Software solutions that can streamline workflows and integrate with existing enterprise solutions will help push AM into large-scale production.
Zach Murphree, vice president of global sales and business at Velo3D, highlights how software can make it easier for engineers to design parts directly for additive manufacturing rather than having to design a part twice.
Editor’s Pick: 5 Questions on the Future of Additive Manufacturing in Aerospace
“Traditional additive manufacturing in the complex, mission-critical metal parts industry is very reliant on design for additive manufacturing (DfAM). After engineers design the part they want, they’ve had to redesign it for additive manufacturing. Then, another engineer takes the DfAM part and builds a print file for a specific machine. However, solutions are emerging that eliminate the need for part-specific development. Engineers simply design the part they want, upload the file, and the software prescribes how it should be manufactured,” said Murphree.
The outlook for AM is bright for 2022, as it appears that industry has finally learned from the initial hurdles that made AM a niche market. With new materials, sustainable processes, and advanced software, AM should be primed for a takeover of part manufacturing.
Carlos M. González is special projects manager.
Market Decline and Resurgence
Across all additive manufacturing companies, there was a significant loss of revenue due to the pandemic. According to IDTechEx’s report “The 3D Printing World After COVID: A Pandemic Post-Mortem”, companies like Desktop Metal, GE Aviation, and 3D Systems reported revenue losses of 38 percent, 32 percent, and 12 percent, respectively, from 2019 to 2020. The primary reason was a decreased demand for 3D printers and materials from industries that were also significantly impacted, such as aerospace, automotive, and manufacturing.
Watch our Video: The Journey of Additive Manufacturing and Artificial Intelligence
In 2021, as the year progressed, companies were able to turn it around and start to perform better than in previous years. In the third quarter, most top companies, including Stratasys, Proto Labs, 3D Systems, ExOne, and Xi’an BLT, were able to report positive revenue recovery. Leading the pack was ExOne, acquired by Desktop Metal, with an almost 75 percent revenue increase over 2019 performance.
According to SmarTech Analysis, metal additives saw significant growth in the third quarter, and companies are now moving toward AM as a source of product development. Sculpteo reported that 36 percent of AM users would use AM for production, 20 percent for customization, and 12 percent would use 3D printing for production flexibility. This coincides with the trends that appeared during the pandemic as companies transitioned to AM for its flexibility and on-demand production capabilities.
Material Growth
The materials driving the AM industry forward in 2021 were a mix of polymers, metal, and ceramics.
To help promote sustainability within AM, 3D printing material suppliers released polymers with renewable characteristics. These new polymers are recyclable and reusable. Chemical company Braskem, for example, partnered with Vartega, a recycling company, to create a polypropylene filament made of 100 percent recycled carbon fiber. Also, in 2021, Materialise released Bluesint PA 12, a 3D printing powder made from 100 percent re-used powder to decrease the wastage of powder in selective laser sintering.
Last year, suppliers introduced novel ceramic materials to the AM market. A primary focus was on micro 3D printing. For example, Boston Micro Fabrication released a high-temperature alumina resin for micro-ceramic components. AGC Chemicals and voxeljet created Brightorb, a ceramic powder mainly for casting modeling and shells. According to IDTechEx, this could increase the use of ceramic 3D printing for the new year.
Recommended for You: Is 3D Printing the Future of Manufacturing?
Lastly, the increased momentum of metal will continue to dominate in 2022. IDTechEx reported on the rise of fused filament fabrication (FFF) among metal materials. FFF technology allows companies to produce parts in three stages: printing, debinding, and sintering. This lowers the costs compared to powder bed fusion. Companies like Desktop Metal and Markforged are investing in FFF systems to advance metal printing systems.
2022 Predictions
Along with increases in metal and ceramics, continued growth will occur within healthcare and aerospace.
“There are two main markets seeing growth: aerospace and medical. So, there are not only implantable
devices using AM but also components of a hospital bed or other handles/fixtures used in the hospital room in equipment. These products are not necessarily related directly to patients but are used within the medical setting,” said Greg Hayes, senior vice president of applied technology at EOS.
Several industry experts also recognize the need for software growth within AM production. Software solutions that can streamline workflows and integrate with existing enterprise solutions will help push AM into large-scale production.
Zach Murphree, vice president of global sales and business at Velo3D, highlights how software can make it easier for engineers to design parts directly for additive manufacturing rather than having to design a part twice.
Editor’s Pick: 5 Questions on the Future of Additive Manufacturing in Aerospace
“Traditional additive manufacturing in the complex, mission-critical metal parts industry is very reliant on design for additive manufacturing (DfAM). After engineers design the part they want, they’ve had to redesign it for additive manufacturing. Then, another engineer takes the DfAM part and builds a print file for a specific machine. However, solutions are emerging that eliminate the need for part-specific development. Engineers simply design the part they want, upload the file, and the software prescribes how it should be manufactured,” said Murphree.
The outlook for AM is bright for 2022, as it appears that industry has finally learned from the initial hurdles that made AM a niche market. With new materials, sustainable processes, and advanced software, AM should be primed for a takeover of part manufacturing.
Carlos M. González is special projects manager.
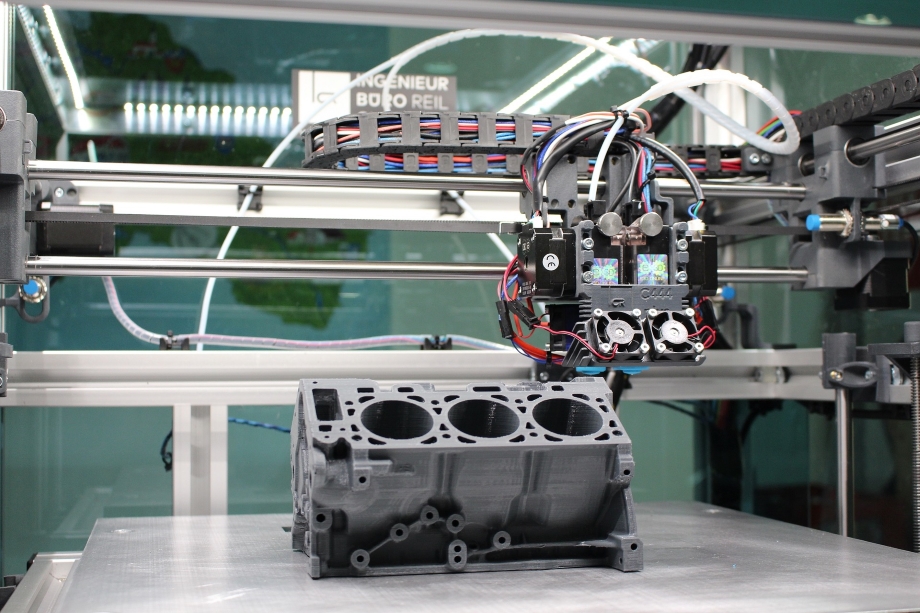
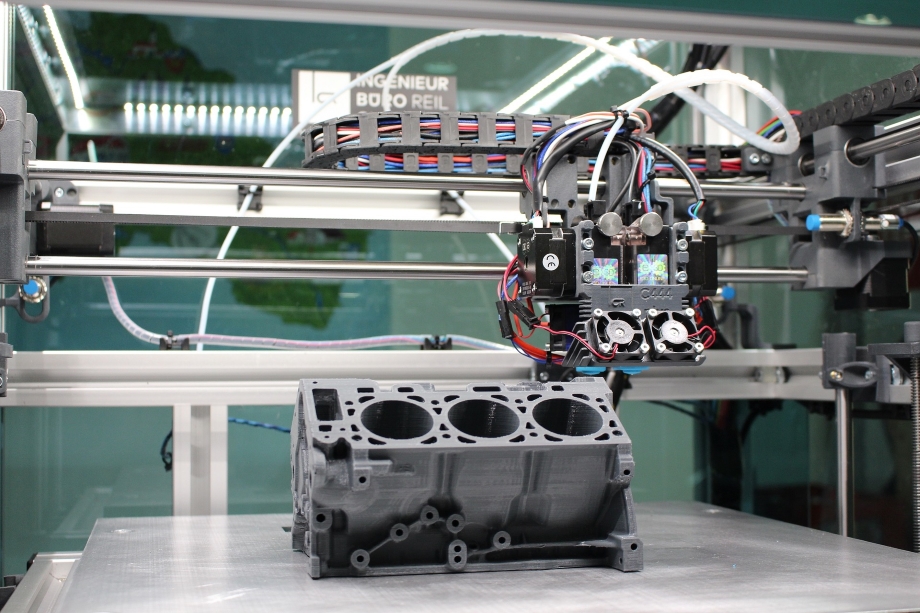