Wettability: How Odd Surfaces and Liquids Interact
Wettability: How Odd Surfaces and Liquids Interact
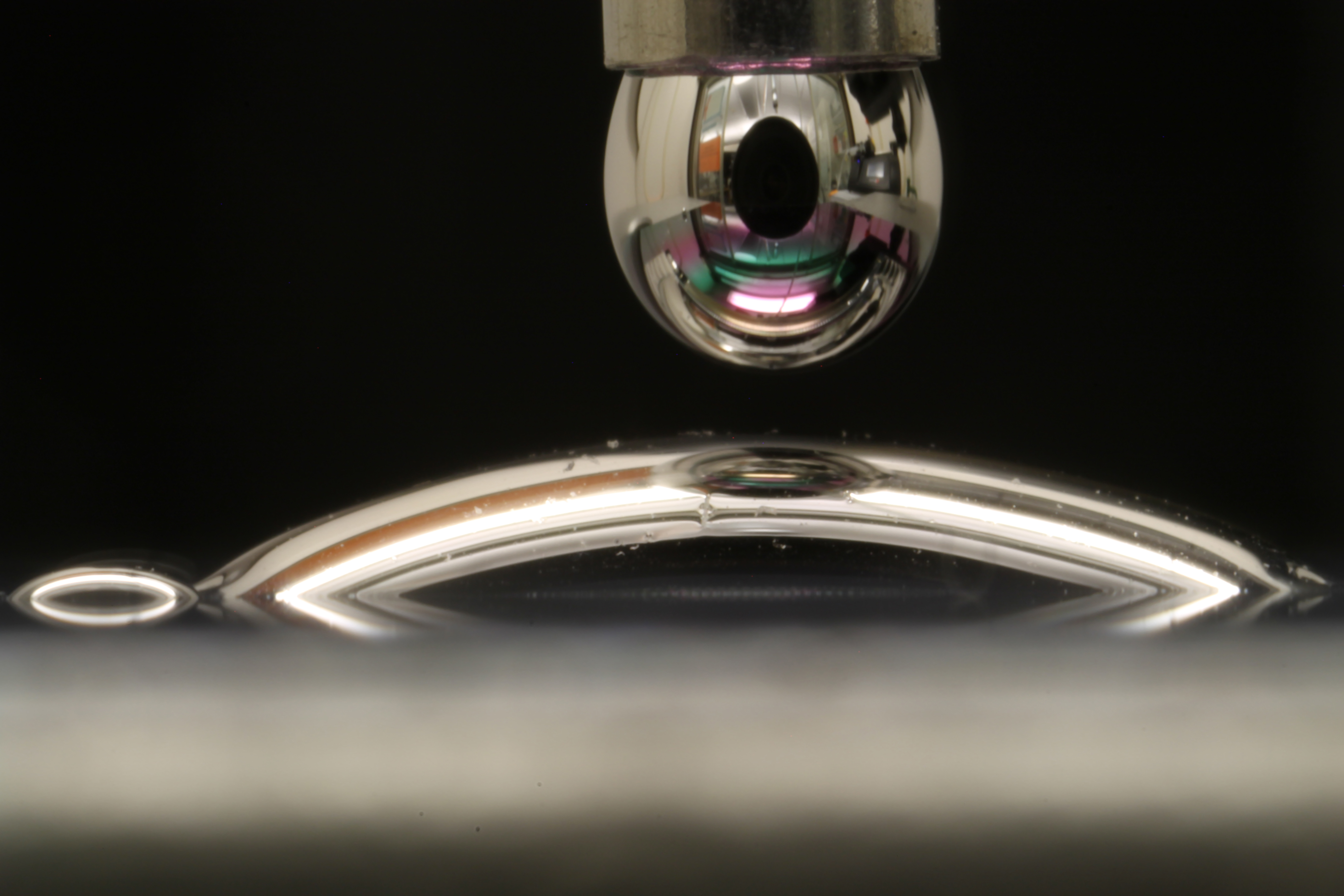
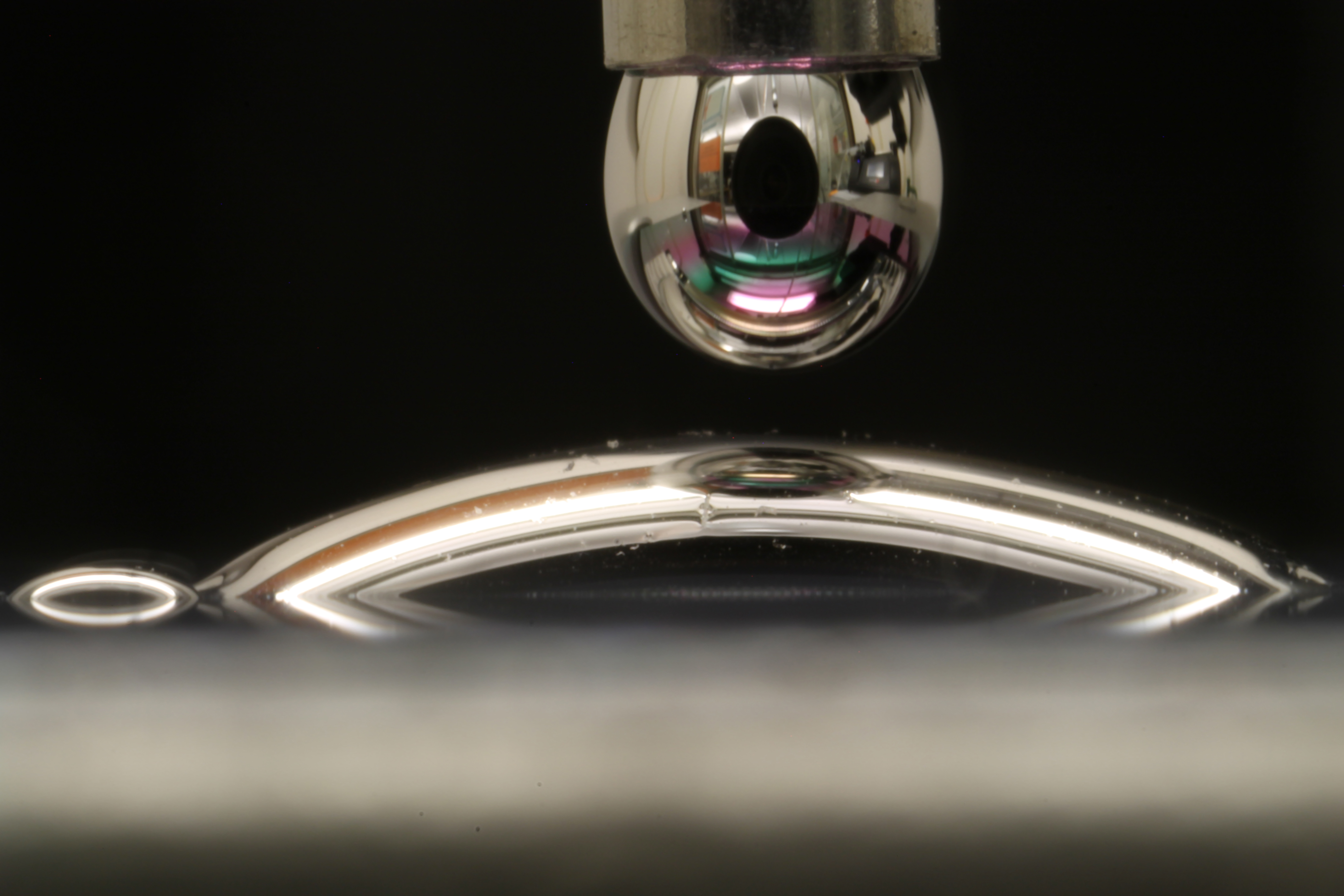
Researchers turn methods to make surfaces “nonwetting” around, producing a method to make unlikely pair of materials “wet.”
The wettability of materials—whether a liquid beads up or spreads out on the surface—has a major impact on how materials can be used in various commercial and industrial applications. Tailoring wettability to cause liquids to spread on a surface has been assumed to be determined by the pairing of liquid and solid materials. However, a team of MIT researchers led by Evelyn Wang, a mechanical engineering professor, has developed a way of making even the most unlikely pair of materials “be wet.”
Wang’s team came up with this idea after a brainstorming session for designing a heat exchanger for supercritical carbon dioxide applications. The session made them realize they needed a material/liquid combination for use in the heat exchanger that needed to be highly wetting in order for the heat exchanger to work properly.
“We wondered if there was a way to make traditional non-wetting material/liquid combinations highly wetting,” Wang said. “From there, we were inspired by previous works that had used re-entrant surfaces to do just the opposite—taking a traditional wetting material/liquid combination and making it highly nonwetting. We were then able to learn about designing re-entrant structures for other applications to discover this new application.”
Wang’s approach involved texturing the surface of a solid material with closely spaced indentations that have “re-entrant openings” where the top of the opening is narrower than the rest of the cavity. The team created these textured surfaces using photolithography followed by reactive ion etching.
More for You: Metamaterials Expand Possibilities in Biomedical Engineering
“While re-entrant structures have been used in research before, they are still relatively new, and the most common methods for creating these features involve semiconductor processes in a cleanroom, since these surface structures smaller generally need to be smaller than a few hundred micrometers,” said Wang.
The textured surface was then treated with a liquid to fill all the cavities, leaving exposed areas of liquid at the surface in each opening, which alters the surface’s properties. Depending on the application, when another liquid is added, its response to the surface is changed from nonwetting to wetting.
Once the liquid fills the openings, it is in a metastable wetting state and will stay there. The design of the openings can influence how stable that metastable state is, as well as how easy it is to get the liquid into the openings.
“We also showed that once the liquid is in the openings, it is easy to keep the openings filled,” Wang said. “For example, if the liquid in the openings is evaporating, this could lead to the openings drying out. But, because the openings are in the highly wetting state even after losing part of the filled liquid, they naturally refill when put into contact with additional liquid, allowing the surface to be replenished.”
Because mercury has exceptionally high surface tension and is a very nonwetting liquid, it was chosen to test a surface made from a typically nonwetting material. Despite the typically nonwetting material/liquid combination, the mercury spread across it, something never before demonstrated.
Reader’s Choice: Ceramic Materials Advance Climate Change Efforts
“Because these structures do not rely on chemical coatings or the chemical nature of the materials, they tend to be durable to things that might typically challenge chemical coatings, such as chemical corrosion, exposure to UV light, or contamination from the air,” Wang added. “However, because re-entrant structures rely on a specific structure geometry to achieve the desired wetting behavior, mechanical damage or abrasion that changes this geometry can negatively affect wetting performance.”
Wang thinks the most interesting aspect of this work is the high wetting potential for previously inaccessible material/liquid combinations, which expands the design space for various thermofluidic applications.
Editor’s Pick: Biomechanics of Pellet-Carrying Honeybees
Possibilities include new designs for high-temperature equipment, wicking, microfluidics, and liquid separation. The technology may also be able to create better joints between dissimilar materials by controlling the wettability.
“Many of these related new behaviors and new applications at this point are still unexplored and we are excited to see what we, or others, come up with next,” Wang said.
Mark Crawford in an engineering and technology writer in Coralles, N.M.
Wang’s team came up with this idea after a brainstorming session for designing a heat exchanger for supercritical carbon dioxide applications. The session made them realize they needed a material/liquid combination for use in the heat exchanger that needed to be highly wetting in order for the heat exchanger to work properly.
“We wondered if there was a way to make traditional non-wetting material/liquid combinations highly wetting,” Wang said. “From there, we were inspired by previous works that had used re-entrant surfaces to do just the opposite—taking a traditional wetting material/liquid combination and making it highly nonwetting. We were then able to learn about designing re-entrant structures for other applications to discover this new application.”
How It Works
Wang’s approach involved texturing the surface of a solid material with closely spaced indentations that have “re-entrant openings” where the top of the opening is narrower than the rest of the cavity. The team created these textured surfaces using photolithography followed by reactive ion etching.
More for You: Metamaterials Expand Possibilities in Biomedical Engineering
“While re-entrant structures have been used in research before, they are still relatively new, and the most common methods for creating these features involve semiconductor processes in a cleanroom, since these surface structures smaller generally need to be smaller than a few hundred micrometers,” said Wang.
The textured surface was then treated with a liquid to fill all the cavities, leaving exposed areas of liquid at the surface in each opening, which alters the surface’s properties. Depending on the application, when another liquid is added, its response to the surface is changed from nonwetting to wetting.
Once the liquid fills the openings, it is in a metastable wetting state and will stay there. The design of the openings can influence how stable that metastable state is, as well as how easy it is to get the liquid into the openings.
“We also showed that once the liquid is in the openings, it is easy to keep the openings filled,” Wang said. “For example, if the liquid in the openings is evaporating, this could lead to the openings drying out. But, because the openings are in the highly wetting state even after losing part of the filled liquid, they naturally refill when put into contact with additional liquid, allowing the surface to be replenished.”
Because mercury has exceptionally high surface tension and is a very nonwetting liquid, it was chosen to test a surface made from a typically nonwetting material. Despite the typically nonwetting material/liquid combination, the mercury spread across it, something never before demonstrated.
Reader’s Choice: Ceramic Materials Advance Climate Change Efforts
“Because these structures do not rely on chemical coatings or the chemical nature of the materials, they tend to be durable to things that might typically challenge chemical coatings, such as chemical corrosion, exposure to UV light, or contamination from the air,” Wang added. “However, because re-entrant structures rely on a specific structure geometry to achieve the desired wetting behavior, mechanical damage or abrasion that changes this geometry can negatively affect wetting performance.”
Potential Industrial Applications
Wang thinks the most interesting aspect of this work is the high wetting potential for previously inaccessible material/liquid combinations, which expands the design space for various thermofluidic applications.
Editor’s Pick: Biomechanics of Pellet-Carrying Honeybees
Possibilities include new designs for high-temperature equipment, wicking, microfluidics, and liquid separation. The technology may also be able to create better joints between dissimilar materials by controlling the wettability.
“Many of these related new behaviors and new applications at this point are still unexplored and we are excited to see what we, or others, come up with next,” Wang said.
Mark Crawford in an engineering and technology writer in Coralles, N.M.
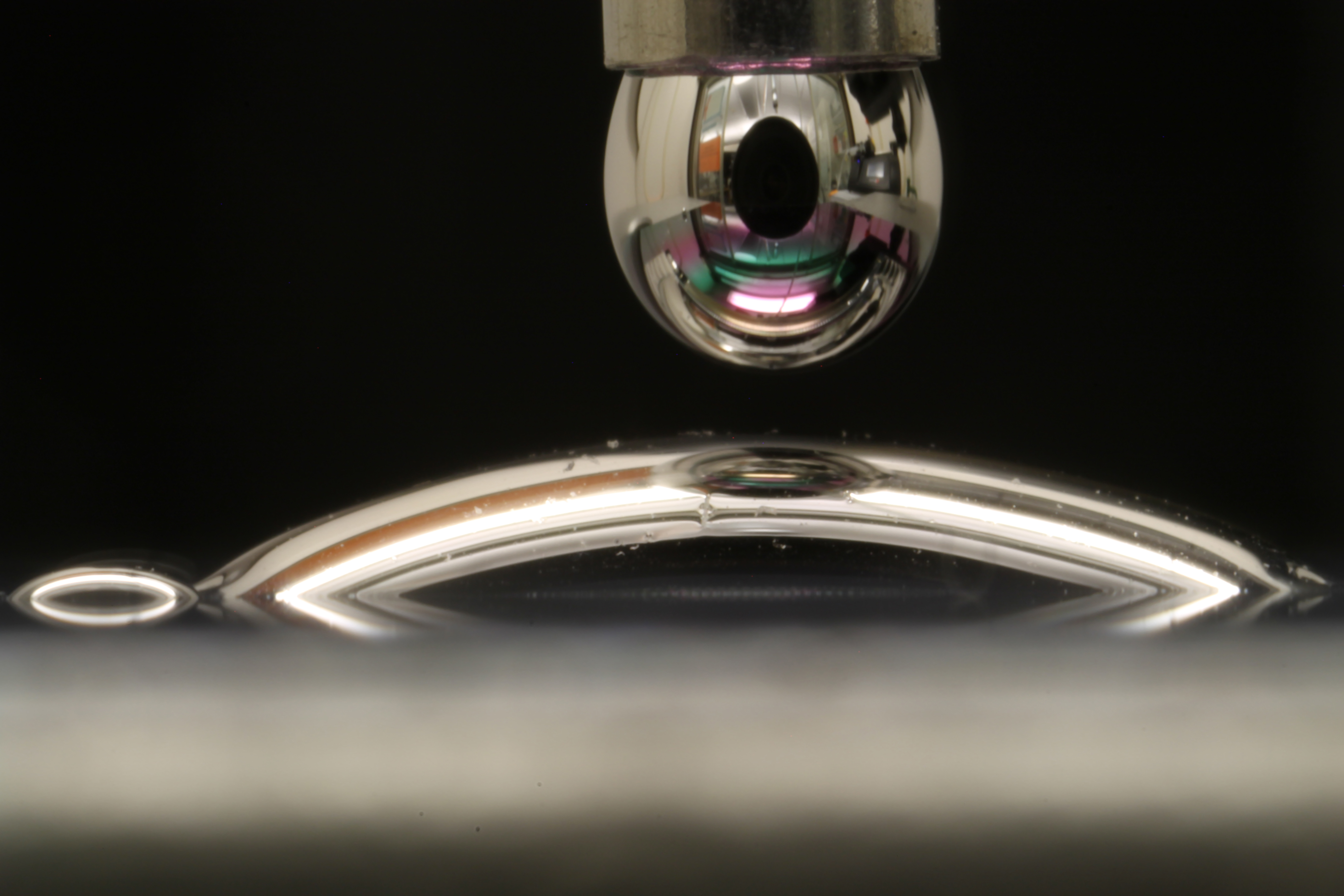
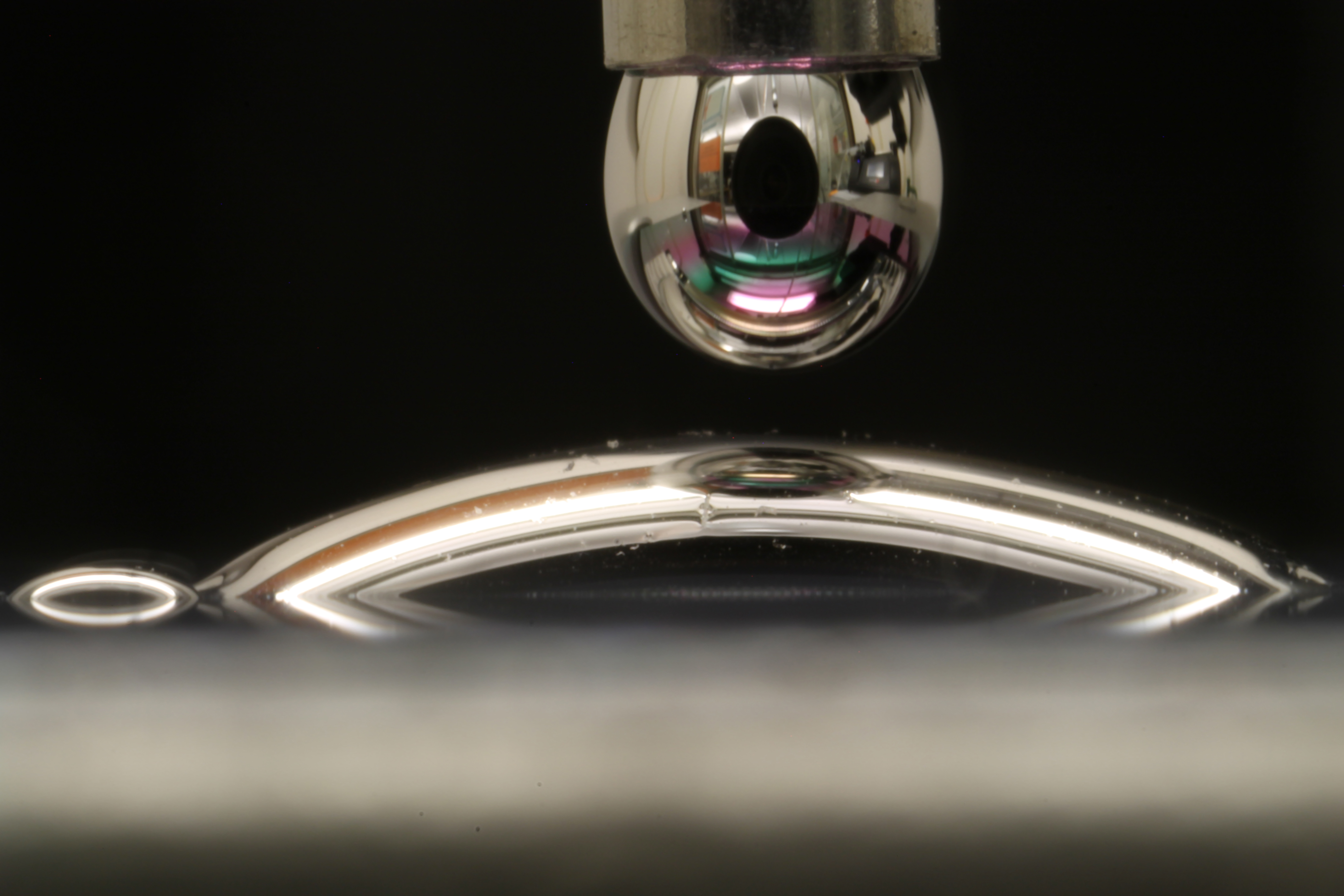