Reimagining Pressure Vessel Design
Reimagining Pressure Vessel Design
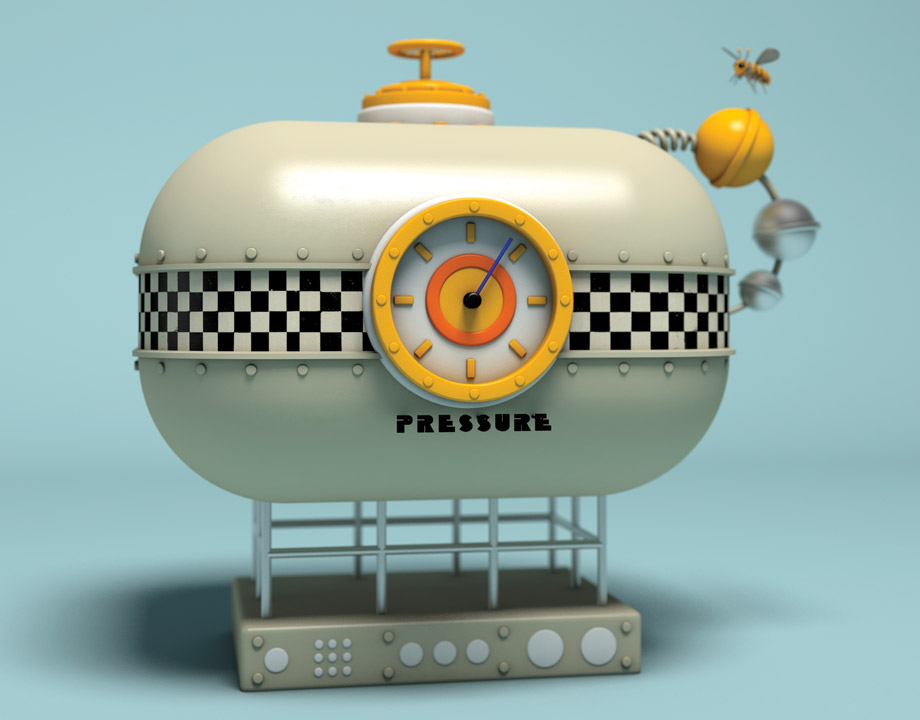
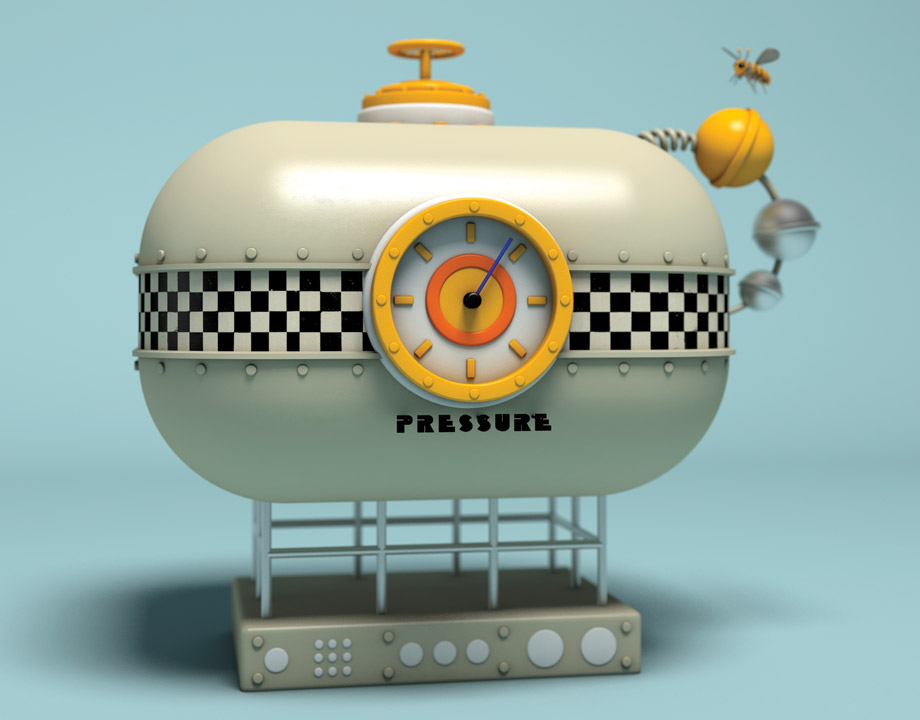
Lattice Technology redefines what a pressure vessel can look like. Image: Richard Borge
With traditional pressure vessels—which can be used to transport oil, dangerous chemicals, or compressed gases like hydrogen or oxygen—if the outer skin fails, the entire structure fails.
For carrying such potentially hazardous cargo, failure cannot be an option.
Pål Bergan and Daejun Chang from the Korean Advanced Institute of Science and Technology set out to change how pressure vessels were built, and founded Lattice Technology in 2012.
“From working in the industry, I saw that there was certainly a need for new pressure vessels,” Bergan said. “Mainly because there are so many limitations with the traditional pressure vessel technology.”
The structural integrity of traditional pressure vessels is dependent on the outer wall, and so is its size. The outer shell must grow proportionally to the pressure inside the vessel. Cost and practical production capabilities will limit how large pressure vessels can be. They typically also have a round construction, which results in poor utilization of space.
The lattice pressure vessels (LPV) developed by Bergan and Chang are completely different from any pressure vessels ever constructed. The interior of the LPVs are what one would expect a 3D-printed object to look like: They are a series of beams joined together, forming a repetitive pattern of lattices.
“If you look at lattice structures in nature, and even have lattice structures in our bones, they are light and efficient structures,” Bergan said.
From Our Archives: The History of ASME's Boiler and Pressure Vessel Code
The pressure on the outer wall is now carried by an internal structure rather than the outer skin and balanced against the opposite outer wall. The internal panel type structure efficiently carries the pressure of four walls in a box-like geometry. The repetitive internal panels provide structural redundancy such that if one internal member fails the forces will be redistributed to its neighbors.
The new design of the LPVs is for scalability in any direction. They can have any shape or size, depending on the available space or application. The design conforms to the ship rather than the ship conforming to the tank.
The secret behind this is the modular internal structure, resulting in larger tanks being just “more of the same” support structure. Thus, the LPV technology has clear advantages both for new-builds and for retrofits of transport vessels.
More on Pressure Technology: Babcock & Wilcox’s Ultra-Supercritical Boiler
Since LPVs are so flexible, this new technology is attractive for fuel tanks, bunkering vessels, cargo tanks, and storage tanks.
The first liquefied natural gas-fueled vessel for public service in South Korea was delivered to the Ulsan Port Authority. The lattice pressure vessel technology was used as containment for liquefied natural gas (LNG) fuel. The tank was designed to hold a volume of 15 m3 and a pressure of 9 bar.
To further commercialize its product, Lattice Technology was granted a $4-million research grant in June to fabricate three LPV tanks of 0.6 m3, 35 m3, and 350 m3 for LNG fuel transport.
The company's goal is to promote and facilitate the use of environmentally friendly fuels and that the design will be a paradigm shift for the containment of all sorts of pressurized gas.
Carlos M. González is special projects manager.
Learn More About Emerging Tech Awards 2019
For carrying such potentially hazardous cargo, failure cannot be an option.
Pål Bergan and Daejun Chang from the Korean Advanced Institute of Science and Technology set out to change how pressure vessels were built, and founded Lattice Technology in 2012.
“From working in the industry, I saw that there was certainly a need for new pressure vessels,” Bergan said. “Mainly because there are so many limitations with the traditional pressure vessel technology.”
The structural integrity of traditional pressure vessels is dependent on the outer wall, and so is its size. The outer shell must grow proportionally to the pressure inside the vessel. Cost and practical production capabilities will limit how large pressure vessels can be. They typically also have a round construction, which results in poor utilization of space.
The lattice pressure vessels (LPV) developed by Bergan and Chang are completely different from any pressure vessels ever constructed. The interior of the LPVs are what one would expect a 3D-printed object to look like: They are a series of beams joined together, forming a repetitive pattern of lattices.
“If you look at lattice structures in nature, and even have lattice structures in our bones, they are light and efficient structures,” Bergan said.
From Our Archives: The History of ASME's Boiler and Pressure Vessel Code
The pressure on the outer wall is now carried by an internal structure rather than the outer skin and balanced against the opposite outer wall. The internal panel type structure efficiently carries the pressure of four walls in a box-like geometry. The repetitive internal panels provide structural redundancy such that if one internal member fails the forces will be redistributed to its neighbors.
The new design of the LPVs is for scalability in any direction. They can have any shape or size, depending on the available space or application. The design conforms to the ship rather than the ship conforming to the tank.
The secret behind this is the modular internal structure, resulting in larger tanks being just “more of the same” support structure. Thus, the LPV technology has clear advantages both for new-builds and for retrofits of transport vessels.
More on Pressure Technology: Babcock & Wilcox’s Ultra-Supercritical Boiler
Since LPVs are so flexible, this new technology is attractive for fuel tanks, bunkering vessels, cargo tanks, and storage tanks.
The first liquefied natural gas-fueled vessel for public service in South Korea was delivered to the Ulsan Port Authority. The lattice pressure vessel technology was used as containment for liquefied natural gas (LNG) fuel. The tank was designed to hold a volume of 15 m3 and a pressure of 9 bar.
To further commercialize its product, Lattice Technology was granted a $4-million research grant in June to fabricate three LPV tanks of 0.6 m3, 35 m3, and 350 m3 for LNG fuel transport.
The company's goal is to promote and facilitate the use of environmentally friendly fuels and that the design will be a paradigm shift for the containment of all sorts of pressurized gas.
Carlos M. González is special projects manager.
Learn More About Emerging Tech Awards 2019
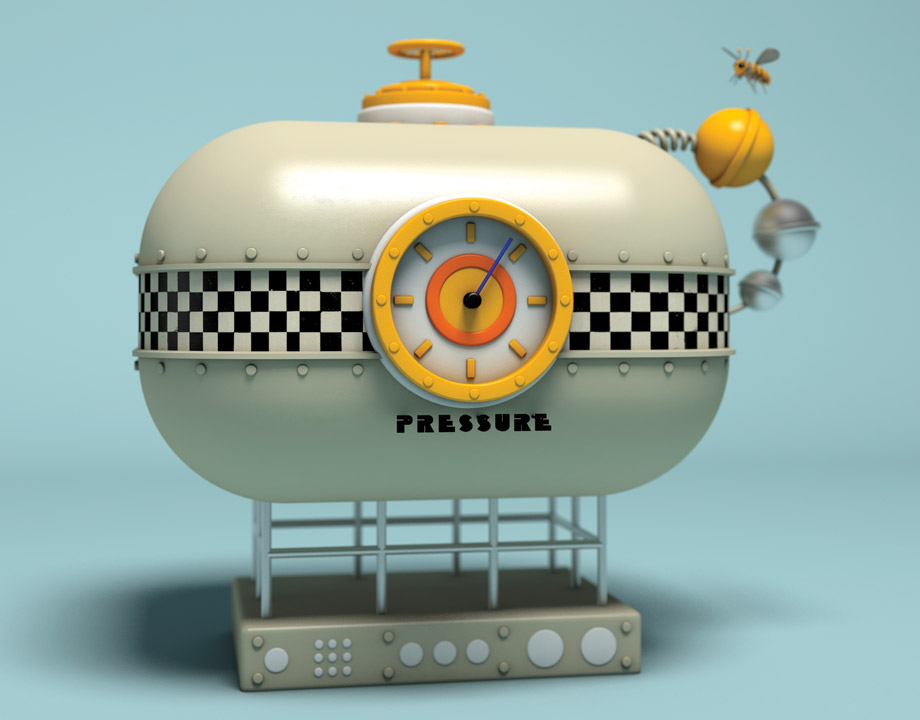
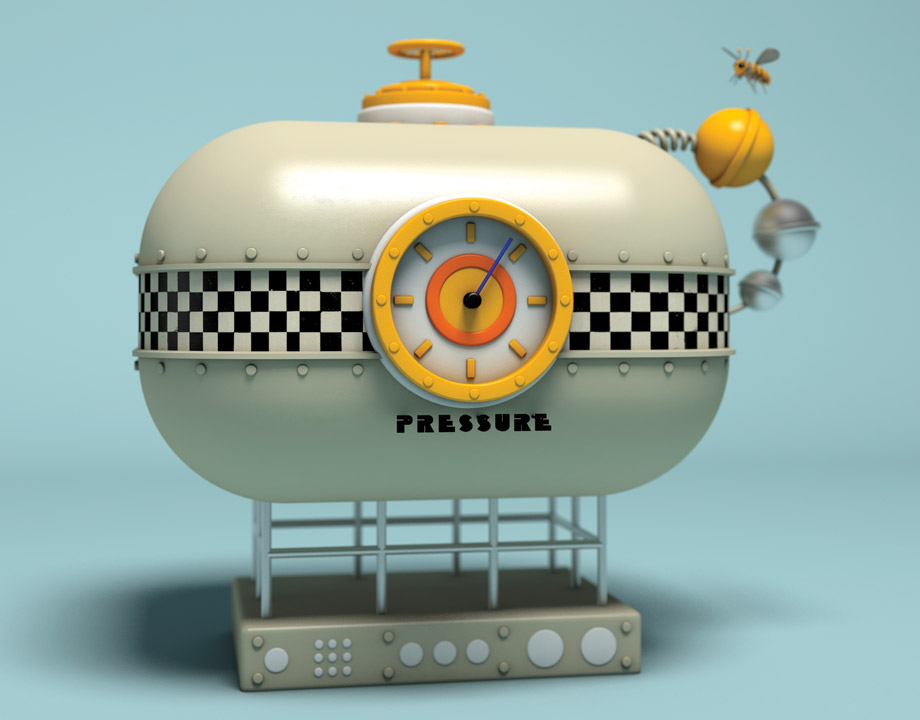