Planning is Critical to Warehouse EV Batteries and Parts
Planning is Critical to Warehouse EV Batteries and Parts
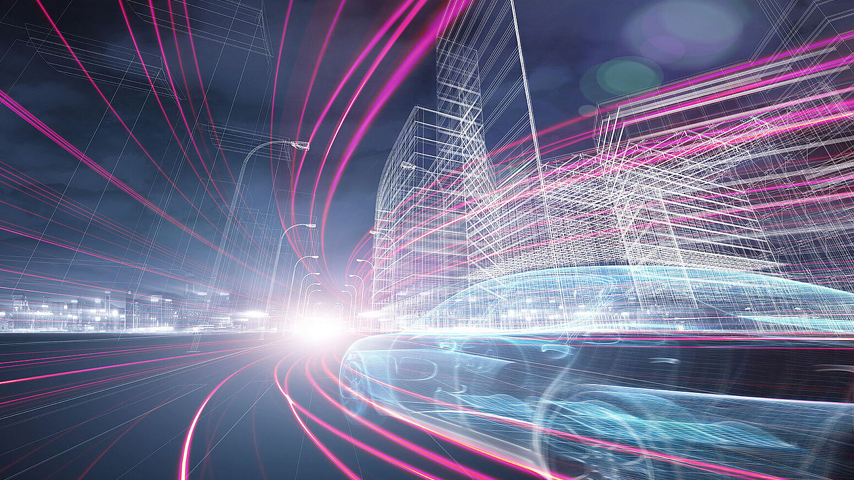
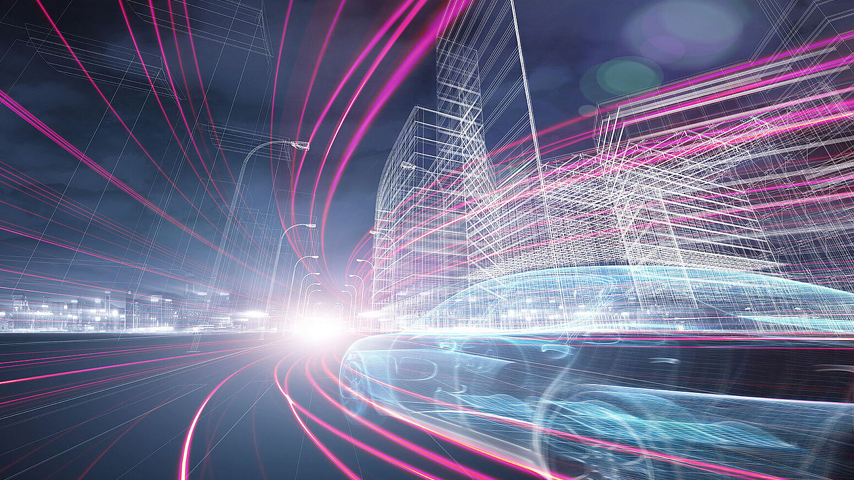
Warehousing of batteries and other EV parts requires coordination with suppliers, and detailed inhouse organization.
Production of electric vehicles (EVs) requires the careful management of various parts and components, which must be stored and organized efficiently to ensure timely and uninterrupted manufacturing. Warehousing of parts for electric vehicle production is a critical aspect of the overall supply chain and logistics management. Here are some of the key elements of warehousing for EV parts, including the role of technology, inventory management, and the importance of a well-organized and secure warehouse.
Warehouse Technologies
A critical aspect of warehousing for EV parts is the use of technology to streamline operations and enhance efficiency. Warehouse management systems can provide real-time tracking of inventory, monitor order fulfillment, and optimize warehouse layout to reduce travel time and improve order picking. Automated storage and retrieval systems can help speed up order fulfillment, reduce labor costs, and increase accuracy by using robots to manage inventory.
Inventory Management
Effective inventory management is also crucial in warehousing of parts for EV production. It is important to maintain optimal inventory levels to avoid stockouts or overstocking, both of which can lead to inefficiencies and higher costs. Just-in-time or Warehouse-On-Wheels inventory management can help reduce inventory holding costs by ordering parts only when needed by keeping certain components from having to be stored in a warehouse at all. Safety stock levels can ensure that essential components are available in case of sudden demand increases or supply chain disruptions.
Determining what components are suitable to what methods of delivery and storage is affected by a number of different factors and is a decision that must be closely aligned with customers. When dealing with EV components, especially items that hold an electrical charge, proper inventory management can be critical because many of these components must be installed with a giuaranteed minimum charge so that certain functionality tests may be performed on the vehicle during and after the assembly process.
Warehouse conditions also play a huge role in the storage of EV components. Humidity and temperature control of storage areas is much more critical for anything holding an electrical charge and may require additional investments in building structure and running cost. This is something that an experienced team must evaluate with the utmost care since it can have a huge impact on the quality and longevity of the finished vehicle.
Warehouse Safety
Safety measures such as fire suppression systems, appropriate storage of hazardous materials, and adherence to health and safety regulations are essential to protect workers and prevent accidents. Security measures such as access control, surveillance cameras, and alarm systems can help prevent theft and unauthorized access to the warehouse.
Safety standards surrounding the storage and production of EVs are still evolving as the process becomes more refined. The safety guidelines supplied by the manufacturer are critical, but additionally there are new and upcoming legislative requirements that must be researched, and occasionally predicted. These generally require the setup of much more effective fire suppression systems, evacuation plans, and locations for battery storage. Often, batteries are placed outside and away from personnel.
Storage placement in this case is critical. Chain reactions and extended burns could happen if there ever is a thermal incident with a battery unit. In the event of an incident, isolating and removing a damaged unit from the warehousing facility in a timely manner is critical to the safety of the facility and those working there. Setting up the warehouse and a defined logistics strategy can eliminate costly restructuring, but this is only possible with comprehensive knowledge of the products and their relevant trends.
Warehouse Organization
A well-organized warehouse can increase efficiency and reduce errors in order picking, leading to faster fulfillment times and improved customer satisfaction. For example, grouping similar parts together or organizing parts based on their frequency of use can help reduce travel time and increase efficiency. It is also important to maintain a clean and secure warehouse to protect the parts from damage, theft, or contamination.
Lean manufacturing concepts should be considered and implemented where applicable to help improve the process flow and organization of the facility. This is often a critical, and mostly manual, step where there is little substitute for real-world experience. Being able to visualize the flow of materials and leverage industry knowledge to predict challenges that warehouse or production associates may face is a critical skill.
Warehousing of parts for electric vehicle production is a crucial aspect of the overall supply chain and logistics management. The use of technology, effective inventory management, and a well-organized and secure warehouse can help increase efficiency, reduce costs, and improve customer satisfaction. As the demand for electric vehicles continues to grow, companies must prioritize the development of efficient and secure warehousing processes to ensure timely and uninterrupted manufacturing of EVs. It is also vital for them to have access to a team with experience and knowledge on how to overcome the challenges that now face the industry.
Jerry Nation is branch manager for ingenics.
Warehouse Technologies
A critical aspect of warehousing for EV parts is the use of technology to streamline operations and enhance efficiency. Warehouse management systems can provide real-time tracking of inventory, monitor order fulfillment, and optimize warehouse layout to reduce travel time and improve order picking. Automated storage and retrieval systems can help speed up order fulfillment, reduce labor costs, and increase accuracy by using robots to manage inventory.
Inventory Management
Effective inventory management is also crucial in warehousing of parts for EV production. It is important to maintain optimal inventory levels to avoid stockouts or overstocking, both of which can lead to inefficiencies and higher costs. Just-in-time or Warehouse-On-Wheels inventory management can help reduce inventory holding costs by ordering parts only when needed by keeping certain components from having to be stored in a warehouse at all. Safety stock levels can ensure that essential components are available in case of sudden demand increases or supply chain disruptions.
Determining what components are suitable to what methods of delivery and storage is affected by a number of different factors and is a decision that must be closely aligned with customers. When dealing with EV components, especially items that hold an electrical charge, proper inventory management can be critical because many of these components must be installed with a giuaranteed minimum charge so that certain functionality tests may be performed on the vehicle during and after the assembly process.
Warehouse conditions also play a huge role in the storage of EV components. Humidity and temperature control of storage areas is much more critical for anything holding an electrical charge and may require additional investments in building structure and running cost. This is something that an experienced team must evaluate with the utmost care since it can have a huge impact on the quality and longevity of the finished vehicle.
Warehouse Safety
Safety measures such as fire suppression systems, appropriate storage of hazardous materials, and adherence to health and safety regulations are essential to protect workers and prevent accidents. Security measures such as access control, surveillance cameras, and alarm systems can help prevent theft and unauthorized access to the warehouse.
Safety standards surrounding the storage and production of EVs are still evolving as the process becomes more refined. The safety guidelines supplied by the manufacturer are critical, but additionally there are new and upcoming legislative requirements that must be researched, and occasionally predicted. These generally require the setup of much more effective fire suppression systems, evacuation plans, and locations for battery storage. Often, batteries are placed outside and away from personnel.
Storage placement in this case is critical. Chain reactions and extended burns could happen if there ever is a thermal incident with a battery unit. In the event of an incident, isolating and removing a damaged unit from the warehousing facility in a timely manner is critical to the safety of the facility and those working there. Setting up the warehouse and a defined logistics strategy can eliminate costly restructuring, but this is only possible with comprehensive knowledge of the products and their relevant trends.
Warehouse Organization
A well-organized warehouse can increase efficiency and reduce errors in order picking, leading to faster fulfillment times and improved customer satisfaction. For example, grouping similar parts together or organizing parts based on their frequency of use can help reduce travel time and increase efficiency. It is also important to maintain a clean and secure warehouse to protect the parts from damage, theft, or contamination.
Lean manufacturing concepts should be considered and implemented where applicable to help improve the process flow and organization of the facility. This is often a critical, and mostly manual, step where there is little substitute for real-world experience. Being able to visualize the flow of materials and leverage industry knowledge to predict challenges that warehouse or production associates may face is a critical skill.
Warehousing of parts for electric vehicle production is a crucial aspect of the overall supply chain and logistics management. The use of technology, effective inventory management, and a well-organized and secure warehouse can help increase efficiency, reduce costs, and improve customer satisfaction. As the demand for electric vehicles continues to grow, companies must prioritize the development of efficient and secure warehousing processes to ensure timely and uninterrupted manufacturing of EVs. It is also vital for them to have access to a team with experience and knowledge on how to overcome the challenges that now face the industry.
Jerry Nation is branch manager for ingenics.
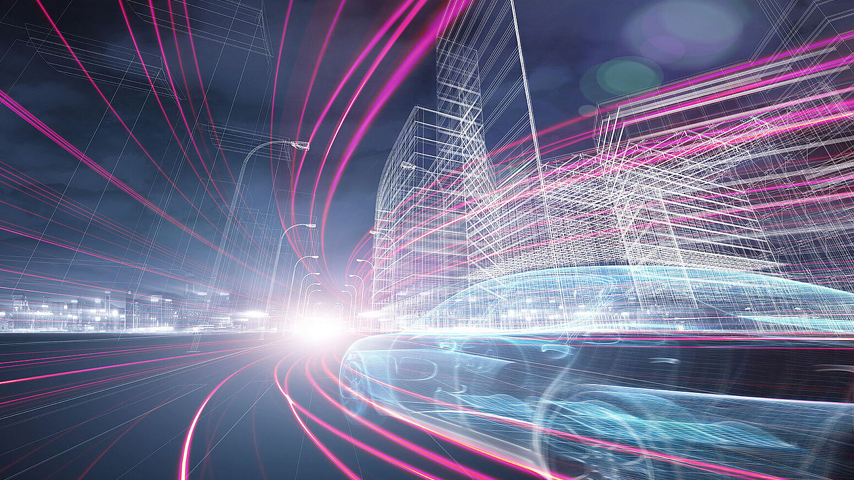
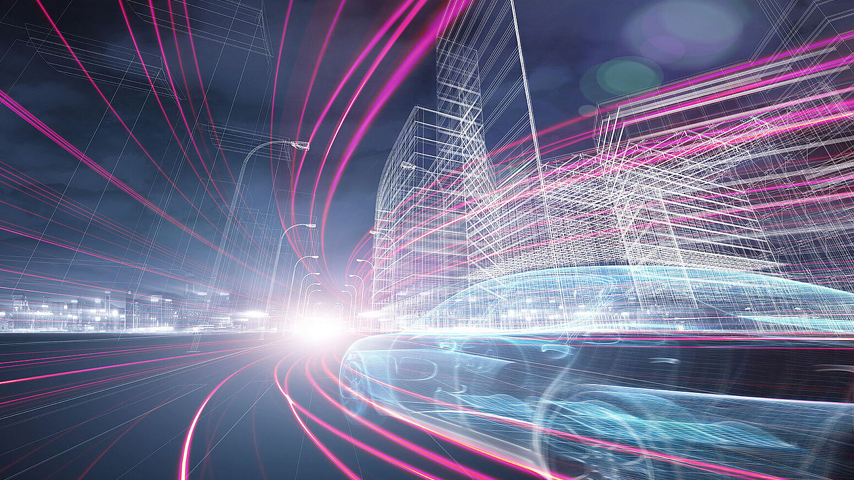