New Nanomaterial Proves Stronger Than Kevlar
New Nanomaterial Proves Stronger Than Kevlar
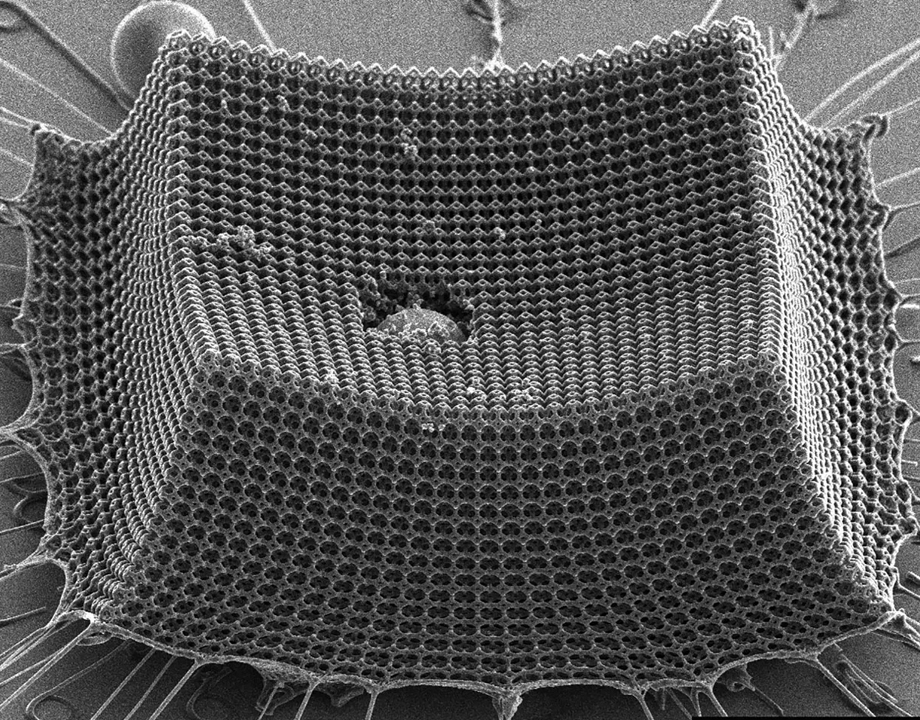
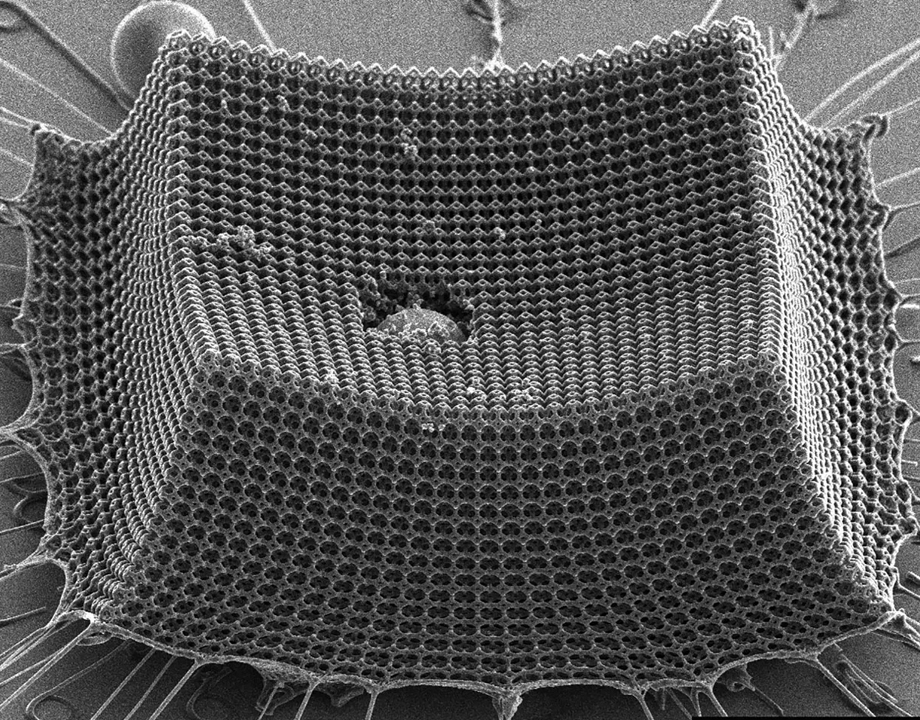
Scientists at Caltech have created a unique nano-architected material that can stop microparticles traveling at supersonic speeds, outperforming Kevlar and other protective materials.
Julia R. Greer, professor of materials science, mechanics, and medical engineering at the California Institute of Technology, has worked in the field of architected materials for much of her career, with most of her experiments conducted via quasi-static deformation (slow loads). When she first started working with carbon nano-architectures, “They always broke under quasi-static conditions, with no recoverability, damage tolerance, or really anything unusual,” she said.
Curious about how nano-architected carbon would behave in “nano-impact experiments” in a fast-deformation setting, she conducted an experiment on a material that she developed with high-speed, laser-induced projectiles. It led to surprising results.
Greer’s new material is a nano-architected material made with tiny carbon struts that proved to be strong enough to stop these nanoparticles traveling at supersonic speeds. Pound for pound, this material was more effective at stopping a projectile than Kevlar and other materials used in personal protective gear.
Greer’s Caltech team fabricated its nano-architected material with two-photon lithography, “a process that uses a fast, high-powered laser to pattern intricate, microscopic 3D architectures in polymer resins,” said Greer. “We then constructed a repeating lattice configuration composed of microscopic struts."
Making the samples for the experiments was challenging. “We knew that we wanted to test nano-architected carbon, which is made using a process called pyrolisis after the 3D lithography process,” she continued.
Similar Reading: Using Muscle to Spin Fiber
Pyrolisis is a process that burns without oxygen, which is what converts polymers and other organic materials into glassy carbon. This process also generates substantial linear and volumetric shrinkage, which made it difficult to work with. “For example, samples were no longer attached to the substrates and flew away in the furnace before we could take them out, or samples cracked, or often were simply too small to manipulate and test,” Greer said.
Once the samples were made, they were subjected to extreme deformation at the Massachusetts Institute of Technology using laser-induced particle impact tests. The technique aims an ultrafast laser through a glass slide coated with a thin film of gold, which itself is coated with a layer of micro silicon-oxide particles. As the laser passes through the slide, a plasma is generated that releases and propels silicon oxide particles toward the target.
To the team’s surprise, its nano-architected carbon was, in fact, highly impact resistant.
“We did not anticipate these results. That at velocities up to almost 1 km/s, the micro-projectiles [silicon beads] would either elastically recover or embed themselves into the material or damage it slightly and then rebound,” said Greer. “In no experiment did the projectile either penetrate through the material or transmit the shock wave onto the underlying matter. This was a big surprise for us, and we didn’t have the benefit of checking the literature because it was a first-of-its-kind experiment on a nano-architected material.”
“Our next steps are to explore the parameter space of exactly how much energy these materials can absorb under impact and to create nano-architected-based composites that would have greater resilience and toughness,” she said.
Become A Member: How to Join ASME
Possible commercial applications include designing ultra-lightweight, impact-resistant materials for use in efficient armor materials, protective coatings, blast-resistant shields desirable in defense and space applications, and other impact-mitigation needs.
Greer notes that two key obstacles for using nano- and micro-architected materials in real-world applications are the lack of scalable solutions to produce them, and the lack of in-situ diagnostics and characterization that could provide useful information for AI methods.
“We are starting to collaborate with some of the AI experts,” said Greer. “It would be tremendously exciting and beneficial to connect the design and additive manufacturing with AI-enabled intelligence.”
Mark Crawford is technology writer based in Corrales, N.M.
Curious about how nano-architected carbon would behave in “nano-impact experiments” in a fast-deformation setting, she conducted an experiment on a material that she developed with high-speed, laser-induced projectiles. It led to surprising results.
Greer’s new material is a nano-architected material made with tiny carbon struts that proved to be strong enough to stop these nanoparticles traveling at supersonic speeds. Pound for pound, this material was more effective at stopping a projectile than Kevlar and other materials used in personal protective gear.
How it works
A nano-architected material consists of patterned nanometer-scale structures that, depending on how they are arranged, can give materials unique or surprising properties, such as exceptional lightness and resilience.Greer’s Caltech team fabricated its nano-architected material with two-photon lithography, “a process that uses a fast, high-powered laser to pattern intricate, microscopic 3D architectures in polymer resins,” said Greer. “We then constructed a repeating lattice configuration composed of microscopic struts."
Making the samples for the experiments was challenging. “We knew that we wanted to test nano-architected carbon, which is made using a process called pyrolisis after the 3D lithography process,” she continued.
Similar Reading: Using Muscle to Spin Fiber
Pyrolisis is a process that burns without oxygen, which is what converts polymers and other organic materials into glassy carbon. This process also generates substantial linear and volumetric shrinkage, which made it difficult to work with. “For example, samples were no longer attached to the substrates and flew away in the furnace before we could take them out, or samples cracked, or often were simply too small to manipulate and test,” Greer said.
Once the samples were made, they were subjected to extreme deformation at the Massachusetts Institute of Technology using laser-induced particle impact tests. The technique aims an ultrafast laser through a glass slide coated with a thin film of gold, which itself is coated with a layer of micro silicon-oxide particles. As the laser passes through the slide, a plasma is generated that releases and propels silicon oxide particles toward the target.
To the team’s surprise, its nano-architected carbon was, in fact, highly impact resistant.
“We did not anticipate these results. That at velocities up to almost 1 km/s, the micro-projectiles [silicon beads] would either elastically recover or embed themselves into the material or damage it slightly and then rebound,” said Greer. “In no experiment did the projectile either penetrate through the material or transmit the shock wave onto the underlying matter. This was a big surprise for us, and we didn’t have the benefit of checking the literature because it was a first-of-its-kind experiment on a nano-architected material.”
Next steps
Greer has been contacted by several companies about the possible commercialization of this material. She and her colleague, assistant professor of applied physics Andrei Faraon, have founded their own start-up company called nFugue, which focuses on producing sheets of nano-architected materials with impact absorbing properties.“Our next steps are to explore the parameter space of exactly how much energy these materials can absorb under impact and to create nano-architected-based composites that would have greater resilience and toughness,” she said.
Become A Member: How to Join ASME
Possible commercial applications include designing ultra-lightweight, impact-resistant materials for use in efficient armor materials, protective coatings, blast-resistant shields desirable in defense and space applications, and other impact-mitigation needs.
Greer notes that two key obstacles for using nano- and micro-architected materials in real-world applications are the lack of scalable solutions to produce them, and the lack of in-situ diagnostics and characterization that could provide useful information for AI methods.
“We are starting to collaborate with some of the AI experts,” said Greer. “It would be tremendously exciting and beneficial to connect the design and additive manufacturing with AI-enabled intelligence.”
Mark Crawford is technology writer based in Corrales, N.M.
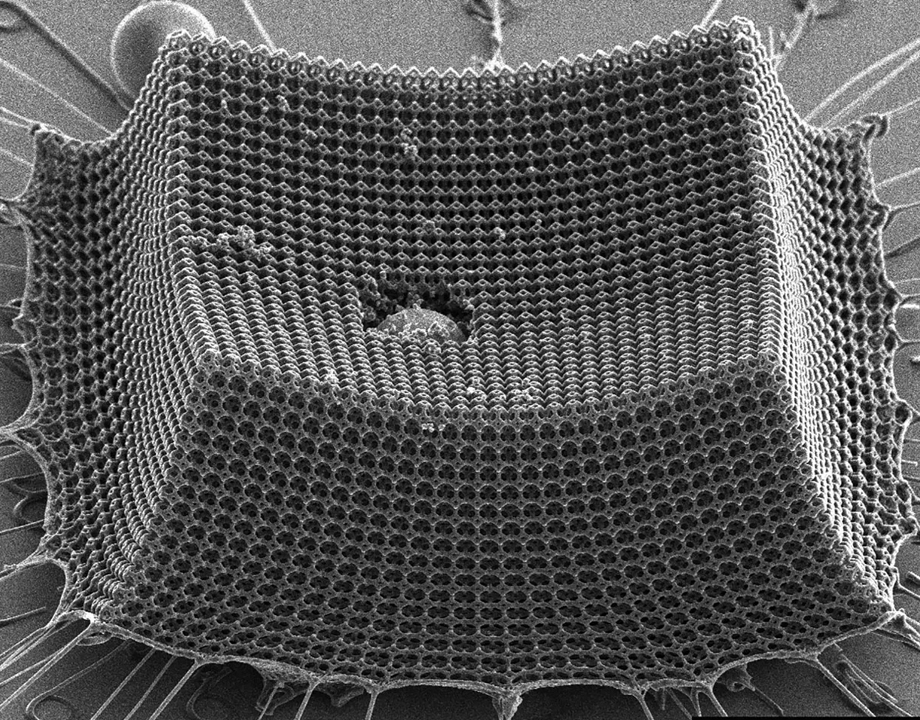
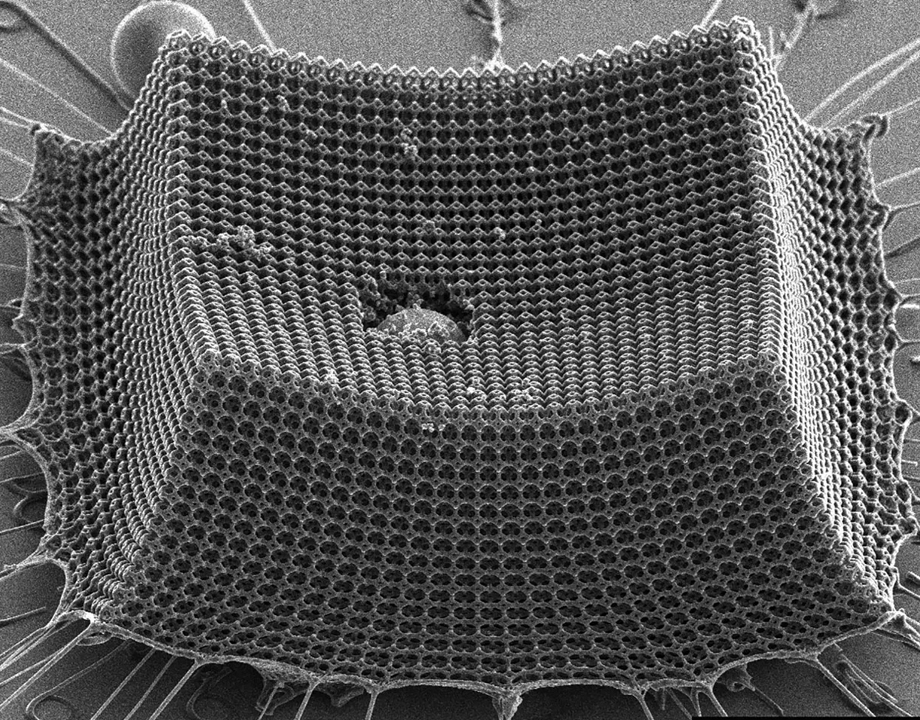