Lunar Settlements Could Be Made from Fabric
Lunar Settlements Could Be Made from Fabric
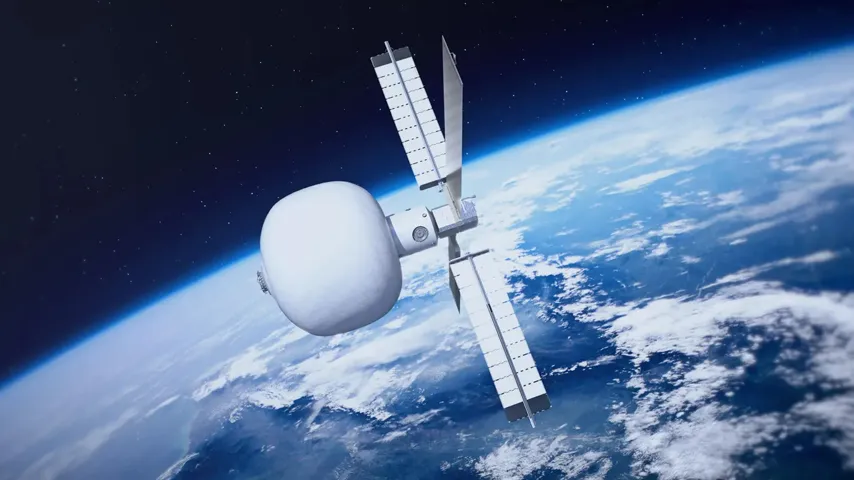
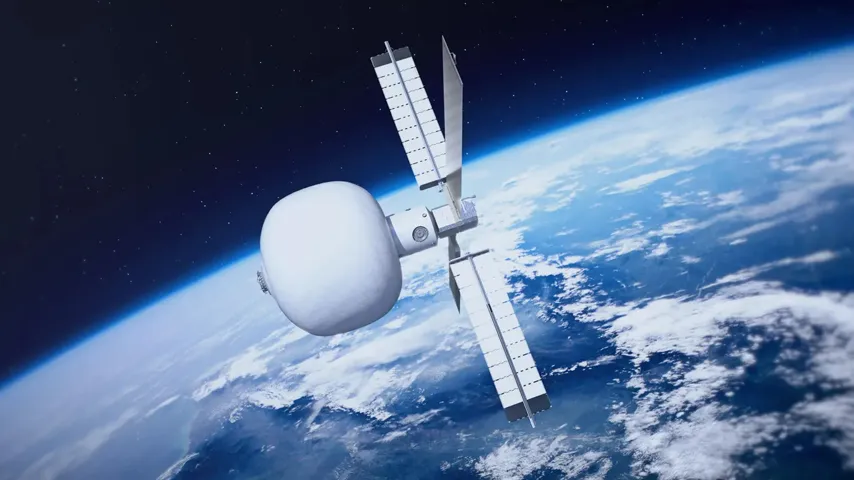
Engineers are designing inflatable habitats made from a fiber five times stronger than steel.
Space enthusiasts are drumming up interest in crewed missions to the moon and Mars, with the intent of ultimately establishing settlements for extended stays by astronauts on these bodies. The goal is to support long-term manufacturing operations that will drive the development of a lunar economy over the next 10-20 years. But anyone thinking of living on the moon or beyond knows they will need safe, spacious, long-term habitation quarters.
Lockheed Martin, the aerospace giant headquartered in Bethesda, Md., is developing innovative inflatable habitats to support these future settlements.
Compared to a habitat made of metal that must be assembled on the surface, an inflatable habitat weighs far less, takes up less room, and is easier to transport. It also offers potential for a greater area of living space, making life more comfortable and less cramped.
An inflatable structure must be built from strong, but flexible material, and according to Uy Duong, habitation chief engineer at Lockheed Martin, the material of choice is Vectran.
“Vectran is a high-performance multifilament yarn spun from liquid crystal polymer,” Duong said. “The fiber is five times stronger than steel, 10 times stronger than aluminum, and offers a unique combination of outstanding properties. It is the fiber of choice where others fail to meet performance requirements.”
In addition, Duong said, the Kevlar-like yarn offers thermal and dimensional stability, low moisture absorption, and electrical insulation. It is also believed that constructing a habitat from a polymer rather than metal will better shield astronauts from radiation and provide improved resistance to leaks and micro-debris impacts.
The Lockheed Martin technology for developing this habitat is derived largely from the research and development conducted for Transhab, NASA’s module that was added to the International Space Station in 2004.
Even with 20 years of experience with inflatable habitats in space, there is much to learn before deploying such a structure on the moon or Mars. For instance, engineers do not have a full understanding of Vectran’s creep performance—the ability to maintain performance capabilities under load over an extended lifetime.
“It is difficult to perform ‘accelerated’ creep testing on Vectran material by testing at elevated temperatures. Much of the life predictions of Vectran rely on longer-term testing and extrapolation based on elevated load testing,” said Tyler Muma, softgoods technology development lead at Lockheed Martin. “NASA has led the way with significant material testing to increase the creep life understanding of Vectran, and Lockheed Martin has also invested in significant testing to increase that knowledge.”
That in-house research has pushed the boundaries of material science, Muma said.
“We have discovered that creep behavior of textiles is far different than that of metallic structures. Textiles can exhibit creep behavior at significantly lower loads than metallics,” he said. “We have developed an intimate understanding of this behavior and have come up with innovative manufacturing processes and a habitat deployment sequence that address concerns with creep behavior and lead to more repeatable and reliable performance of our habitat.”
Habitable structures in space—whether in orbit or on the surface of a body with little or no atmosphere—are pressure vessels, though not the sort that most mechanical engineers encounter in their work.
More on Aerospace: Space Station Could Bring Weight to the Weightless
“When mechanical engineers think about pressure vessels, they likely envision a rigid metallic cylinder with domed ends,” Muma said. “The interesting thing about what we’re doing is that it redefines the architecture of a pressure vessel, the way in which they are made, and applications for which they can be used. Our space habitats are essentially pressure vessels with flexible textile walls that can be folded and packed into a very small volume for launch, then deployed on orbit to make use of far more internal volume than would be offered by an equivalent-mass metallic pressure vessel.”
Of course, not everything can be flexible—bulkhead hatches and viewports are made from strong solids than can be airtight—so creating an interface between all these various materials requires planning. “It presents unique challenges and opportunities to design interface geometries that can change from a packed state through different inflation pressures, along with interfaces featuring materials with drastically different strain properties,” Muma said.
While Mars settlements are decades away and the Artemis II mission to the moon has been delayed to 2025 at the earliest, work on inflatable habitats is continuing at a rapid pace.
“Our development schedule is in sync with both NASA and commercial space opportunities,” Duong said. He added that there are significant development and test activities planned for later this year.
Mark Crawford is a technology writer in Corrales, N.M.
Lockheed Martin, the aerospace giant headquartered in Bethesda, Md., is developing innovative inflatable habitats to support these future settlements.
Compared to a habitat made of metal that must be assembled on the surface, an inflatable habitat weighs far less, takes up less room, and is easier to transport. It also offers potential for a greater area of living space, making life more comfortable and less cramped.
An inflatable structure must be built from strong, but flexible material, and according to Uy Duong, habitation chief engineer at Lockheed Martin, the material of choice is Vectran.
“Vectran is a high-performance multifilament yarn spun from liquid crystal polymer,” Duong said. “The fiber is five times stronger than steel, 10 times stronger than aluminum, and offers a unique combination of outstanding properties. It is the fiber of choice where others fail to meet performance requirements.”
In addition, Duong said, the Kevlar-like yarn offers thermal and dimensional stability, low moisture absorption, and electrical insulation. It is also believed that constructing a habitat from a polymer rather than metal will better shield astronauts from radiation and provide improved resistance to leaks and micro-debris impacts.
The Lockheed Martin technology for developing this habitat is derived largely from the research and development conducted for Transhab, NASA’s module that was added to the International Space Station in 2004.
Even with 20 years of experience with inflatable habitats in space, there is much to learn before deploying such a structure on the moon or Mars. For instance, engineers do not have a full understanding of Vectran’s creep performance—the ability to maintain performance capabilities under load over an extended lifetime.
“It is difficult to perform ‘accelerated’ creep testing on Vectran material by testing at elevated temperatures. Much of the life predictions of Vectran rely on longer-term testing and extrapolation based on elevated load testing,” said Tyler Muma, softgoods technology development lead at Lockheed Martin. “NASA has led the way with significant material testing to increase the creep life understanding of Vectran, and Lockheed Martin has also invested in significant testing to increase that knowledge.”
That in-house research has pushed the boundaries of material science, Muma said.
“We have discovered that creep behavior of textiles is far different than that of metallic structures. Textiles can exhibit creep behavior at significantly lower loads than metallics,” he said. “We have developed an intimate understanding of this behavior and have come up with innovative manufacturing processes and a habitat deployment sequence that address concerns with creep behavior and lead to more repeatable and reliable performance of our habitat.”
Habitable structures in space—whether in orbit or on the surface of a body with little or no atmosphere—are pressure vessels, though not the sort that most mechanical engineers encounter in their work.
More on Aerospace: Space Station Could Bring Weight to the Weightless
“When mechanical engineers think about pressure vessels, they likely envision a rigid metallic cylinder with domed ends,” Muma said. “The interesting thing about what we’re doing is that it redefines the architecture of a pressure vessel, the way in which they are made, and applications for which they can be used. Our space habitats are essentially pressure vessels with flexible textile walls that can be folded and packed into a very small volume for launch, then deployed on orbit to make use of far more internal volume than would be offered by an equivalent-mass metallic pressure vessel.”
Of course, not everything can be flexible—bulkhead hatches and viewports are made from strong solids than can be airtight—so creating an interface between all these various materials requires planning. “It presents unique challenges and opportunities to design interface geometries that can change from a packed state through different inflation pressures, along with interfaces featuring materials with drastically different strain properties,” Muma said.
While Mars settlements are decades away and the Artemis II mission to the moon has been delayed to 2025 at the earliest, work on inflatable habitats is continuing at a rapid pace.
“Our development schedule is in sync with both NASA and commercial space opportunities,” Duong said. He added that there are significant development and test activities planned for later this year.
Mark Crawford is a technology writer in Corrales, N.M.
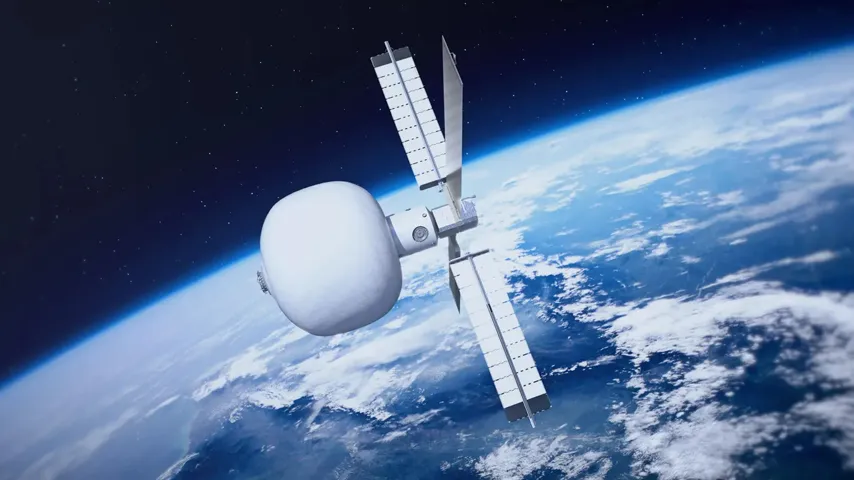
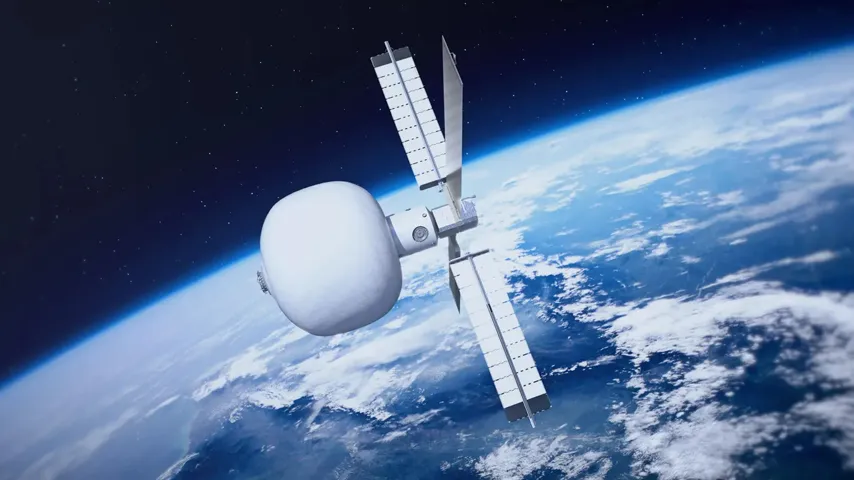