Implanted Medical Devices Depend on Bioresorbable Materials
Implanted Medical Devices Depend on Bioresorbable Materials
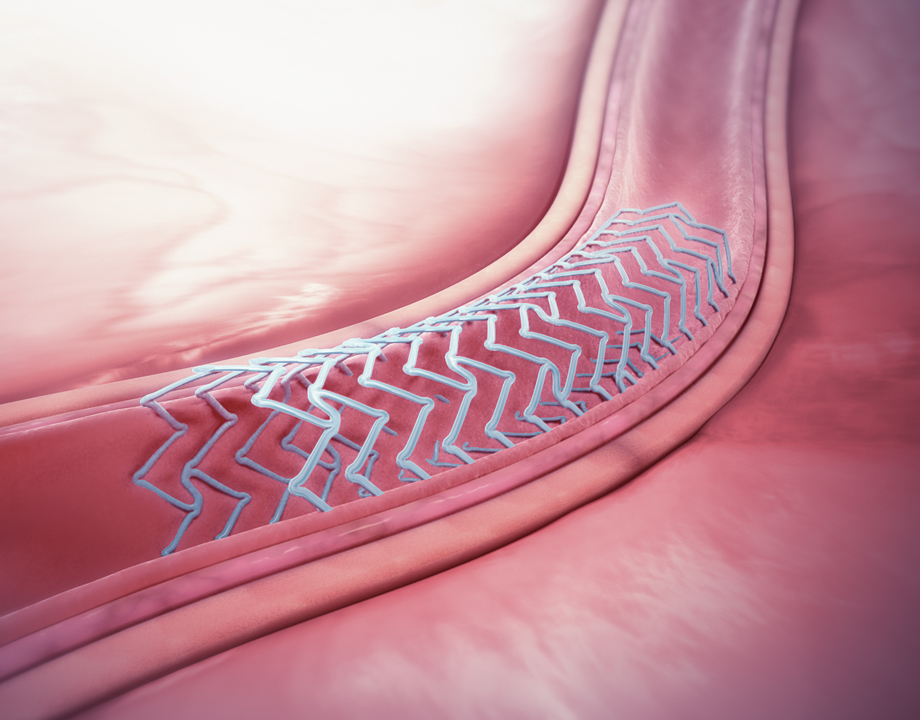
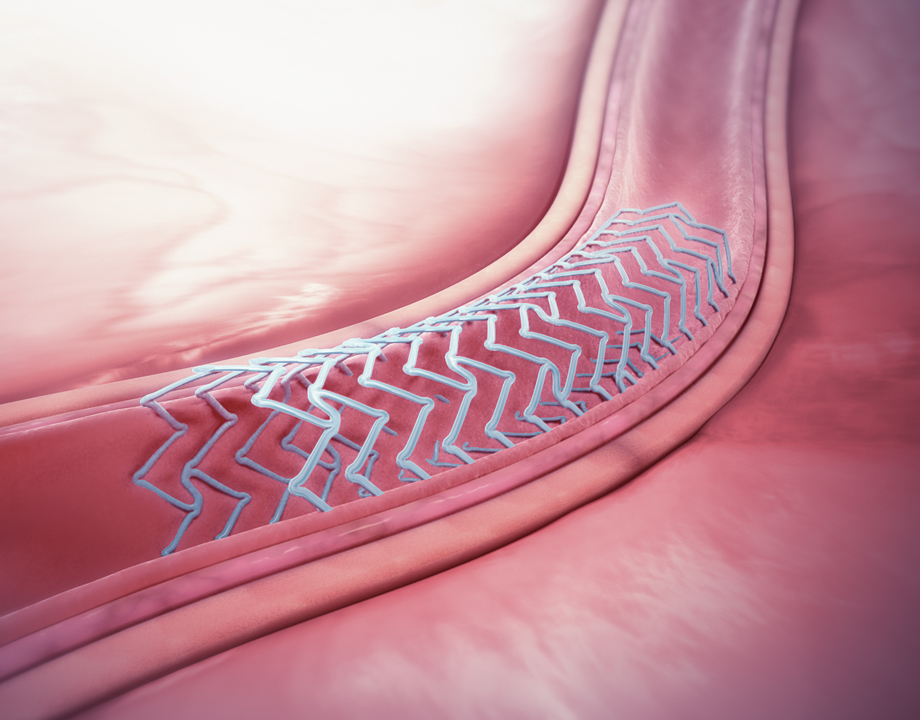
A bioresorbable stent uses biodegradable mesh that dissolves in the body.
Medical device innovation continues to generate highly complex medical devices that often rely on new or advanced materials. One group of materials that is growing in popularity is bioresorbable polymers, used to make products that, when implanted into the body, gradually dissolve at a pre-determined rate through the process of hydrolysis and are safely assimilated.
The big advantage of medical devices made from bioresorbable polymers is, at the end of their intended service, they simply dissolve and do not require a second surgery to be removed. For example, children often outgrow pediatric medical devices, thus requiring an additional surgery to remove them. However, a bioresorbable device will break down gradually and be absorbed by the body. Bioresorbables can also be engineered to enhance bone growth and repel bacteria and infection.
Bioresorbable devices are manufactured from a wide range of natural or synthetic polymers and some metals, such as magnesium. Popular bioresorbable polymers include PLLA and PLA-like derivatives. Other common materials are TPU, PC, ABS, PSU, and PPSU.
Bioresorbable polymers are sensitive materials that need to be processed with care to avoid any structural or chemical degradation that could impact their performance. These materials are especially susceptible to environmental factors that arise during manufacturing.
“For example, application of too much heat during the injection-molding process, or exposing the material to heat over too long a time, can degrade long-term performance of the material,” said Robert Schwenker, vice president of sales, specialty molding, and medical tubing for Spectrum Plastics Group.
Likewise, materials can also be easily damaged by improper handling, exposure to moisture, or improper storage. Failure to maintain quality control can lead to a lower molecular weight and reduced strength, undermining the part’s stability and longevity.
Because bioresorbable polymers have very high viscosity, excessive shear can destroy the integrity of the material during processing, noted Schwenker.
Watch Our Video: Bioinspired Breakthroughs Transform Medical Devices
“Even for mold design, design engineers must understand how the product behaves throughout the runner system. Therefore the entire molding process must be carried out in a controlled environment [possibly cleanroom] that is managed by a robust quality system.”
For environmental and sustainability reasons, biomaterials are also a good choice over standard plastics because they break down much more easily.
The key benefit of a bioresorbable product is that it will eventually be absorbed into the patient. The targeted absorption rate—whether it is 12 months or four years—is often the primary factor and depends on the application. The actual geometry of a part plays a critical role as well.
“Spectrum has developed laser processing technology to drill micro-ports into components to help create a porous framework that will allow for more consistent absorption, without damaging overall strength,” said Schwenker.
Bioresorbable materials are used to create micro-scale medical devices, often for soft tissue applications. Key considerations include strength requirements, tissue reactivity, absorption rate, and additives that enhance certain functions or qualities, such as antimicrobial.
Medical applications include:
New materials and manufacturing technologies like additive manufacturing and laser processing are changing the manufacturing landscape rapidly.
“Although the medical device industry tends to resist change, these new capabilities are also driving a renewed sense of innovation,” said Schwenker. This includes bioresorbable materials, he noted, which will be at the forefront of creative engineering and design for implantable medical devices for years to come.
Mark Crawford is a science and technology writer in Corrales, N.M.
The big advantage of medical devices made from bioresorbable polymers is, at the end of their intended service, they simply dissolve and do not require a second surgery to be removed. For example, children often outgrow pediatric medical devices, thus requiring an additional surgery to remove them. However, a bioresorbable device will break down gradually and be absorbed by the body. Bioresorbables can also be engineered to enhance bone growth and repel bacteria and infection.
Bioresorbable devices are manufactured from a wide range of natural or synthetic polymers and some metals, such as magnesium. Popular bioresorbable polymers include PLLA and PLA-like derivatives. Other common materials are TPU, PC, ABS, PSU, and PPSU.
Bioresorbable polymers are sensitive materials that need to be processed with care to avoid any structural or chemical degradation that could impact their performance. These materials are especially susceptible to environmental factors that arise during manufacturing.
“For example, application of too much heat during the injection-molding process, or exposing the material to heat over too long a time, can degrade long-term performance of the material,” said Robert Schwenker, vice president of sales, specialty molding, and medical tubing for Spectrum Plastics Group.
Likewise, materials can also be easily damaged by improper handling, exposure to moisture, or improper storage. Failure to maintain quality control can lead to a lower molecular weight and reduced strength, undermining the part’s stability and longevity.
Because bioresorbable polymers have very high viscosity, excessive shear can destroy the integrity of the material during processing, noted Schwenker.
Watch Our Video: Bioinspired Breakthroughs Transform Medical Devices
“Even for mold design, design engineers must understand how the product behaves throughout the runner system. Therefore the entire molding process must be carried out in a controlled environment [possibly cleanroom] that is managed by a robust quality system.”
For environmental and sustainability reasons, biomaterials are also a good choice over standard plastics because they break down much more easily.
The key benefit of a bioresorbable product is that it will eventually be absorbed into the patient. The targeted absorption rate—whether it is 12 months or four years—is often the primary factor and depends on the application. The actual geometry of a part plays a critical role as well.
“Spectrum has developed laser processing technology to drill micro-ports into components to help create a porous framework that will allow for more consistent absorption, without damaging overall strength,” said Schwenker.
Bioresorbable materials are used to create micro-scale medical devices, often for soft tissue applications. Key considerations include strength requirements, tissue reactivity, absorption rate, and additives that enhance certain functions or qualities, such as antimicrobial.
Medical applications include:
- Stent-like couplers that can hold the ends of an artery securely in place, providing a support structure for vascular surgery.
- Scaffolds that provide a framework for tissue or bone growth or that open occluded arteries to restore blood flow and deliver medication.
- ·Delivery systems for the timed release of medication—once the course of treatment has been completed, the delivery system is reabsorbed by the body.
- Pediatric medical devices that dissolve over time after implantation and healing, which allows normal bone and tissue growth as the child ages.
- Bioresorbable surgical screws and plates, for example, used to hold a compound fracture in place during surgery and healing, but not needed after the bone is completely healed.
- Bioresorbable electronics. Researchers have designed an implantable bioresorbable-based wireless device that can send out short spikes of electricity to restore circulation and stimulate damaged peripheral nerves.
- Optics. Scientists at the Institute of Electronic Structure and Laser (IESL) at the Foundation of Research and Technology in Greece have created bioresorbable optical devices made with biocompatible magnesium, calcium, silicon, and sodium that can be used to monitor bone healing, medicine utilization, or organ health.
- Wound dressings made from hydrogel materials, bioresorbable wound dressings do not need to be replaced and are charged with antimicrobial particles, such as silver zeolites.
New materials and manufacturing technologies like additive manufacturing and laser processing are changing the manufacturing landscape rapidly.
“Although the medical device industry tends to resist change, these new capabilities are also driving a renewed sense of innovation,” said Schwenker. This includes bioresorbable materials, he noted, which will be at the forefront of creative engineering and design for implantable medical devices for years to come.
Mark Crawford is a science and technology writer in Corrales, N.M.
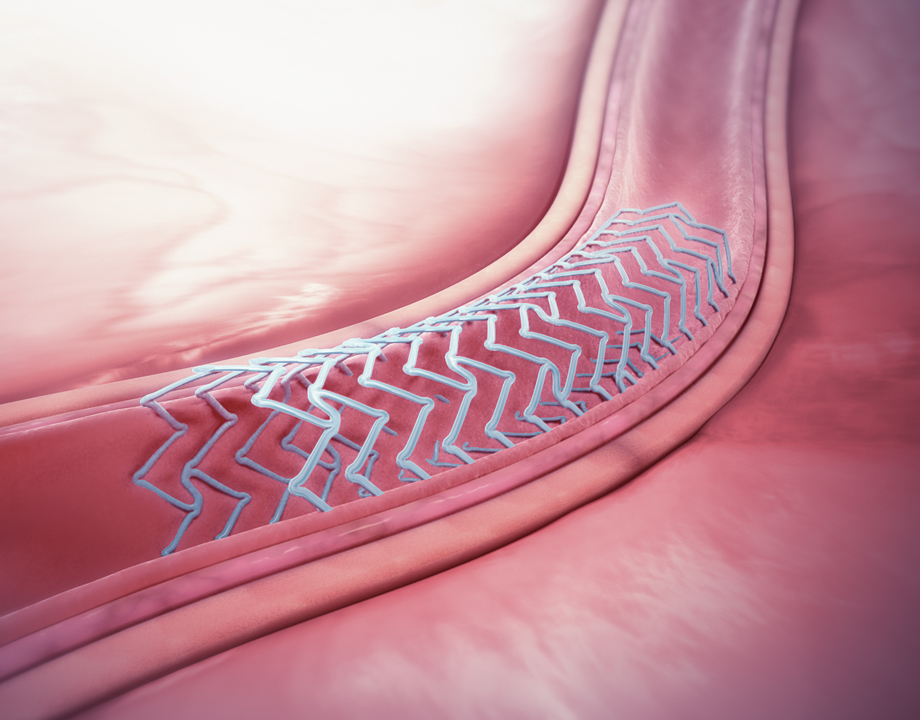
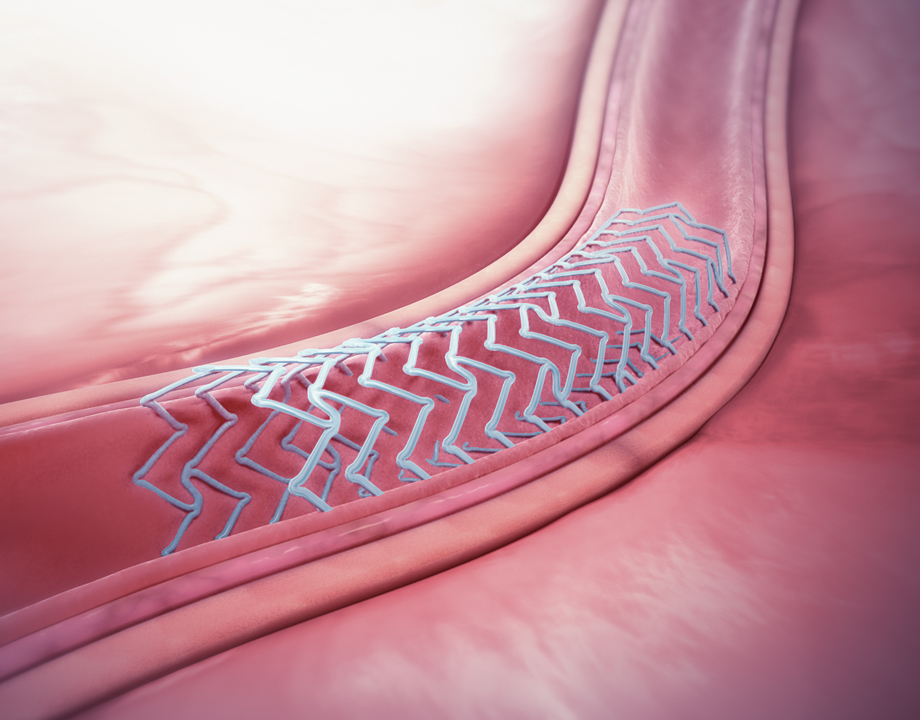