Clean Combustion: Trapping Carbon Emissions
Clean Combustion: Trapping Carbon Emissions
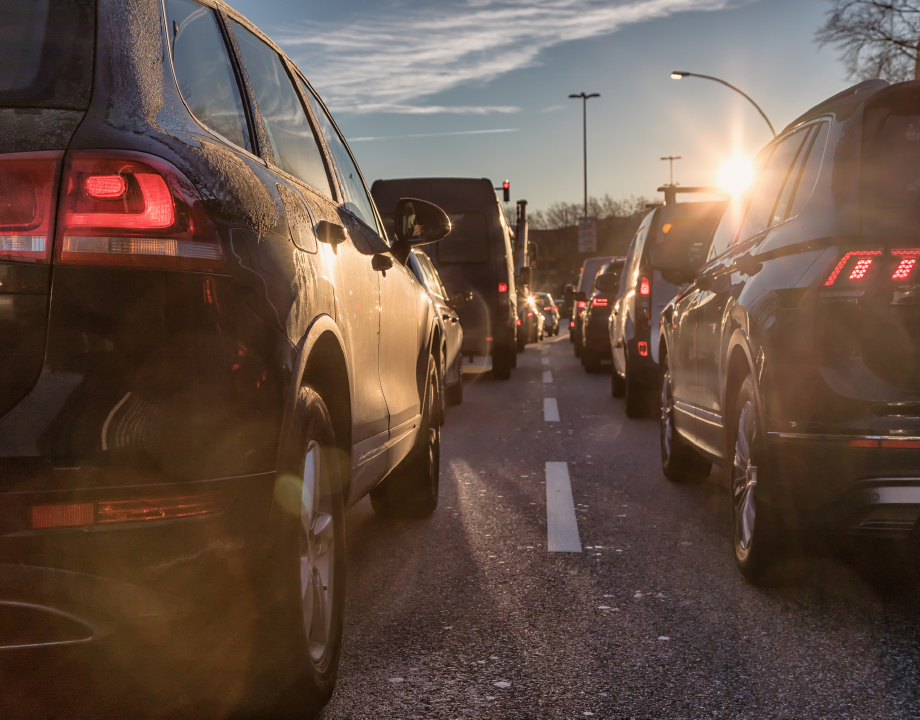
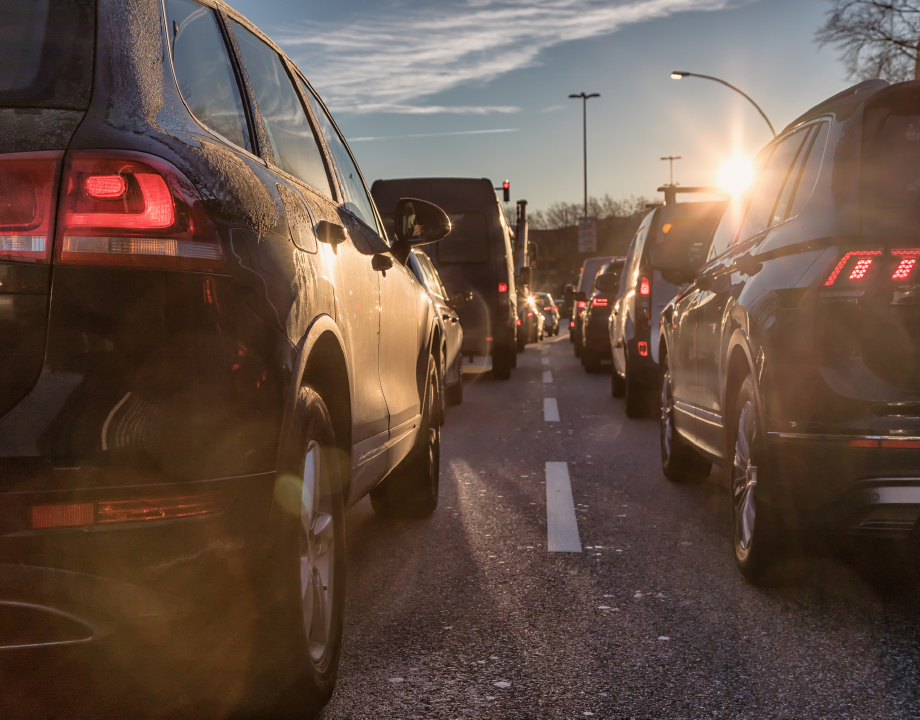
New engine design eliminates greenhouse gases from exhaust pipes.
Though governments are tightening their emissions standards, trucks, trains, and ships aren’t going away. They have a vital role in the supply chain.
Acknowledging this, researchers from Spain’s Polytechnic University of Valencia (VPU) have designed an internal combustion engine that doesn’t emit damaging gases or carbon dioxide. So far, the oxycombustion engine is also highly efficient and complies with the European Union’s upcoming emissions regulations.
The engine will come at the right time, as regulations are stricter than ever.
As part of the Paris Agreement, the European Union aims to be climate-neutral by 2040, eliminating greenhouse gas emissions. The United States is also seeing the push toward zero emissions. In August, the California Air Resources Board and major automakers finalized an agreement to cut vehicle emissions in the state. The agreement with carmakers includes Ford Motor Co, Volkswagen, Honda, and BMW.
Due to its size, the VPU engine can only be used for large vehicles used for carrying goods, mostly diesel-powered tractor-trailers, ships, or trains. The developers also believe there could be applications for airplanes and for stationary power units, said Francisco José Arnau Martínez, an associate professor at the university and a member of the team developing the oxy-combustion engine.
Editor's Pick: Infographic: Looking for Capturable Carbon
Developers of the engine liken it to electric vehicle engines because of its clean combustion. They claim it can operate autonomously and will not emit any greenhouse gases, including carbon dioxide and nitrogen oxide, two of the biggest contributors to smog and climate change. The exhaust is simply water vapor.
“Our technology combines the best of both types of engines, electric and combustion,” said Luis Miguel García-Cuevas González, a researcher in CMT-Thermal Motors, a VPU research center in Valencia. He and his colleagues are now building prototypes of the engine.
Because the engine can operate on fossil fuels, biofuel or synthetic fuels, it won’t require a dramatic change to the way fuel is provided,” Martinez said.
Many components of the researcher’s newly designed engine are the same as in traditional combustion engines, including turbochargers, coolers, and valves. The key to the new technology is a mixed ionic-electronic conducting (MIEC) ceramic membrane module, Martinez said.
The design for the VPU engine is made up of two vessels, with the membrane placed between them as a filter. “Inside the vehicle, we have a tank for fuel and another for the carbon dioxide generated after burning the fuel,” García-Cuevas said. The carbon dioxide is filtered out, condensed, and stored in one of the tanks.
“We could draw value from the pure, high-quality carbon dioxide,” García-Cuevas said. “It could be sold at a service station or for industrial use.”
The separation happens when oxygen ions are diffused through crystalline ceramic at high temperature. It’s driven by the difference of oxygen’s partial pressure across the membrane, Martinez said.
Reader's Choice: Energy Blog: Trading One Crisis for Another
In other words, the MIEC separates the oxygen from nitrogen and other air components before introducing it into the cylinders, generating a pure combustion gas. The oxygen is burned and the technology captures and liquifies the carbon dioxide the engine generates, Martinez said. Eliminating nitrogen before combustion precludes the formation of nitrogen oxide.
Preferred operating temperatures are between 1,700 and 1,800 degrees F with a high-pressure drop between the feed and the permeate for a pressure ratio between four and six.
“From the point of view of the engine architecture, the main difference is the presence of the MIEC membrane,” said Martinez. “The rest of the elements used can be generally found in traditional engines. Moreover, the need to use after-treatment devices is highly reduced. From an operational point of view, the only difference is in the exhaust gas. This gas does not contain nitrogen oxides, and it is composed mainly of vapor water and CO2. In case that the CO2 is captured, only water is delivered to the atmosphere.”
More for You: Energy Blog: Time Is Energy
Once the prototype is built, it will be tested in an engine test bench in order to demonstrate its performance at different operating points.
After they’ve perfected the large engines, the researchers believe they can make adjustments so it can be used in automobiles.
“In the case of smaller vehicles, it could also be applied by sequestering only part of the carbon dioxide in the exhaust,” said Francisco José Arnau, a fellow researcher at the CMT-Thermal Motors.
Imagine being trapped in slow-moving traffic behind a tractor-trailer. Now imagine it without the smell of diesel exhaust permeating your car. That’s what these researchers are going for: a world free of diesel fumes.
Jean Thilmany is a technology writer based in Saint Paul, Minn.
Acknowledging this, researchers from Spain’s Polytechnic University of Valencia (VPU) have designed an internal combustion engine that doesn’t emit damaging gases or carbon dioxide. So far, the oxycombustion engine is also highly efficient and complies with the European Union’s upcoming emissions regulations.
The engine will come at the right time, as regulations are stricter than ever.
As part of the Paris Agreement, the European Union aims to be climate-neutral by 2040, eliminating greenhouse gas emissions. The United States is also seeing the push toward zero emissions. In August, the California Air Resources Board and major automakers finalized an agreement to cut vehicle emissions in the state. The agreement with carmakers includes Ford Motor Co, Volkswagen, Honda, and BMW.
Due to its size, the VPU engine can only be used for large vehicles used for carrying goods, mostly diesel-powered tractor-trailers, ships, or trains. The developers also believe there could be applications for airplanes and for stationary power units, said Francisco José Arnau Martínez, an associate professor at the university and a member of the team developing the oxy-combustion engine.
Editor's Pick: Infographic: Looking for Capturable Carbon
Developers of the engine liken it to electric vehicle engines because of its clean combustion. They claim it can operate autonomously and will not emit any greenhouse gases, including carbon dioxide and nitrogen oxide, two of the biggest contributors to smog and climate change. The exhaust is simply water vapor.
“Our technology combines the best of both types of engines, electric and combustion,” said Luis Miguel García-Cuevas González, a researcher in CMT-Thermal Motors, a VPU research center in Valencia. He and his colleagues are now building prototypes of the engine.
Because the engine can operate on fossil fuels, biofuel or synthetic fuels, it won’t require a dramatic change to the way fuel is provided,” Martinez said.
Many components of the researcher’s newly designed engine are the same as in traditional combustion engines, including turbochargers, coolers, and valves. The key to the new technology is a mixed ionic-electronic conducting (MIEC) ceramic membrane module, Martinez said.
The design for the VPU engine is made up of two vessels, with the membrane placed between them as a filter. “Inside the vehicle, we have a tank for fuel and another for the carbon dioxide generated after burning the fuel,” García-Cuevas said. The carbon dioxide is filtered out, condensed, and stored in one of the tanks.
“We could draw value from the pure, high-quality carbon dioxide,” García-Cuevas said. “It could be sold at a service station or for industrial use.”
The separation happens when oxygen ions are diffused through crystalline ceramic at high temperature. It’s driven by the difference of oxygen’s partial pressure across the membrane, Martinez said.
Reader's Choice: Energy Blog: Trading One Crisis for Another
In other words, the MIEC separates the oxygen from nitrogen and other air components before introducing it into the cylinders, generating a pure combustion gas. The oxygen is burned and the technology captures and liquifies the carbon dioxide the engine generates, Martinez said. Eliminating nitrogen before combustion precludes the formation of nitrogen oxide.
Preferred operating temperatures are between 1,700 and 1,800 degrees F with a high-pressure drop between the feed and the permeate for a pressure ratio between four and six.
“From the point of view of the engine architecture, the main difference is the presence of the MIEC membrane,” said Martinez. “The rest of the elements used can be generally found in traditional engines. Moreover, the need to use after-treatment devices is highly reduced. From an operational point of view, the only difference is in the exhaust gas. This gas does not contain nitrogen oxides, and it is composed mainly of vapor water and CO2. In case that the CO2 is captured, only water is delivered to the atmosphere.”
More for You: Energy Blog: Time Is Energy
Once the prototype is built, it will be tested in an engine test bench in order to demonstrate its performance at different operating points.
After they’ve perfected the large engines, the researchers believe they can make adjustments so it can be used in automobiles.
“In the case of smaller vehicles, it could also be applied by sequestering only part of the carbon dioxide in the exhaust,” said Francisco José Arnau, a fellow researcher at the CMT-Thermal Motors.
Imagine being trapped in slow-moving traffic behind a tractor-trailer. Now imagine it without the smell of diesel exhaust permeating your car. That’s what these researchers are going for: a world free of diesel fumes.
Jean Thilmany is a technology writer based in Saint Paul, Minn.
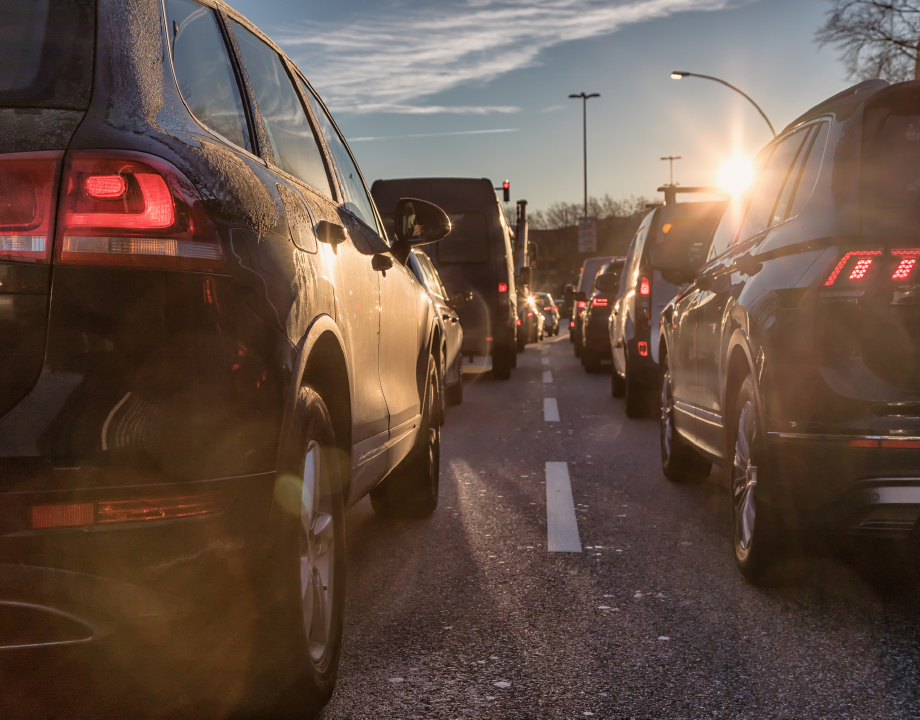
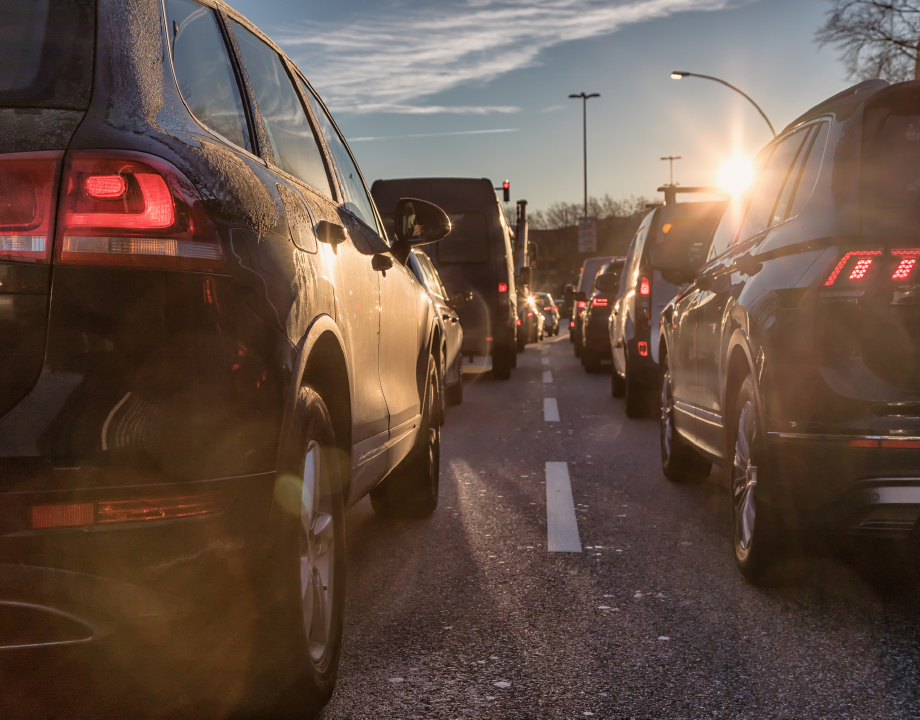