Cameras and Lasers Measure Thrust from Gas Turbines
Cameras and Lasers Measure Thrust from Gas Turbines
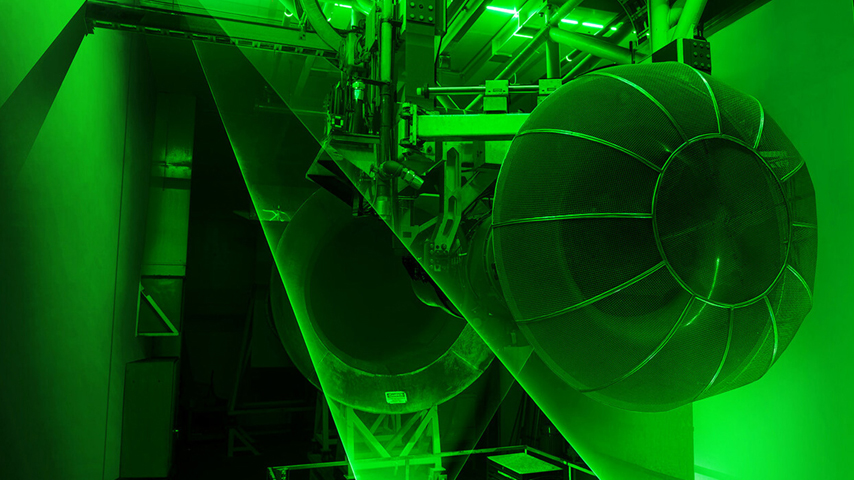
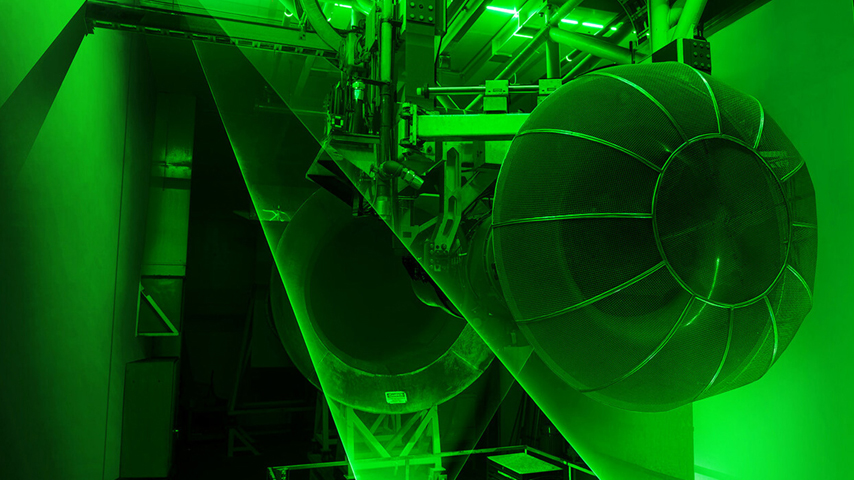
Advancements in computing power, lasers, and cameras improve Rayleigh scattering and work as well as sensors and probes.
A pioneering new technology developed through a partnership between Pratt & Whitney and Virginia Tech promises to help engineers better calculate gas turbine engine thrust by allowing for high fidelity measurement of conditions using optical laser instrumentation.
Called Filtered Rayleigh Scattering for Thrust measurement, or FRST, the technique is a less intrusive and more cost-effective method for measuring a range of engine metrics because it uses the ultraviolet light spectrum rather than traditional probes or sensors. First announced earlier this year, the patent-pending technology relies on the principle that light scattering back from air molecules passing over a laser-illuminated area can provide information about the gas flow field, which engineers can use to derive thrust. Laser beams are directed across the turbine's gas path, while the resulting scatter is recorded by a high-performance camera and "filtered" for corruptions in the signal.
Rayleigh scattering itself is not new, but the joint research team used advancements in computing power, laser, and camera technology to demonstrate the first successful application on a turbofan engine. Recorded results on a research engine in a test stand at Virginia Tech demonstrated similar accuracy to that of traditional sensors and probes.
Become a Member: How to Join ASME
Nonintrusive measurements such as FRST enables Pratt & Whitney “to measure more for less,” said Geoff Hunt, senior vice president of engineering and technology at Pratt & Whitney.
The inside of an operating engine “is a very, very unpleasant environment,” said Hunt. With the harshest parts of an engine experiencing temperatures over 2,000˚ F, pressures of 600 psi and components rotating at 20,000 rpm, an already very complex product can become more so with added instrumentation.
"You can barely see the underlying actual product for all the instrumentation that's all over it,” said Hunt. The use of probes and sensors can also complicate the interpretation of the measured data, which should be investigated and compensated for better accuracy to accommodate the conditions created by the probe being inside the engine [in the first place]. And of course, a sensor or probe that breaks off within an engine can also create serious problems, Hunt added.
FRST is a tool that can be used to help advance gas turbine propulsion technologies, particularly involving smaller and more thermally efficient engine cores, according to Pratt & Whitney. Those are key to next generation military and sustainable commercial engines.
More for You: Gas Power Plants Are Efficiency Giants
Hunt said his group has between 20 and 40 development engines in fabrication and testing stages at a point in time and spends tens of millions of dollars every year running development engines.
"They run across all of the product lines from military to general aviation to large commercial engines,” said Hunt, adding the testing includes both ground and flight tests in the U.S. and across the globe.
FRST provides key benefits of speed and reliability. Instrumentation is not always complex, said Hunt, but can certainly become so. It can take weeks or months off an engine’s build cycle, which, on a typical commercial engine usually takes two to three years to complete and certify.>
"A meaningful part of an engine program can be taken up by the time it takes me to build a highly instrumented engine,” said Hunt. Reducing intrusive instrumentation helps compress the longer lead times associated with its equipment and labor.
A lot of the world we live in wants product development faster and more agile, and this is just one of the techniques that can facilitate [that],” said Hunt.
Pratt & Whitney has had a long-standing collaboration with Virginia Tech in propulsion technology development, with a focus on advanced instrumentation.
"They have a range of very strong specializations at Virginia Tech, but in this particular case, development, engine instrumentation and measurements, which may sound like a pretty narrow sort of specialization, is actually incredibly important to us,” said Hunt.
Editor's Pick: 3D-Printed Ceramic Turbine Parts Withstand High Temperatures
Hunt said the company’s academic partnerships are a fundamental part of Pratt & Whitney’s engineering and technology strategy. They maintain dozens of relationships with primary research universities in the U.S. and overseas.This provides a connection to a pipeline of engineering talent and access to research facilities and capabilities, but also a network that opens up opportunities to partner with the government or others in private industry, such as Rolls Royce.
Pratt & Whitney recently teamed with Rolls Royce and Virginia Tech on a separate research project focusing on the impact of environmental contaminants on aeroengine operation and testing.
"That becomes a very powerful perspective,” said Hunt. “When you bring the business perspective, the regulator perspective, the academic perspective, and get them looking at the same problem through different lenses, you really get some pretty compelling outcomes.”
Next steps for the team’s work with FRST may include progress toward using it as a basis for engine certification. Pratt & Whitney is also actively looking for opportunities to test it in other applications, such as measuring particulate emissions, which could contribute to industry-wide efforts to understand and mitigate their environmental impact.
“We can prove it works,” Hunt said of FRST. “It's very much a journey from proving convenience a viable and meaningful concept to having it as an everyday usage for all types of measurements.”
Nancy Kristof is a technology writer in Denver.
Called Filtered Rayleigh Scattering for Thrust measurement, or FRST, the technique is a less intrusive and more cost-effective method for measuring a range of engine metrics because it uses the ultraviolet light spectrum rather than traditional probes or sensors. First announced earlier this year, the patent-pending technology relies on the principle that light scattering back from air molecules passing over a laser-illuminated area can provide information about the gas flow field, which engineers can use to derive thrust. Laser beams are directed across the turbine's gas path, while the resulting scatter is recorded by a high-performance camera and "filtered" for corruptions in the signal.
Rayleigh scattering itself is not new, but the joint research team used advancements in computing power, laser, and camera technology to demonstrate the first successful application on a turbofan engine. Recorded results on a research engine in a test stand at Virginia Tech demonstrated similar accuracy to that of traditional sensors and probes.
Become a Member: How to Join ASME
Nonintrusive measurements such as FRST enables Pratt & Whitney “to measure more for less,” said Geoff Hunt, senior vice president of engineering and technology at Pratt & Whitney.
The inside of an operating engine “is a very, very unpleasant environment,” said Hunt. With the harshest parts of an engine experiencing temperatures over 2,000˚ F, pressures of 600 psi and components rotating at 20,000 rpm, an already very complex product can become more so with added instrumentation.
"You can barely see the underlying actual product for all the instrumentation that's all over it,” said Hunt. The use of probes and sensors can also complicate the interpretation of the measured data, which should be investigated and compensated for better accuracy to accommodate the conditions created by the probe being inside the engine [in the first place]. And of course, a sensor or probe that breaks off within an engine can also create serious problems, Hunt added.
FRST is a tool that can be used to help advance gas turbine propulsion technologies, particularly involving smaller and more thermally efficient engine cores, according to Pratt & Whitney. Those are key to next generation military and sustainable commercial engines.
More for You: Gas Power Plants Are Efficiency Giants
Hunt said his group has between 20 and 40 development engines in fabrication and testing stages at a point in time and spends tens of millions of dollars every year running development engines.
"They run across all of the product lines from military to general aviation to large commercial engines,” said Hunt, adding the testing includes both ground and flight tests in the U.S. and across the globe.
FRST provides key benefits of speed and reliability. Instrumentation is not always complex, said Hunt, but can certainly become so. It can take weeks or months off an engine’s build cycle, which, on a typical commercial engine usually takes two to three years to complete and certify.>
"A meaningful part of an engine program can be taken up by the time it takes me to build a highly instrumented engine,” said Hunt. Reducing intrusive instrumentation helps compress the longer lead times associated with its equipment and labor.
A lot of the world we live in wants product development faster and more agile, and this is just one of the techniques that can facilitate [that],” said Hunt.
Pratt & Whitney has had a long-standing collaboration with Virginia Tech in propulsion technology development, with a focus on advanced instrumentation.
"They have a range of very strong specializations at Virginia Tech, but in this particular case, development, engine instrumentation and measurements, which may sound like a pretty narrow sort of specialization, is actually incredibly important to us,” said Hunt.
Editor's Pick: 3D-Printed Ceramic Turbine Parts Withstand High Temperatures
Hunt said the company’s academic partnerships are a fundamental part of Pratt & Whitney’s engineering and technology strategy. They maintain dozens of relationships with primary research universities in the U.S. and overseas.This provides a connection to a pipeline of engineering talent and access to research facilities and capabilities, but also a network that opens up opportunities to partner with the government or others in private industry, such as Rolls Royce.
Pratt & Whitney recently teamed with Rolls Royce and Virginia Tech on a separate research project focusing on the impact of environmental contaminants on aeroengine operation and testing.
"That becomes a very powerful perspective,” said Hunt. “When you bring the business perspective, the regulator perspective, the academic perspective, and get them looking at the same problem through different lenses, you really get some pretty compelling outcomes.”
Next steps for the team’s work with FRST may include progress toward using it as a basis for engine certification. Pratt & Whitney is also actively looking for opportunities to test it in other applications, such as measuring particulate emissions, which could contribute to industry-wide efforts to understand and mitigate their environmental impact.
“We can prove it works,” Hunt said of FRST. “It's very much a journey from proving convenience a viable and meaningful concept to having it as an everyday usage for all types of measurements.”
Nancy Kristof is a technology writer in Denver.
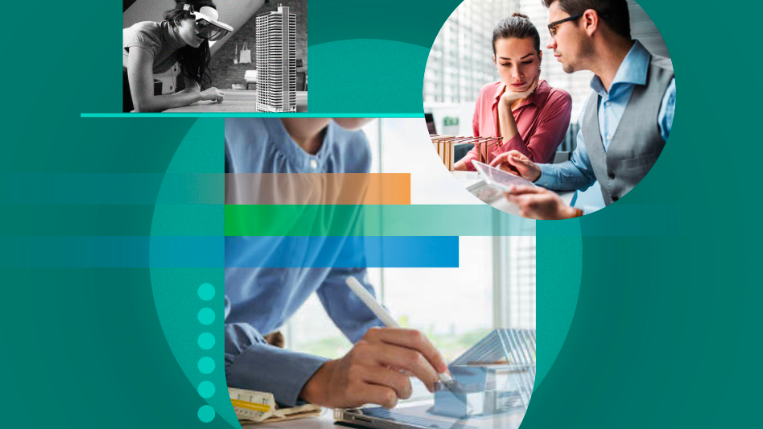
Pulse of the Profession: CAD in 2030
CAD technologies and their applications are rising in tandem with trends in Industry 4.0.
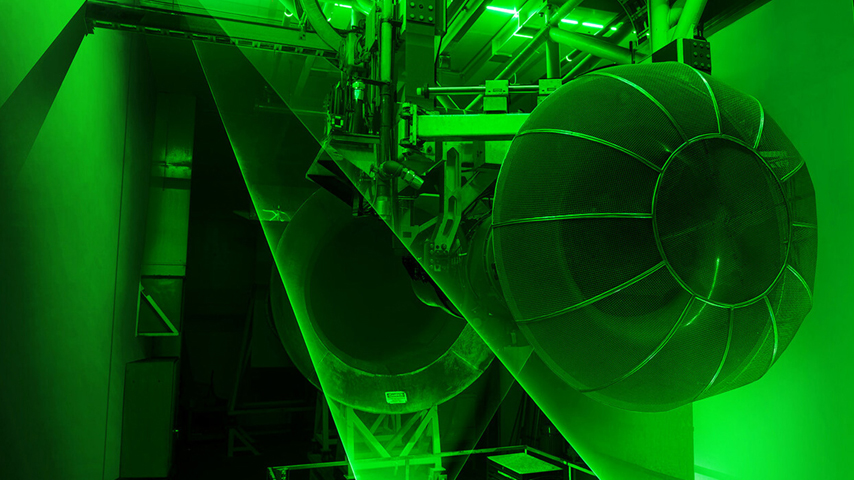
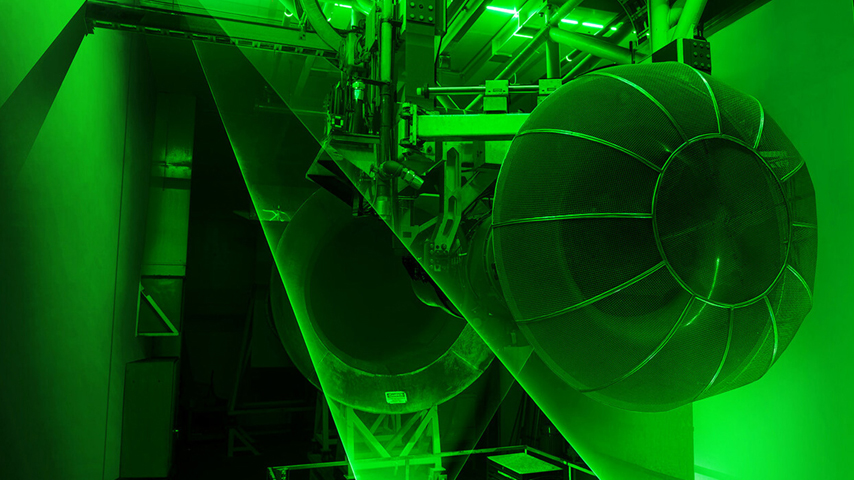