A Squidbot Hits the Seas
A Squidbot Hits the Seas
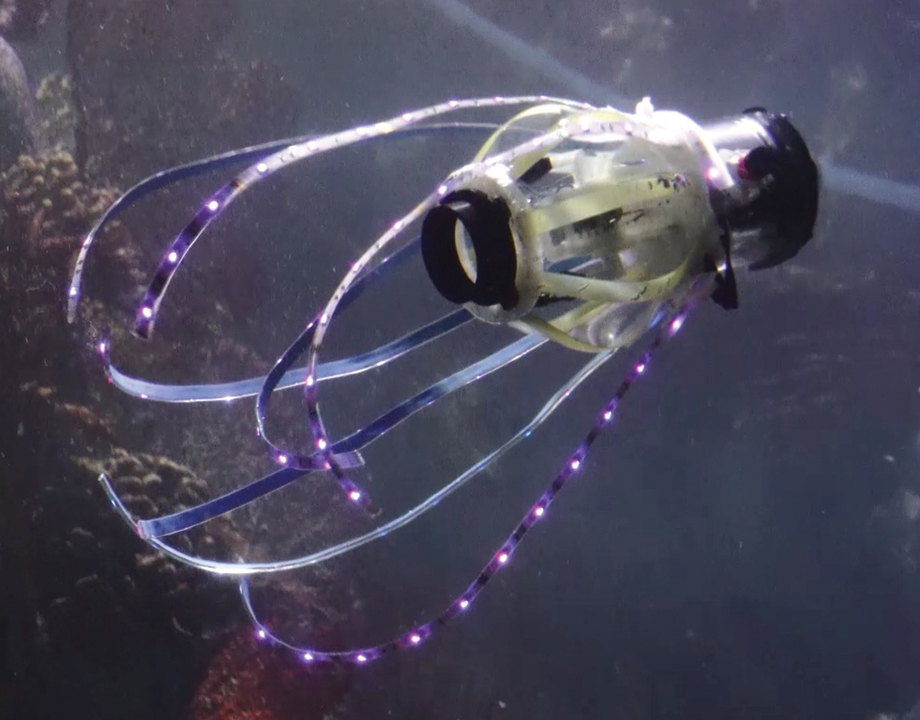
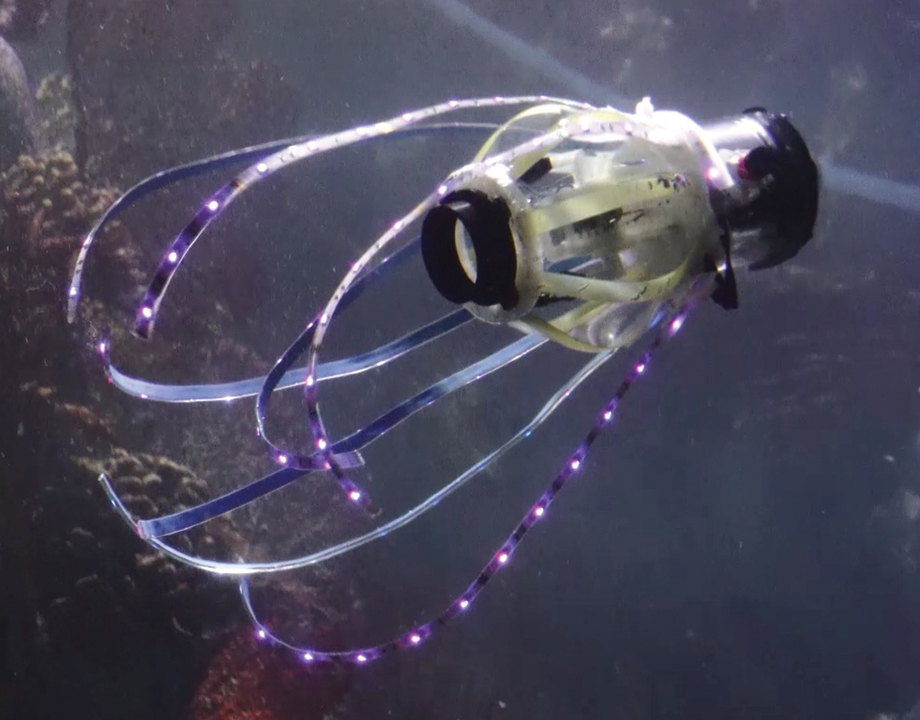
Engineers at the University of California San Diego have created a soft-bodied squidbot that does justice to the real thing. Photo: UCSD
The fastest aquatic invertebrate is the squid, clocking in at some 10 to 25 body lengths a second, or 36 feet in that same time. Without a bone in their bodies, the mollusks have a completely different mode of locomotion than the vertebrates of land or sea. And yet, unlike seemingly every other creature, the roboticists have yet to turn to the squid for inspiration.
Until now, that is. A cadre of engineers at the University of California San Diego have created a robot that uses the squid’s unique form of propulsion.
“Squid have a chamber inside that they fill with water,” explained Qiang Zhu, an engineering professor who ran the numerical modeling of the squidbot, “then they quickly shrink their body size, and push the water out. That turns out to be a very efficient way to achieve high speed.”
New and Noteworthy: Georgia Tech's SlothBot is Engineered to be Slow
To properly imitate a squid’s propulsive inhalations and exhalations, the team used a rack and pinion system with a mutilated gear mechanism. “Sounds a bit macabre,” said Caleb Christianson, a graduate student researcher at the university. “So we started calling it a slipped gear mechanism—kind of a misnomer, but it sounds better.”
As the gear goes to the end of the rack the robot expands, sucking up water and storing energy in its elastic body. When it gets to the limit of its motion, the gear finds itself toothless and slips against the rack. “All that elastic energy is released at once,” Christianson said, and the gear is forced back to the other end of the pinion, the robot ready to contract again.
To store that energy, the cephalopodic automaton’s body needs be elastic to just the right degree. Christianson and his team had started the project using balloons, but it was difficult to find one with the perfect size and shape.
“Either they were too tight, and compressing too much, or too loose, with a bunch of flapping membrane that didn’t fit with the motion,” he said. Christianson and his team turned to a rib and membrane combo instead. Initially those ribs were spring steel which seemed to provide the right flexibility and control, but it proved difficult to cut to the right dimensions.
Recommended for You: A Robot Crab to Clean the Ocean
Eventually they settled on FR-4, the plastic most used to make circuit boards, with the membrane between ribs made of an acrylic elastomer often used in artificial muscles. The result is a robot that swims around in a very squid-like manner, but without animal’s quickness.
“We weren’t trying to optimize for speed, but for the amount of water ejected on each pulse,” Christianson said. “The goal is to go from perfectly spherical to basically cylindrical,” he said. To do that they could turn to smart materials, like shape-altering alloys, to work as actuators instead of the mo-tor currently moving the slipped gear mechanism.
Another impediment to higher speeds is the intake hole. At the moment, the robot takes in water through the same nozzle from which it expels. Flesh-and-blood squids have valves for intake separate from the orifice from which they jet. Once the squidbot does something similar, its speed will skyrocket.
Editors’ Pick: 7 Big Advances in Soft Robotic Grippers
In addition to the obvious advantages of speed, the soft marinebot will eventually have the ability to turn in tight quarters—once it’s outfitted with a variable nozzle.
“It can turn in a very small space and will be useful in very complicated environments,” Zhu said.
Michael Abrams is a technology writer based in Westfield, N.J.
Until now, that is. A cadre of engineers at the University of California San Diego have created a robot that uses the squid’s unique form of propulsion.
“Squid have a chamber inside that they fill with water,” explained Qiang Zhu, an engineering professor who ran the numerical modeling of the squidbot, “then they quickly shrink their body size, and push the water out. That turns out to be a very efficient way to achieve high speed.”
New and Noteworthy: Georgia Tech's SlothBot is Engineered to be Slow
To properly imitate a squid’s propulsive inhalations and exhalations, the team used a rack and pinion system with a mutilated gear mechanism. “Sounds a bit macabre,” said Caleb Christianson, a graduate student researcher at the university. “So we started calling it a slipped gear mechanism—kind of a misnomer, but it sounds better.”
As the gear goes to the end of the rack the robot expands, sucking up water and storing energy in its elastic body. When it gets to the limit of its motion, the gear finds itself toothless and slips against the rack. “All that elastic energy is released at once,” Christianson said, and the gear is forced back to the other end of the pinion, the robot ready to contract again.
To store that energy, the cephalopodic automaton’s body needs be elastic to just the right degree. Christianson and his team had started the project using balloons, but it was difficult to find one with the perfect size and shape.
“Either they were too tight, and compressing too much, or too loose, with a bunch of flapping membrane that didn’t fit with the motion,” he said. Christianson and his team turned to a rib and membrane combo instead. Initially those ribs were spring steel which seemed to provide the right flexibility and control, but it proved difficult to cut to the right dimensions.
Recommended for You: A Robot Crab to Clean the Ocean
Eventually they settled on FR-4, the plastic most used to make circuit boards, with the membrane between ribs made of an acrylic elastomer often used in artificial muscles. The result is a robot that swims around in a very squid-like manner, but without animal’s quickness.
“We weren’t trying to optimize for speed, but for the amount of water ejected on each pulse,” Christianson said. “The goal is to go from perfectly spherical to basically cylindrical,” he said. To do that they could turn to smart materials, like shape-altering alloys, to work as actuators instead of the mo-tor currently moving the slipped gear mechanism.
Another impediment to higher speeds is the intake hole. At the moment, the robot takes in water through the same nozzle from which it expels. Flesh-and-blood squids have valves for intake separate from the orifice from which they jet. Once the squidbot does something similar, its speed will skyrocket.
Editors’ Pick: 7 Big Advances in Soft Robotic Grippers
In addition to the obvious advantages of speed, the soft marinebot will eventually have the ability to turn in tight quarters—once it’s outfitted with a variable nozzle.
“It can turn in a very small space and will be useful in very complicated environments,” Zhu said.
Michael Abrams is a technology writer based in Westfield, N.J.
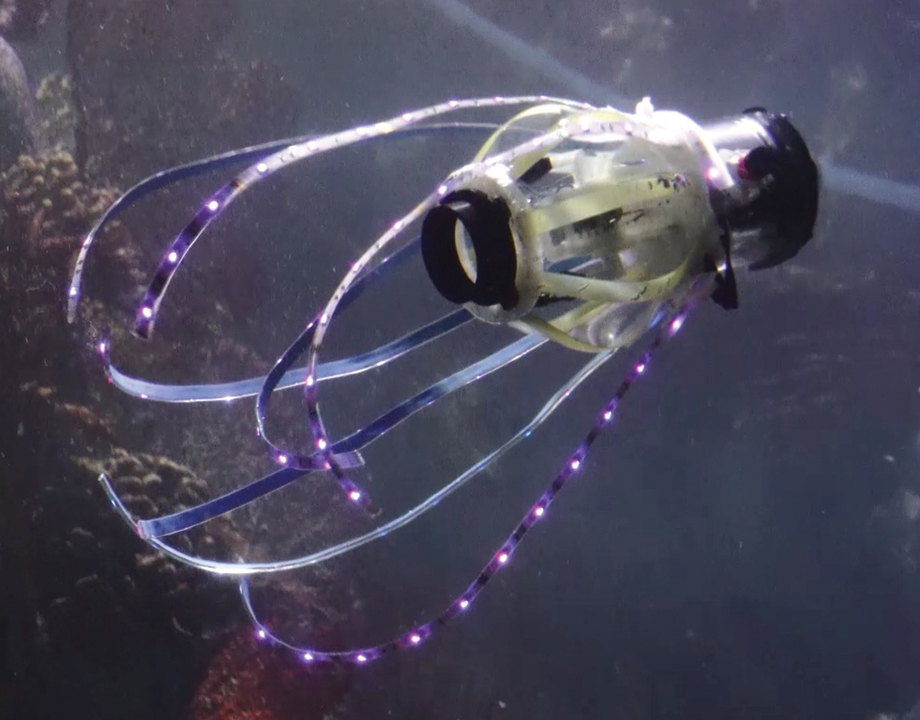
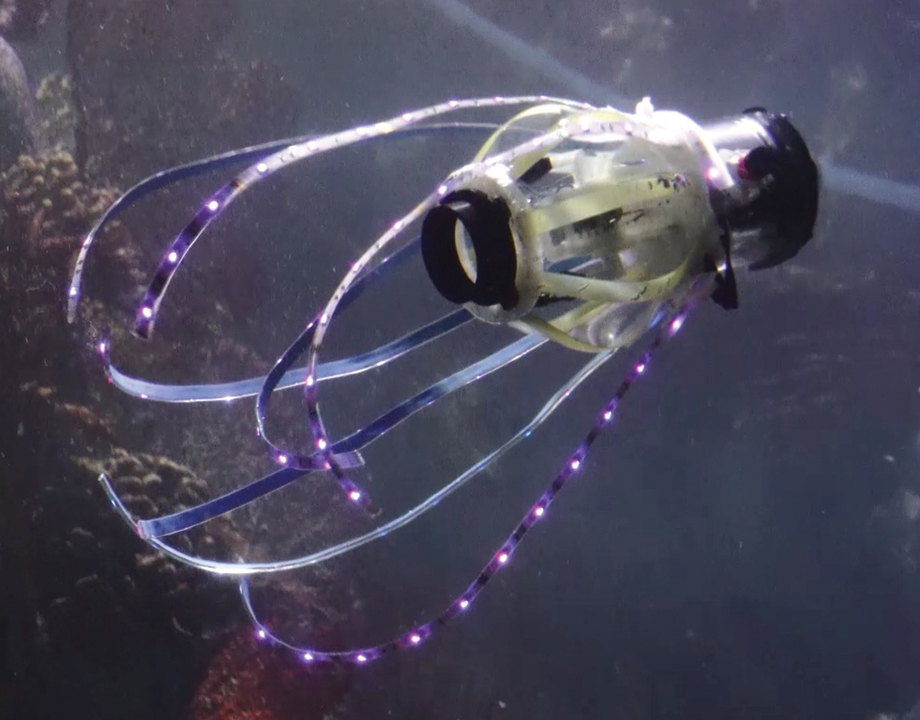