Turning One Plastic into Another
Turning One Plastic into Another
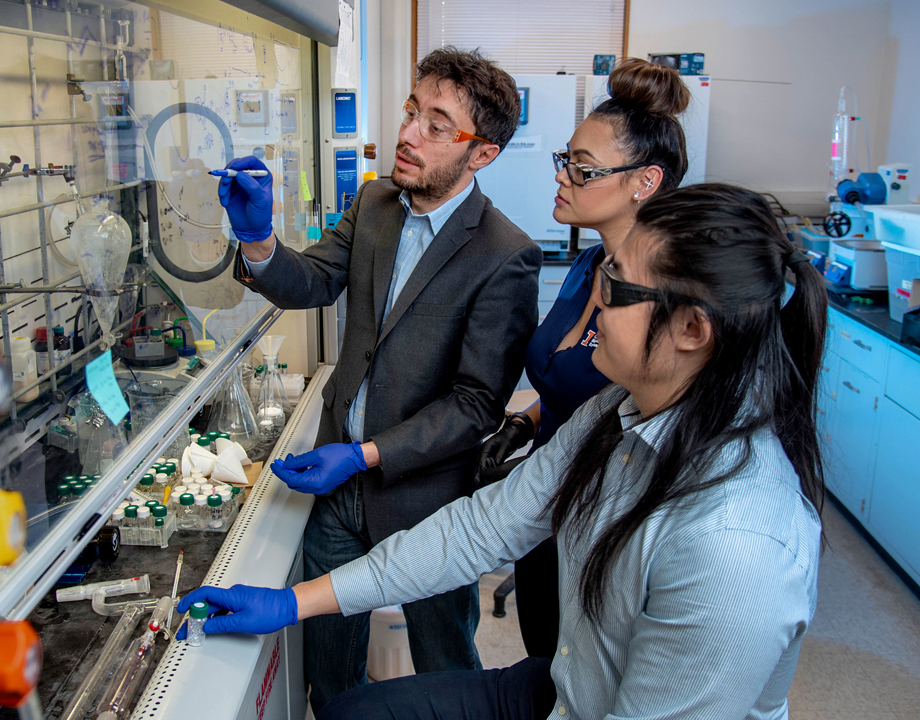
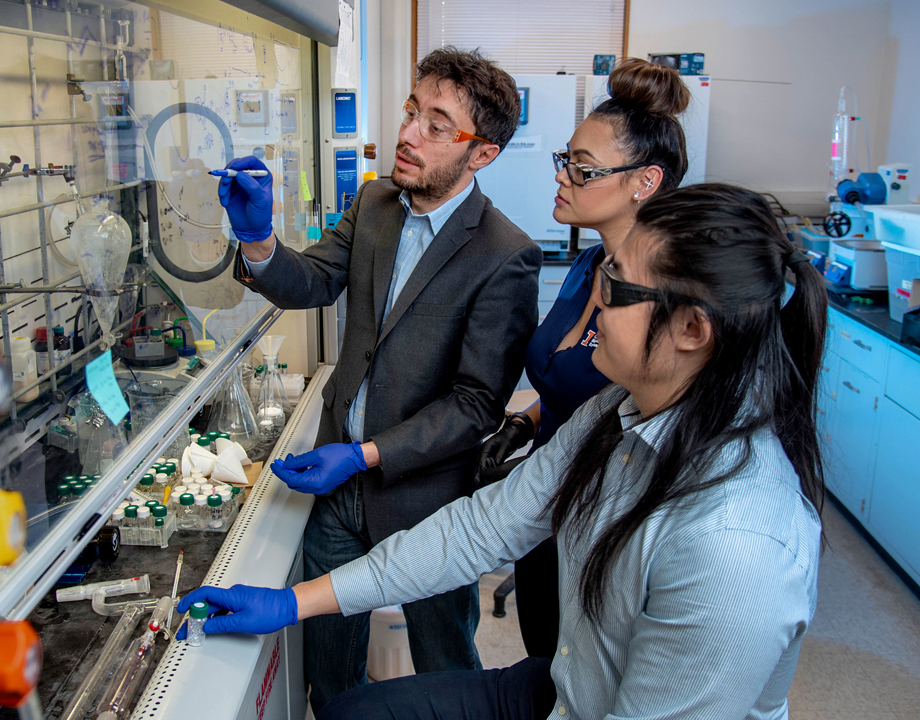
A new system of catalysts transforms old plastics into new, which could both optimize and revolutionize the entire recycling process.
The state of recycling is abysmal. The amount of energy it takes to sort plastics, clean, and process them, makes it barely worth the effort. The end product is strictly bottom of the barrel stuff that is good for bags, straps, carpets, and plastic lumber at best.
“That’s a sad story, at the end of the day, for the recycling industry,” said Damien Guironnet, a professor of chemical and bimolecular engineering at the University of Illinois Urbana-Champaign. “It’s just failing.”
But now Guironnet and Susannah Scott, a professor of chemical engineering at the University of California, Santa Barbara, have created a chemical process that turns one plastic, polyethylene, into the building block for another, polypropylene, using minimal energy. The end product is as good as new, ready to be turned into anything normally made with polypropylene.
“Polymers are such complex, beautiful molecules,” said Scott. “Think about all that effort that goes into taking small molecules, which we normally get from fossil fuels, and building up large complex molecules with very finely tailored properties. Then after some short period of use, you just throw them away.”
The pair set out to reverse that process, driven by a frustration with the world’s growing plastic waste problem and the current inability to do anything smart about it.
Similar to This: A New Enzyme Eats Plastics
There are two big reasons for inefficient recycling. One is the simple fact that not all plastics are alike. Symbols on packaging do help, but because of those triangles with numbers inside, most people think there are only seven types of plastic.
“But each one is actually dozens, if not hundreds, of different grades of that type of plastic,” Scott said. “Each grade is specifically engineered to have the properties it needs for that purpose. So you can imagine if you take even just one kind of plastic [such as] polyethylene and mix all the different grades together, you get a material which has properties nothing like the original milk jug or the original plastic bag. And so, it's only suitable for really low value uses.”
The other big problem is that plastics degrade somewhat when processed. That’s fine for virgin plastic, which maintains most of its integrity after going through an extruder. But the second time around, that same plastic degrades too much for mid- to high-end uses.
Plus, the carbon-carbon bonds that make up polymer chains are incredibly strong, requiring high temperatures to break them.
Scott and Guironnet’s solution uses three catalysts that work together to simultaneously break those bonds and form new ones, so that minimal heat is necessary. Their paper describing the process, "Chemical Recycling of Polyethylene by Tandem Catalytic Conversion to Propylene," appeared in The Journal of the American Chemical Society this September.
In short, one catalyst performs a “transfer dehydrogenation,” which creates a double carbon-carbon bond in the polymer chain to prime it for cutting. A second catalyst does the actual cutting and a third moves that double carbon-carbon bond further into the polymer chain for additional cutting.
“What we do, rather than just pulling the bonds apart, is simultaneously form new bonds while we are breaking the old bonds,” Scott explained.
The entire process, which is nearly energy-neutral, takes place in a reactor that separates the smaller cut sections from larger molecules.
Work remains to be done before the polymer slicing process transforms the contents of recycling bins into a product ripe for extrusion. “Currently, our catalytic productivity is not high enough to be implemented on a big scale,” Guironnet said.
Some of the materials used in the catalysts, namely rhenium, are expensive as well. But with large-scale conversion on some of the 100 million tons of plastic waste produced each year, the catalyst cost would be negligible.
Video: The Power of Recycling Plastic
“The catalysts that the oil industry uses for refining petroleum are also made of very expensive materials,” Scott said. “The benefit is that you put them in the reactor and 10 years later, they’re still in the reactor and they're still doing their job. So, the cost is really amortized over this huge productivity that they have.” Given the amount of plastic in the world, the costs of the catalysts would be similarly amortized.
Regardless of the work that lies ahead, the process Scott and Guironnet created proves something that once seemed impossible: that all waste plastic has the potential to become a fresh source for new plastic, with all the properties of the stuff coming straight from crude oil. When that happens, milk jugs, water bottles, and all other plastic throwaways, will no longer have the low value they do now, but will be as in demand as the oil from which they first came.
“What we've developed is an energy efficient way of turning plastic into new virgin plastic,” said Guironnet, “It really is the direction that the world needs to take. Because we need to make virgin plastic that doesn’t depend on fossil fuel.”
Michael Abrams is a technology writer based in Westfield, N.J.
“That’s a sad story, at the end of the day, for the recycling industry,” said Damien Guironnet, a professor of chemical and bimolecular engineering at the University of Illinois Urbana-Champaign. “It’s just failing.”
But now Guironnet and Susannah Scott, a professor of chemical engineering at the University of California, Santa Barbara, have created a chemical process that turns one plastic, polyethylene, into the building block for another, polypropylene, using minimal energy. The end product is as good as new, ready to be turned into anything normally made with polypropylene.
“Polymers are such complex, beautiful molecules,” said Scott. “Think about all that effort that goes into taking small molecules, which we normally get from fossil fuels, and building up large complex molecules with very finely tailored properties. Then after some short period of use, you just throw them away.”
The pair set out to reverse that process, driven by a frustration with the world’s growing plastic waste problem and the current inability to do anything smart about it.
Similar to This: A New Enzyme Eats Plastics
There are two big reasons for inefficient recycling. One is the simple fact that not all plastics are alike. Symbols on packaging do help, but because of those triangles with numbers inside, most people think there are only seven types of plastic.
“But each one is actually dozens, if not hundreds, of different grades of that type of plastic,” Scott said. “Each grade is specifically engineered to have the properties it needs for that purpose. So you can imagine if you take even just one kind of plastic [such as] polyethylene and mix all the different grades together, you get a material which has properties nothing like the original milk jug or the original plastic bag. And so, it's only suitable for really low value uses.”
The other big problem is that plastics degrade somewhat when processed. That’s fine for virgin plastic, which maintains most of its integrity after going through an extruder. But the second time around, that same plastic degrades too much for mid- to high-end uses.
Plus, the carbon-carbon bonds that make up polymer chains are incredibly strong, requiring high temperatures to break them.
Scott and Guironnet’s solution uses three catalysts that work together to simultaneously break those bonds and form new ones, so that minimal heat is necessary. Their paper describing the process, "Chemical Recycling of Polyethylene by Tandem Catalytic Conversion to Propylene," appeared in The Journal of the American Chemical Society this September.
In short, one catalyst performs a “transfer dehydrogenation,” which creates a double carbon-carbon bond in the polymer chain to prime it for cutting. A second catalyst does the actual cutting and a third moves that double carbon-carbon bond further into the polymer chain for additional cutting.
“What we do, rather than just pulling the bonds apart, is simultaneously form new bonds while we are breaking the old bonds,” Scott explained.
The entire process, which is nearly energy-neutral, takes place in a reactor that separates the smaller cut sections from larger molecules.
Work remains to be done before the polymer slicing process transforms the contents of recycling bins into a product ripe for extrusion. “Currently, our catalytic productivity is not high enough to be implemented on a big scale,” Guironnet said.
Some of the materials used in the catalysts, namely rhenium, are expensive as well. But with large-scale conversion on some of the 100 million tons of plastic waste produced each year, the catalyst cost would be negligible.
Video: The Power of Recycling Plastic
“The catalysts that the oil industry uses for refining petroleum are also made of very expensive materials,” Scott said. “The benefit is that you put them in the reactor and 10 years later, they’re still in the reactor and they're still doing their job. So, the cost is really amortized over this huge productivity that they have.” Given the amount of plastic in the world, the costs of the catalysts would be similarly amortized.
Regardless of the work that lies ahead, the process Scott and Guironnet created proves something that once seemed impossible: that all waste plastic has the potential to become a fresh source for new plastic, with all the properties of the stuff coming straight from crude oil. When that happens, milk jugs, water bottles, and all other plastic throwaways, will no longer have the low value they do now, but will be as in demand as the oil from which they first came.
“What we've developed is an energy efficient way of turning plastic into new virgin plastic,” said Guironnet, “It really is the direction that the world needs to take. Because we need to make virgin plastic that doesn’t depend on fossil fuel.”
Michael Abrams is a technology writer based in Westfield, N.J.