Condenser Coating Provides Efficiency Boost
Condenser Coating Provides Efficiency Boost
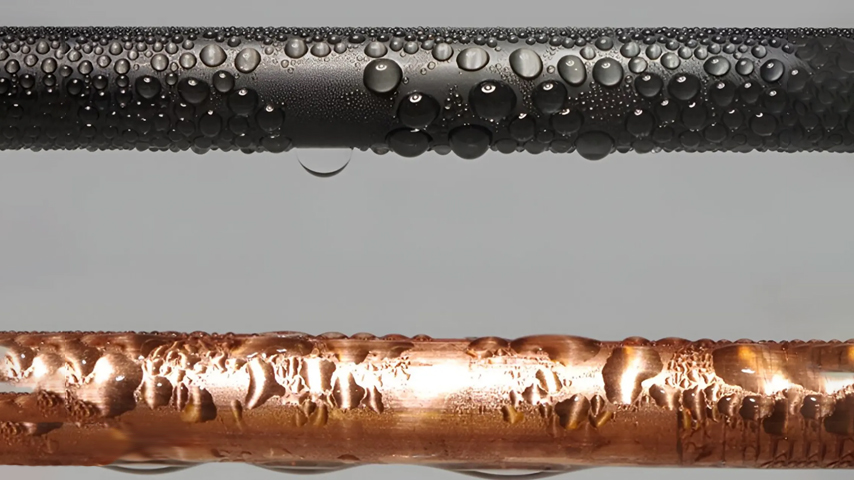
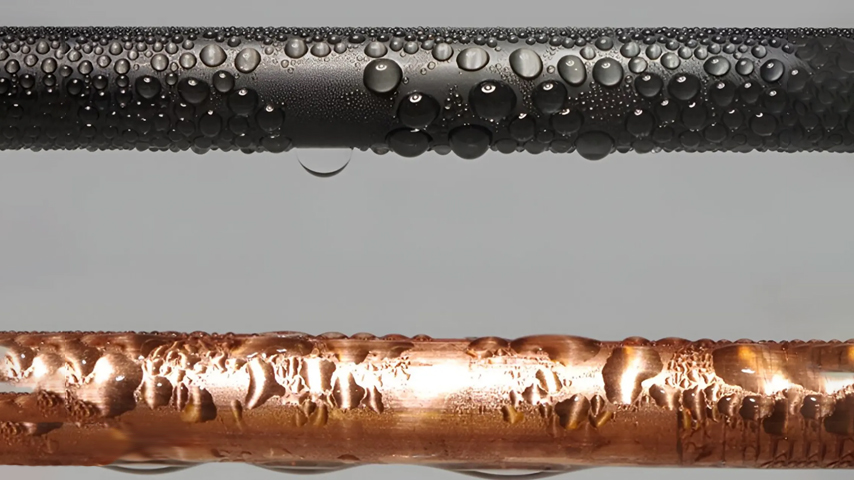
Fluorinated diamond-like carbon is a long-lasting coating that may improve process efficiency in steam power plants. The coated pipe (top) forms water droplets.
Engineers have tried to commercialize steam condensation and dropwise condensation (DWC) heat transfer for decades. DWC is a heterogeneous phase-change process where vapor changes to liquid in the form of discrete drops on an unwetted surface. The promise has been improved efficiency for steam power plants. But dropwise condensation is not used in industry today because the coatings required to promote droplet formation are very fragile and deteriorate quickly, sometimes within a few months.
One way to improve the viability of DWC heat transfer is to develop coatings that promote dropwise condensation and are durable and long-lasting.
Researchers at the University of Illinois Urbana-Champaign, led by associate professor of mechanical engineering Nenad Miljkovic, set out to find or develop a better coating that would solve this challenge. Their research directed them to an anti-fouling coating called diamond-like carbon, or DLC—a popular anti-wear coating for internal combustion engines (ICE). Because an ICE environment is very harsh, with high temperatures and shearing forces, the durability of DLC is already proven.
To enhance its thermal properties, “We thought that perhaps this DLC coating could be made to be hydrophobic and applied as a condenser coating,” Miljkovic said.
The team found a winner: fluorinated diamond-like carbon, or F-DLC. When applied as a coating on the steam condensers that are used in fossil fuel steam-cycle generation, F-DLC improved the overall process efficiency by 2 percent.
“In terms of impact, the transition from filmwise condensers—condensation forms as a film instead of droplets—to DWCs can increase overall power plant efficiency by up to 2 percent,” Miljkovic said. “Although this may sound small, 85 percent of the world’s electricity is generated by steam power plants. So 2 percent is a very large number and can lead to very significant CO2 emissions reductions and fuel savings.”
The F-DLC coating improves the heat transfer because the material is hydrophobic. When the steam condenses into water, it does not form a thin film that coats the surface, like water does on many clean metals and their oxides. Instead, the water forms droplets on the F-DLC surface, putting the steam into direct contact with the condenser and allowing heat to be directly transferred.
“To demonstrate its durability to power plant operators, they need to see that the coating will last for more than three years,” Miljkovic said. “There are no good models or standards to do accelerated testing of coating for steam condensation. So, we were forced to develop a steam condensation system where we could mount samples and let them condense for a three-year timeframe and watch what happens. This was very time-consuming but well worth the wait for the result.”
After performing the longest durability test ever reported in the literature—1,095 days—the team was delighted that the coated metals maintained their hydrophobic properties over the entire length of testing. They even maintained their hydrophobic properties after 5,000 scratches in an abrasion test.
“I’d say the biggest surprise was how well our coating worked,” Miljkovic said. “Not only did F-DLC last for three years in steam condensation, its abrasion resistance and thermal stability always beat out the contender coatings and worked very well. By the end of the three-year condensation test, the coating had not failed. We then decided to end the test because we felt three years was long enough and it was time to publish the work.”
And, from the mechanical engineering point of view, the cross-disciplinary aspects “made the project was extremely fun, as it involved steam systems, vacuum components, balance of plant analysis, component design and optimization, thermal and flow measurements, uncertainty analysis, materials characterization, reliability and economic analysis, and many more fields,” he added.
More for you: Researchers Destroy “Forever Chemicals” Using Supercritical Water
Miljkovic is currently collaborating with the Abbott Power Plant at the University of Illinois to install a real shell-and-tube heat exchanger (with F-DLC-coated tubing) in their steam line to test performance on real power plant steam (which can have properties different from laboratory generated steam). “A six-month demonstration run is planned to hopefully take our concept to a higher technology readiness level,” he said. “We have also been contacted by a number of power plant operators and builders in the U.S. and in other countries [Europe and India] that want to discuss potential implementation.”
Besides steam condensation, other potential applications include hydrodynamic drag reduction on ships, anti-fouling coatings, anti-corrosion coatings, frost-free heat exchangers, anti-icing surfaces, low adhesion surfaces in medical applications, anti-bacterial surfaces, and many more.
Mark Crawford is a technology writer in Corrales, N.M.
One way to improve the viability of DWC heat transfer is to develop coatings that promote dropwise condensation and are durable and long-lasting.
Researchers at the University of Illinois Urbana-Champaign, led by associate professor of mechanical engineering Nenad Miljkovic, set out to find or develop a better coating that would solve this challenge. Their research directed them to an anti-fouling coating called diamond-like carbon, or DLC—a popular anti-wear coating for internal combustion engines (ICE). Because an ICE environment is very harsh, with high temperatures and shearing forces, the durability of DLC is already proven.
To enhance its thermal properties, “We thought that perhaps this DLC coating could be made to be hydrophobic and applied as a condenser coating,” Miljkovic said.
The team found a winner: fluorinated diamond-like carbon, or F-DLC. When applied as a coating on the steam condensers that are used in fossil fuel steam-cycle generation, F-DLC improved the overall process efficiency by 2 percent.
“In terms of impact, the transition from filmwise condensers—condensation forms as a film instead of droplets—to DWCs can increase overall power plant efficiency by up to 2 percent,” Miljkovic said. “Although this may sound small, 85 percent of the world’s electricity is generated by steam power plants. So 2 percent is a very large number and can lead to very significant CO2 emissions reductions and fuel savings.”
The F-DLC coating improves the heat transfer because the material is hydrophobic. When the steam condenses into water, it does not form a thin film that coats the surface, like water does on many clean metals and their oxides. Instead, the water forms droplets on the F-DLC surface, putting the steam into direct contact with the condenser and allowing heat to be directly transferred.
The test of time
The biggest research challenge in developing F-DLC was simply time.“To demonstrate its durability to power plant operators, they need to see that the coating will last for more than three years,” Miljkovic said. “There are no good models or standards to do accelerated testing of coating for steam condensation. So, we were forced to develop a steam condensation system where we could mount samples and let them condense for a three-year timeframe and watch what happens. This was very time-consuming but well worth the wait for the result.”
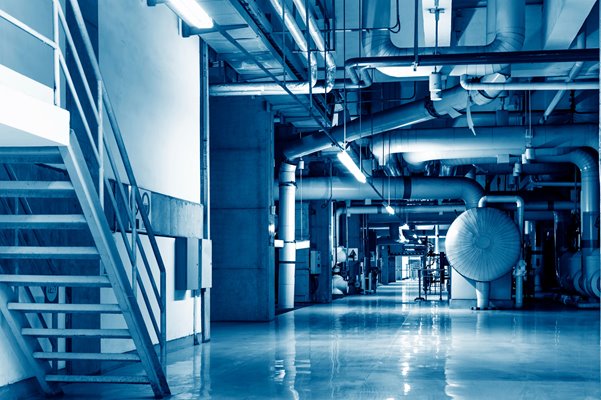
Learn from the Experts
Enroll in an official ASME online course to learn industry best practices for careful application of Section VIII of ASME’s Boiler and Pressure Vessel Code.
“I’d say the biggest surprise was how well our coating worked,” Miljkovic said. “Not only did F-DLC last for three years in steam condensation, its abrasion resistance and thermal stability always beat out the contender coatings and worked very well. By the end of the three-year condensation test, the coating had not failed. We then decided to end the test because we felt three years was long enough and it was time to publish the work.”
And, from the mechanical engineering point of view, the cross-disciplinary aspects “made the project was extremely fun, as it involved steam systems, vacuum components, balance of plant analysis, component design and optimization, thermal and flow measurements, uncertainty analysis, materials characterization, reliability and economic analysis, and many more fields,” he added.
Making power generation more efficient
The potential is impressive—if F-DLC can make coal and natural gas power generation 2 percent more efficient, there could be 460 million fewer tons of carbon dioxide released every year into the atmosphere, and 2 trillion fewer gallons of water used.More for you: Researchers Destroy “Forever Chemicals” Using Supercritical Water
Miljkovic is currently collaborating with the Abbott Power Plant at the University of Illinois to install a real shell-and-tube heat exchanger (with F-DLC-coated tubing) in their steam line to test performance on real power plant steam (which can have properties different from laboratory generated steam). “A six-month demonstration run is planned to hopefully take our concept to a higher technology readiness level,” he said. “We have also been contacted by a number of power plant operators and builders in the U.S. and in other countries [Europe and India] that want to discuss potential implementation.”
Besides steam condensation, other potential applications include hydrodynamic drag reduction on ships, anti-fouling coatings, anti-corrosion coatings, frost-free heat exchangers, anti-icing surfaces, low adhesion surfaces in medical applications, anti-bacterial surfaces, and many more.
Mark Crawford is a technology writer in Corrales, N.M.
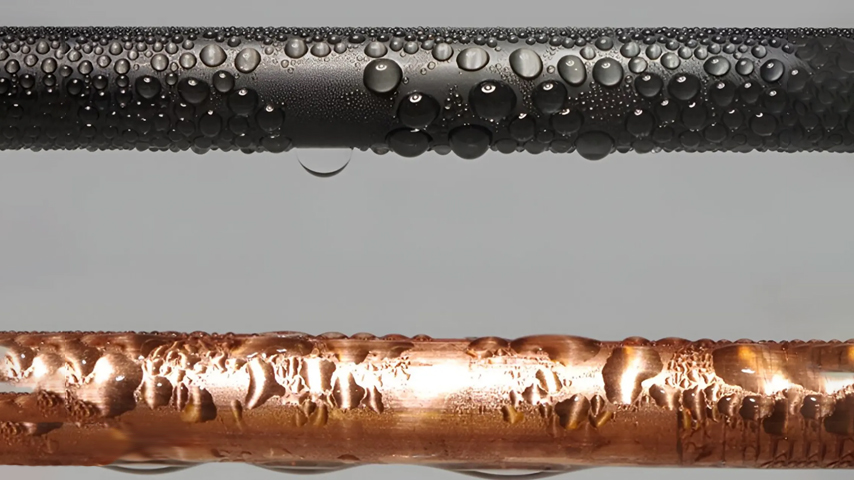
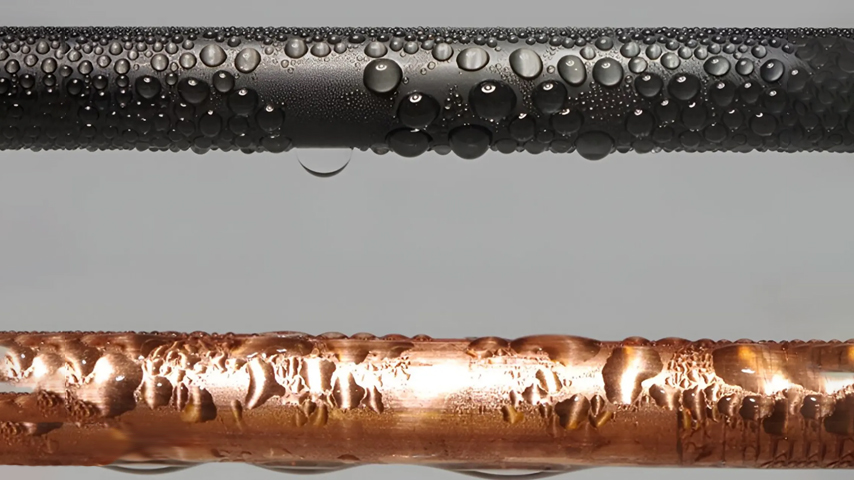