Bone Repair with 3D Painted Ceramics
Bone Repair with 3D Painted Ceramics
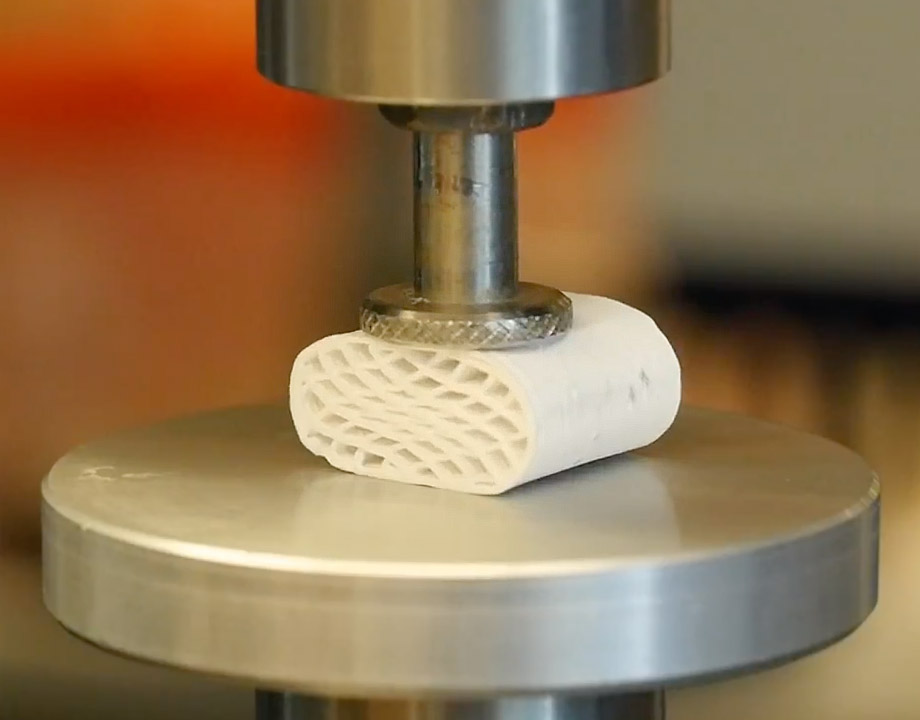
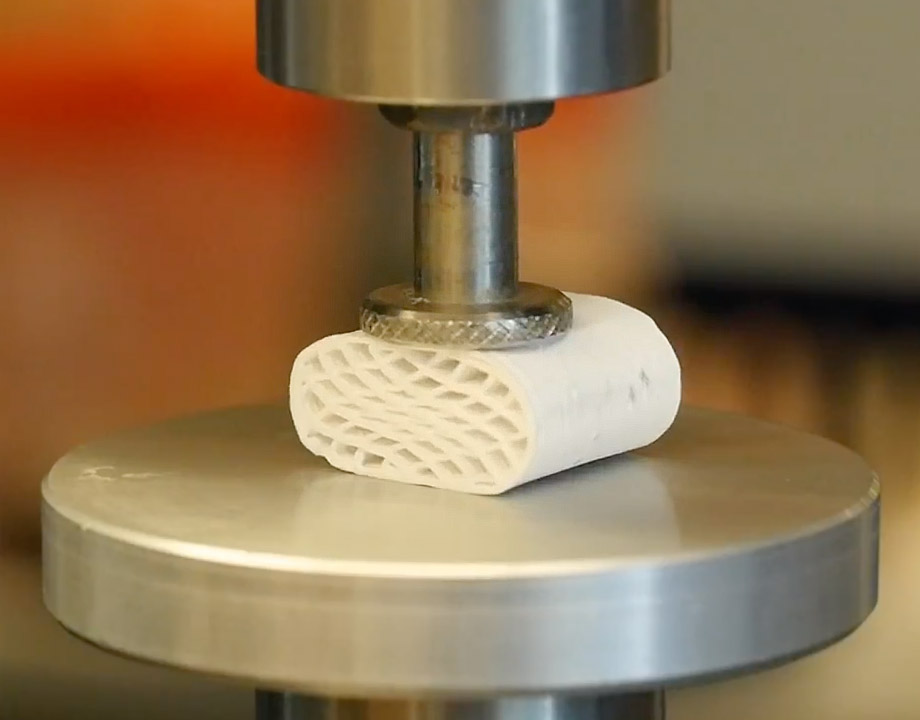
Hyperelastic Bone is a ceramic biomaterial that is easily printed on most extrusion 3D printers and is difficult to distinguish from natural bone. Photo: Dimension Inx
Ramille Shah and Adam Jakus founded Dimension Inx in 2016 to commercialize and translate new biomaterials compatible with additive manufacturing that they had previously developed in the academic laboratory.
“There were virtually no clinically relevant 3D-printable biomaterials,” Jakus said. “For example, although alginates, celluloses, and chitosans are easy to 3D print, they have very limited bioactivity and biocompatibility.”
Within a few years the team had created a suite of 3D-printable materials called “3D Paints,” including biomaterials with high regenerative capacity and surgical friendliness. After almost a decade of study and development, one of these materials, known as Hyperelastic Bone, is moving toward FDA approval.
“Both in vitro and in vivo studies over the past seven to eight years have shown Hyperelastic Bone to be highly bioactive and osteoregenerative,” Jakus said. “Scaffolds made from this material not only support adult stem cell attachment and proliferation, but also stem cell differentiation to osteoblast-like [bone-producing] cells, without the need for added growth factors or chemical or mechanical stimuli.”
“3D Painting” is a materials-centric advanced manufacturing technology that allows almost any material to be 3D printed via simple, room-temperature extrusion, with even the simplest machines, without the need for powder beds, resin baths, cross linking, or curing.
Further Reading: 3D Bioprinter Prints Healthy Skin onto Patients in Minutes
Each 3D paint or material is distinguished by its main ingredients, including graphene, metals and alloys, ceramics, and biological powders made from decellularized tissues (scaffolds made from tissues after cellular contents have been removed) and organs. Particles of these materials are suspended within a small volume of medical quality biodegradable polymer. Using their process, Shah and Jakus have created hundreds of materials via simple room-temperature 3D printing.
“Any machine that operates via material extrusion will work,” Jakus said. “This excludes laser and e-beam powder sintering and stereolithography methods, but includes fused deposition modeling machines and liquid, gel, and paste extrusion machines, often referred to as direct ink write, robocasting, or bioprinting.”
All 3D paints are co-3D-printing compatible with each other, meaning that multi-material structures can be created. Additionally, they can be blended or mixed prior to or during printing to create materials with blended or gradient functionality that change over length or depth—a property that is essential for tissue and organ fabrication.
Hyperelastic Bone consists of 90 weight percent calcium phosphate ceramic microparticles, linked by a matrix of 10 weight percent high-quality, biodegradable polymer. “The composition and microstructure are so similar to natural bone that resulting computed tomography reconstructions of 3D painted Hyperelastic Bone parts are difficult to distinguish from natural bone,” Jakus said.
Further Reading: “3D Painting” Structures in Space
The ceramic-polymer composite matrix microstructure is characterized by interconnected micro- and nanoporosity, producing a total microstructural porosity of up to 50 percent—imparting advantageous mechanical and handling properties and liquid absorption capabilities. The unique composition and architecture of rigid ceramic particles linked by elastomer bridges and surrounded by substantial porosity create elastic-like properties that facilitate bone regeneration into the implant.
3D paints can also be synthesized in different-sized batches at rapid speeds with any extrusion-based 3D-printing hardware. Materials solidify via near-instantaneous evaporation of the evaporant, and also chemically weld with previously deposited materials. “The process is so simple,” Jakus noted, “that a handheld syringe could be used to ‘3D print’ this material, if one had a very steady hand and was very patient.”
Because the 3D painting process is a platform technology, it can be used to rapidly design new 3D-printable materials. If an organization has a specific material it wants to 3D print but cannot achieve it using existing additive manufacturing technologies, it can likely be achieved through Dimension Inx's 3D painting process, claimed Jakus.
Hyperelastic Bone is a singular 3D-painted material specifically engineered for bone repair and regeneration applications. Initially demonstrated in 2012, it was first published in 2016, became commercially available for research use in 2017, and is currently progressing toward FDA approval and clinical use.
Further Reading: 6 Innovative Ways to Use 3D Printing
“Beyond the structural, biological, handling, manufacturing, and economic advantages of Hyperelastic Bone, its current form offers many future opportunities for ceramic-based 3D-painted products that take advantage of the unique nature of 3D-painting technologies,” Jakus said.
One such advantage is compositional versatility. Because the 3D-painting process is primarily chemistry-independent, many distinct types of ceramics and even glasses can be used to create 3D paints and 3D-painted structures. “Additional agents, such as antibiotics, small molecules, peptides, proteins, or nanoparticles, can also be directly incorporated into 3D paints prior to 3D painting, enhancing functionality and performance,” Jakus said.
Mark Crawford is a technology writer based in Corrales, N.M.
Register Today for AM Medical: May 27–28, 2020 in Minneapolis, MN
“There were virtually no clinically relevant 3D-printable biomaterials,” Jakus said. “For example, although alginates, celluloses, and chitosans are easy to 3D print, they have very limited bioactivity and biocompatibility.”
Within a few years the team had created a suite of 3D-printable materials called “3D Paints,” including biomaterials with high regenerative capacity and surgical friendliness. After almost a decade of study and development, one of these materials, known as Hyperelastic Bone, is moving toward FDA approval.
“Both in vitro and in vivo studies over the past seven to eight years have shown Hyperelastic Bone to be highly bioactive and osteoregenerative,” Jakus said. “Scaffolds made from this material not only support adult stem cell attachment and proliferation, but also stem cell differentiation to osteoblast-like [bone-producing] cells, without the need for added growth factors or chemical or mechanical stimuli.”
3D Painting
“3D Painting” is a materials-centric advanced manufacturing technology that allows almost any material to be 3D printed via simple, room-temperature extrusion, with even the simplest machines, without the need for powder beds, resin baths, cross linking, or curing.
Further Reading: 3D Bioprinter Prints Healthy Skin onto Patients in Minutes
Each 3D paint or material is distinguished by its main ingredients, including graphene, metals and alloys, ceramics, and biological powders made from decellularized tissues (scaffolds made from tissues after cellular contents have been removed) and organs. Particles of these materials are suspended within a small volume of medical quality biodegradable polymer. Using their process, Shah and Jakus have created hundreds of materials via simple room-temperature 3D printing.
“Any machine that operates via material extrusion will work,” Jakus said. “This excludes laser and e-beam powder sintering and stereolithography methods, but includes fused deposition modeling machines and liquid, gel, and paste extrusion machines, often referred to as direct ink write, robocasting, or bioprinting.”
All 3D paints are co-3D-printing compatible with each other, meaning that multi-material structures can be created. Additionally, they can be blended or mixed prior to or during printing to create materials with blended or gradient functionality that change over length or depth—a property that is essential for tissue and organ fabrication.
3D Printed Ceramic Biomaterial
Hyperelastic Bone consists of 90 weight percent calcium phosphate ceramic microparticles, linked by a matrix of 10 weight percent high-quality, biodegradable polymer. “The composition and microstructure are so similar to natural bone that resulting computed tomography reconstructions of 3D painted Hyperelastic Bone parts are difficult to distinguish from natural bone,” Jakus said.
Further Reading: “3D Painting” Structures in Space
The ceramic-polymer composite matrix microstructure is characterized by interconnected micro- and nanoporosity, producing a total microstructural porosity of up to 50 percent—imparting advantageous mechanical and handling properties and liquid absorption capabilities. The unique composition and architecture of rigid ceramic particles linked by elastomer bridges and surrounded by substantial porosity create elastic-like properties that facilitate bone regeneration into the implant.
3D paints can also be synthesized in different-sized batches at rapid speeds with any extrusion-based 3D-printing hardware. Materials solidify via near-instantaneous evaporation of the evaporant, and also chemically weld with previously deposited materials. “The process is so simple,” Jakus noted, “that a handheld syringe could be used to ‘3D print’ this material, if one had a very steady hand and was very patient.”
Because the 3D painting process is a platform technology, it can be used to rapidly design new 3D-printable materials. If an organization has a specific material it wants to 3D print but cannot achieve it using existing additive manufacturing technologies, it can likely be achieved through Dimension Inx's 3D painting process, claimed Jakus.
Hyperelastic Bone is a singular 3D-painted material specifically engineered for bone repair and regeneration applications. Initially demonstrated in 2012, it was first published in 2016, became commercially available for research use in 2017, and is currently progressing toward FDA approval and clinical use.
Further Reading: 6 Innovative Ways to Use 3D Printing
“Beyond the structural, biological, handling, manufacturing, and economic advantages of Hyperelastic Bone, its current form offers many future opportunities for ceramic-based 3D-painted products that take advantage of the unique nature of 3D-painting technologies,” Jakus said.
One such advantage is compositional versatility. Because the 3D-painting process is primarily chemistry-independent, many distinct types of ceramics and even glasses can be used to create 3D paints and 3D-painted structures. “Additional agents, such as antibiotics, small molecules, peptides, proteins, or nanoparticles, can also be directly incorporated into 3D paints prior to 3D painting, enhancing functionality and performance,” Jakus said.
Mark Crawford is a technology writer based in Corrales, N.M.
Register Today for AM Medical: May 27–28, 2020 in Minneapolis, MN
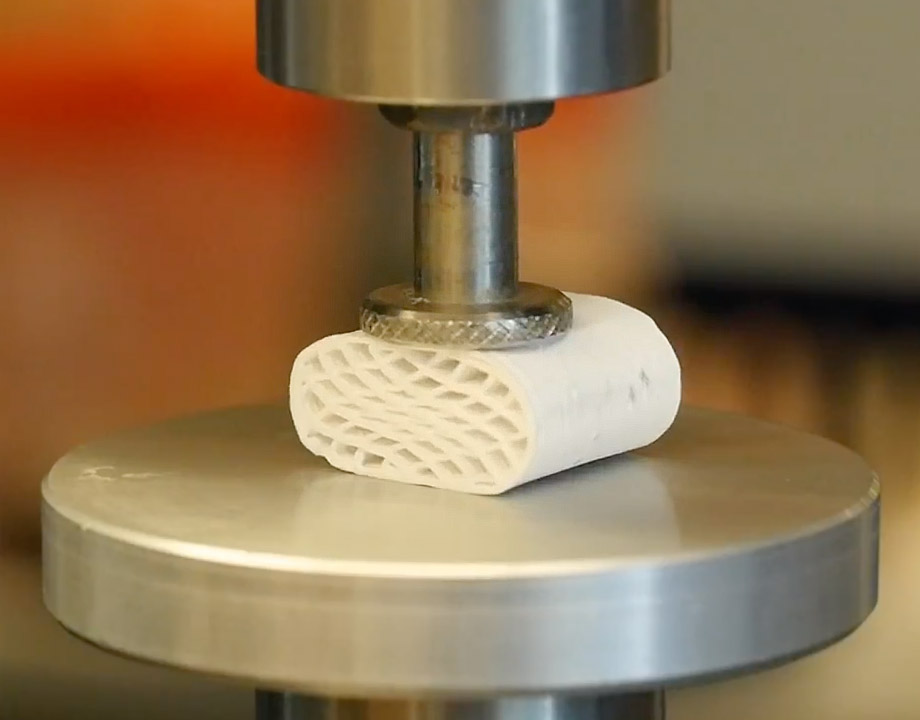
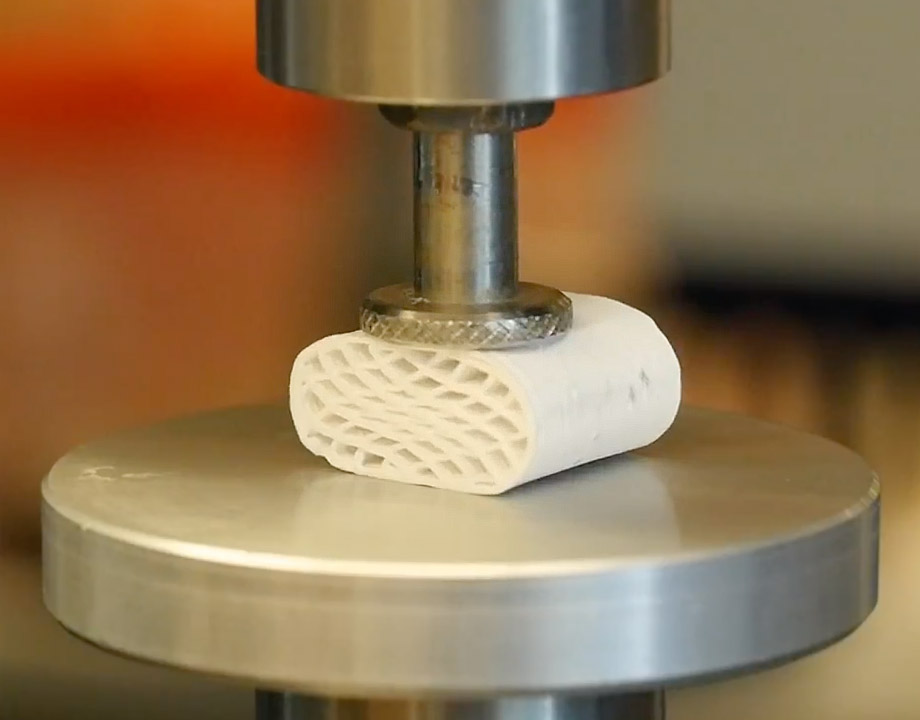