Vertical-Axis Wind Turbines: Time for a Comeback?
Vertical-Axis Wind Turbines: Time for a Comeback?
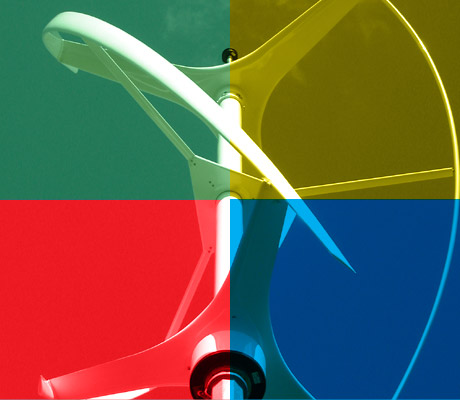
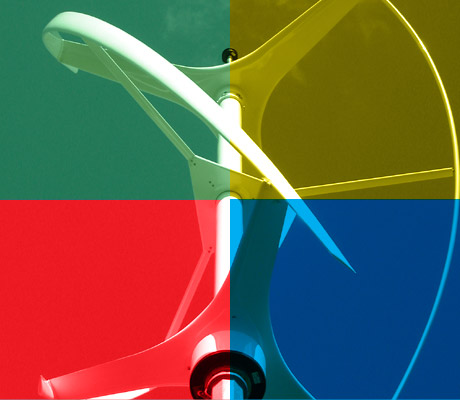
Invented prior to World War II, the vertical-axis wind turbine (VAWT) had some appealing features: the vertical orientation accepted wind from any direction and the heavy generator and gearbox equipment rested on the ground instead of on the tower (much easier to access). However, compared to advances in horizontal-axis wind turbines, VAWT disadvantages included the longer total blade length per swept area, cyclic loading, structural resonance, lack of aerodynamic braking, and higher operating costs. As horizontal-axis wind turbine (HAWT) technologies continued to improve and rotor costs dropped, the HAWT became the dominant technology for land-based wind systems, especially over the last two decades.
Although they are not the frontrunner for 5-MW-10-MW land-based systems, VAWTs may be the favored technology for larger offshore systems in the 10-MW-20-MW scale, where the vertical-axis rotor architecture offers potentially large reductions in cost of energy (COE) for operations and maintenance, substructure, installation, and infrastructure.
Evaluating Feasibility
This idea is currently being tested at Sandia National Laboratories in New Mexico, where a research team is evaluating the feasibility of VAWT architecture for large-scale deployment in the offshore environment. The goal is to reduce the biggest barrier to offshore wind development—high COE—by 20% or more through the application of VAWT rotor technology. The research project will:
- Develop innovative VAWT rotor designs that result in cost-effective and easily manufactured rotors for deep-water offshore machines
- Demonstrate the potential for greater than 20%t reduction in COE for deep-water, floating VAWT systems
- Develop specialized manufacturing techniques, certification test methods, and a commercialization plan for offshore VAWT rotors
- Test, in a wind tunnel and combined wind-wave tank, a proof-of-concept subscale, deep-water floating offshore wind-turbine generator employing a VAWT rotor
Sandia National Laboratories is undertaking a project to test the feasibility of vertical-axis wind turbine (VAWT) architecture for large-scale deployment in the offshore environment. Image: Sandia National Laboratories
"Modeling suggests the COE reduction opportunities follow from three fundamental characteristics of the VAWT: lower turbine center of gravity, reduced machine complexity, and the opportunity for scaling the machine to the 10-MW-20-MW size," says Matthew Barone, one of the project's lead researchers in Sandia's Wind & Water Power Technologies Department.
Several rotor architecture concepts that incorporate unique VAWT load-alleviation and braking strategies will be considered, especially for curved-bladed Darrieus rotors and lightweight, towerless V- or U-shaped rotors. A rotor optimized for increased energy capture, as well as airfoils optimized for use with load-alleviation concepts, will also be tested.
Design Requirements
"The most original and innovative aspect of this work will be the suite of rotor design solutions we are developing that simultaneously address the need for reliable aerodynamic braking, while also smoothing out power and torque oscillations associated with VAWTs," says Barone. "By addressing these design requirements through rotor innovations, we hope to retain the VAWT's inherent advantage of simplicity of design, while improving its overall cost-effectiveness in the offshore environment."
The ultimate VAWT rotor design may also create manufacturing challenges. The complexity and scale of a 10-MW-20-MW VAWT blade structure, along with significant differences in blade loading, may require specialized manufacturing processes. Researchers will also identify the best materials, coatings, and manufacturing options for the VAWT rotors.
Total estimated reduction in COE from the baseline work is 28%. The most important COE reduction categories are the increased annual energy production and reduced operations and maintenance, support structure, and balance-of-system costs. These reductions more than offset the increase in blade costs due to the longer VAWT blades. Deep-water deployment in a larger wind resource also plays an important role, accounting for 32% of the COE reduction due to increased energy capture. However, calculations were also performed for the HAWT baseline in the deep-water wind resource, and COE reduction for the VAWT concept relative to the revised baseline is still 21%.
"The greatest challenge of this project is combining past successes in VAWT design with new innovations that will result in dramatically improved machines for offshore," says Barone. "This type of research runs counter to the usual incremental nature of wind turbine innovation. We feel, however, that the challenges presented by offshore wind demand new approaches. For deepwater applications at the 10MW-20-MW scale, the VAWT architecture is potentially a transformational technology—something that may be necessary for large-scale offshore wind development in the U.S."
Mark Crawford is an independent writer.
The greatest challenge of this project is combining past successes in VAWT design with new innovations that will result in dramatically improved machines for offshore.Matthew Barone, lead researcher, Sandia's Wind & Water Power Technologies Department
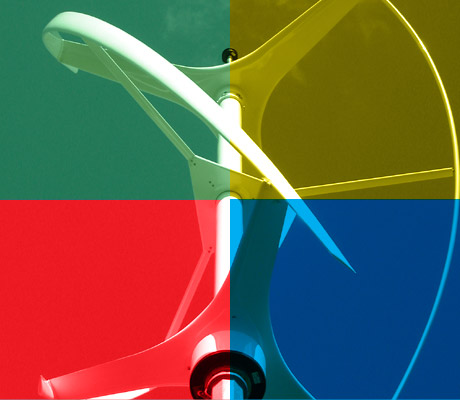
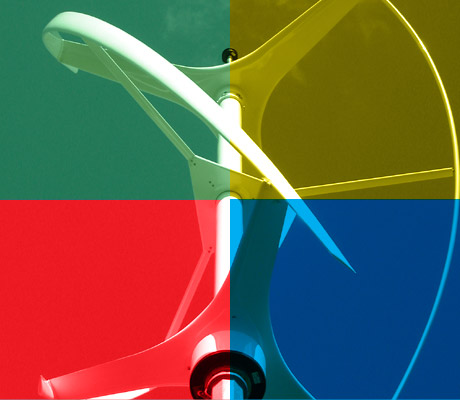