Offshore Platform Promises Less Tilt
Offshore Platform Promises Less Tilt
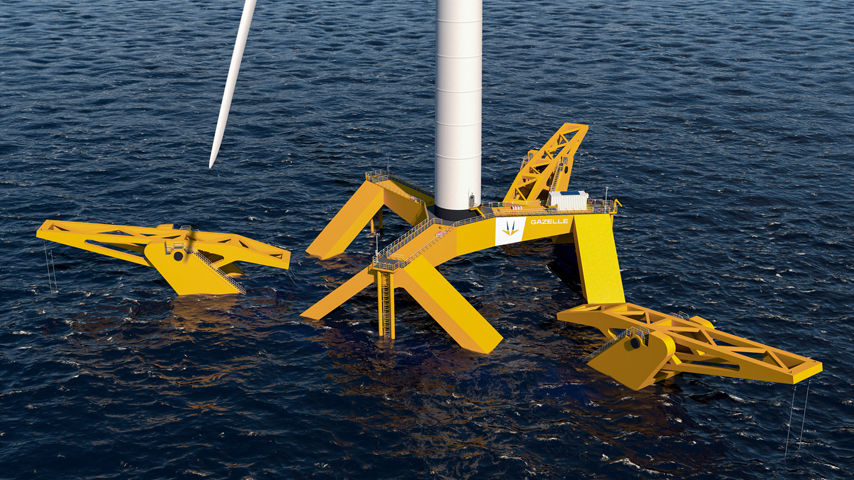
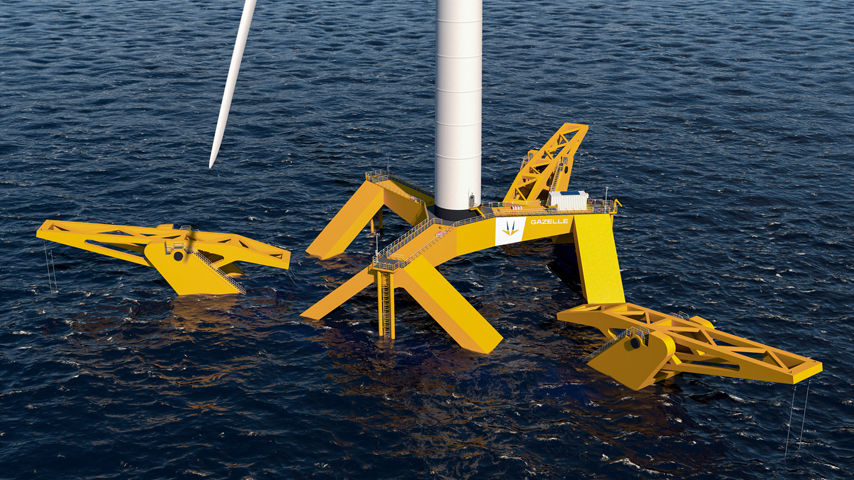
Platform's legs pivot to work with counterweight to provide greater stability.
Offshore wind turbines have a problem. Whether they’re in deep or shallow waters, they're mounted on massive platforms that require large semi-submersible vessels for towing and installation. Most require a thickness of steel that can only be manufactured by a select number of producers, and there are limited numbers of barges and ships that can handle the large pieces, some of which can only access deepwater ports.
Now, new platform designs for deeper water offer lighter configurations that can be produced by more manufacturers and sail from a larger number of ports because of their lower draft. They will play an important part in meeting global demand for offshore wind generation, such as the European Commission's goal of generating 450 GW of offshore wind power by 2050.
Ireland’s Gazelle Wind Power has a platform design that may help reduce a production bottleneck and speed the deployment of deepwater floating wind turbines. Gazelle engineers are testing a modified tension leg platform (TLP) that doesn’t require high tension or overly heavy structural materials, can be launched in seven meters of water (or less), and can be towed and assembled with the current fleet of towing vessels. It’s also scalable, so it can handle a range of turbine sizes.
The idea first came to Antonio García, the company’s chief innovation officer, seven years ago. He was disturbed by the number of problems that plague floating platforms with catenary mooring systems, the most common anchor system for offshore platforms.
“They have to be very big, they have to have a lot of buoyancy, and they have to be very heavy,” said Jason Wormald, the company’s chief technology officer. “The mooring footprint on these things can be thousands of meters, you've got installation and handling issues, and they are damaging the seabed. It’s just a nightmare.”
Most TLP designs aren’t much better as an alternative. The lines that connect the platform to the ocean floor demand high tension, requiring about 5,000 tons of anchor line; the tension of each connection must be precisely calibrated. The thousands of tons of tension needed just to connect the tension lines to mooring lines can only be done with heavy-lift vessels. Though they’re stable once connected, there’s no give and take for the rise and fall of the sea, and a mooring line failure can be catastrophic.
Becme a Member: How to Join ASME
Garcia devised a hybrid TLP/semi-submersible with three arms connected to the central platform. Each limb is a pivot that is connected to the sea floor by lines on the outside edge, and to a counterweight under the center of the platform. As a result, motion is transferred to the counterweight, which absorbs the energy, minimizing any tilt to the turbine on top. It’s essentially a passive ballast system.
Most offshore wind turbines are designed to support pitch angles of up to 10 degrees, according to the company. That allows for operation but creates additional wear and tear. The Gazelle design allows the platform to move horizontally and vertically with almost zero pitch and may reduce mooring loads by 50 percent compared to a tension leg platform, claims the firm.
The design will also accommodate production by a greater number of producers. Garcia approached the design from a naval architectural point of view, thinking of the platform less as a structure than as a vessel.
“So, what we've done is come up with a design that uses flat panel technology that effectively uses thin coiled steel with stiffened ribs on it,” said Wormald. “And what that means is that there are thousands of shipyards globally that already have the capability to produce this equipment.”
Listen to Our Podcast; Building Infrastructure for Offshore Wind Power
The buoyancy incorporated in the triangular base allows it to float in the low depth of shipyards and to be towed to its destination using traditional towing vessels. With a foundation and anchors preinstalled, the platform will simply be towed to site and connected to the lines waiting for them on buoys.
“There’s no subsea operation that goes on, there are no divers involved, there are no ROVs,” said Wormald. “You hook up top side, and then all you do is release the counterweight, and the counterweight tensions the lines.”
At the moment, the company is testing a 1/30 scale. Earlier this year Gazelle teamed with Portugal’s WAM Horizon, a renewable energy developer, to accelerate development of a pilot using the Gazelle design.
Michael Abrams is a science and technology writer in Westfield, N.J.
Now, new platform designs for deeper water offer lighter configurations that can be produced by more manufacturers and sail from a larger number of ports because of their lower draft. They will play an important part in meeting global demand for offshore wind generation, such as the European Commission's goal of generating 450 GW of offshore wind power by 2050.
Ireland’s Gazelle Wind Power has a platform design that may help reduce a production bottleneck and speed the deployment of deepwater floating wind turbines. Gazelle engineers are testing a modified tension leg platform (TLP) that doesn’t require high tension or overly heavy structural materials, can be launched in seven meters of water (or less), and can be towed and assembled with the current fleet of towing vessels. It’s also scalable, so it can handle a range of turbine sizes.
The idea first came to Antonio García, the company’s chief innovation officer, seven years ago. He was disturbed by the number of problems that plague floating platforms with catenary mooring systems, the most common anchor system for offshore platforms.
“They have to be very big, they have to have a lot of buoyancy, and they have to be very heavy,” said Jason Wormald, the company’s chief technology officer. “The mooring footprint on these things can be thousands of meters, you've got installation and handling issues, and they are damaging the seabed. It’s just a nightmare.”
Most TLP designs aren’t much better as an alternative. The lines that connect the platform to the ocean floor demand high tension, requiring about 5,000 tons of anchor line; the tension of each connection must be precisely calibrated. The thousands of tons of tension needed just to connect the tension lines to mooring lines can only be done with heavy-lift vessels. Though they’re stable once connected, there’s no give and take for the rise and fall of the sea, and a mooring line failure can be catastrophic.
Becme a Member: How to Join ASME
Garcia devised a hybrid TLP/semi-submersible with three arms connected to the central platform. Each limb is a pivot that is connected to the sea floor by lines on the outside edge, and to a counterweight under the center of the platform. As a result, motion is transferred to the counterweight, which absorbs the energy, minimizing any tilt to the turbine on top. It’s essentially a passive ballast system.
Most offshore wind turbines are designed to support pitch angles of up to 10 degrees, according to the company. That allows for operation but creates additional wear and tear. The Gazelle design allows the platform to move horizontally and vertically with almost zero pitch and may reduce mooring loads by 50 percent compared to a tension leg platform, claims the firm.
The design will also accommodate production by a greater number of producers. Garcia approached the design from a naval architectural point of view, thinking of the platform less as a structure than as a vessel.
“So, what we've done is come up with a design that uses flat panel technology that effectively uses thin coiled steel with stiffened ribs on it,” said Wormald. “And what that means is that there are thousands of shipyards globally that already have the capability to produce this equipment.”
Listen to Our Podcast; Building Infrastructure for Offshore Wind Power
The buoyancy incorporated in the triangular base allows it to float in the low depth of shipyards and to be towed to its destination using traditional towing vessels. With a foundation and anchors preinstalled, the platform will simply be towed to site and connected to the lines waiting for them on buoys.
“There’s no subsea operation that goes on, there are no divers involved, there are no ROVs,” said Wormald. “You hook up top side, and then all you do is release the counterweight, and the counterweight tensions the lines.”
At the moment, the company is testing a 1/30 scale. Earlier this year Gazelle teamed with Portugal’s WAM Horizon, a renewable energy developer, to accelerate development of a pilot using the Gazelle design.
Michael Abrams is a science and technology writer in Westfield, N.J.
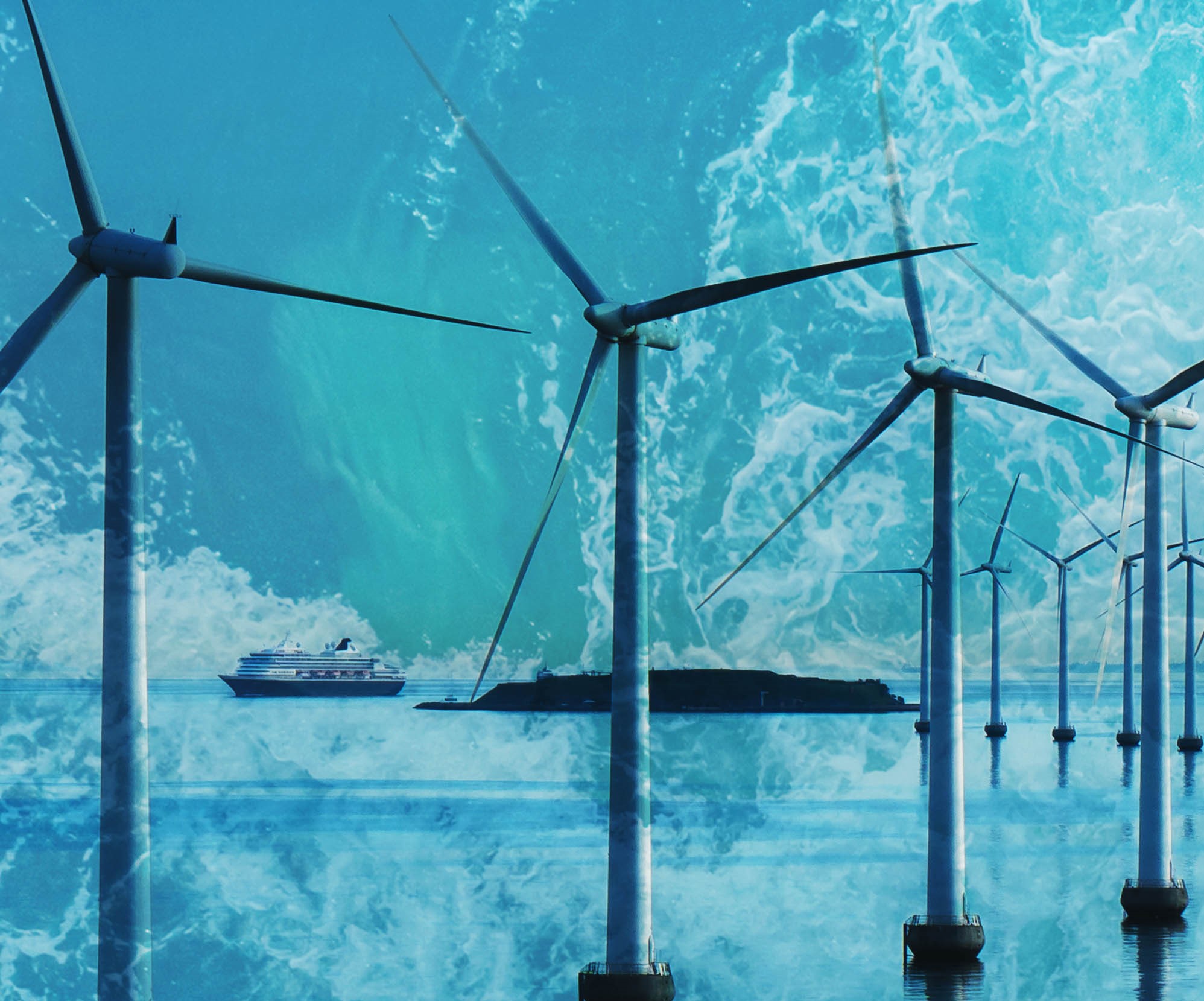
International Offshore Wind Technical Conference
Take a deep dive into innovative projects working to deploy offshore wind faster, more responsibly, and at lower cost. December 18–19, 2023
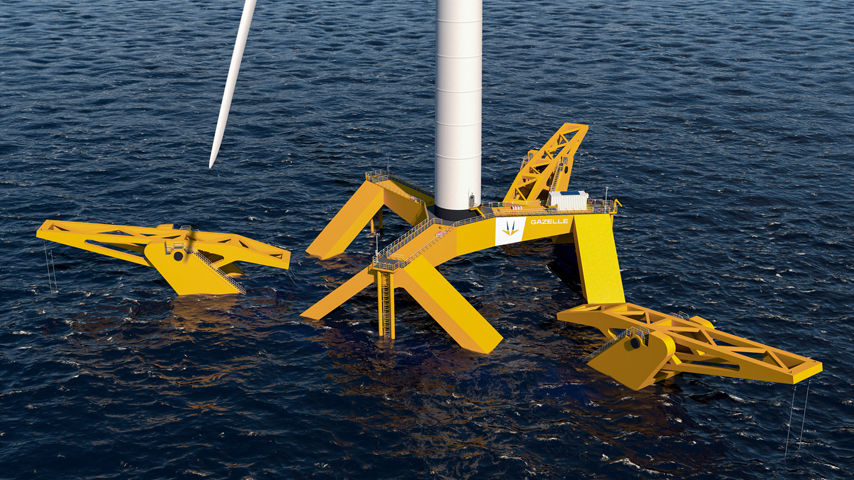
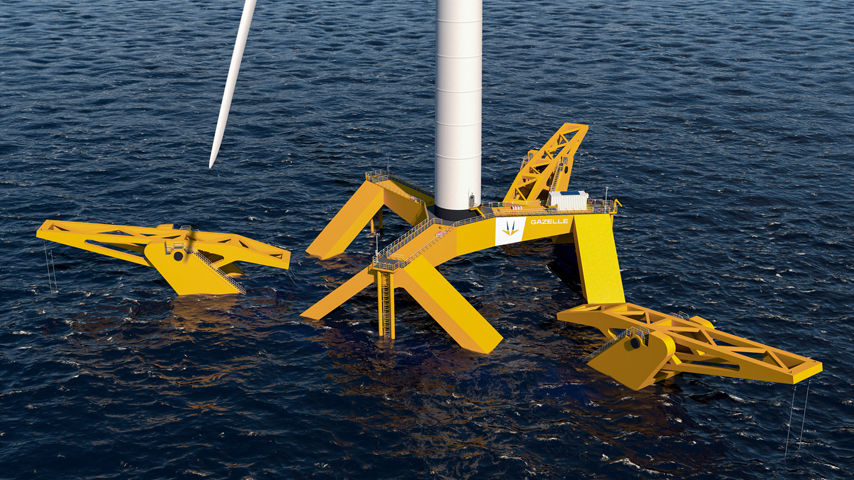