New Refrigeration Method Relies on Ionocaloric Cooling
New Refrigeration Method Relies on Ionocaloric Cooling
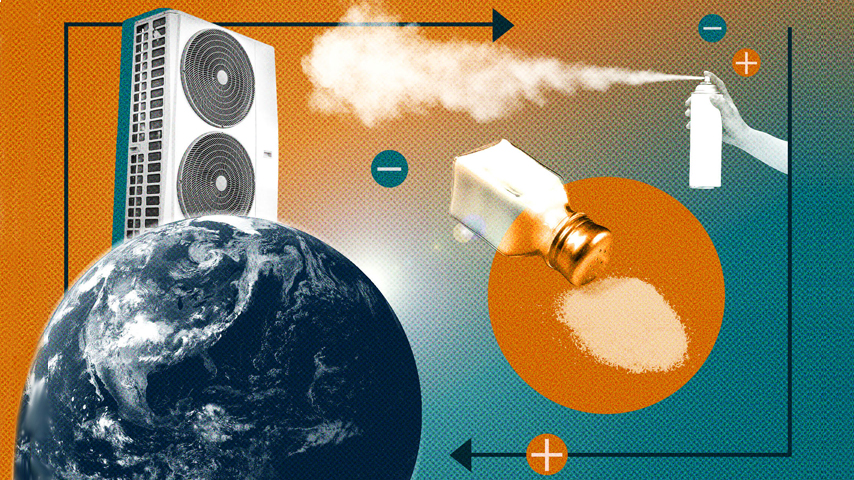
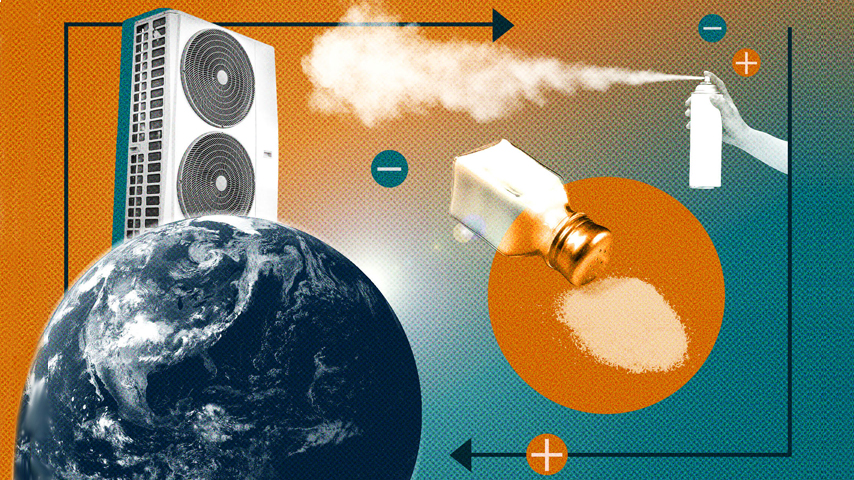
UC Berkeley scientists have developed a cooling method that could replace environmentally unfriendly refrigerants, while also delivering more efficient heating and cooling.
At first, two researchers at the University of California, Berkeley—Ravi Prasher, adjunct professor in mechanical engineering, and graduate student research assistant Drew Lilley—were working on a project for thermal energy storage with the goal of tuning the liquid/vapor phase transition temperature of a material using electricity. But both were struck by the possibility that they could tune a solid/liquid transition the same way.
This insight made Prasher and Lilley wonder how effective a solid/liquid transition would be in a thermodynamic cycle for refrigeration. Caloric effect-based cooling technologies, such as magneto- or electrocaloric refrigeration, have potential, but typically require large electric fields in return for relatively low coefficients of performance and adiabatic temperature change. If the team could create this high-efficiency cooling system with safe, low global warming potential refrigerants, this innovation could have a positive impact on the environment.
Ionocaloric cooling takes advantage of how energy, or heat, is stored or released when a material changes phases. For example, melting a material absorbs heat and solidifying it releases heat. Ionocaloric cooling uses ions that come from a salt to drive solid-to-liquid phase changes. When a current is added, ions flow and change the material from solid to liquid, causing the material to absorb heat from the surroundings. When the process is reversed and ions are removed, the material crystallizes into a solid, releasing heat.
Similar Reading: Using Fluids to Control Energy Use in Buildings
Lilley and Prasher concluded that ionocaloric cooling has potential to compete with, or even exceed, the efficiency of gaseous refrigerants found in the majority of systems today.
They then demonstrated the technique experimentally. Lilley used a salt made with iodine and sodium, alongside ethylene carbonate, which is a safe, common organic solvent used in lithium-ion batteries. Ethylene carbonate has the potential to be global warming potential (GWP)-zero, or even GWP-negative, because it can be produced using carbon dioxide that is captured from other processes.
One of the biggest challenges was finding an ion exchange membrane that worked.
“Most ion exchange membranes are designed for aqueous media and we were using an organic solvent,” Prasher explained. “The organic solvent dissolved most of the membranes we tried, and the ones that survived usually saw very bad performance. We went through 16 different ion exchange membranes before finding one that was compatible with all the materials we used in the system.”
Another challenge was identifying the right material combinations for use in the ionocaloric cycle. “There were five or six variables associated with each material combination, which all had to align, so we had to be especially careful with our choices,” Lilley added.
The ionocaloric heat pump cycles between the solid/liquid states instead of the liquid/vapor states, as is currently done.
“When we cycle between the solid/liquid states, we have to now contend with conveying solid matter, usually in a slurry,” said Prasher. “This is a lot trickier than conveying liquids/gases, which are routinely handled by pumps and compressors. The challenge of dealing with the solids is very interesting at the system level. Very creative and talented engineers will have to come up with some innovative ways to make the solid/liquid loop affordable and effective.”
Become a Member: How to Join ASME
The first experiment showed a temperature change of 25 °C using less than one volt—a greater temperature lift than demonstrated by other caloric technologies. Theoretical and experimental results show higher adiabatic temperature change and entropy change per unit mass and volume compared with other caloric effects under low applied field strengths.
The biggest surprise for Prasher was on the theoretical side. When they calculated the maximum achievable efficiency of the ionocaloric cycle, the researchers saw numbers that hovered around 90 percent to 95 percent relative to Carnot (ideal thermodynamic cycle). “In contrast, the vapor compression systems with current state-of-the-art refrigerants have numbers more like 75 percent to 80 percent,” he said. “As a mechanical engineer, we were always taught that vapor compression is as close to an ideal cycle as anything that can be practically achieved, so I was really surprised and excited that the ionocaloric cycle can take a few steps further on the efficiency.”
Prototype development is underway to test scalability and improve efficiency.
The team has also received a provisional patent for the ionocaloric refrigeration cycle and the technology is now available for licensing. Prasher and Lilley have formed a company, Calion Technologies, and are actively working to make a pilot-scale demonstration using ionocaloric technology.
To date, no one has successfully developed an alternative solution that “makes stuff cold, works efficiently, is safe, and doesn’t hurt the environment,” said Lilley. “We think the ionocaloric cycle has the potential to meet all these goals if realized appropriately.”
Mark Crawford is technology writer in Corrales, N.M.
This insight made Prasher and Lilley wonder how effective a solid/liquid transition would be in a thermodynamic cycle for refrigeration. Caloric effect-based cooling technologies, such as magneto- or electrocaloric refrigeration, have potential, but typically require large electric fields in return for relatively low coefficients of performance and adiabatic temperature change. If the team could create this high-efficiency cooling system with safe, low global warming potential refrigerants, this innovation could have a positive impact on the environment.
How it works
The researchers named their new method of heating and cooling “ionocaloric cooling.”Ionocaloric cooling takes advantage of how energy, or heat, is stored or released when a material changes phases. For example, melting a material absorbs heat and solidifying it releases heat. Ionocaloric cooling uses ions that come from a salt to drive solid-to-liquid phase changes. When a current is added, ions flow and change the material from solid to liquid, causing the material to absorb heat from the surroundings. When the process is reversed and ions are removed, the material crystallizes into a solid, releasing heat.
Similar Reading: Using Fluids to Control Energy Use in Buildings
Lilley and Prasher concluded that ionocaloric cooling has potential to compete with, or even exceed, the efficiency of gaseous refrigerants found in the majority of systems today.
They then demonstrated the technique experimentally. Lilley used a salt made with iodine and sodium, alongside ethylene carbonate, which is a safe, common organic solvent used in lithium-ion batteries. Ethylene carbonate has the potential to be global warming potential (GWP)-zero, or even GWP-negative, because it can be produced using carbon dioxide that is captured from other processes.
One of the biggest challenges was finding an ion exchange membrane that worked.
“Most ion exchange membranes are designed for aqueous media and we were using an organic solvent,” Prasher explained. “The organic solvent dissolved most of the membranes we tried, and the ones that survived usually saw very bad performance. We went through 16 different ion exchange membranes before finding one that was compatible with all the materials we used in the system.”
Another challenge was identifying the right material combinations for use in the ionocaloric cycle. “There were five or six variables associated with each material combination, which all had to align, so we had to be especially careful with our choices,” Lilley added.
The ionocaloric heat pump cycles between the solid/liquid states instead of the liquid/vapor states, as is currently done.
“When we cycle between the solid/liquid states, we have to now contend with conveying solid matter, usually in a slurry,” said Prasher. “This is a lot trickier than conveying liquids/gases, which are routinely handled by pumps and compressors. The challenge of dealing with the solids is very interesting at the system level. Very creative and talented engineers will have to come up with some innovative ways to make the solid/liquid loop affordable and effective.”
Become a Member: How to Join ASME
The first experiment showed a temperature change of 25 °C using less than one volt—a greater temperature lift than demonstrated by other caloric technologies. Theoretical and experimental results show higher adiabatic temperature change and entropy change per unit mass and volume compared with other caloric effects under low applied field strengths.
The biggest surprise for Prasher was on the theoretical side. When they calculated the maximum achievable efficiency of the ionocaloric cycle, the researchers saw numbers that hovered around 90 percent to 95 percent relative to Carnot (ideal thermodynamic cycle). “In contrast, the vapor compression systems with current state-of-the-art refrigerants have numbers more like 75 percent to 80 percent,” he said. “As a mechanical engineer, we were always taught that vapor compression is as close to an ideal cycle as anything that can be practically achieved, so I was really surprised and excited that the ionocaloric cycle can take a few steps further on the efficiency.”
Moving forward
Prasher and Lilley want to balance three things: the GWP of the refrigerant, energy efficiency, and the cost of the equipment itself. “From the first try, our data looks very promising on all three of these aspects,” Prasher said.Prototype development is underway to test scalability and improve efficiency.
The team has also received a provisional patent for the ionocaloric refrigeration cycle and the technology is now available for licensing. Prasher and Lilley have formed a company, Calion Technologies, and are actively working to make a pilot-scale demonstration using ionocaloric technology.
To date, no one has successfully developed an alternative solution that “makes stuff cold, works efficiently, is safe, and doesn’t hurt the environment,” said Lilley. “We think the ionocaloric cycle has the potential to meet all these goals if realized appropriately.”
Mark Crawford is technology writer in Corrales, N.M.
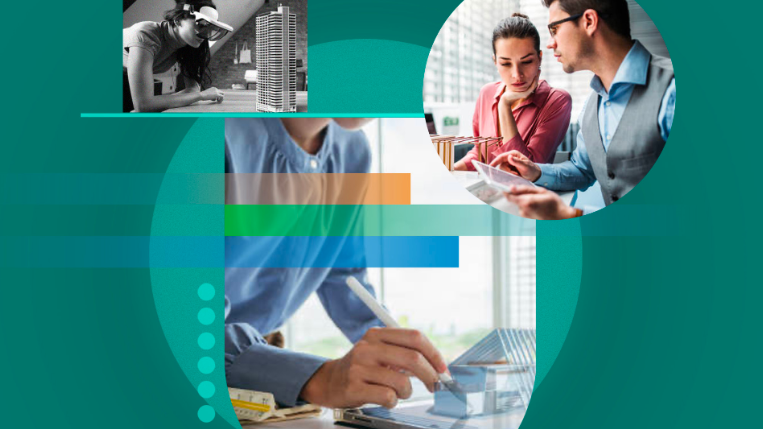
Pulse of the Profession: CAD in 2030
CAD technologies and their applications have been steadily evolving ever since, ushering in a bevy of new techniques and approaches over the decades.
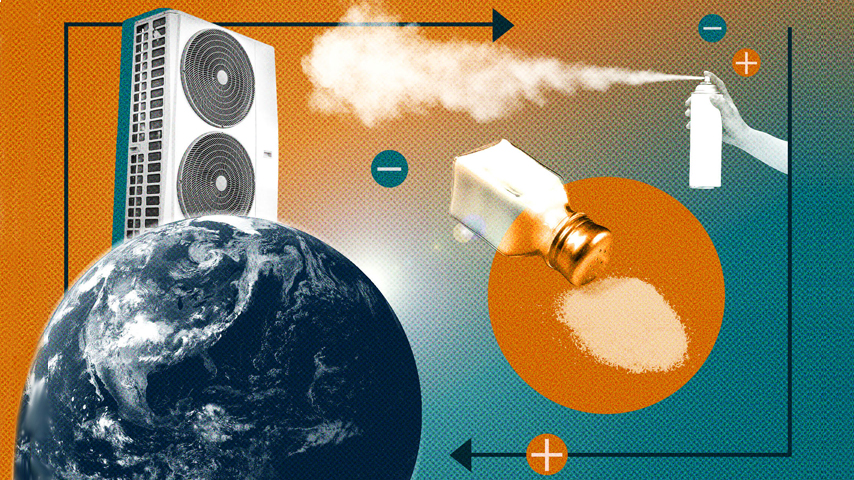
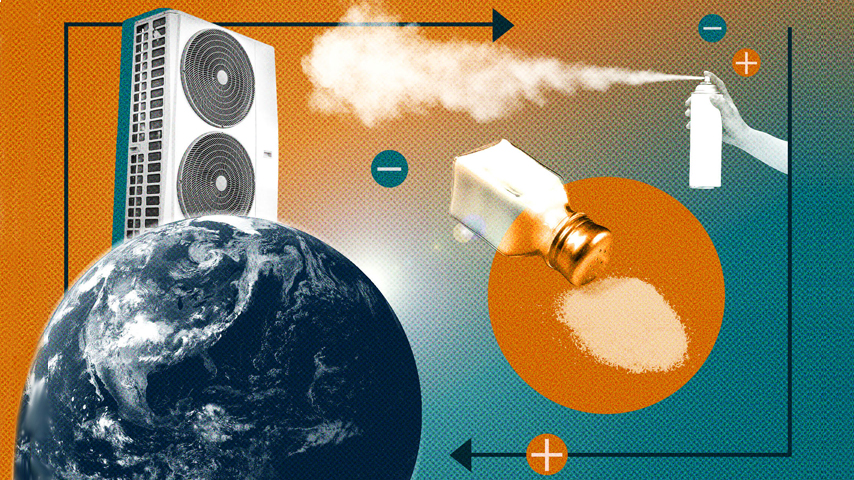