Manufacturing Blog: Should Maintenance Professionals Be Afraid of AI and Automation?
Manufacturing Blog: Should Maintenance Professionals Be Afraid of AI and Automation?
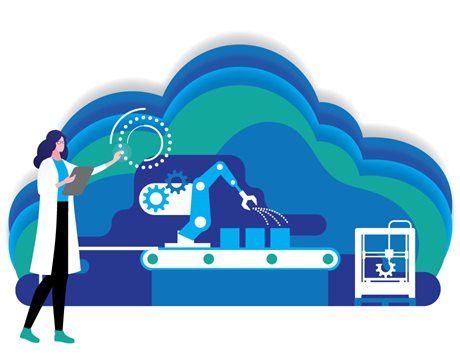
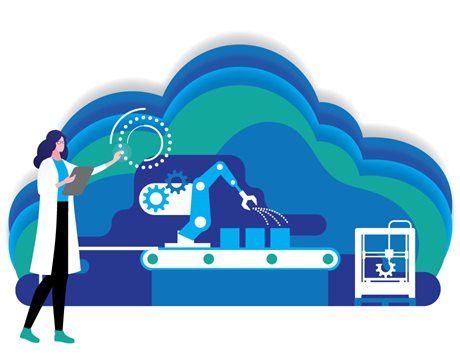
Maintenance professionals may fear that automation will replace them, but in reality it may become their biggest asset.
Most maintenance professionals in manufacturing are aware of the broad digital trends affecting the production floor. These trends—nested under the umbrella of “Industry 4.0”—include automation, artificial intelligence (AI), machine learning (ML), and more.
It is understandable that workers on the production floor may believe that their job is doomed, that they will replaced by robots and computers. Perhaps they have heard the “Lights Out Factory,” the factory where the entire process is automated. In this model, there is no need for humans, therefore the lights don’t even need to be turned on. Some may believe this “Lights Out” idea is the eventual future of all manufacturing.
Despite the views of some influential thinkers today, it is unclear if this vision of a fully automated factory will ever be feasible. Even if so, it is arguably not the optimal way to operate a manufacturing plant, or maintain it.
Let us first lay out general goals for AI and automation. Simply put, most automation projects should have one or more of these goals:
Notice that reducing labor does not appear among these goals. It may be a byproduct, but replacing labor for no reason should not be an objective. Rather, the goal is to move the labor into areas that provide more value.
Toyota, the company mimicked all over the world for its lean principles, has continued a strategy of putting humans first. In a continuous improvement culture, there must be humans on the production floor to find the areas that need improvement. Therefore, the emphasis with automation is to place people where their intellect and creativity can help optimize the process. Automation and AI are tools that aid the maintenance technician in completing their jobs most effectively, either by providing information quickly, error-proofing, or taking repetitive tasks away.
Recommended for You: Soft Robotic Glove Boosts Workers’ Grip
Preventative maintenance (PM) tasks often become a sore subject among maintenance and operations staff. PMs are often overprescribed, which bogs down the maintenance staff in tedious and sometimes frivolous tasks. But PMs should not necessarily be jettisoned for no reason; there can be importance in their completion. This is one area where automation can help.
One of the first areas to automate is scheduling and capturing PM tasks. Rather than conducting PMs on a calendar basis, you could move to schedule based on machine run time. Or better yet, it could be based on the wear and tear that the machine sees, such as changing a filter based on pressure drop, or bearing based on vibration level.
This condition-based maintenance approach requires some automation, but most maintenance professionals agree it is a better method of asset management. Less effort is spent on administrative tasks or needless work, which allows maintenance to focus on more pressing issues.
Building the Factory of the Future: Leveraging New Technologies for the Engineering Workforce
Maintenance has started using AI in certain situations as well. A corollary of condition- based maintenance is predictive maintenance (PdM). With PdM, the conditions of the equipment, along with theoretical or empirical models, are used to predict when a failure will occur. When this information is known, the operation can plan for the repair with minimal disruption.
Taking this further is the concept of prescriptive maintenance (RxM). Besides using AI to predict when a machine will fail, RxM also assists the technician with the repair. It could give information on where to start troubleshooting, what to replace, and much more. Again, these programs aim not to replace maintenance workers, but to ease their jobs by improving the information available to them. Armed with this information, the technician can be more effective, and the plant will run more efficiently. One other thing about AI implementation. It absolutely requires local experts to deploy and function properly. So, the knowledge of maintenance personnel becomes more invaluable in this situation.
Maintenance personnel should be looking for ways that automation can enhance their jobs. By not embracing the wave of available technology, factories could be risking their business. Consider this fact: Research shows that since 2000, 52 percent of companies in the Fortune 500 have either gone bankrupt, been acquired, or ceased to exist as a result of digital disruption. The maintenance manager does not want to add their company to this list.
Check Out Our Video: The State of Robots for Maintenance
The best maintenance strategy will be the one that effectively blends human inventiveness with machine and computer efficiency. Automation will be used alongside the people to help them in their jobs. The need for individuals in maintenance will not go away – at least not for a very long time.
Bryan Christiansen is the founder and CEO of Limble CMMS.
It is understandable that workers on the production floor may believe that their job is doomed, that they will replaced by robots and computers. Perhaps they have heard the “Lights Out Factory,” the factory where the entire process is automated. In this model, there is no need for humans, therefore the lights don’t even need to be turned on. Some may believe this “Lights Out” idea is the eventual future of all manufacturing.
Despite the views of some influential thinkers today, it is unclear if this vision of a fully automated factory will ever be feasible. Even if so, it is arguably not the optimal way to operate a manufacturing plant, or maintain it.
The Goals of Implementing Automation
Let us first lay out general goals for AI and automation. Simply put, most automation projects should have one or more of these goals:
- Increase efficiency in repetitive, mundane tasks.
- Reduce the possibility of errors.
- Increase the amount of information available in order to make intelligent decisions.
Notice that reducing labor does not appear among these goals. It may be a byproduct, but replacing labor for no reason should not be an objective. Rather, the goal is to move the labor into areas that provide more value.
Toyota, the company mimicked all over the world for its lean principles, has continued a strategy of putting humans first. In a continuous improvement culture, there must be humans on the production floor to find the areas that need improvement. Therefore, the emphasis with automation is to place people where their intellect and creativity can help optimize the process. Automation and AI are tools that aid the maintenance technician in completing their jobs most effectively, either by providing information quickly, error-proofing, or taking repetitive tasks away.
Recommended for You: Soft Robotic Glove Boosts Workers’ Grip
Automation and AI in Maintenance
Preventative maintenance (PM) tasks often become a sore subject among maintenance and operations staff. PMs are often overprescribed, which bogs down the maintenance staff in tedious and sometimes frivolous tasks. But PMs should not necessarily be jettisoned for no reason; there can be importance in their completion. This is one area where automation can help.
One of the first areas to automate is scheduling and capturing PM tasks. Rather than conducting PMs on a calendar basis, you could move to schedule based on machine run time. Or better yet, it could be based on the wear and tear that the machine sees, such as changing a filter based on pressure drop, or bearing based on vibration level.
This condition-based maintenance approach requires some automation, but most maintenance professionals agree it is a better method of asset management. Less effort is spent on administrative tasks or needless work, which allows maintenance to focus on more pressing issues.
Building the Factory of the Future: Leveraging New Technologies for the Engineering Workforce
Maintenance has started using AI in certain situations as well. A corollary of condition- based maintenance is predictive maintenance (PdM). With PdM, the conditions of the equipment, along with theoretical or empirical models, are used to predict when a failure will occur. When this information is known, the operation can plan for the repair with minimal disruption.
Taking this further is the concept of prescriptive maintenance (RxM). Besides using AI to predict when a machine will fail, RxM also assists the technician with the repair. It could give information on where to start troubleshooting, what to replace, and much more. Again, these programs aim not to replace maintenance workers, but to ease their jobs by improving the information available to them. Armed with this information, the technician can be more effective, and the plant will run more efficiently. One other thing about AI implementation. It absolutely requires local experts to deploy and function properly. So, the knowledge of maintenance personnel becomes more invaluable in this situation.
Maintenance personnel should be looking for ways that automation can enhance their jobs. By not embracing the wave of available technology, factories could be risking their business. Consider this fact: Research shows that since 2000, 52 percent of companies in the Fortune 500 have either gone bankrupt, been acquired, or ceased to exist as a result of digital disruption. The maintenance manager does not want to add their company to this list.
Check Out Our Video: The State of Robots for Maintenance
The best maintenance strategy will be the one that effectively blends human inventiveness with machine and computer efficiency. Automation will be used alongside the people to help them in their jobs. The need for individuals in maintenance will not go away – at least not for a very long time.
Bryan Christiansen is the founder and CEO of Limble CMMS.
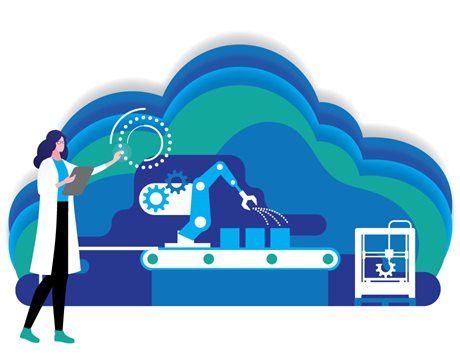
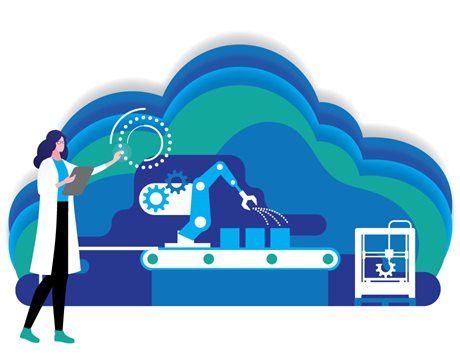