Inspired by an Octopus, Ringbots Flip and Crawl
Inspired by an Octopus, Ringbots Flip and Crawl
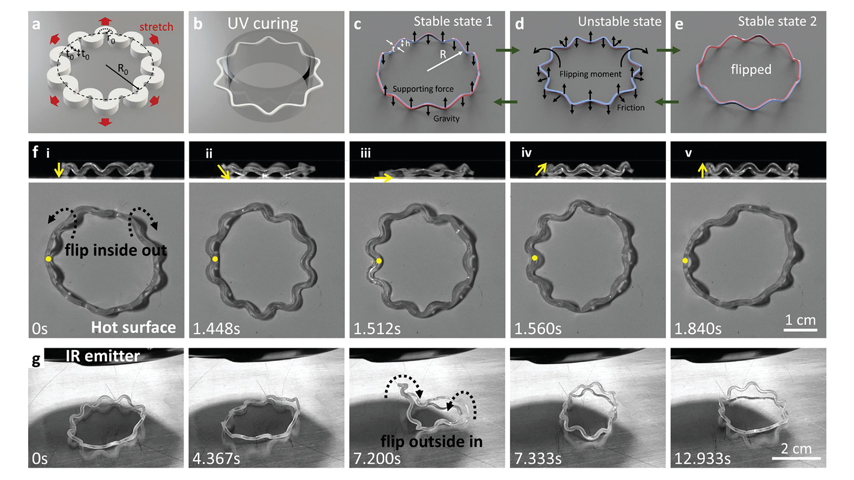
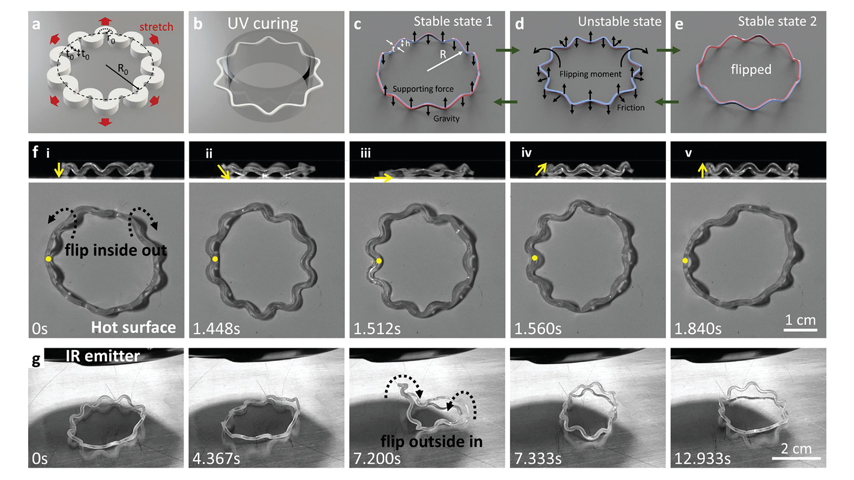
Soft robot responds to heat and moves in a rolling motion.
A research team led by Jie Yin, an associate professor of mechanical and aerospace engineering at North Carolina State University, have created a bracelet-shaped soft robot that crawls across surfaces when exposed to elevated temperatures or infrared light. The robot responds to external stimuli only—no computational input is required. It is also capable of pulling a small payload across a surface and is flexible enough to pass through an opening that is narrower than its ring size.
As is common in mechanical engineering, Yin’s discovery was inspired by movement and structure present in nature. In this case, it was an octopus.
“When an octopus is in a cage with one-inch holes, it can escape through one of these narrow holes by adapting and shrinking its soft body,” said Yin. “This made us wonder if it was possible to design a simplified version of a similar soft robot that can pass through a confined space with the gap size smaller than the soft robot’s body size.”
Become a Member: How to Join ASME
The “ringbot” is made from heat-responsive soft materials called liquid crystal elastomers (LCEs) and shaped like a looped ribbon, resembling a bracelet. When the ringbot is placed on a hot surface that is at least 55˚ C (131˚ F), the part of the ringbot that is in contact with the surface contracts, while the portion of the ringbot that is exposed to the air does not. This induces a rolling motion in the ringbot. Similarly, when exposed to infrared light, the portion of the ringbot exposed to the light contracts, while the portion shielded from the light does not, inducing a similar movement.
Early on, one of biggest challenges for the research team was making the ringbot crawl along in a defined direction. When its first ringbot design was placed on a hot surface, the ringbot continuously flipped, but without forward motion. The researchers realized the robot could not self-crawl because its body shape was too symmetrical and could not generate enough friction for movement.
To make it self-crawl, Yin created a hybrid ringbot design. He changed the left half of the ring to be a twisted wavy shape, while the right half stayed smooth, with no wavy or twisted features.
“This broke the symmetry between left and right halves of the ringbot,” said Yin. “When the loop is exposed to the heat or infrared light unevenly, the soft robot moves laterally across the surface due to asymmetric friction.”
More for You: 7 Soft Designs that are Reimagining Robotics
The biggest surprise for the team came when the self-crawling ringbot was placed within a V-shaped wall on a hot surface. “The ringbot managed to self-squeeze its soft body through adaptive interactions with the walls to pass through a narrow gap, which was about 30 percent narrower than its body size,” said Yin. When the gap size became too small for the ringbot to pass through, it self-directed itself via interactions with the wall to crawl away from the opening.
Yin’s research represents one example of autonomous and intelligent soft robots. Over the next few years, he noted, achieving both autonomy and intelligence in soft robots will be increasingly attractive since it can greatly reduce the burden from the control with on-board devices.
The next steps for his research team are devising new ways for ringbots to pass through smaller gap sizes by designing new shapes for their soft bodies, as well as making ringbots more intelligent in exploring unknown confined spaces and environments.
“For mechanical engineers, most of us are working with hard or stiff materials like metals, ceramic, or semiconductors, which are inert to stimuli,” said Yin. “This work shows the benefits of soft materials, including their responsiveness to heat or light, self-sensing and self-actuation capabilities, and high adaptivity to environments, such as passing through narrow gaps. This work could find potential applications in environmental monitoring, especially in hard-to-access confined spaces and harsh environments.”
Mark Crawford is a science and technology writer in Corrales, N.M.
As is common in mechanical engineering, Yin’s discovery was inspired by movement and structure present in nature. In this case, it was an octopus.
“When an octopus is in a cage with one-inch holes, it can escape through one of these narrow holes by adapting and shrinking its soft body,” said Yin. “This made us wonder if it was possible to design a simplified version of a similar soft robot that can pass through a confined space with the gap size smaller than the soft robot’s body size.”
Become a Member: How to Join ASME
The “ringbot” is made from heat-responsive soft materials called liquid crystal elastomers (LCEs) and shaped like a looped ribbon, resembling a bracelet. When the ringbot is placed on a hot surface that is at least 55˚ C (131˚ F), the part of the ringbot that is in contact with the surface contracts, while the portion of the ringbot that is exposed to the air does not. This induces a rolling motion in the ringbot. Similarly, when exposed to infrared light, the portion of the ringbot exposed to the light contracts, while the portion shielded from the light does not, inducing a similar movement.
Early on, one of biggest challenges for the research team was making the ringbot crawl along in a defined direction. When its first ringbot design was placed on a hot surface, the ringbot continuously flipped, but without forward motion. The researchers realized the robot could not self-crawl because its body shape was too symmetrical and could not generate enough friction for movement.
To make it self-crawl, Yin created a hybrid ringbot design. He changed the left half of the ring to be a twisted wavy shape, while the right half stayed smooth, with no wavy or twisted features.
“This broke the symmetry between left and right halves of the ringbot,” said Yin. “When the loop is exposed to the heat or infrared light unevenly, the soft robot moves laterally across the surface due to asymmetric friction.”
More for You: 7 Soft Designs that are Reimagining Robotics
The biggest surprise for the team came when the self-crawling ringbot was placed within a V-shaped wall on a hot surface. “The ringbot managed to self-squeeze its soft body through adaptive interactions with the walls to pass through a narrow gap, which was about 30 percent narrower than its body size,” said Yin. When the gap size became too small for the ringbot to pass through, it self-directed itself via interactions with the wall to crawl away from the opening.
Yin’s research represents one example of autonomous and intelligent soft robots. Over the next few years, he noted, achieving both autonomy and intelligence in soft robots will be increasingly attractive since it can greatly reduce the burden from the control with on-board devices.
The next steps for his research team are devising new ways for ringbots to pass through smaller gap sizes by designing new shapes for their soft bodies, as well as making ringbots more intelligent in exploring unknown confined spaces and environments.
“For mechanical engineers, most of us are working with hard or stiff materials like metals, ceramic, or semiconductors, which are inert to stimuli,” said Yin. “This work shows the benefits of soft materials, including their responsiveness to heat or light, self-sensing and self-actuation capabilities, and high adaptivity to environments, such as passing through narrow gaps. This work could find potential applications in environmental monitoring, especially in hard-to-access confined spaces and harsh environments.”
Mark Crawford is a science and technology writer in Corrales, N.M.
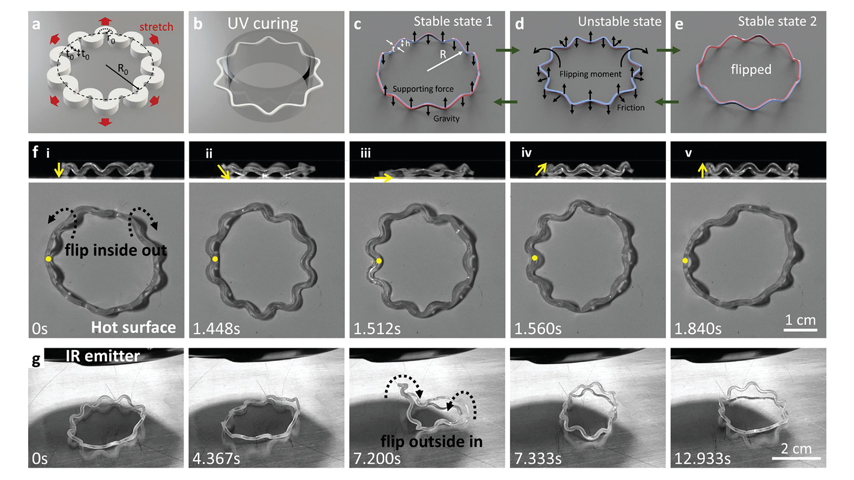
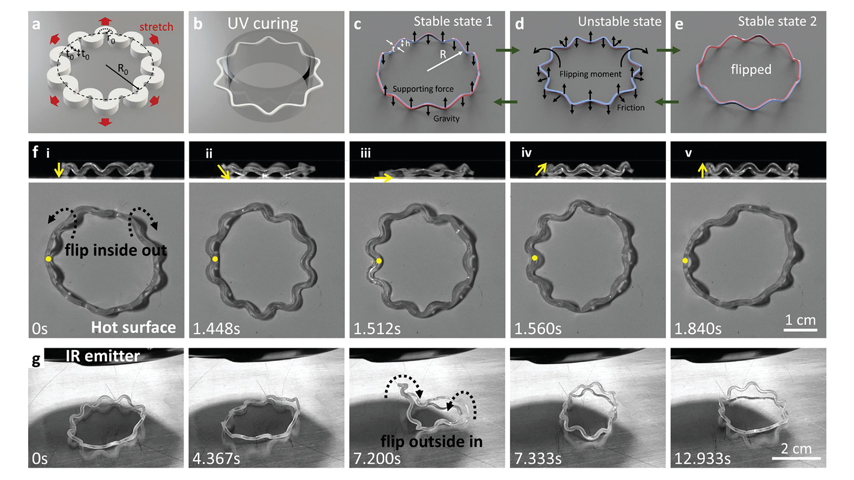