Electrospinning Carbon Fibers from Petroleum Byproducts
Electrospinning Carbon Fibers from Petroleum Byproducts
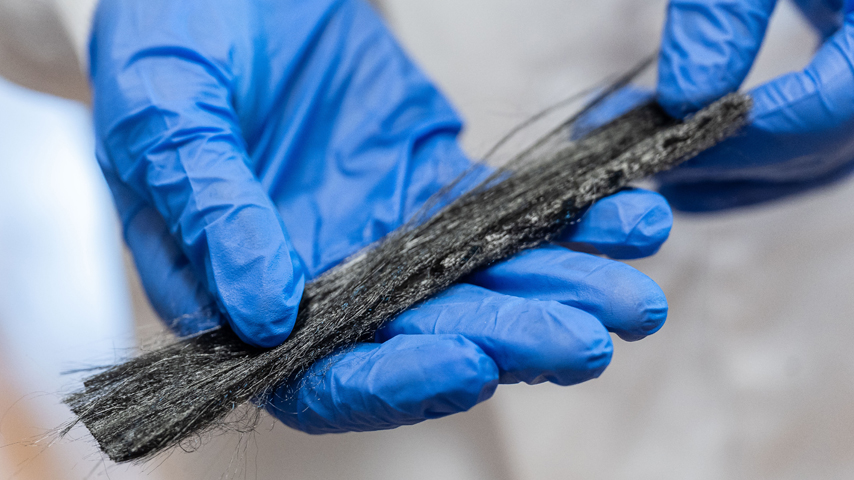
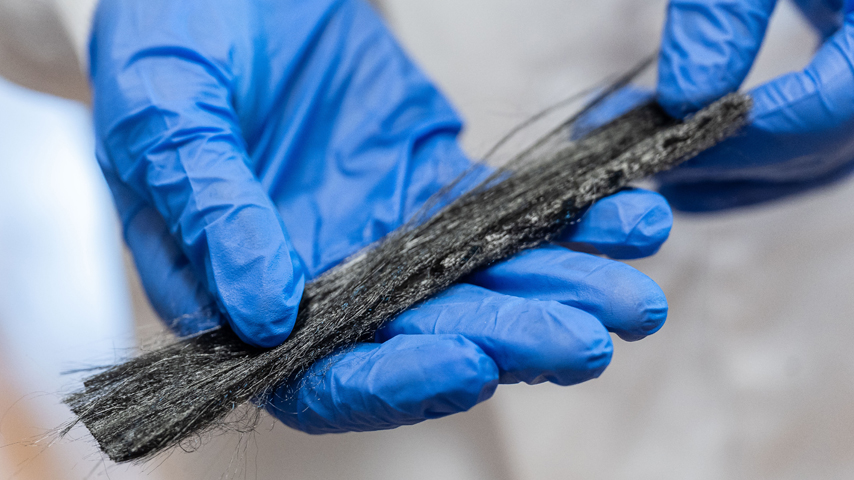
Canada’s oil sands process large volumes of bitumen. A new method of producing carbon fiber may better monetize some of the those byproducts.
A team of researchers at the University of British Columbia’s Vancouver campus has developed a method to turn asphaltene—a byproduct of bitumen processing—into a carbon-fiber replacement for many other materials.
The key innovation lies in the first step of carbon fiber creation, the spinning process. The most common methods to spin carbon fiber are through processes called solution or melt spinning, which produces micron-sized fibers. The polymer blend is melted and extruded through a small orifice in a device called a spinneret. When the material contacts the air or liquid downstream, it solidifies into fibers which are wound like a ball of yarn and later used to make carbon fiber.
The UBC team developed a unique method to create bitumen carbon fibers using electrospinning. An electrical charge draws fibers from a polymer liquid solution, producing sub-micron fibers roughly 500 nanometers in diameter. These fibers are ideal for energy storage applications such as super capacitors and massless or structural batteries.
There is not a standard application and performance of carbon fiber. Each recipe and manufacturing process produces different results. For example, in electric vehicles, traditional melt-spun carbon fiber could be used to construct the load-carrying structure of the vehicle, and electro-spun fibers could be used for energy storage to replace the heavy and bulky batteries.
“Melt spinning produces the traditional geometry of micron sized fibers in the range of seven to ten microns,” said Yasmine Abdin, an assistant professor in UBC’s Department of Materials Engineering. “Those are typically used for structural applications, such as vehicle structure for automotive components.”
Her team is one of 20 teams across North America competing in the Alberta Innovates’ Carbon Fiber Grand Challenge (CFGC). The goal is to develop methods for commercial manufacturing of various carbon-fiber products using asphaltene as a base material in the recipe.
Become a Member: How to Join ASME
The competition is broken up into three phases. “Phase one was a proof of concept to see if we could spin any fibers from asphaltene,” Abdin said. “Then in phase two, we worked on optimizing those fibers. We had a very intensive and dedicated focus and have successfully developed several technologies for spinning fibers. In phase three, which is underway now, we want to make sure our fiber properties are reliable and consistent in large production rates. After phase three is done, we are looking at full commercialization.”
Traditional carbon-fiber production for aerospace, defense, and similar applications needs to meet very high-performance requirements, but this is a small and expensive market. “We’re looking at utilizing the low-cost electro-spun carbon fibers for mass production markets like automotive and sporting goods,” Abdin said.
In Alberta, oil sand is a naturally occurring petrochemical imitating a grainy version of cold molasses at room temperature. It is made up of sand, clay, minerals, water, and bitumen, a dense and viscous form of petroleum. Through a hot water separation process developed in 1926 perfected over the decades, the bitumen is separated from the other materials and transported to refining facilities. To make the bitumen less viscous and easier to transport, the asphaltene is removed first and discarded. While there are some uses for asphaltene in construction materials, the supply greatly outweighs the demand.
More for You: Spinning a Bandage
Carbon fibers are a great manufacturing substitute for metal or fiberglass due to the high strength to weight ratio, high chemical resistance, and high temperature tolerance. The most common raw material for carbon-fiber production is polyacrylonitrile (PAN), a costly synthetic resin. The manufacturing process of PAN-based carbon fiber is expensive, driving production into niche markets such as aerospace, where the benefits of a stronger and lighter material outweigh the high cost.
Traditional carbon-fiber production includes four steps; spinning to develop the fibers, stabilization to pre-heat and stretch the fibers with air up to 570 °F (300 °C), carbonization to remove non-carbon atoms by heating the fibers with nitrogen or argon up to 3,090 °F (1,700 °C), and graphitization to heat the fibers a third time with nitrogen or argon up to 5,070 °F (2,800 °C).
Commercially manufacturing electro-spun carbon fiber using an oil sands byproduct will greatly expand the characteristics, performance, and potential applications of carbon fiber materials. In the automotive industry specifically, using this new carbon fiber to reduce the weight of electric vehicles will improve performance, extend the driving range, and boost the adoption of electric vehicles.
Nicole Imeson is an engineer and wrtier in Calgary, Alberta.
The key innovation lies in the first step of carbon fiber creation, the spinning process. The most common methods to spin carbon fiber are through processes called solution or melt spinning, which produces micron-sized fibers. The polymer blend is melted and extruded through a small orifice in a device called a spinneret. When the material contacts the air or liquid downstream, it solidifies into fibers which are wound like a ball of yarn and later used to make carbon fiber.
The UBC team developed a unique method to create bitumen carbon fibers using electrospinning. An electrical charge draws fibers from a polymer liquid solution, producing sub-micron fibers roughly 500 nanometers in diameter. These fibers are ideal for energy storage applications such as super capacitors and massless or structural batteries.
There is not a standard application and performance of carbon fiber. Each recipe and manufacturing process produces different results. For example, in electric vehicles, traditional melt-spun carbon fiber could be used to construct the load-carrying structure of the vehicle, and electro-spun fibers could be used for energy storage to replace the heavy and bulky batteries.
“Melt spinning produces the traditional geometry of micron sized fibers in the range of seven to ten microns,” said Yasmine Abdin, an assistant professor in UBC’s Department of Materials Engineering. “Those are typically used for structural applications, such as vehicle structure for automotive components.”
Her team is one of 20 teams across North America competing in the Alberta Innovates’ Carbon Fiber Grand Challenge (CFGC). The goal is to develop methods for commercial manufacturing of various carbon-fiber products using asphaltene as a base material in the recipe.
Become a Member: How to Join ASME
The competition is broken up into three phases. “Phase one was a proof of concept to see if we could spin any fibers from asphaltene,” Abdin said. “Then in phase two, we worked on optimizing those fibers. We had a very intensive and dedicated focus and have successfully developed several technologies for spinning fibers. In phase three, which is underway now, we want to make sure our fiber properties are reliable and consistent in large production rates. After phase three is done, we are looking at full commercialization.”
Traditional carbon-fiber production for aerospace, defense, and similar applications needs to meet very high-performance requirements, but this is a small and expensive market. “We’re looking at utilizing the low-cost electro-spun carbon fibers for mass production markets like automotive and sporting goods,” Abdin said.
In Alberta, oil sand is a naturally occurring petrochemical imitating a grainy version of cold molasses at room temperature. It is made up of sand, clay, minerals, water, and bitumen, a dense and viscous form of petroleum. Through a hot water separation process developed in 1926 perfected over the decades, the bitumen is separated from the other materials and transported to refining facilities. To make the bitumen less viscous and easier to transport, the asphaltene is removed first and discarded. While there are some uses for asphaltene in construction materials, the supply greatly outweighs the demand.
More for You: Spinning a Bandage
Carbon fibers are a great manufacturing substitute for metal or fiberglass due to the high strength to weight ratio, high chemical resistance, and high temperature tolerance. The most common raw material for carbon-fiber production is polyacrylonitrile (PAN), a costly synthetic resin. The manufacturing process of PAN-based carbon fiber is expensive, driving production into niche markets such as aerospace, where the benefits of a stronger and lighter material outweigh the high cost.
Traditional carbon-fiber production includes four steps; spinning to develop the fibers, stabilization to pre-heat and stretch the fibers with air up to 570 °F (300 °C), carbonization to remove non-carbon atoms by heating the fibers with nitrogen or argon up to 3,090 °F (1,700 °C), and graphitization to heat the fibers a third time with nitrogen or argon up to 5,070 °F (2,800 °C).
Commercially manufacturing electro-spun carbon fiber using an oil sands byproduct will greatly expand the characteristics, performance, and potential applications of carbon fiber materials. In the automotive industry specifically, using this new carbon fiber to reduce the weight of electric vehicles will improve performance, extend the driving range, and boost the adoption of electric vehicles.
Nicole Imeson is an engineer and wrtier in Calgary, Alberta.
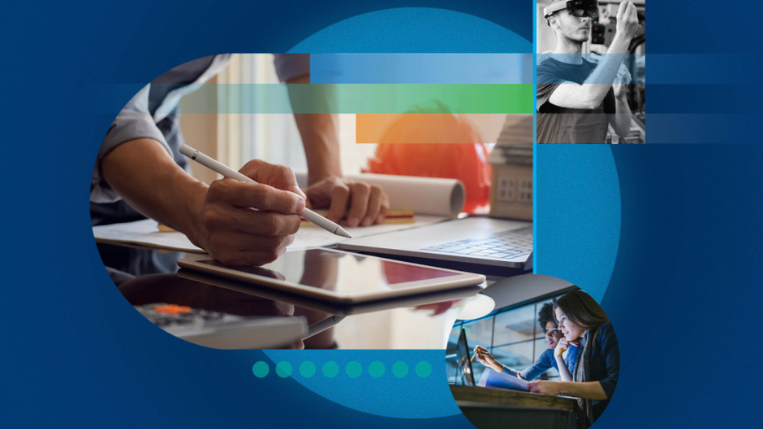
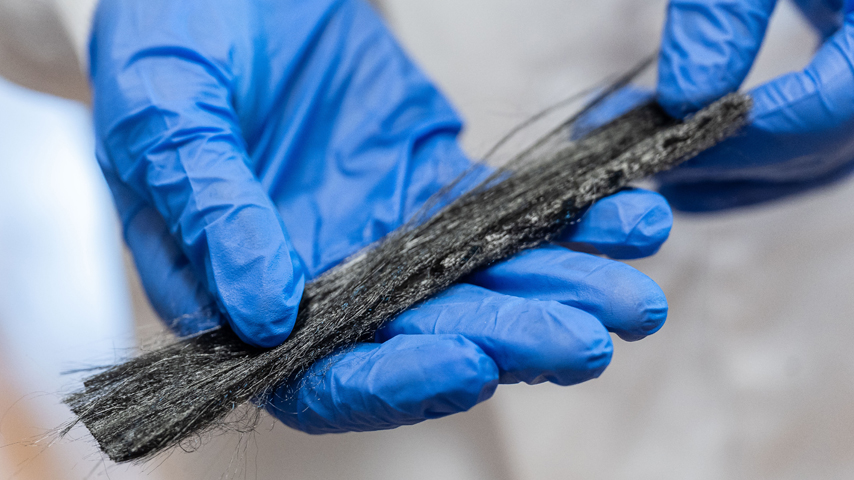
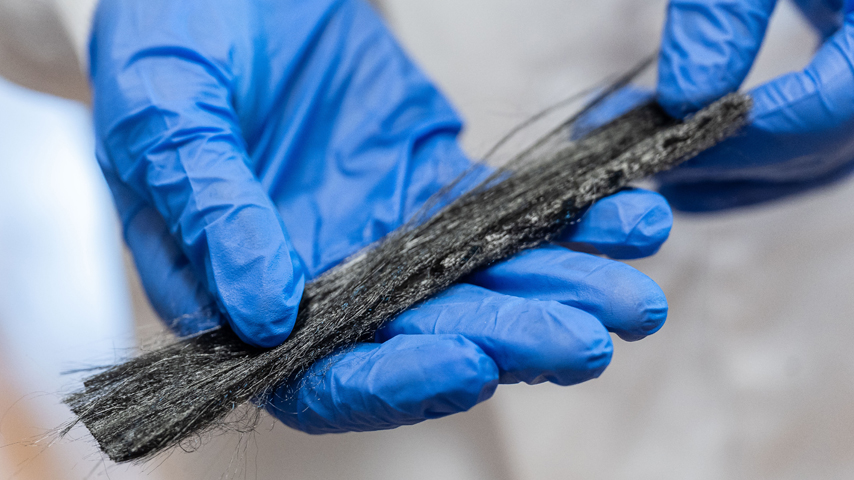