Cleaning Up Industrial Water
Cleaning Up Industrial Water
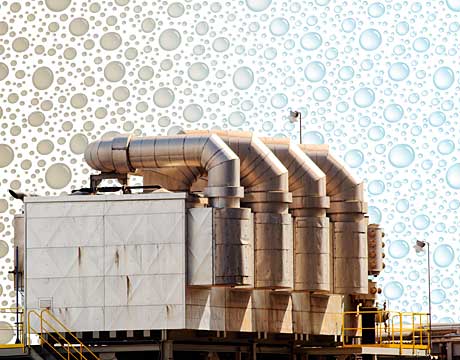
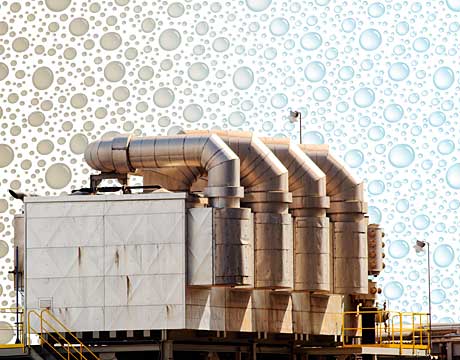
Water—clean water—is one of life's essentials. People need it to live and industry needs it to churn out products ranging from computer chips to electricity. As access to stable supplies of clean, fresh water shrinks, municipalities and industry are looking to other sources and the technologies to cleanse them of salts, minerals, and pollutants. Putting together a successful project requires a host of project participants to maneuver through a range of regulatory, technological, and communication barriers, hopefully following a series of best practices.
Identifying and defining those practices, as well as obstacles, is the goal of industry professionals convened by ASME to tackle the development and implementation of industrial demineralization, or desalination, technologies. The group, which met January 28-29 in Washington, D.C., is working along the parameters of an earlier group tasked with investigating best practices and future directions of municipal wastewater reuse by electric utilities.
There are similarities: electric generating stations as well as process plants or other industrial facilities require a water supply treated to specific quality. It is critical that water professionals from the owner define the water chemistry required and communicate that to prospective vendors and engineering-construction firms. The concept seems simple enough but group members agreed it does not always occur.
"What happened to the process engineer?" asked Doug Hubbard, manager of generation chemistry standard and controls for American Electric Power, the giant Columbus, OH-based electric utility. "Who takes ownership?"
Pick and Choose
Desalination, with a long history of producing drinking water from seawater, is not new. But it is energy intensive and expensive. The Middle East is studded with plants, the largest to produce 228 million gallons per day, using multi-stage flashing and reverse-osmosis technology. Membrane technology is newer than distallation, with reverse/osmosis being the most widely used system for desalination in the U.S. It uses pressure as a force to drive saline water through semipermeable membranes, producing a stream of brine and another of clean product water. It primarily removes sodium and chloride; nanofiltration is also a membrane process that removes calcium, magnesium, and sulphates.
In the U.S., the most high-profile demineralization project belongs to Carlsbad, CA. The southern California city and San Diego County are being squeezed by higher prices and reduced volume for drinking water brought in from northern California and the Colorado River. The privately owned 50,000-gallon-per-day plant will desalinate seawater for drinking water, meeting about 7% of the region's needs, according to city water officials. But industrial users across the country depend on clean water just as much, and often need their water treated to above federal drinking water standards.
Participants also warned of expected zero-liquid-discharge requirements coming in the not-too-distant future. Technically, that can mean building a pond within the industrial plant's boundaries but more often it is evaporators, crystalizers, or electrodialysis. All are costly and generally driven by regulatory obligations, often in regions where water is scarce, making reuse cost-effective.
At the Source
Identifying the properties of the source water and defining the quality of the product water are perhaps the first two keys to producing a successful project, agreed workshop members. Ideally, there should be three to five years of data on source water quality to ensure a proper treatment system. Designing and building a system with limited data courts trouble: A system designed to handle one type of water could fail, or produce a product that compromises the industrial plant's equipment.
Details are often overlooked because the cost of a water treatment plant is minor compared to overall project costs, said workshop members, who noted that off-the-shelf systems are often recommended by vendors when an engineered system is the better answer.
The workshop produced groupings describing characteristics of successful projects and barriers to success. Participants agreed that successful projects have the following characteristics:
- Defensible design basis for inlet water quality and sufficient quality and quantity of inlet and discharge water data, with adequate history.
- Frequent and meaningful communication among all project participants, including the owner, solution provider, and architecture/engineering firm, potentially written into the contract.
- The solution provider has proven, successful prior experience.
- The owner has prioritized cost, performance, reliability, and operability, a thorough cost estimate based on full economic analysis.
- Performance specifications for each piece of equipment are provided.
Barriers to success were found to include:
- Unclear project objectives or mid-steam changes in scope.
- No regulatory drivers to create a sense of urgency.
- The owner's abdication of project management responsibility.
- Lack of "real world" experience by design professionals.
- Anti-innovation bias.
- Water projects not viewed as a revenue enhancer by owner's financial staff, a view that often results in an inadequate final system.
The group will review the findings with the goal of producing a report to enhance best practices and future initiatives within the industry.
"What I need is a document that becomes the industry best practice or standard for desalination system and equipment design," said Hubbard. "Something that forces everybody's hand to do this right."
What I need is a document that becomes the industry best practice or standard for desalination system and equipment design. Something that forces everybody's hand to do this right.Doug Hubbard, American Electric Power
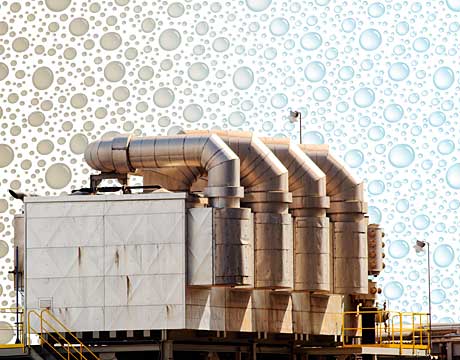
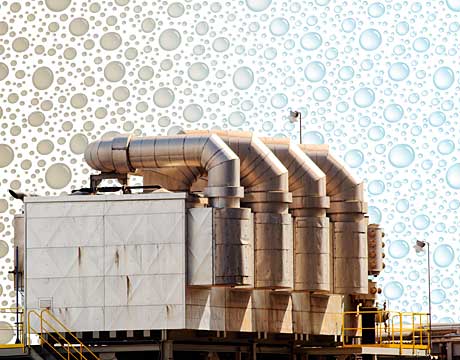