Building Robot Brawn with AI Brains
Building Robot Brawn with AI Brains
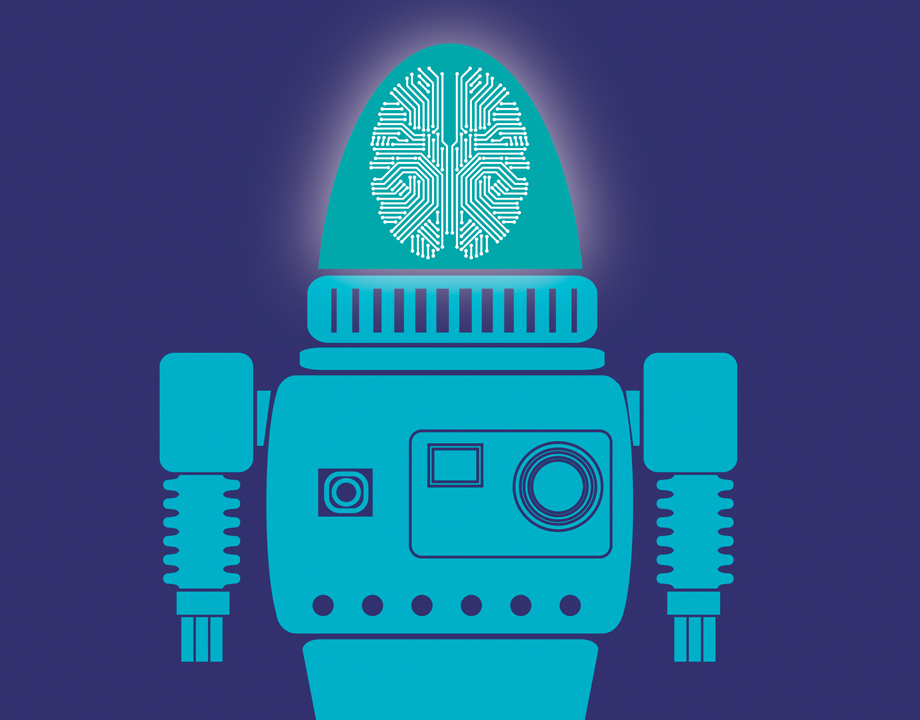
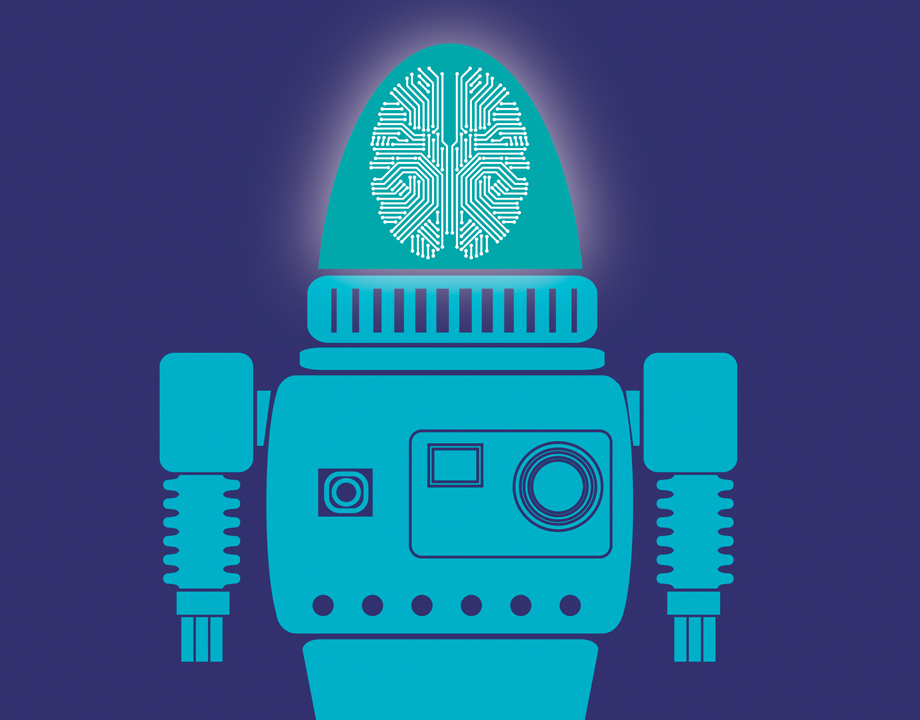
Industrial robots are used for all sorts of dangerous, repetitive jobs. Now that robots are being combined with artificial intelligence, will they take over the rest of the factory floor?
Today, advances in artificial intelligence, or AI, may be changing that equation. There are now many organizations that are utilizing some form of AI- or machine learning (ML)-powered robotics to help with automation capabilities; both Tesla and Siemens come to mind. While the actual applications in place vary quite a bit from organization to organization, Matthew Gombolay, head of the Cognitive Optimization and Relational (CORE) Robotics Lab at the Georgia Institute of Technology in Atlanta, said one of the most well-known AI robot success stories involves Amazon’s warehouse robots, which carry shelves of products to and from different areas of the warehouse using barcodes on the floor to find their way. (They use the barcodes, by the way, not because they have to—they could find their own way over time—but for the safety of the human warehouse workers also milling around the premises).
“Amazon has hundreds of thousands of these hockey puck-like robots that move products around their warehouses,” he said. “We also see robots in stores like Walmart that can clean and restock shelves. There are even robots at BMW that can bring parts to and from anywhere in the factory. It’s getting to the point where these robots can do a lot of different things. They don’t need to be fixed in one location, doing a single repetitive task, caged off from the rest of the operation.”
More on this topic: Service with a Robot Smile
These smarter, more flexible robots are creating opportunities to rethink the way manufacturing operations are structured. Robotics with AI integration can do more than just operate a single, set routine. They can look, sense, feel, and make decisions, reducing their reliance on computer programming to function.
“In many ways, the combination of AI and robotics is not a new thing,” said Tom Hummel, vice president of technology at Rapid Robotics in San Francisco. “But the systems that are currently out there remain quite bespoke. There’s a huge market and need for smarter robotics. But the real issue is how we use the latest advances in AI/ML to create a product that actually scales and can be used across a number of different markets.”
As companies find new and innovative ways to meaningfully couple AI/ML programming with robotics, there is huge potential to change the way manufacturers can and will do business. But what might those changes mean for factories—and manufacturing engineers—in 10 years’ time?
On the Verge
Robots are already a common sight on factory floors. According to the International Federation of Robotics, there are nearly three million industrial robots in use today, with an estimated 370,000 units deployed in 2019 alone. During the first phases of the global coronavirus pandemic, however, manufacturers that had already invested in robots and other Industry 4.0 solutions discovered they had a significant advantage, able to adjust quickly to disruptions created by labor shortages, public health mandates, and demand for new products.
Check Out Our Robotics Blog: Robotics Automation Explores New Frontiers
“What we kept hearing from our customers was the importance of flexibility in response to what was happening,” he said. “If you need to switch a line that’s making giant pistons to making tiny pistons—the sort that might go on a ventilator—their existing automation solutions weren’t going to cut it. They needed more flexibility in their operations and were looking toward AI solutions to get that.”
Manufacturers, even outside of pandemic response, are now realizing the potential of robotics with AI integration. And they are ready to get on board.
“We’re on the verge of rethinking about how robots can and should be used in the workspace,” Gombolay said. “AI is opening up the possibility of allowing manufacturers greater flexibility and agility in their product lines, and improving how quickly they can respond to market demand. That’s huge.”
Some of this is due to advances in hardware. For instance, the cost of sensors, cameras, and computer processors have dropped fast, enabling robots a better visualize their surroundings.
But software, such as AI-based computer vision applications, is harnessing that hardware in a way that makes robots more capable than ever before. According to Juan Aparicio Ojea, vice president of products at Ready Robotics, many companies are exploring different types of AI solutions, including those that support autonomous pick and place tasks.
“Grasping, for a very long time, was the holy grail of robotics,” Aparicio Ojea said. “When you consider all the operations that occur in a factory, a large majority of them are pick and place. For a long time, we couldn’t make robots that could pick up and grasp things as fast or as accurately as humans do. But, now, we are seeing some robots that can achieve human-like rates of picking.”
Other forward-thinking organizations have used Industry 4.0 applications to allow operators to monitor and control different manufacturing machines remotely, which allowed them to continue production during the worst of the pandemic last year.
“Companies like Tesla have fully automated almost all of their production line,” said Amir Barati Farimani, head of the Mechanical and Artificial Intelligence Laboratory, at Carnegie Mellon University in Pittsburgh. “Operators can see what’s happening on the floor, even control different aspects of production, remotely. In some cases, they’ve also installed sensors that can predict the behavior of the different machines and identify potential problems before they happen.”
Hummel said that as these advances continue, the field is undergoing a transformation regarding the way AI-powered robots should be used in manufacturing spaces. There is certainly a huge potential for smart robotics, and organizations are quickly realizing that the adoption of such technologies can make them more efficient, more productive, and, as a consequence, more competitive. However, instead of old-school ideas about replacing human factory workers with some sort of super robots, Hummel said many organizations are now more interested in solutions that can leverage robotics with AI integration to augment their employees’ abilities.
“The idea is to make the human more effective,” Hummel said. “You can’t automate every step of the manufacturing process. But when you can take your human workforce and put them on jobs that actually require a human to do—some manufacturing steps, like assembly and quality control are actually quite complex and need that human element—you can then leave the more repetitive or physically demanding tasks to the robots, so you can increase the work your company can take on and improve your business.”
Working Together
As manufacturing engineers, roboticists, and AI/ML programmers consider the future of the factory and how to inspire more widespread adoption of robotics with AI integration, they will need to address a variety of challenges. If the future is collaborative, as Hummel suggested, then robots need to be designed to safely operate next to human workers, said Jessica Cauchard, a computer scientist at Ben Gurion University of the Negev in Beersheba, Israel. She studies how people will interact with technologies in the future.
Editor’s Choice: Driverless Cars Will Race at Indy
Artificial intelligence can help in this, too, since AI/ML can not only be trained to differentiate between types of parts to pick up, but also to read human expressions. “A lot of communication that happens between co-workers involves nonverbal cues or direction,” Cauchard said. “Right now, robots cannot understand those cues, and they will need in order to be fully integrated in some factory environments.”
What’s more, Aparicio Ojea said, to get full use of AI capabilities, robots will need to upgrade other senses in addition to vision.
“We have made a lot of progress in vision, but we haven’t made as much progress with regards to the haptic information involved with grasping,” he said. “If you think about trying to put your key in the door at night, you can’t get it in with just your vision. You need to feel that the key is connected in the lock and is more or less in place. I think that’s the next domain we need to explore to make the leap to better and broader applications in manufacturing.”
Finally, Gombolay said mechanical engineers and roboticists should start thinking beyond the typical arm-like manufacturing robot to see greater acceptance. Today’s industry robots may be lighter and less expensive than GM’s Unimate, but they still conform to the same basic shape.
“I think we would benefit from designs that aren’t elastic, actuator-based robots,” he said. “We now have snake-like robots and origami-like designs, but we haven’t figured out how to make those types of robots useful. Manufacturing robots that are smart, safe, and, perhaps, have breakaway components or some other non-traditional design could offer us new ways to make hardware for the factory that is more accurate and more controllable than what we have now.”
When these sorts of changes will be realized on the factory floor is anyone’s guess. As has been seen with the development of autonomous vehicles, integrating AI and automation is not a smooth process.
Frontiers of Robotics: Construction Robots that Read Your Mind
“We were talking about the future of AI and robotics when I was a Ph.D. student at MIT. Then, these advances were going to happen 10 years in the future,” Veo Robotics’s Sobalvarro said. “I’ve been out of MIT for a long time now, but the discussion still is about what’s going to happen 10 years from now.”
Realizing the full potential of AI, Farimani said, will require mechanical engineers and robot designers who understand computer science and probability, as well as the manufacturing space. They can provide the kinds of designs and algorithms to take manufacturing far beyond Industry 4.0.
“As we put more sensors on manufacturing machines, we are going to have an ambush of data—videos, images, acoustics, vibrations, and more,” he said. “But we still need to figure out what to do with all that data. In the next four or five years, I think we can learn quite a bit from this data that will direct how these robots might work in the future. Engineers who understand the fundamentals of linear algebra, statistics, probability, and machine learning, and who can make sense of all this information, are going to be the ones who end up driving where we eventually go.”
Kayt Sukel is a science and technology writer based in Houston, Texas.
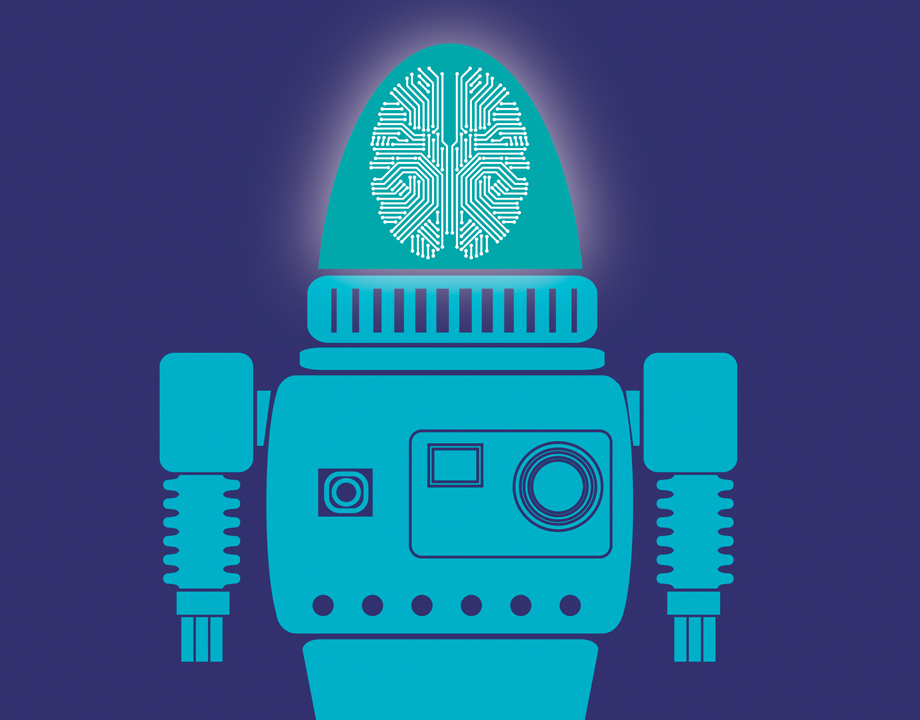
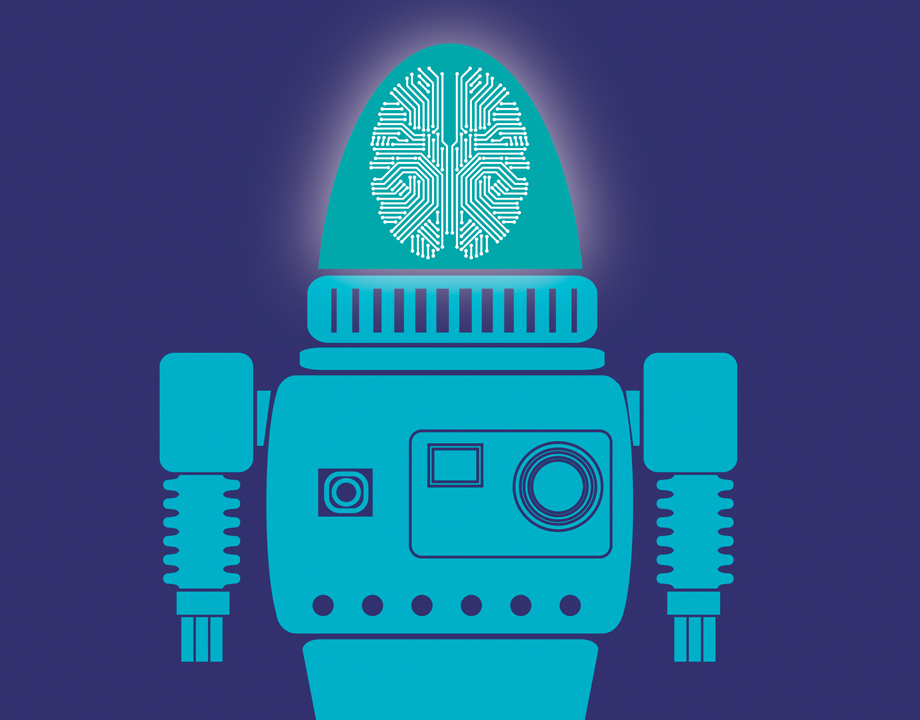