A Toolkit for Customizing Your Parts with Digital Manufacturing
A Toolkit for Customizing Your Parts with Digital Manufacturing
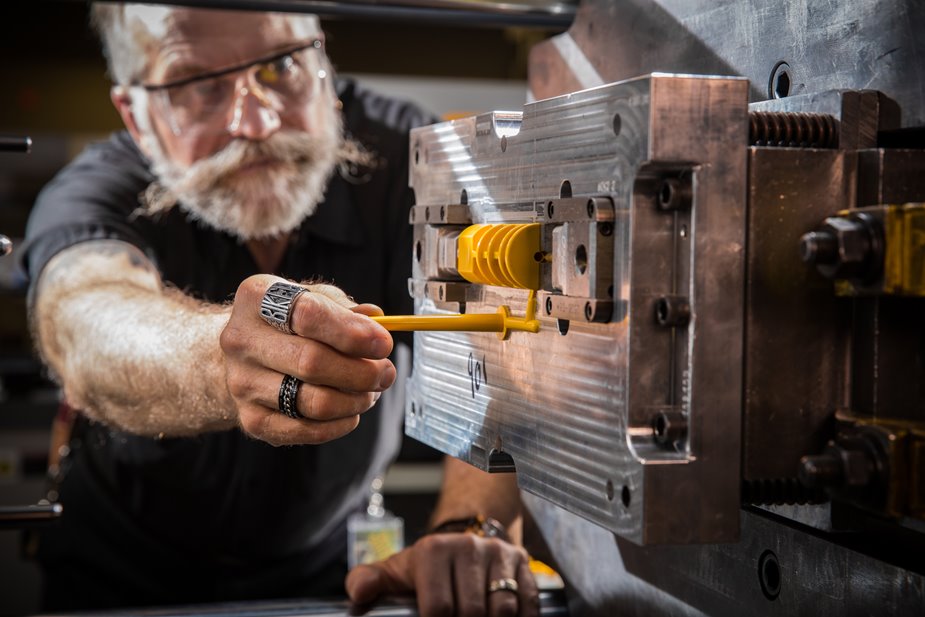
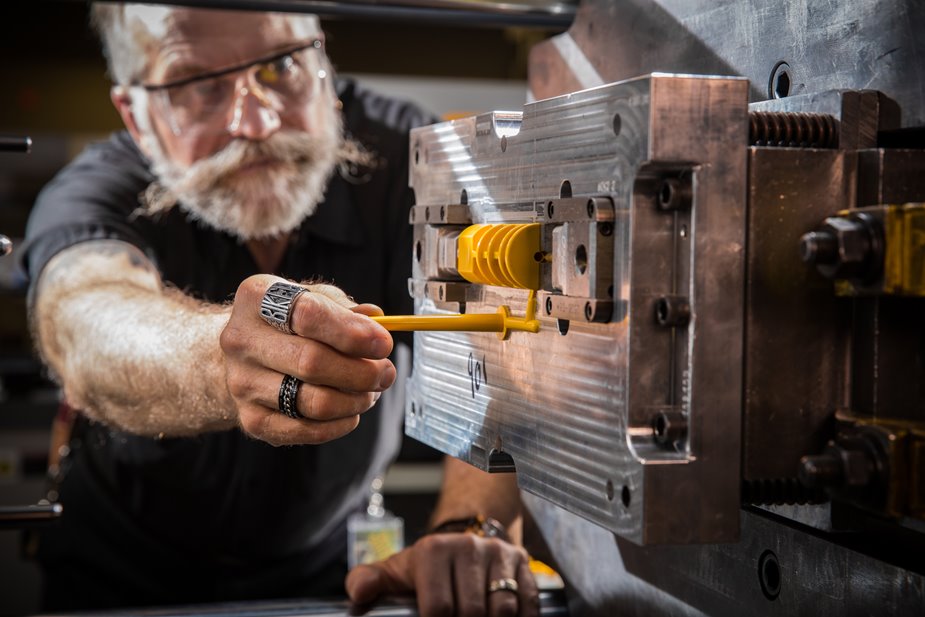
Digital manufacturers combine 3D printing, injection molding, and CNC machining for mass part customization and on-demand production. (Photo: Protolabs)
In today’s competitive marketplace, good design can help a product stand out from its competitors. A product made from off-the-shelf components is at a disadvantage. But customization is expensive. There are costs for design, development, tooling, testing—and on and on.
So, is customization worth it?
In a word, yes. While customization bears the up-front cost of design, modern digital design and manufacturing methods have reduced that premium. A custom design can reduce production costs—for example, by combining multiple parts into one. It can also eliminate potential points of failure and allow components to be designed for better spacing or a more compact layout. Connectors can be placed precisely where needed, eliminating steps in assembly. Customizable panels can reduce tooling costs and allow customer-specific solutions.
Customization also allows a choice of materials: plastic (molded or machined), sheet metal, or 3D-printing materials. With plastics, which are most commonly injection molded, it’s possible to incorporate inserts such as small metal features like connectors, mounts, crush limiters, or fine threads. These smaller features are not easily machined into a molded part. Injection molding also allows designers to do over-molding—the layering of one resin onto another—which makes it possible to combine what would otherwise be multiple parts into one, and to choose from a variety of finishing or post-processing options.
Recommended for You: Additive Manufacturing: From Prototypes to Manufacturing Transformation
Plastics are available to suit any need. There are common plastics like ABS, polycarbonate (PC), and ABS-PC blends. Where transparent plastics are needed for lenses and screens, there are PC, acrylic, polystyrene, or liquid silicone rubber (LSR). Where heat tolerance or heat conductivity is required, there are reinforced engineering-grade resins which use glass fiber or ceramic powders. There are electrically conductive materials for grounding or shielding. And for grips, buttons, or shock-protecting bumpers, there are pliable materials like elastomers, LSR, polypropylene, or polyethylene.
Let’s not forget aluminum. Rather than putting your new product in an uninteresting metal box, today’s digital manufacturing allows you to create your own design at a remarkably low cost, using either machined or formed sheet metal.
Prototyping is an essential part of product development. It helps to perfect design, make sure assembly goes smoothly, and allow experimentation with different materials. Iterative prototyping is the application of lessons from the initial prototype, and it is not uncommon for several generations of prototypes to be needed, as each unveils nuances not obvious before. After all, no one wants to go to production with a flawed—or too expensive, or difficult to manufacture—design. But iterative prototyping makes sense only if a way can be found to control costs.
While the first prototype may be done using 3D printing, later iterations will most likely be done using injection molding, for cost reasons and because it more closely resembles what will be used in production. By using a multi-cavity mold, it’s possible to produce several slightly differing prototypes in one shot. It’s also possible to experiment with different resins.
Read our Manufacturing Blog: Should You Design for Additive Manufacturing?
Product development must be both quick and thorough—particularly with electronic products, which typically require extensive testing. A digital manufacturer can help shorten and simplify every step of the development process.
A good digital manufacturer can create prototypes directly from CAD files and will automatically evaluate your design and highlight areas that are not manufacturable or that don’t comply with best practices. At the same time, it will produce a quote. A good digital manufacturer can also provide in-house application engineers to advise on design.
Editors' Pick: 7 Reasons Manufacturers Are Returning to the US
A digital manufacturer can provide parts quickly, using 3D printing, CNC machining, sheet metal fabrication, and injection molding—in some cases in as little as one day.
Once a design is finalized, a digital manufacturer can provide several different production options. To get to market quickly, and make sure that a part can actually be molded, there is quick-turn bridge tooling, which will sustain production while final production tools for ultra-high volume are being made. For low-volume production of end-use molded parts of thousands or even tens of thousands of parts, there is on-demand manufacturing. And for mass part customization, there is on-demand production. The ability to produce this mass customization is yet another benefit of partnering with a digital manufacturer, which provides manufacturing speed and low-volume production, enabling you to streamline your supply chain by procuring parts on-demand, without minimum order quantities (MOQs).
So, is customization worth it?
In a word, yes. While customization bears the up-front cost of design, modern digital design and manufacturing methods have reduced that premium. A custom design can reduce production costs—for example, by combining multiple parts into one. It can also eliminate potential points of failure and allow components to be designed for better spacing or a more compact layout. Connectors can be placed precisely where needed, eliminating steps in assembly. Customizable panels can reduce tooling costs and allow customer-specific solutions.
Customization also allows a choice of materials: plastic (molded or machined), sheet metal, or 3D-printing materials. With plastics, which are most commonly injection molded, it’s possible to incorporate inserts such as small metal features like connectors, mounts, crush limiters, or fine threads. These smaller features are not easily machined into a molded part. Injection molding also allows designers to do over-molding—the layering of one resin onto another—which makes it possible to combine what would otherwise be multiple parts into one, and to choose from a variety of finishing or post-processing options.
Recommended for You: Additive Manufacturing: From Prototypes to Manufacturing Transformation
Plastics are available to suit any need. There are common plastics like ABS, polycarbonate (PC), and ABS-PC blends. Where transparent plastics are needed for lenses and screens, there are PC, acrylic, polystyrene, or liquid silicone rubber (LSR). Where heat tolerance or heat conductivity is required, there are reinforced engineering-grade resins which use glass fiber or ceramic powders. There are electrically conductive materials for grounding or shielding. And for grips, buttons, or shock-protecting bumpers, there are pliable materials like elastomers, LSR, polypropylene, or polyethylene.
Let’s not forget aluminum. Rather than putting your new product in an uninteresting metal box, today’s digital manufacturing allows you to create your own design at a remarkably low cost, using either machined or formed sheet metal.
Prototyping Approaches During Development
Prototyping is an essential part of product development. It helps to perfect design, make sure assembly goes smoothly, and allow experimentation with different materials. Iterative prototyping is the application of lessons from the initial prototype, and it is not uncommon for several generations of prototypes to be needed, as each unveils nuances not obvious before. After all, no one wants to go to production with a flawed—or too expensive, or difficult to manufacture—design. But iterative prototyping makes sense only if a way can be found to control costs.
While the first prototype may be done using 3D printing, later iterations will most likely be done using injection molding, for cost reasons and because it more closely resembles what will be used in production. By using a multi-cavity mold, it’s possible to produce several slightly differing prototypes in one shot. It’s also possible to experiment with different resins.
Read our Manufacturing Blog: Should You Design for Additive Manufacturing?
Digital Manufacturers Help Transition to Rapidly to Market Rollout
Product development must be both quick and thorough—particularly with electronic products, which typically require extensive testing. A digital manufacturer can help shorten and simplify every step of the development process.
A good digital manufacturer can create prototypes directly from CAD files and will automatically evaluate your design and highlight areas that are not manufacturable or that don’t comply with best practices. At the same time, it will produce a quote. A good digital manufacturer can also provide in-house application engineers to advise on design.
Editors' Pick: 7 Reasons Manufacturers Are Returning to the US
A digital manufacturer can provide parts quickly, using 3D printing, CNC machining, sheet metal fabrication, and injection molding—in some cases in as little as one day.
Once a design is finalized, a digital manufacturer can provide several different production options. To get to market quickly, and make sure that a part can actually be molded, there is quick-turn bridge tooling, which will sustain production while final production tools for ultra-high volume are being made. For low-volume production of end-use molded parts of thousands or even tens of thousands of parts, there is on-demand manufacturing. And for mass part customization, there is on-demand production. The ability to produce this mass customization is yet another benefit of partnering with a digital manufacturer, which provides manufacturing speed and low-volume production, enabling you to streamline your supply chain by procuring parts on-demand, without minimum order quantities (MOQs).
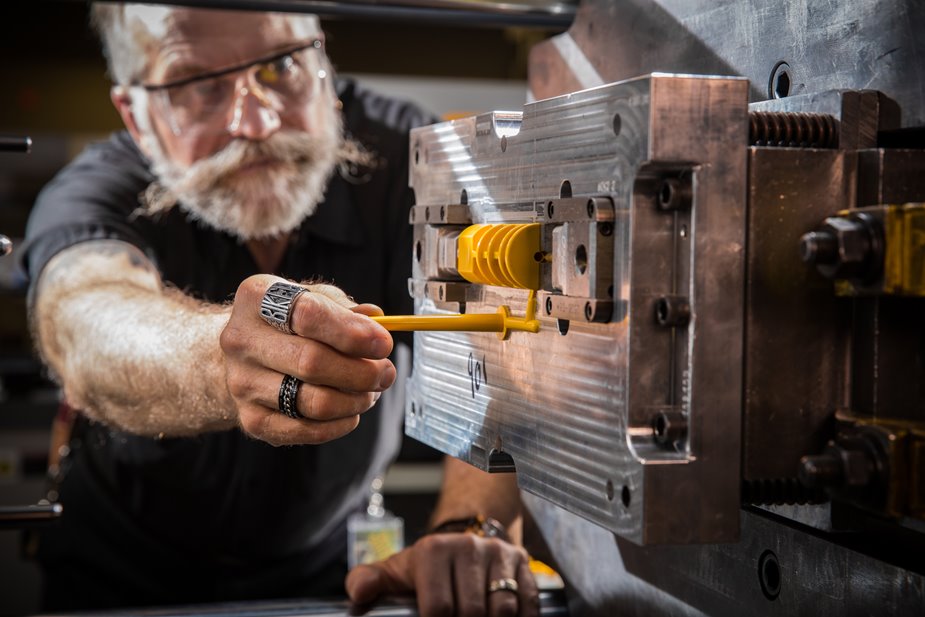
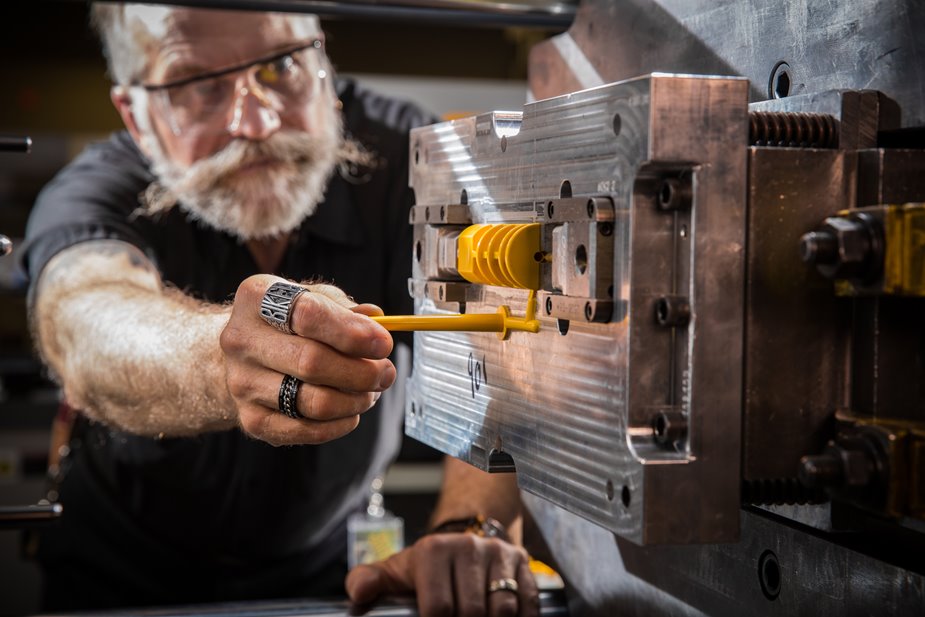