A Greener Way to Make Graphene
A Greener Way to Make Graphene
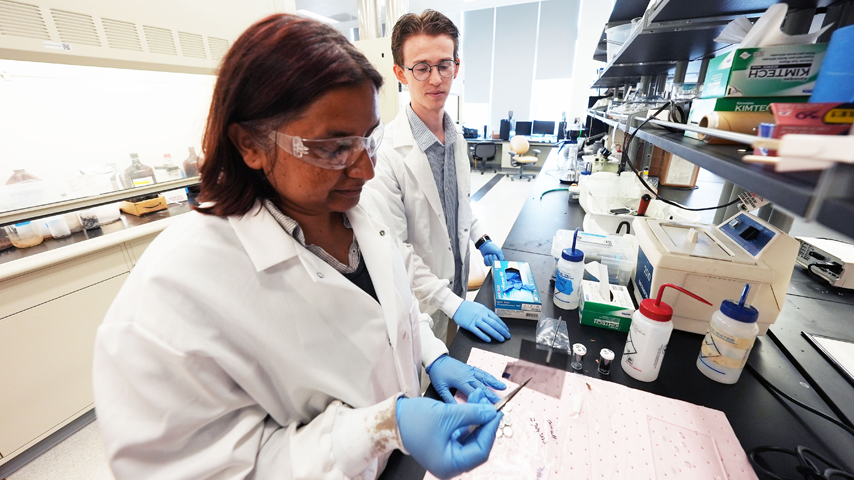
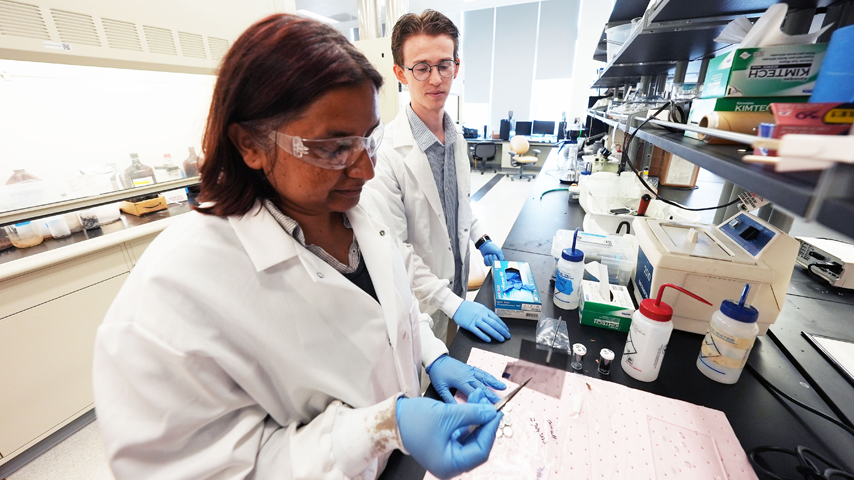
Researchers at Virginia Tech have developed a new method to derive a carbon-based “wonder material” from coal refuse.
In 2010, physicists Andre Geim and Konstantin Novoselov were awarded the Nobel Prize for their discovery six years earlier of a strong and versatile new material called graphene. This unique substance, which consists of a single layer of carbon atoms, has incredible thermal, mechanical, electrical, and chemical properties despite its thinness. With a strength more than 250 times that of steel, as well as remarkable thermal and electrical conductivity, many have hailed graphene as a “wonder material.” They have also sought to find ways to manufacture enough of it to support a wide range of new and existing applications across industry verticals.
“This material can be used in many different ways,” said Roop Majahan, the Lewis A. Hester Professor of Mechanical Engineering at Virginia Tech. “It is strong enough that you could use it to help make car bumpers stronger and make automobiles more resistant to collision damage. It could help make batteries charge faster—and increase their power. And it could be used in a number of different biomedical applications. It really is a remarkable material.”
More for You: Graphene-based Biosensor Offers Instant Diagnosis
The issue is how to make enough of it to help it to reach its full potential across these various industries and applications. The current method, known as the Hummers’ method, involves a number of powerful oxidizing agents to transform common graphite into graphene. Majahan said that not only is this approach costly, but the acids used to transform graphite to graphene are bad for the environment. In addition to those issues, graphite, an ingredient for pencil lead as well as many types of batteries, is generally sourced from China, which means that manufacturers interested in making graphene may have to deal with an unpredictable supply chain.
“To make graphene, what you need is a source that is rich in carbon,” explained Majahan. “So, we wanted to find a way to make graphene using an abundantly available carbon source and then do it in a way that was much friendlier to the environment. In doing so, we can lower the costs associated with graphene production and do it in a more sustainable manner too.”
The question was which carbon source might be the right one. Mahajan and colleagues had been investigating various applications for graphene for some time, looking for ways to integrate graphene into materials like aluminum and glass fiber-reinforced polymers, as well as pursuing a number of biomedical applications. Thanks to all that work, Mahajan became quite familiar with the material’s properties. And given his background working extensively with carbonaceous materials, he believed strongly that the Hummers’ method could not be the only way to make graphene. Other precursor materials should also work—provided one could come up with the right chemistry.
One day, while taking a long walk, he had the sudden thought that coal might work as a suitable precursory material to manufacture graphene on a bigger scale.
Become a Member: How to Join ASME
“There was no dramatic moment. I was just walking and thinking about graphene,” he said. “It occurred to me that coal and graphite both have a lot of carbon. Coal is an abundant source of carbon. And like with graphite, the carbon in coal transforms when it is put under high heat and pressure. So why couldn’t coal provide a way for us to make graphene too?”
When he shared his idea with one of his post-doctoral fellows, Suel-Yi Lee, who is trained as a chemist, the two decided to develop a new production method for “wonder material.” Within a few weeks, Lee put the right processes together to make it happen, Majahan said.
The new method involves taking coal, or even coal refuse, and grinding the material down to a fine powder. After that powder is purified, it is exposed to nitric acid to turn it into graphene oxide. After further processing, as well as chemical or thermal reduction, the researchers can easily produce multilayer graphene in a more cost-effective and environmentally friendly way. But, equally as important, the graphene they produce in this way performs better than that manufactured using the traditional method, Majahan added.
“We’ve explored several different applications and found that coal-derived graphene outperforms graphite-derived graphene, especially in regard to mechanical and thermal properties,” he said.
Given the increasing demand for graphene—Majahan said analysts predict it will grow into a $4.84-billion market by 2028—having this new method will provide researchers like himself, as well as other industries, wider opportunity to leverage graphene’s many fantastic properties.
“The good news is that we need a small fraction of this remarkable material to make composites to reap large benefits,” he said. “And coal is readily available. We don’t even need to mine coal to make graphene. Instead, we can utilize coal refuse already present in existing coal mines. There is also the potential for us to synthesize graphene from other precursors like agricultural waste and plastics. It’s just going to take time to fully develop and test these new processes.”
Kayt Sukel is a science and technology writer in Houston.
“This material can be used in many different ways,” said Roop Majahan, the Lewis A. Hester Professor of Mechanical Engineering at Virginia Tech. “It is strong enough that you could use it to help make car bumpers stronger and make automobiles more resistant to collision damage. It could help make batteries charge faster—and increase their power. And it could be used in a number of different biomedical applications. It really is a remarkable material.”
More for You: Graphene-based Biosensor Offers Instant Diagnosis
The issue is how to make enough of it to help it to reach its full potential across these various industries and applications. The current method, known as the Hummers’ method, involves a number of powerful oxidizing agents to transform common graphite into graphene. Majahan said that not only is this approach costly, but the acids used to transform graphite to graphene are bad for the environment. In addition to those issues, graphite, an ingredient for pencil lead as well as many types of batteries, is generally sourced from China, which means that manufacturers interested in making graphene may have to deal with an unpredictable supply chain.
“To make graphene, what you need is a source that is rich in carbon,” explained Majahan. “So, we wanted to find a way to make graphene using an abundantly available carbon source and then do it in a way that was much friendlier to the environment. In doing so, we can lower the costs associated with graphene production and do it in a more sustainable manner too.”
The question was which carbon source might be the right one. Mahajan and colleagues had been investigating various applications for graphene for some time, looking for ways to integrate graphene into materials like aluminum and glass fiber-reinforced polymers, as well as pursuing a number of biomedical applications. Thanks to all that work, Mahajan became quite familiar with the material’s properties. And given his background working extensively with carbonaceous materials, he believed strongly that the Hummers’ method could not be the only way to make graphene. Other precursor materials should also work—provided one could come up with the right chemistry.
One day, while taking a long walk, he had the sudden thought that coal might work as a suitable precursory material to manufacture graphene on a bigger scale.
Become a Member: How to Join ASME
“There was no dramatic moment. I was just walking and thinking about graphene,” he said. “It occurred to me that coal and graphite both have a lot of carbon. Coal is an abundant source of carbon. And like with graphite, the carbon in coal transforms when it is put under high heat and pressure. So why couldn’t coal provide a way for us to make graphene too?”
When he shared his idea with one of his post-doctoral fellows, Suel-Yi Lee, who is trained as a chemist, the two decided to develop a new production method for “wonder material.” Within a few weeks, Lee put the right processes together to make it happen, Majahan said.
The new method involves taking coal, or even coal refuse, and grinding the material down to a fine powder. After that powder is purified, it is exposed to nitric acid to turn it into graphene oxide. After further processing, as well as chemical or thermal reduction, the researchers can easily produce multilayer graphene in a more cost-effective and environmentally friendly way. But, equally as important, the graphene they produce in this way performs better than that manufactured using the traditional method, Majahan added.
“We’ve explored several different applications and found that coal-derived graphene outperforms graphite-derived graphene, especially in regard to mechanical and thermal properties,” he said.
Given the increasing demand for graphene—Majahan said analysts predict it will grow into a $4.84-billion market by 2028—having this new method will provide researchers like himself, as well as other industries, wider opportunity to leverage graphene’s many fantastic properties.
“The good news is that we need a small fraction of this remarkable material to make composites to reap large benefits,” he said. “And coal is readily available. We don’t even need to mine coal to make graphene. Instead, we can utilize coal refuse already present in existing coal mines. There is also the potential for us to synthesize graphene from other precursors like agricultural waste and plastics. It’s just going to take time to fully develop and test these new processes.”
Kayt Sukel is a science and technology writer in Houston.
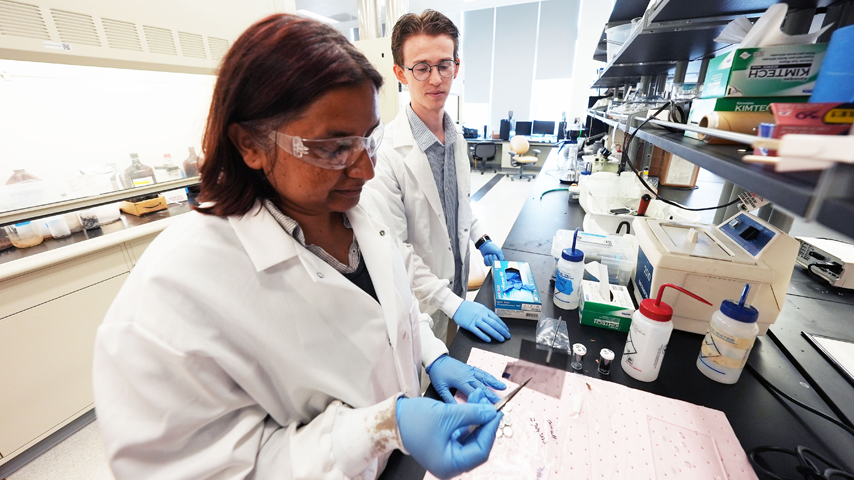
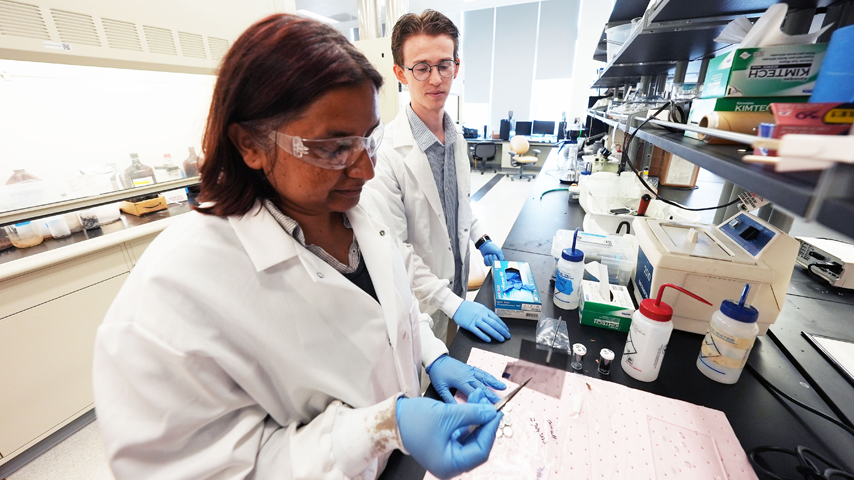