3-D Printing Vet Terry Wohlers Sees Endless Opportunities
3-D Printing Vet Terry Wohlers Sees Endless Opportunities
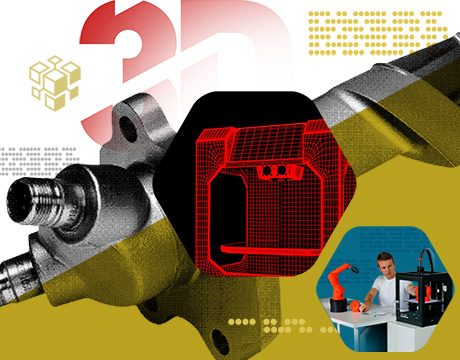
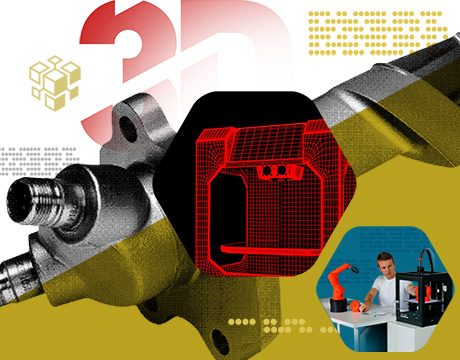
Terry Wohlers was there before additive manufacturing was an established industry. He began developing 3-D printed parts 30 years ago, when the technology was still untested. Wohlers, now president of Wohlers Associates, has written more than 420 books, articles, and technical papers, and delivered 150 keynote presentations on five continents. This year marks the 23rd anniversary of his Wohlers Report, which provides an in-depth analysis of the global additive manufacturing industry. Alan Brown, Mechanical Engineering magazine’s senior editor, recently caught up with Wohlers.
ME: You were one the world’s first AM consultants. What got you interested in additive manufacturing? T.W: I started Wohlers Associates as a CAD consultant in 1986 and quickly stumbled across 3-D printing. I contacted 3D Systems, and they sent me a full-scale distributor cap, back in the days when cars had those. I was just astounded, and I thought “Wow, if this is really possible, it could be as big as CAD and a perfect complement to solid modeling.”
ME: Then what happened? T.W: I started working with the world’s largest manufacturer of in-ear hearing aids to design and manufacture custom-fit devices. They sent me to events. I was like a sponge, soaking it all up and meeting people. One thing led to another, and eventually I was spending almost all my time in additive manufacturing.
For You: Additive Manufacturing Requires Different Approach
ME: That was 25 years ago. What’s the biggest change since then? T.W: Additive manufacturing is finally getting the respect it deserves. And with that comes investment. We’re seeing incredible amounts of money being spent on this technology, such as Stryker’s $400-million AM manufacturing facility.
ME: There is a lot of interest in metal AM. What’s going on there? T.W: Metal is smoking hot today. There are many new vendors. Where companies previously bought one, two, or three machines to qualify processes, they are now buying five, 10, or 20 machines to go into production.
ME: Are the economics changing? T.W: The prices are being driven down, and they need to be. You can afford to pay $250 per kilogram for materials to get prototypes right, because that’s where changes are least expensive in the design cycle. When you get into production, it’s a whole different animal. Your costs must be closer to conventional materials and processes. This issue is being addressed, but it will take time.
ME: Are engineers taking true advantage of AM’s flexibility? T.W: Engineers who used AM for prototyping didn’t really change their designs because they still had to produce them on conventional equipment. To use 3-D printing effectively and affordably, you need to design differently. For example, you can consolidate many parts into one, or optimize a part’s topology to increase its strength-to-weight ratio. These are new ways of thinking, and we’re just beginning to scratch the surface.
ME: To gain widespread acceptance, new technologies must turn people’s heads. Has 3-D printing done that? T.W: GE did it with the nozzle system for its LEAP engine. That was a real milestone, a critical part that cannot fail. Boeing, Airbus, and Stryker are also great examples. Companies can look at them and say, “Hey, we can do that, too.” But cost remains an issue. When volumes are low and part value is high, it is easier to build a business case around AM.
ME: Do you believe AM can transform industry? T.W: It has the ability to disrupt the supply chain almost entirely. When you consolidate 500 parts down to 10, you can imagine how that might impact your material suppliers, your part vendors, and the people that assemble and test your products. It introduces the possibility of doing more local manufacturing and really simplifying the supply base and making things much faster and more economically.
ME: What do you think will be making news in five years? T.W: I hope costs improve to the point where major automobile companies are adopting this technology in a big way for production.
Read More: Additive Manufacturing Transform Supply Chain Protecting a New World of 3D-Printed Products New 3D Printer Extruder Takes Manufacturing to Next Level
To use 3-D printing effectively and affordably, you need to design differently.Terry Wohlers
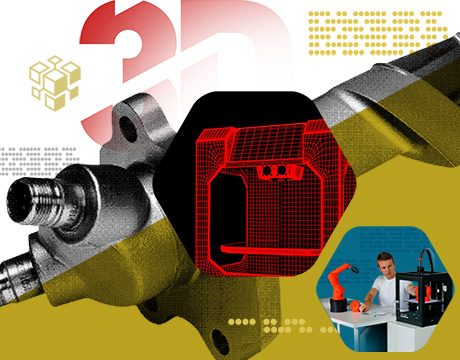
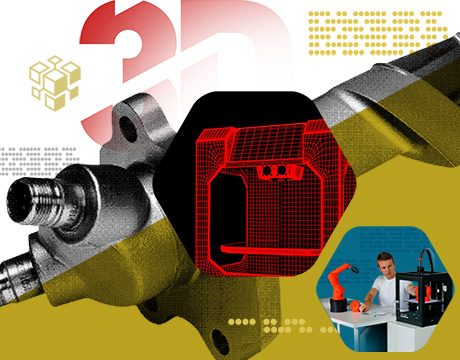