New 3D Printer Extruder Takes Manufacturing to Next Level
New 3D Printer Extruder Takes Manufacturing to Next Level
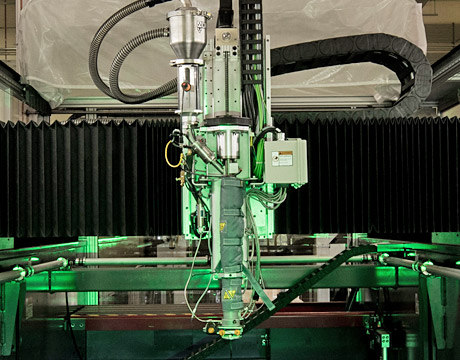
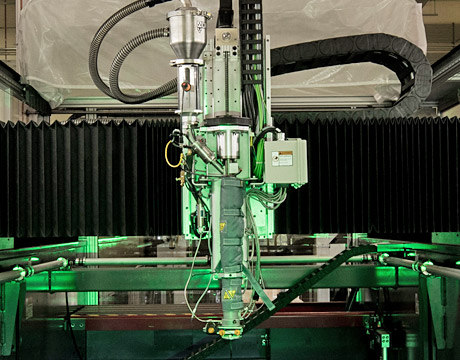
A large-area multi-material 3D printer. Image: ORNL
A new industrial 3D-printing extruder technology - designed to greatly increase the output and quality of high-resolution printed polymers and decrease postproduction time and costs – is set to take additive manufacturing of large parts, machine tools and molds to the next level.
The Department of Energy’s Oak Ridge National Laboratory (ORNL) developed the system as part of its evolving large-scale additive manufacturing initiative. It recently licensed the designs through an exclusive arrangement to Strangpresse, a Youngstown, Ohio-based manufacturer that sells its extruders and nozzles to 3D-printer manufacturers.
“This is an enabling technology that allows manufacturers to print high resolutions at high rates,” says Bill Peter, director of DOE's Manufacturing Demonstration Facility at ORNL.
The extruders are built for robotic and gantry 3D printers used in manufacturing parts with up to a 20-foot axis. They can be retrofit to most large AM printers.
“These designs help to advance additive manufacturing from a prototyping industry to an actual production industry,” says Chuck George, CEO of Strangpresse, a division of Hapco, a global manufacturing and design company. “It’s about getting these types of designs and technologies out of the lab and into the factory. These are the types of advancements that allow us to do that.”
Many industrial 3D printers can quickly pump out hundreds of pounds of printed material to produce fairly uniform products that require few variations or details, like surgical tubing or weather stripping. But it’s more time consuming and costly for those machines to print high-resolution components for such applications as machine tooling and dies used in the aerospace, automotive and other industries.
To achieve the different layer thicknesses and heights required for printing fine geometric resolution, operators of large 3D printers have to slow or stop the machines to manually change nozzles and switch feedstocks. That diminishes the quality and increases the roughness of the printed components, which have to be fine-tuned in postproduction, adding costs to the project.
ORNL’s new extruder technology changes that by enabling the printers to automatically alternate among multiple nozzles of various diameters on the fly. “Having the ability to do that while moving allows for a much more efficient processing of material,” George says.
The nozzles - attached to a turntable that resembles the revolving base of a microscope that holds different lenses - quickly and accurately deposit a variety of material thicknesses and heights to achieve the desired resolution. “The breakthroughs are in how we can now process polymers with a wide range of variables,” George says. “That’s been accomplished by various things like extruder control.”
ORNL also redesigned the bell-shaped cavity of the nozzle to improve the flow of material and added a new poppet-like valve that quickly shuts off the flow of material to each nozzle. The team also developed new slicing software to control the resolution of the material while it’s being printed on the fly.
“It gives us the ability to do so much more,” Peter says about the redesigned system.
The new extruder increases high-resolution deposition rates of polymers by three orders of magnitude compared with earlier wire feedstock printers, going from about four cubic inches (the size of a chicken egg) per hour to 2,400 cubic inches (about two-thirds the size of a beer keg) per hour.
The improvements translate to up to 100 pounds of high resolution material per hour, depending on the diameter of the extruder’s nozzle screw and the size and density of the polymer pellets.
For another comparison, take one of ORNL’s last high-profile projects. In 2015 the lab partnered with Cincinnati Inc. to use their collaboratively developed Big Area Additive Manufacturing (BAAM) machine to print parts for a Shelby Cobra. That machine produced about 10 pounds of high-resolution material per hour. Peter expects ORNL’s extruders to print 1,000 pounds of high-resolution material per hour within a year.
ORNL also recently printed a proof-of-concept 30-foot submersible hull for one of the Navy’s prototype vessels. Using traditional manufacturing, the hull would have cost $600,000 to $800,000 and taken three to five months to build. The new additive manufacturing capabilities reduced costs by 90 percent and build time to just a few days.
“We’ve come up significantly in our rates since the Shelby and the original BAAM system,” Peter says. “This [new extruder] is about using the output more effectively. This represents a steady progression in extruder technology.”
That’s something Strangpresse’s George likes to hear.
He sees the ability to quickly, cheaply and efficiently print dies and molds as the low hanging fruit of large additive manufacturing. But as the industry continues to advance its work with high-strength, lightweight polymers and higher-resolution designs, it will expand beyond those parts, incorporating such new elements as cooling and wiring channels into 3D-printed parts. Easily printing inexpensive prototypes or molds for a limited amount of products can also lower a company’s costs, drive profits and improve its competitive edge, George says.
“We can now print highly customizable and unique things that weren’t possible,” he says. “The bottom line is printing usable parts and structures instead of just a mold, a die, or a jig.”
This is an enabling technology that allows manufacturers to print high resolutions at high rates.Bill Peter, ORNL.
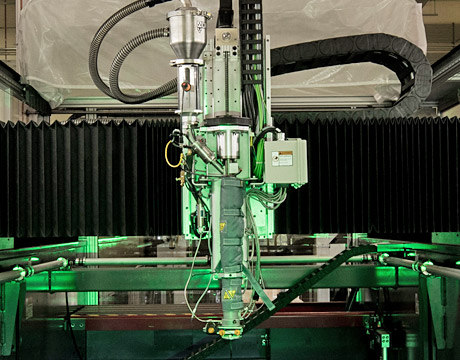
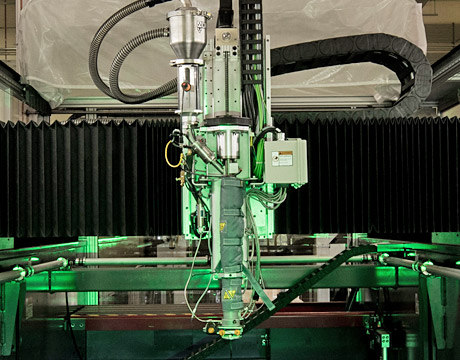