Lengthening the Life of Lithium-Ion Batteries
Lengthening the Life of Lithium-Ion Batteries
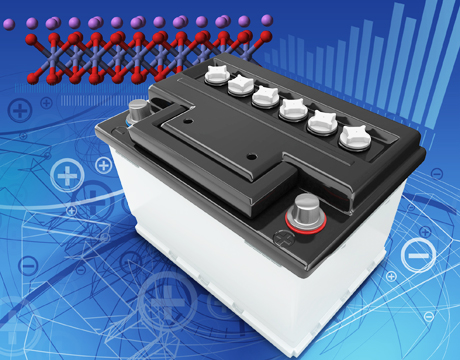
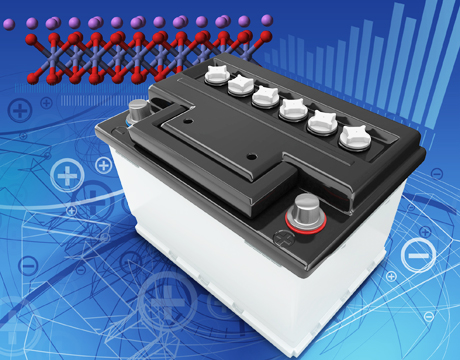
An unprecedented increase in lithium-ion battery research has occurred in recent years, with the goals of improving performance, durability, and safety—especially for electric-drive vehicles. To achieve these goals, afundamental understanding of the underlying degradation mechanisms that limit battery life is of critical importance. Research opportunities for mechanical engineers are plentiful and include material-structure relationships, thermal-electrochemical issues, and thermal management strategies.
“The lithium-ion battery is a dynamic system with multiple physicochemical interactions that occur at multiple scales,” says Partha P. Mukherjee, assistant professor of mechanical engineering at Texas A&M University. “How can we optimize these fundamental interactions? What are the influences of electrochemistry and transport? How can we manipulate the interaction of nanomaterials and nanostructures at the mesoscale to improve performance?”
Mechanical Degradation
One way to improve lithium-ion battery performance is by reducing or eliminating the degradation that occurs within the electrodes.
“Diffusion-induced stress and fracture formation in the active particles is a critical degradation issue in lithium-ion battery electrodes,” says Mukherjee. “We are trying to understand why these fractures form and the best ways to minimize this mechanical degradation.”
Lithium-ion batteries work on the principle of lithium ions inserting and de-inserting into the host material lattice—a process known as intercalation. This intercalation of lithium ions into the material lattice structure causes volume expansion, which is known as diffusion-induced stress (DIS). For example, graphite, an anode material, shows 5-10% volume expansion, whereas high-capacity anode materials such as tin and silicon exhibit 200-350% volume expansion. This diffusion-induced stress and volume expansion during lithium insertion, and the contraction during de-insertion, result in microfracture development. For high-volume expansion materials, this may lead to particle isolation and pulverization, reducing electrode life and overall performance.
“Fracture due to DIS of electrode active particles is one of the critical factors for capacity fade and impedance rise in lithium-ion batteries,” says Mukherjee. “The inherent stochastics underlying crack formation and propagation in brittle intercalation materials is critical toward understanding the degradation phenomena that limit battery life and performance.”
Controlling Fracture Development
When the DIS stress exceeds the fracture threshold in existing structural flaws or cracks in the active particles, microfractures may develop in the particles. Orientation of the initial pre-existing flaw or crack can also impact how it will propagate over time. Fractures interfere with lithium transport and reduce performance. The fresh surfaces that result from these fractures can also induce the formation of solid electrolyte interphase layers, removing lithium from the transport mechanism and further reducing performance.
Research to identify the impact of microscopic imperfections on the lithium-ion transport is still in its early stages.
“A key question to be answered is how to minimize the formation of cracks in electrode particles during operational conditions, without diminishing performance,” says Mukherjee.
To better understand this issue, Mukherjee and his research team developed a stochastic methodology for characterizing the diffusion-induced damage inside typical intercalation particles. The methodology is based on a random lattice spring model, coupled with solid-state diffusion of lithium in active particles and performance prediction analysis. A fracture phase-map was developed that shows the safe/unsafe operating regimes according to particle size and C-rate (charge/discharge rate).
“Higher C-rates can lead to a greater amount of micro-crack formation, which is also linked to the active particle size,” says Mukherjee. “For example, larger particles (10 micron radius) experience significant mechanical degradation at high C-rates, whereas smaller particles (0.5-1 micron) may exhibit only slight structural damage. Due to strain energy release, most of the damage occurs within the first two or three delithiation-lithiation cycles; during subsequent cycles, damage propagation may not be significant.”
Future Work
Because the majority of the mechanical degradation occurs during the first few cycles, there is potential for optimizing the influence of active particle morphology, size, mechano-electrochemical properties, and interactions with other components (such as binder, conductive additives) in the electrode microstructures. Smaller particles experience less stress during lithiation and delithiation. The presence of pre-existing cracks in particles also results in strain energy release, which enhances mechanical and electrochemical stability. Based on this observation, it may be feasible to utilize specially designed imperfections in electrode materials to limit the growth of microfracturing.
“Understanding the underlying stochastics and mechano-electrochemical interactions related to diffusion-induced stress is an important step toward reducing mechanical degradation in lithium-ion battery electrodes,” says Mukherjee. “This has the potential to improve the performance and cycle life of lithium-ion batteries and broaden the scope of future electroactive materials design.”
Mark Crawford is an independent writer.
A key question to be answered is how to minimize the formation of cracks in electrode particles during operational conditions, without diminishing performance.Partha P. Mukherjee, Texas A&M University
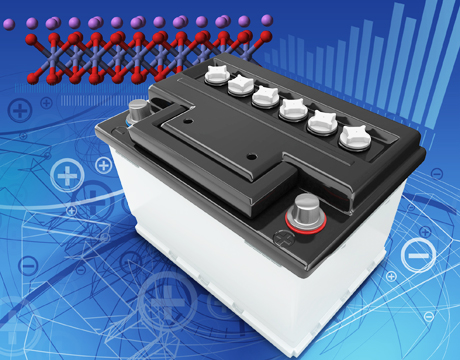
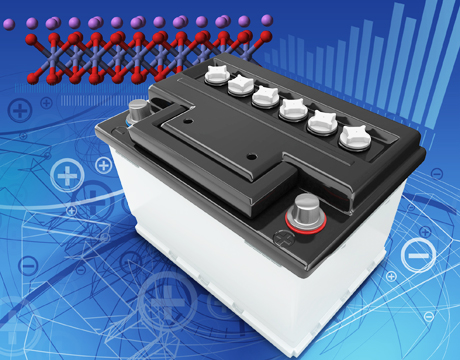