Printing Houses
Printing Houses
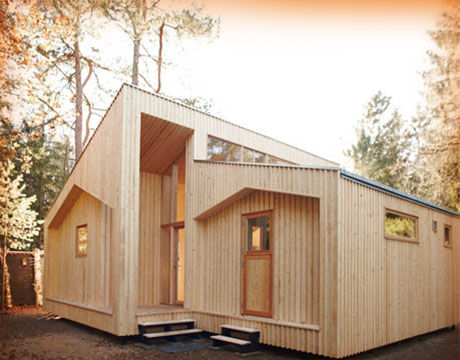
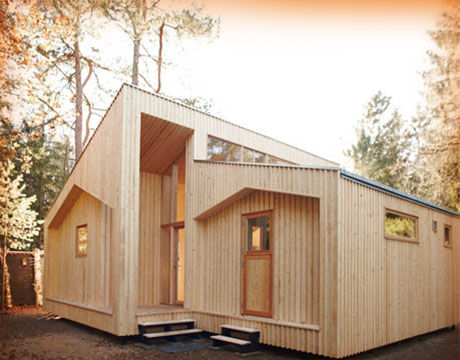
The printable house is created from a 3-D design morphed into a 2-D print and assembled by hand. Image: Urik Jantzen and Das Büro for UPM
Open the flat box from Ikea, find the wordless instructions and the complimentary Allen wrench, and, unless you're one of those instruction-following-impaired laymen, your shelves, or crib, or whatever, will be up in no time.
Now, thanks to two ingenious Danish architects, a CNC milling machine, and some clever software, you can build your own house the same way.
"The goal is that two people should be able to build the house," says Frederik Agdrup, who, with Nicholas Bjørnda, makes up the team that is Eentileen. "There is nothing that is so heavy that two people could not lift it. You do need a ladder, you don't need cranes or heavy equipment." Working with Facit Homes out of London, Agdrup and Bjørnda have managed to design and build the first printable house. "Printable" that is, if using a three-axis CNC milling machine to cut plywood into the necessary shapes can be called printing.
The system is not in any way limited to blocky, simplistic, or obviously modular designs, as a look at Villa Asserbo, their latest construction, makes clear. Agdrup says he can draw up "all our wishes and desires" in the CAD program Revit, then send off the design to Facit. They run it through their software, which turns the 3-D into 2-D (they call it the "D-process"). The resulting pages are sent back to Eentileen and they print them out, on plywood, with their recently purchased 500,000 krone CNC machine.
Designing to Building
The pair of architects put the Villa Asserbo home together themselves. "We have backgrounds as architects, but we've always wanted to have our own hands on the building, not just design it on the computer, send it off to the builders, and lose control of the project," Agdrup says. Together, they assembled the 420 pieces of plywood by hand.
Each piece is one of four modular types: wall, floor, roof, and header (which connects wall to roof). Extra elements, such as windows or a cut-out for an electric box, are easily added. "If we need to curve the piece even more than usually possible, we can carve slices into it so it can bend," says Agdrup. Once printed, the pieces come with Ikea-like step-by-step instructions and numbers for easy assembly. The result costs no more than a traditional home, and if such homes catch on, the price is likely to come down much more.
Sustainable Construction
In addition to its ease of assembly, potential affordability, and sleek design, the home is also "the most sustainable house on the market," says Agdrup. The insulation is wood fiber. The plywood is all spruce form the Nordic Forrest. The material is printed as efficiently as possible to minimize waste. A three-layered window generates heat when the sun is out. Instead of resting on concrete, as most Danish homes do, Villa Asserbo sits atop screwpiles. The home can be assembled in the most remote location with minimal impact.
Water, however, will come in and out of the home in the traditional fashion. "We could easily take that to the next level by using recycled water," notes Agdrup. Future iterations might have solar cells.
So where are all the printed houses? The hurdles are threefold, at least in Denmark. "The building regulations are very concerned about damp inside the construction," says Agdrup. "It's a challenge." And the conservative construction market wants to "do things as they've always done them." And then there's the economy.
None of these impediments seem insurmountable. Before long you may be leafing through an architect's catalog to pick a home. And the plywood villas will be printed out and popped up everywhere.
Michael Abrams is an independent writer.
We've always wanted to have our own hands on the building, not just design it on the computer, send it off to the builders, and lose control of the project.Frederik Agdrup, architect
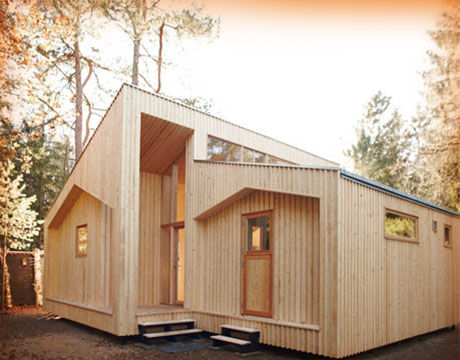
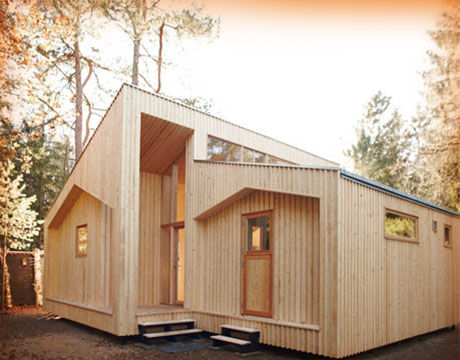