Nanoscale-Fortified Wood Could Pave Way for Eco-Friendly Construction
Nanoscale-Fortified Wood Could Pave Way for Eco-Friendly Construction
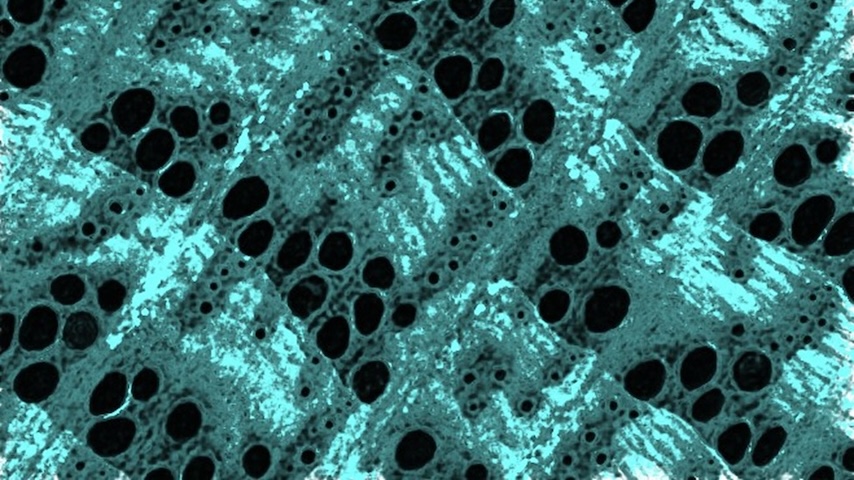
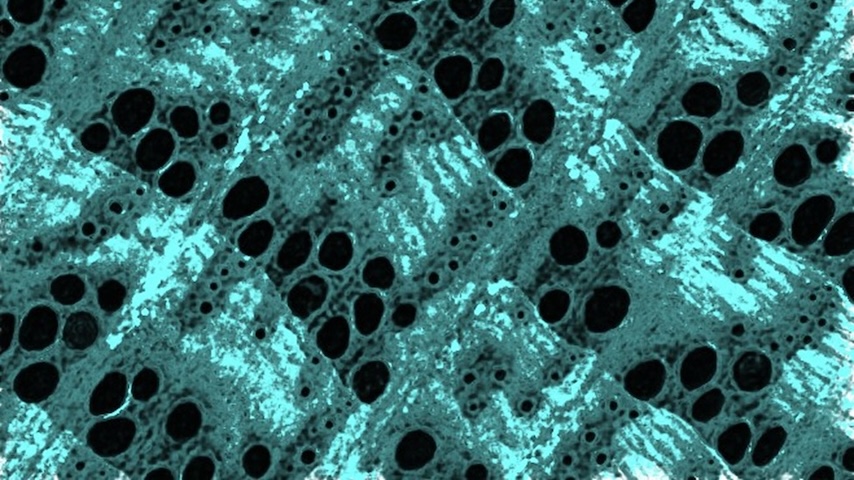
By enhancing wood with the right chemical treatments, the resulting bio-based material could one day replace traditional construction materials like steel and concrete.
Imagine a fortified wood that is strong and inexpensive that it could be used for large-scale projects, reducing the need for steel and other costly components. This isn't a futuristic fantasy, but a groundbreaking reality being forged by researchers at Florida Atlantic University. Their approach to infusing wood with inorganic materials holds the potential to transform the construction and manufacturing industries by offering a sustainable, high-performance alternative to traditional structural materials.
At the forefront of this pioneering research is Vivian Merk, senior author and assistant professor with a dual appointment in the Departments of Ocean and Mechanical Engineering and Chemistry. Their work goes beyond simply filling the macroscopic pores within wood—the true innovation lies in reinforcing the intricate cellular structure itself, Merk explained.
“Wood has fairly hollow cells,” she continued. “But it’s much more difficult to reinforce the cell wall. The idea was always, if we managed to incorporate some inorganic or any hard materials into the cell wall, we might achieve some sort of reinforcement. Our goal was not only to reinforce the wood, but to ensure the process and the material would be environmentally benign.”
This focus on internal cellular fortification is what sets their method apart, as it fundamentally alters the wood's inherent mechanical properties from the inside out. The specific material the team investigated, and successfully integrated, is known as amorphous iron oxide, or ferrihydrite—a compound resulting from the reaction between ferric nitrate and potassium hydroxide. This choice was deliberate, as ferrihydrite is naturally occurring in soils, aligning with the project’s goal of environmental compatibility.
More for You: Strength from the Deep Sea
To infuse this material into the wood, in this case red oak, the process involves a series of carefully orchestrated steps designed for efficiency and effectiveness. First, the wood undergoes a vacuum impregnation with an iron salt solution, specifically iron nitrate. This vacuum step is crucial for removing air from the wood's porous structure, allowing the solution to fully penetrate and saturate the material. During a second subsequent treatment, the wood is impregnated with an alkaline solution, again utilizing a vacuum to ensure comprehensive distribution. Lastly, the treated wood is simply washed with water.
The critical distinction between this staged, two-solution process and a simpler, single-step treatment is that the minerals are formed inside the wood structure, rather than being pre-mixed and forced in. This in-situ crystallization allows the ferrihydrite nanoparticles to grow within the nanoscale confines of the wood cell walls, leading to a much more effective bond.
Unlike other wood treatment methods, such as those aimed at increasing hydrophobicity (water resistance), which often inadvertently weaken mechanical properties, this new method consistently improves them. Furthermore, it simplifies what has historically been a complicated and often cost-prohibitive process in material science. This streamlined approach, combined with the use of readily available and environmentally benign chemicals, makes the new method and material highly attractive for real-world industrial applications and ensures cost-effectiveness.
“Some modifications are too complicated,” Merk said. “They might work quite well, but then you need a lot of different expensive chemicals and solvents, making it not commercially viable. We’re keeping it fairly simple to make it also industrially relevant.”
To rigorously test the mechanical enhancements of the fortified wood, the team employed a specialized technique known as atomic force microscopy (AFM). Unlike traditional optical microscopes, which are limited by the wavelength of light and cannot resolve features at the nanoscale, AFM operates by physically “feeling” the surface with an ultra-sharp probe. Imagine a record player’s needle, but on an incredibly precise, atomic scale, capable of discerning features down to fractions of a nanometer.
Discover the Benefits of ASME Membership
The core principle involves a minuscule, sharp tip mounted on a flexible cantilever—a tiny, delicate beam. As this tip is systematically scanned across the sample surface, attractive and repulsive forces between the tip and the sample cause the cantilever to deflect, or bend, by infinitesimal amounts. A laser beam reflected off the cantilever onto a position-sensitive photodetector precisely measures these deflections. This allows the AFM to construct a highly detailed topographical map of the surface.
Merk's team utilized a specific type of AFM that allows for simultaneous topographical and mechanical mapping. In this mode, the cantilever vibrates at a precise, controlled frequency. As it interacts with the sample, changes in its oscillation are detected. By meticulously analyzing these changes, particularly the amplitude and phase of the cantilever's vibration, and applying established contact mechanics models, researchers can derive critical mechanical properties, such as the elastic modulus, at each individual data point. This capability generates high-resolution maps of mechanical properties across the sample surface.
“Especially at the nano and microscale, we saw that we actually managed to achieve a reinforcement,” Merk explained. This nanoscale precision is crucial for understanding materials like wood, which possess a complex hierarchical structure from the molecular level up to the macroscopic. By generating thousands of data points across a sample, AFM provides unparalleled insight into the distribution and efficacy of the fortification. “We could actually distinguish between the different cell wall layers,” she added.
During initial testing of the fortified wood using this sophisticated AFM method, the team found that the reinforcement of the cell wall was improved by a factor of three. This significant increase in strength was achieved with very little added weight. This low-density, high-strength outcome is particularly attractive, as it maintains wood's inherent advantage over denser materials like steel when strength-to-weight ratio is considered.
The next step for Merk and her team is to create a clear path toward commercializing this innovative material and method. Their focus is now on finding industry partners who can help scale up the laboratory-based techniques to industrial production.
Cassandra Kelly is a technology writer in Columbus, Ohio.
At the forefront of this pioneering research is Vivian Merk, senior author and assistant professor with a dual appointment in the Departments of Ocean and Mechanical Engineering and Chemistry. Their work goes beyond simply filling the macroscopic pores within wood—the true innovation lies in reinforcing the intricate cellular structure itself, Merk explained.
“Wood has fairly hollow cells,” she continued. “But it’s much more difficult to reinforce the cell wall. The idea was always, if we managed to incorporate some inorganic or any hard materials into the cell wall, we might achieve some sort of reinforcement. Our goal was not only to reinforce the wood, but to ensure the process and the material would be environmentally benign.”
This focus on internal cellular fortification is what sets their method apart, as it fundamentally alters the wood's inherent mechanical properties from the inside out. The specific material the team investigated, and successfully integrated, is known as amorphous iron oxide, or ferrihydrite—a compound resulting from the reaction between ferric nitrate and potassium hydroxide. This choice was deliberate, as ferrihydrite is naturally occurring in soils, aligning with the project’s goal of environmental compatibility.
More for You: Strength from the Deep Sea
To infuse this material into the wood, in this case red oak, the process involves a series of carefully orchestrated steps designed for efficiency and effectiveness. First, the wood undergoes a vacuum impregnation with an iron salt solution, specifically iron nitrate. This vacuum step is crucial for removing air from the wood's porous structure, allowing the solution to fully penetrate and saturate the material. During a second subsequent treatment, the wood is impregnated with an alkaline solution, again utilizing a vacuum to ensure comprehensive distribution. Lastly, the treated wood is simply washed with water.
The critical distinction between this staged, two-solution process and a simpler, single-step treatment is that the minerals are formed inside the wood structure, rather than being pre-mixed and forced in. This in-situ crystallization allows the ferrihydrite nanoparticles to grow within the nanoscale confines of the wood cell walls, leading to a much more effective bond.
Unlike other wood treatment methods, such as those aimed at increasing hydrophobicity (water resistance), which often inadvertently weaken mechanical properties, this new method consistently improves them. Furthermore, it simplifies what has historically been a complicated and often cost-prohibitive process in material science. This streamlined approach, combined with the use of readily available and environmentally benign chemicals, makes the new method and material highly attractive for real-world industrial applications and ensures cost-effectiveness.
“Some modifications are too complicated,” Merk said. “They might work quite well, but then you need a lot of different expensive chemicals and solvents, making it not commercially viable. We’re keeping it fairly simple to make it also industrially relevant.”
To rigorously test the mechanical enhancements of the fortified wood, the team employed a specialized technique known as atomic force microscopy (AFM). Unlike traditional optical microscopes, which are limited by the wavelength of light and cannot resolve features at the nanoscale, AFM operates by physically “feeling” the surface with an ultra-sharp probe. Imagine a record player’s needle, but on an incredibly precise, atomic scale, capable of discerning features down to fractions of a nanometer.
Discover the Benefits of ASME Membership
The core principle involves a minuscule, sharp tip mounted on a flexible cantilever—a tiny, delicate beam. As this tip is systematically scanned across the sample surface, attractive and repulsive forces between the tip and the sample cause the cantilever to deflect, or bend, by infinitesimal amounts. A laser beam reflected off the cantilever onto a position-sensitive photodetector precisely measures these deflections. This allows the AFM to construct a highly detailed topographical map of the surface.
Merk's team utilized a specific type of AFM that allows for simultaneous topographical and mechanical mapping. In this mode, the cantilever vibrates at a precise, controlled frequency. As it interacts with the sample, changes in its oscillation are detected. By meticulously analyzing these changes, particularly the amplitude and phase of the cantilever's vibration, and applying established contact mechanics models, researchers can derive critical mechanical properties, such as the elastic modulus, at each individual data point. This capability generates high-resolution maps of mechanical properties across the sample surface.
“Especially at the nano and microscale, we saw that we actually managed to achieve a reinforcement,” Merk explained. This nanoscale precision is crucial for understanding materials like wood, which possess a complex hierarchical structure from the molecular level up to the macroscopic. By generating thousands of data points across a sample, AFM provides unparalleled insight into the distribution and efficacy of the fortification. “We could actually distinguish between the different cell wall layers,” she added.
During initial testing of the fortified wood using this sophisticated AFM method, the team found that the reinforcement of the cell wall was improved by a factor of three. This significant increase in strength was achieved with very little added weight. This low-density, high-strength outcome is particularly attractive, as it maintains wood's inherent advantage over denser materials like steel when strength-to-weight ratio is considered.
The next step for Merk and her team is to create a clear path toward commercializing this innovative material and method. Their focus is now on finding industry partners who can help scale up the laboratory-based techniques to industrial production.
Cassandra Kelly is a technology writer in Columbus, Ohio.
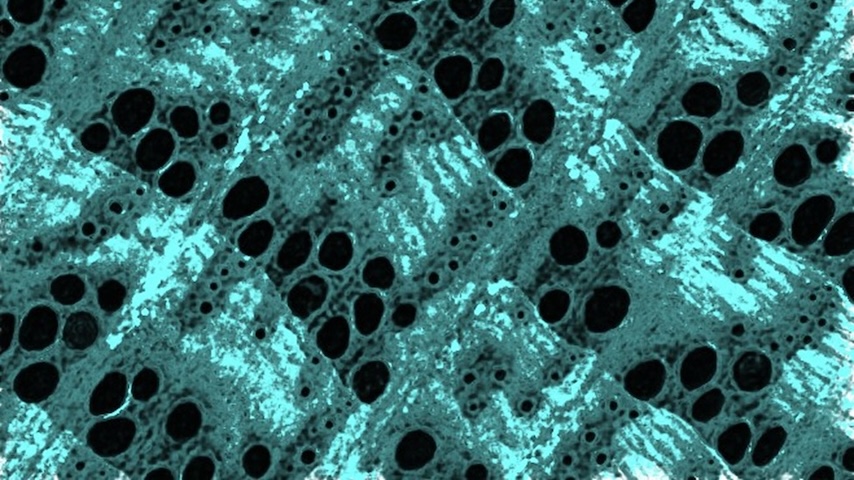
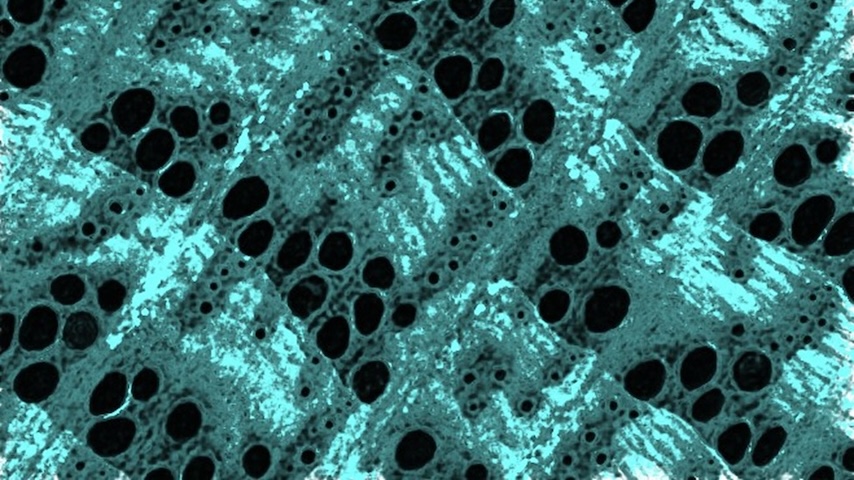