Mixing Plastic into Asphalt Yields Superior Results
Mixing Plastic into Asphalt Yields Superior Results
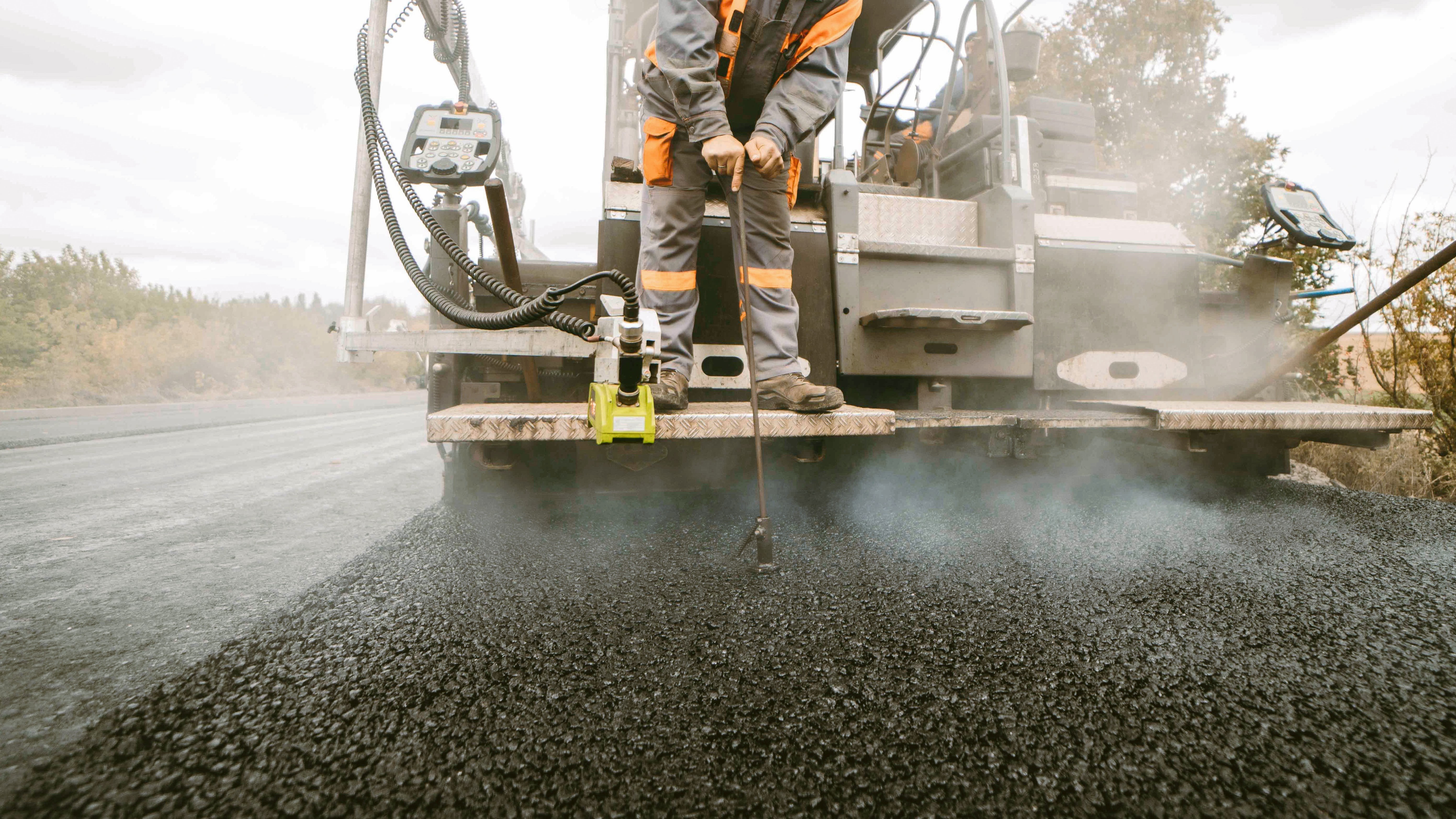
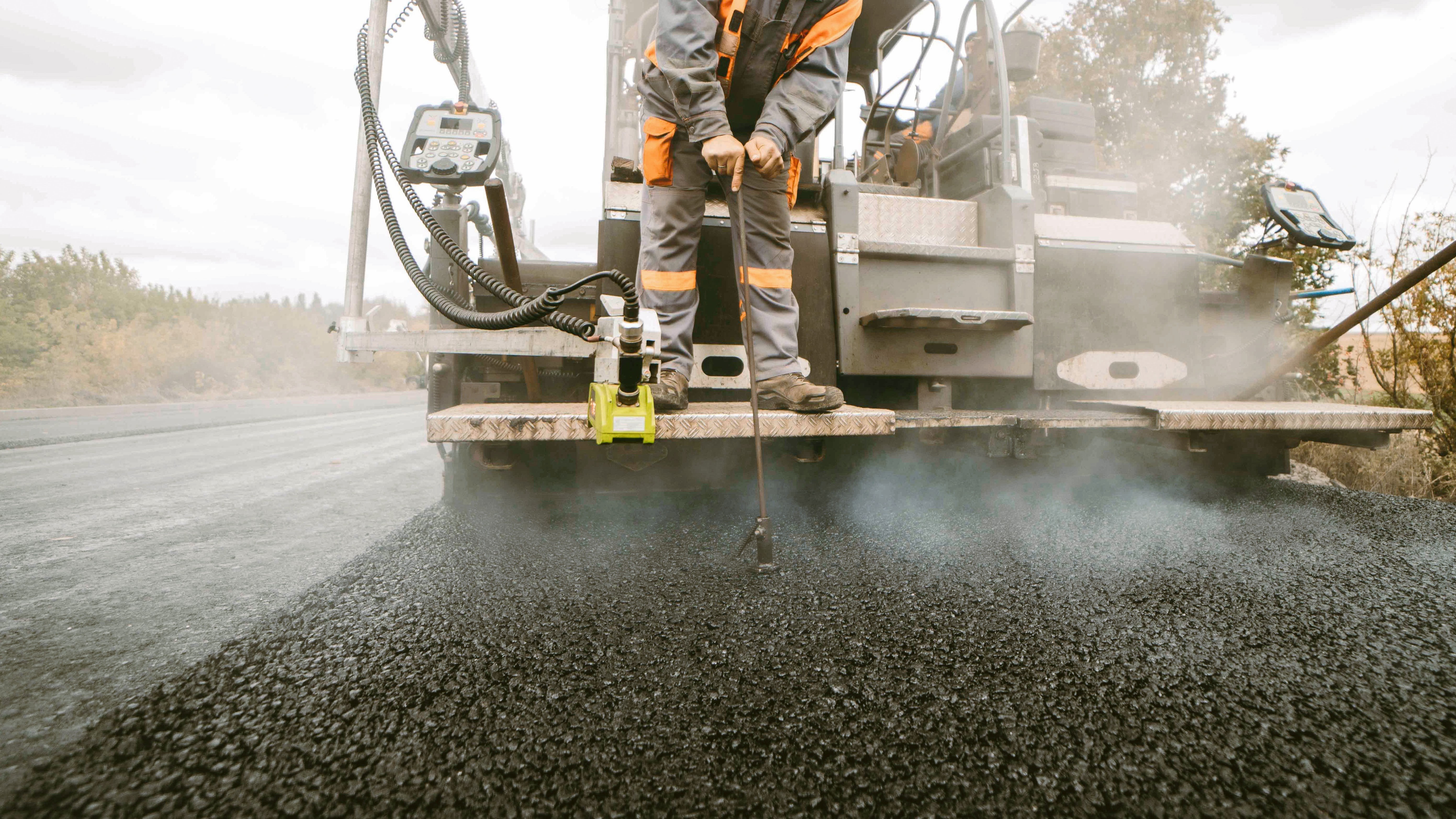
Bitumen is expensive and recycled plastic is cheap. A team at the University of Missouri is studying the performance of asphalt enhanced with polyethylene.
Thousands of square miles of North America are paved over with what’s commonly called “blacktop”—asphalt that covers roads, runways, and parking lots. Asphalt producers combine aggregate, crushed stone, gravel, and sand, with a binder, typically a bitumen product. While crushed stone and gravel dominate the mix by volume (typically asphalt is as much as 95 percent aggregate), bitumen dominates the cost.
Finding a way to supplement bitumen, a black, tarry constituent of petroleum, would make asphalt cheaper and could improve its performance.
Researchers at the University of Missouri are developing a post-consumer plastic asphalt. In recent trials, they replaced up to 40 percent of the bitumen with polyethylene, referred to as a modifier, to reduce expensive binder volume, improve asphalt performance, and advance sustainability. Their work showed that recycled materials could meet engineering demands and reduce environmental impact.
Now, they are looking to extend their work to much more demanding airport runways.
The asphalt modification used two main methods. The so-called wet process blends modifiers with the binder before combining it with aggregates, often resulting in a more uniform binder.
In their work, the University of Missouri team prioritized the dry process, where they added modifiers directly to the aggregate during mixing. This approach simplified production but risked creating a nonuniform binder.
“The dry process lets contractors modify asphalt on demand,” explained Bill Buttlar, the Glen Barton Chair in Flexible Pavement Technology in the Department of Civil and Environmental Engineering at the University of Missouri in Columbia. “They injected granulated or powdered plastic into the mixing drum with aggregate and binder, avoiding days-ahead orders and higher costs tied to supplier-prepared wet-modified binder.”
“Given the significant cost gap between binder, at least $600-700 per ton, and aggregate, around $20 per ton, even a partial 20 percent replacement of the binder with lower cost recycled materials delivered major economic benefits, especially in high-priced modified asphalt mixtures,” Buttlar said.
Looking for a substance that was readily available, relatively low-cost, but with superior performance attributes, the Missouri team focused on polyethylene.
Polyethylene ranked as the world’s most common plastic due to its wide range of uses, from plastic bags to synthetic fibers and construction materials. Recycling limitations, driven by product type and local infrastructure, send large volumes of polyethylene waste to landfills.
“To sustainably enhance asphalt pavements, we targeted vast, often unutilized streams of polyethylene waste; the films and mixed-color plastics others found challenging to recycle,” Buttlar said. “This abundant, low-cost resource offered a robust supply for large-scale modification.”
The team discovered that polyethylene’s thermal stability and chemical resistance helped pavements withstand temperature changes and environmental stress. Its flexibility and toughness strengthened the asphalt, reducing cracking and rutting under pressure while improving durability and water resistance to extend pavement life. Additionally, polyethylene bonded well with asphalt binders, boosting stability, flow, dynamic modulus, water sensitivity, deformation resistance, strength, and density.
The next test involved paving nine sections on Interstate 55 in Missouri, a major highway connecting Chicago and New Orleans. The team experimented with different plastics and aggregate structures, which also held up well.
More For You: Conductive Asphalt Deices Itself
Contractors also applied various traffic-level mixes to neighborhood streets in Kansas City, where the asphalt withstood its first winter successfully. Across these projects, spanning diverse traffic demands and environments, the plastic-modified asphalt delivered reliable performance and practical usability.
Extending their research to airport runways meant the research team had to meet a higher performance level. For airfield pavements, safety concerns extended beyond highway standards. Foreign Object Debris (FOD), loose pieces of aggregate or other materials, posed a serious hazard to aircraft, potentially damaging engines or fuselages. Because of these risks, new runway surfaces needed more than performance gains like rutting resistance; they had to reduce cracking at low temperatures and avoid contributing to FOD.
Smooth, rut-free surfaces also helped prevent hydroplaning and supported softer landings by improving breaking conditions.
On This Topic: Leveraging Symbiosis for Self-Healing Concrete
“Runway design demands strict control of foreign object debris since broken pavement can damage aircraft. No innovation should improve heat resistance at the cost of increased low-temperature cracking and FOD risk,” Buttlar said.
The research team collaborated with the Federal Aviation Administration to identify potential test sites in Missouri, Iowa, or Illinois for post-consumer plastic runways. While scouting locations, the team completed lab testing and simulations to adapt the highway-tested asphalt formula for airfield demands.
They also conducted proactive testing for PFAS (per- and polyfluoroalkyl substances also known as “forever chemicals”), detecting none in their plastic feedstock. Their process safely entombed waste plastic inside the asphalt, preventing leaching and environmental exposure.
This project is a collaboration between the Mizzou Asphalt Pavement and Innovation Lab and the Federal Aviation Administration (FAA). As infrastructure demands increased globally, researchers offered a timely, sustainable solution. Their work diverted waste plastics from landfills and strengthened essential infrastructure, from roads to runways. Through continued testing and partnerships, this innovative asphalt technology could soon transform transportation networks, paving the way for greener, safer, and more resilient roads and runways.
Nicole Imeson is an engineer and writer in Calgary, Alta.
Finding a way to supplement bitumen, a black, tarry constituent of petroleum, would make asphalt cheaper and could improve its performance.
Researchers at the University of Missouri are developing a post-consumer plastic asphalt. In recent trials, they replaced up to 40 percent of the bitumen with polyethylene, referred to as a modifier, to reduce expensive binder volume, improve asphalt performance, and advance sustainability. Their work showed that recycled materials could meet engineering demands and reduce environmental impact.
Now, they are looking to extend their work to much more demanding airport runways.
The asphalt modification used two main methods. The so-called wet process blends modifiers with the binder before combining it with aggregates, often resulting in a more uniform binder.
In their work, the University of Missouri team prioritized the dry process, where they added modifiers directly to the aggregate during mixing. This approach simplified production but risked creating a nonuniform binder.
“The dry process lets contractors modify asphalt on demand,” explained Bill Buttlar, the Glen Barton Chair in Flexible Pavement Technology in the Department of Civil and Environmental Engineering at the University of Missouri in Columbia. “They injected granulated or powdered plastic into the mixing drum with aggregate and binder, avoiding days-ahead orders and higher costs tied to supplier-prepared wet-modified binder.”
Cutting costs
The aggregate to binder mix varies depending on traffic demands, environmental concerns like temperature or humidity, and the need to balance strength with flexibility, though a 95:5 ratio is common. Even with that relatively small contribution has prompted engineers to look for an alternative to bitumen.“Given the significant cost gap between binder, at least $600-700 per ton, and aggregate, around $20 per ton, even a partial 20 percent replacement of the binder with lower cost recycled materials delivered major economic benefits, especially in high-priced modified asphalt mixtures,” Buttlar said.
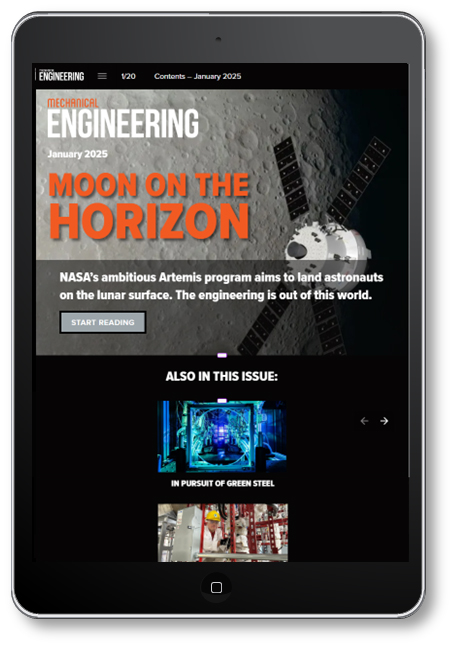
Read Mechanical Engineering
Mechanical Engineering magazine is available for ASME members. Read the magazine wherever you go!
Polyethylene ranked as the world’s most common plastic due to its wide range of uses, from plastic bags to synthetic fibers and construction materials. Recycling limitations, driven by product type and local infrastructure, send large volumes of polyethylene waste to landfills.
“To sustainably enhance asphalt pavements, we targeted vast, often unutilized streams of polyethylene waste; the films and mixed-color plastics others found challenging to recycle,” Buttlar said. “This abundant, low-cost resource offered a robust supply for large-scale modification.”
The team discovered that polyethylene’s thermal stability and chemical resistance helped pavements withstand temperature changes and environmental stress. Its flexibility and toughness strengthened the asphalt, reducing cracking and rutting under pressure while improving durability and water resistance to extend pavement life. Additionally, polyethylene bonded well with asphalt binders, boosting stability, flow, dynamic modulus, water sensitivity, deformation resistance, strength, and density.
Asphalt into action
The research team previously collaborated with the Missouri Department of Transportation to develop and test road asphalt using recycled materials. In 2021, researchers launched field trials of plastic-modified asphalt with a thin overlay south of the University of Missouri campus. After enduring four winters, the test sections demonstrated strong durability.The next test involved paving nine sections on Interstate 55 in Missouri, a major highway connecting Chicago and New Orleans. The team experimented with different plastics and aggregate structures, which also held up well.
More For You: Conductive Asphalt Deices Itself
Contractors also applied various traffic-level mixes to neighborhood streets in Kansas City, where the asphalt withstood its first winter successfully. Across these projects, spanning diverse traffic demands and environments, the plastic-modified asphalt delivered reliable performance and practical usability.
Extending their research to airport runways meant the research team had to meet a higher performance level. For airfield pavements, safety concerns extended beyond highway standards. Foreign Object Debris (FOD), loose pieces of aggregate or other materials, posed a serious hazard to aircraft, potentially damaging engines or fuselages. Because of these risks, new runway surfaces needed more than performance gains like rutting resistance; they had to reduce cracking at low temperatures and avoid contributing to FOD.
Smooth, rut-free surfaces also helped prevent hydroplaning and supported softer landings by improving breaking conditions.
On This Topic: Leveraging Symbiosis for Self-Healing Concrete
“Runway design demands strict control of foreign object debris since broken pavement can damage aircraft. No innovation should improve heat resistance at the cost of increased low-temperature cracking and FOD risk,” Buttlar said.
The research team collaborated with the Federal Aviation Administration to identify potential test sites in Missouri, Iowa, or Illinois for post-consumer plastic runways. While scouting locations, the team completed lab testing and simulations to adapt the highway-tested asphalt formula for airfield demands.
Avoiding microplastics
The team addressed environmental concerns by examining the potential for microplastic release over the lifespan of the plastic modified runway, even though the binder encapsulated the plastic and protected it from the elements. In the lab, tests confirmed negligible microplastic runoff and researchers found no significant release from the modified asphalt.They also conducted proactive testing for PFAS (per- and polyfluoroalkyl substances also known as “forever chemicals”), detecting none in their plastic feedstock. Their process safely entombed waste plastic inside the asphalt, preventing leaching and environmental exposure.
This project is a collaboration between the Mizzou Asphalt Pavement and Innovation Lab and the Federal Aviation Administration (FAA). As infrastructure demands increased globally, researchers offered a timely, sustainable solution. Their work diverted waste plastics from landfills and strengthened essential infrastructure, from roads to runways. Through continued testing and partnerships, this innovative asphalt technology could soon transform transportation networks, paving the way for greener, safer, and more resilient roads and runways.
Nicole Imeson is an engineer and writer in Calgary, Alta.
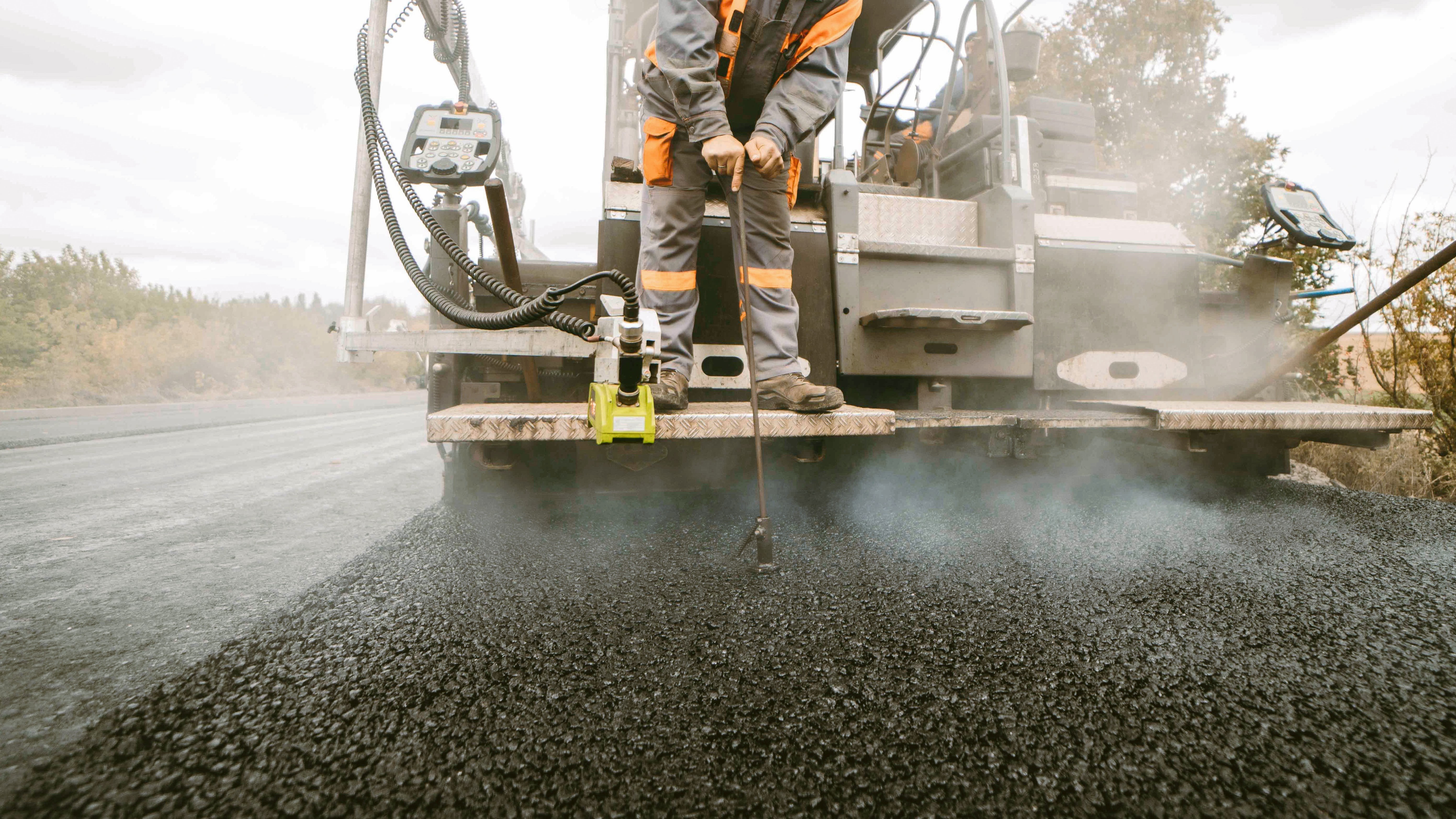
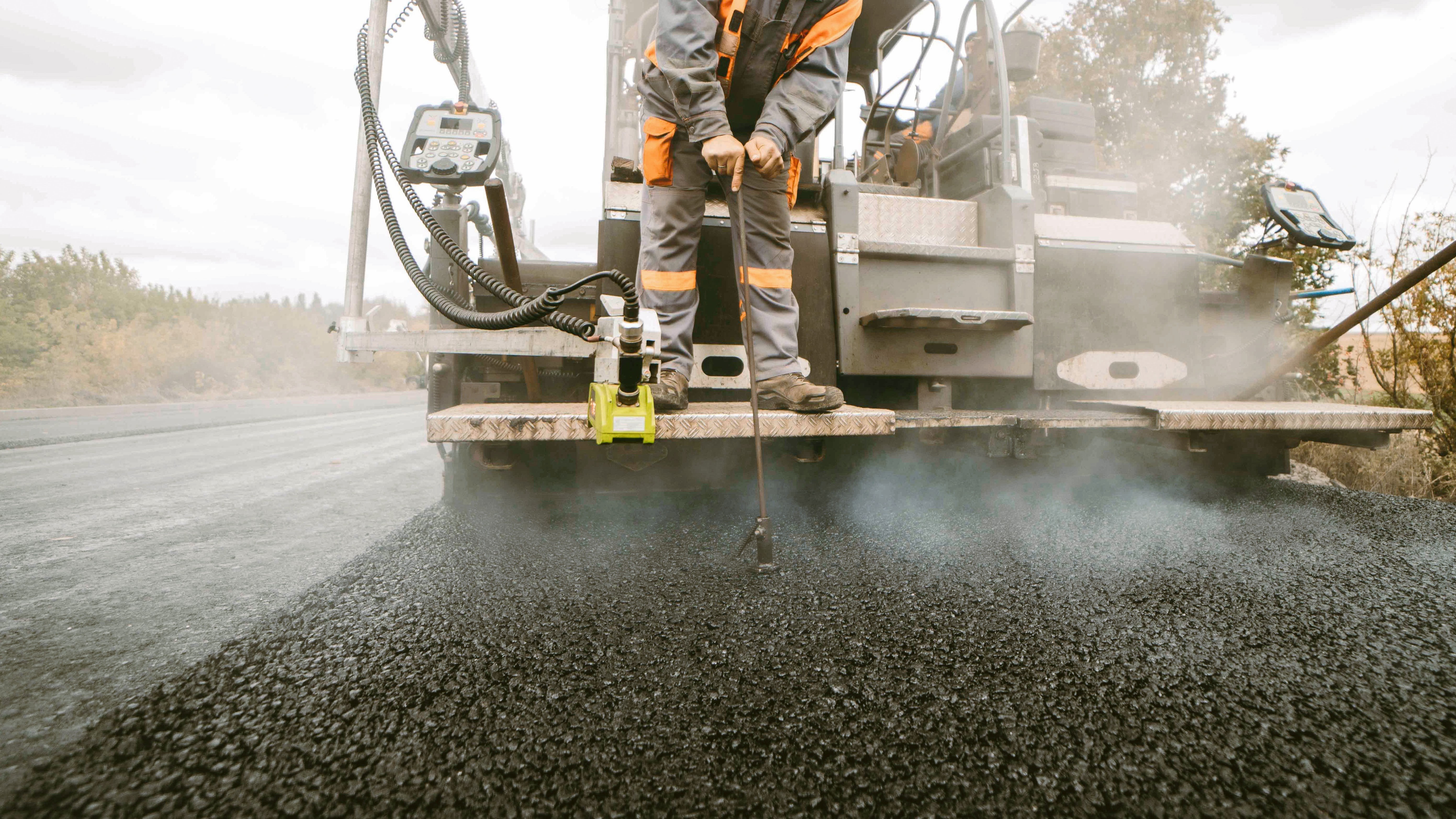