Manufacturing Blog: Mining Looks to Digitalization and More to Decarbonize
Manufacturing Blog: Mining Looks to Digitalization and More to Decarbonize
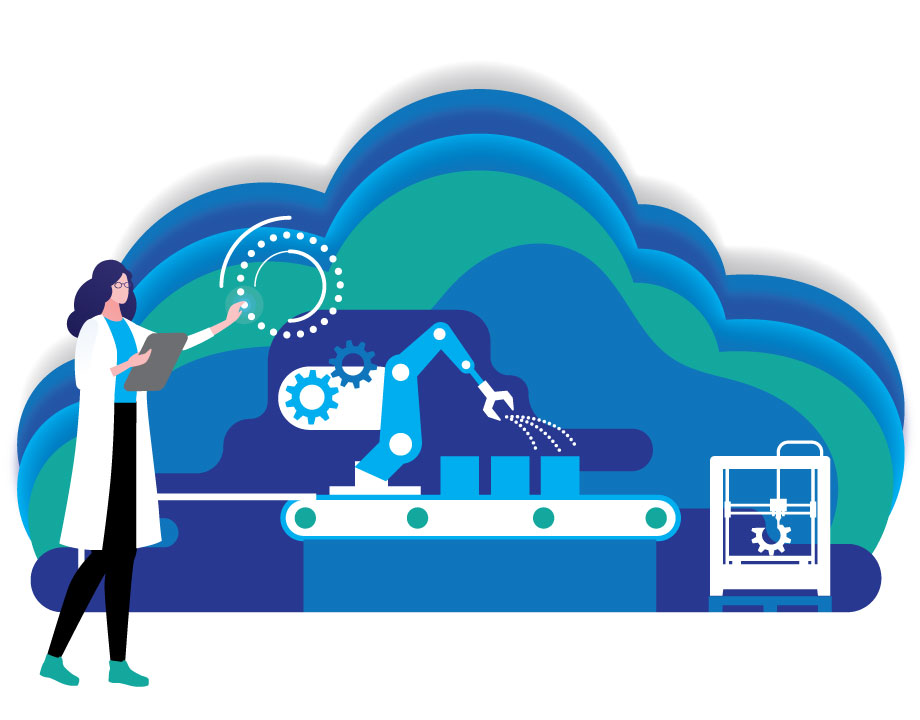
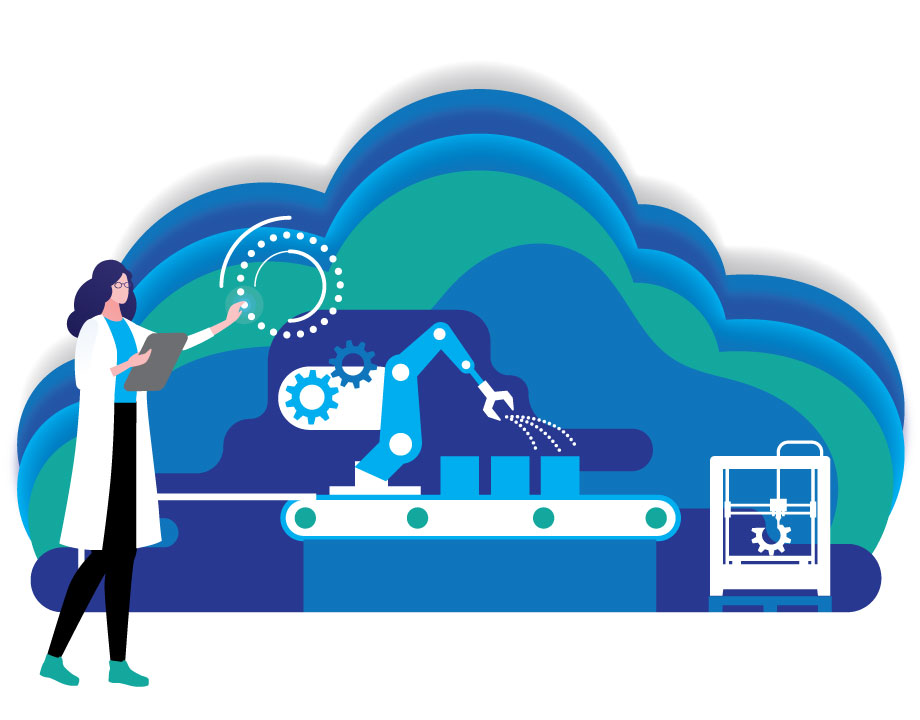
Mining companies are beginning to clean up their operations in efforts to quickly decarbonize.
There is a paradox in decarbonization efforts, where the move toward electric and autonomous vehicles is so dependent on metals and rare earth minerals needed for batteries to power those emissionless vehicles. Mining those materials has traditionally been a dirty and environmentally unfriendly job. But the industry is starting to pay attention.
At its heart is the need to overcome what EY calls “stubborn resistance” to modernization, similar to what other industries are now going through. Cross-functional collaboration, integration of Big Data, and rapid innovation are key to the future of mining. “If mining and metals companies are to survive and thrive in a new energy world, they must embrace digital to optimize productivity from market to mine,” according to an EY analysis.
An earlier EY poll showed that the majority of leading mining business have introduced digital technology of some sort, especially in autonomous and IoT technologies. But that only accounts for some 10 percent of the universe. Many firms still rely on manual or cabled readings rather than wireless systems connected to digitized mining assets.
“Cross-sector thinking also means borrowing digital know-how from nonparallel industries,” wrote Iliya Garkov, vice president and managing director of Dundee Precious Metals, in the EY report. “Industries like air traffic control and even electronic gaming, where the use of advance cameras and AI can boost safety, transparency and sustainability while reducing cost.”
Watch the Video: Aerospace Embraces Digitalization
Like others, the mining industry is looking to decarbonize operations. The industry contributes 2 percent to 3 percent of global carbon dioxide emissions, according to McKinsey & Co. The industry has been divesting itself of coal assets, but regulators and customers are also exerting pressure. Sweden’s H2 Green Steel wants to be the world’s first zero-carbon steel producer, and to do that it needs zero or low-carbon iron ore.
Mining follows other industries where automation is key for more efficient operations. Autonomous mining vehicles already have a track record, although many are semi-autonomous, needing some operator assistance. The next step is developing an autonomous mining system, where many tasks are performed automatically.
An autonomous operation uses an interconnected digital network that, for instance, could protect miners through sensors to detect ground movement or gas leaks. The system can also be used remotely, where workers control multiple operations. In open pit mines, driverless trucks move material using GPS coordinates while automated loading equipment moves the material into the truck bed.
Fortescue Metals Group, an Australian mining company, recently accelerated its decarbonization efforts, moving to achieve carbon neutrality by 2030. Stationary power sources and its fleet of mining equipment represents the bulk of FMG’s emissions. The firm’s initial efforts focus on using renewable energy to power its sites, including battery storage, and eliminating diesel and gas-fueled generating operations.
More for You: How Five Countries Work toward Decarbonization
Vehicle and equipment emissions account for 26 percent of the firm’s emissions, and eliminating that source is one of the biggest problems facing the industry, according to the firm. The industry lacks large-scale, technically viable vehicles for haulage.
FMG already had been working with UK-based Williams Advanced Engineering to develop a prototype battery system that can power an electric mining haul truck, and acquired the firm earlier this year to bolster its portfolio. The work is expanding to develop a zero-emissions train powered by regenerating batteries.
FMG’s rail operations include 54 diesel locomotives that haul 16 train sets, along with other on-track mobile equipment. Each train set hauls iron ore in 244 ore cars. In 2021, the trains accounted for 11 percent of the firm’s emissions.
The firm claims the “Infinity Train” is the first to use gravitational energy generated in the downhill sections of its rail network to recharge the batteries. That would supply enough power for the train to return and reload.
Reader's Choice: Hydrogen Straight from the Earth
“The Infinity Train has the capacity to be the world’s most efficient battery electric locomotive,” said Elizabeth Gaines, FMG chief executive officer in a statement. “The regeneration of electricity on the downhill loaded sections will remove the need for the installation of renewable energy generation and recharging infrastructure, making it a capital efficient solution for eliminating diesel and emissions from our rail operations.”
Battery-powered mining equipment is beginning to be more broadly used, according to research firm Global Data. There are currently 157 electric loaders and 45 electric trucks operating globally in underground mines. Besides reducing greenhouse gases, their use significantly reduces ventilation and cooling costs, the firm noted.
John Kosowatz is senior editor.
At its heart is the need to overcome what EY calls “stubborn resistance” to modernization, similar to what other industries are now going through. Cross-functional collaboration, integration of Big Data, and rapid innovation are key to the future of mining. “If mining and metals companies are to survive and thrive in a new energy world, they must embrace digital to optimize productivity from market to mine,” according to an EY analysis.
An earlier EY poll showed that the majority of leading mining business have introduced digital technology of some sort, especially in autonomous and IoT technologies. But that only accounts for some 10 percent of the universe. Many firms still rely on manual or cabled readings rather than wireless systems connected to digitized mining assets.
“Cross-sector thinking also means borrowing digital know-how from nonparallel industries,” wrote Iliya Garkov, vice president and managing director of Dundee Precious Metals, in the EY report. “Industries like air traffic control and even electronic gaming, where the use of advance cameras and AI can boost safety, transparency and sustainability while reducing cost.”
Watch the Video: Aerospace Embraces Digitalization
Like others, the mining industry is looking to decarbonize operations. The industry contributes 2 percent to 3 percent of global carbon dioxide emissions, according to McKinsey & Co. The industry has been divesting itself of coal assets, but regulators and customers are also exerting pressure. Sweden’s H2 Green Steel wants to be the world’s first zero-carbon steel producer, and to do that it needs zero or low-carbon iron ore.
Mining follows other industries where automation is key for more efficient operations. Autonomous mining vehicles already have a track record, although many are semi-autonomous, needing some operator assistance. The next step is developing an autonomous mining system, where many tasks are performed automatically.
An autonomous operation uses an interconnected digital network that, for instance, could protect miners through sensors to detect ground movement or gas leaks. The system can also be used remotely, where workers control multiple operations. In open pit mines, driverless trucks move material using GPS coordinates while automated loading equipment moves the material into the truck bed.
Fortescue Metals Group, an Australian mining company, recently accelerated its decarbonization efforts, moving to achieve carbon neutrality by 2030. Stationary power sources and its fleet of mining equipment represents the bulk of FMG’s emissions. The firm’s initial efforts focus on using renewable energy to power its sites, including battery storage, and eliminating diesel and gas-fueled generating operations.
More for You: How Five Countries Work toward Decarbonization
Vehicle and equipment emissions account for 26 percent of the firm’s emissions, and eliminating that source is one of the biggest problems facing the industry, according to the firm. The industry lacks large-scale, technically viable vehicles for haulage.
FMG already had been working with UK-based Williams Advanced Engineering to develop a prototype battery system that can power an electric mining haul truck, and acquired the firm earlier this year to bolster its portfolio. The work is expanding to develop a zero-emissions train powered by regenerating batteries.
FMG’s rail operations include 54 diesel locomotives that haul 16 train sets, along with other on-track mobile equipment. Each train set hauls iron ore in 244 ore cars. In 2021, the trains accounted for 11 percent of the firm’s emissions.
The firm claims the “Infinity Train” is the first to use gravitational energy generated in the downhill sections of its rail network to recharge the batteries. That would supply enough power for the train to return and reload.
Reader's Choice: Hydrogen Straight from the Earth
“The Infinity Train has the capacity to be the world’s most efficient battery electric locomotive,” said Elizabeth Gaines, FMG chief executive officer in a statement. “The regeneration of electricity on the downhill loaded sections will remove the need for the installation of renewable energy generation and recharging infrastructure, making it a capital efficient solution for eliminating diesel and emissions from our rail operations.”
Battery-powered mining equipment is beginning to be more broadly used, according to research firm Global Data. There are currently 157 electric loaders and 45 electric trucks operating globally in underground mines. Besides reducing greenhouse gases, their use significantly reduces ventilation and cooling costs, the firm noted.
John Kosowatz is senior editor.