AI Robotic Automation Key to Poultry Processing Evolution
AI Robotic Automation Key to Poultry Processing Evolution
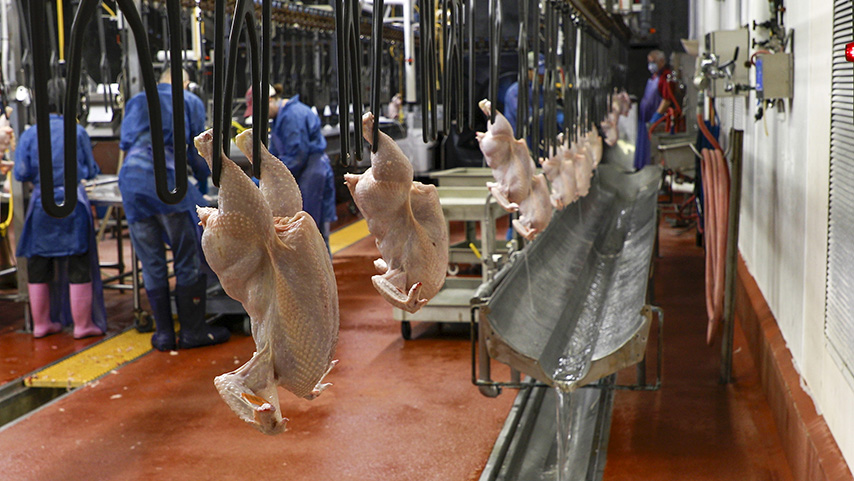
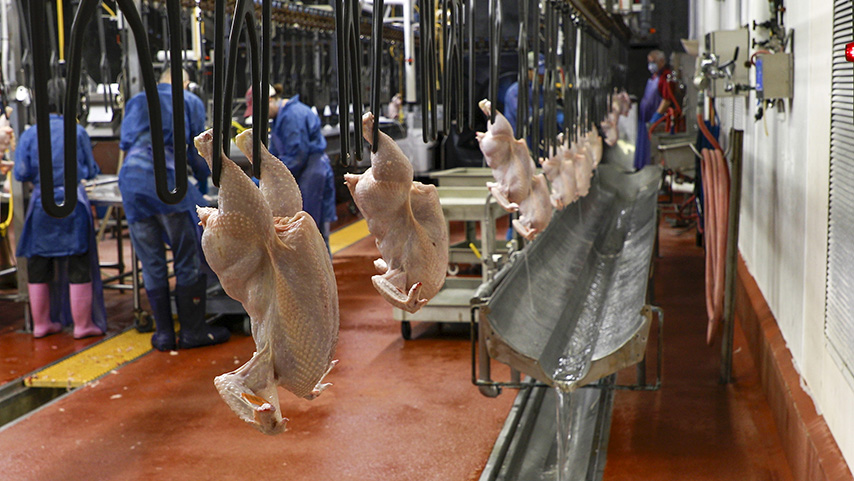
The Center for Scalable and Intelligent Automation in Poultry Processing aims to adapt robotic automation to the poultry processing industry.
Although the advent of the assembly line helped set the stage for increased productivity and efficiency across numerous industries, some benefited more than others. The poultry industry has taken some steps to adopt assembly line strategies but has remained somewhat stagnant with limited addition of robotics at the product level, still relying heavily on human workers to debone chickens to get the most meat yield possible at processing plants. But a team from four research institutions—the University of Arkansas, Georgia Institute of Technology, University of Nebraska-Lincoln, and Fort Valley State University—is leading an effort to develop industry-specific AI and robotics specifically for this purpose.
A four-year $5-million grant from the U.S. Department of Agriculture's National Institute of Food and Agriculture establishes the Center for Scalable and Intelligent Automation in Poultry Processing. Led by the University of Arkansas System Division of Agriculture, this collaborative effort will merge AI, machine learning, and robotics to advance chicken meat processing operations, sanitation, and even the social effects of AI robotics on the industry.
“There are few robotic deboning systems implemented in the industry,” he said. “So, one of the things we are trying to look at is how do we use AI and how do we individualize the cut based on each bird? That's the main objective.”
Raw chickens are slippery and squishy, affecting how they respond to robotic manipulation. Automated robotics has lagged not only in meat processing, but in other processes where there are innumerable variables, such as harvesting fruits and vegetables outdoors.
You Might Also Enjoy: 5 Agricultural Robots Bringing Food to the Table
“Because of AI's ability to use deep learning, where you can give the computer just lots and lots of examples of chickens or lots and lots of examples of peach trees, it'll figure out the patterns that will allow you to make sense of that unstructured environment,” explained Ai-Ping Hu, principal research engineer, Agricultural Technology Research Program, at Georgia Tech. “So that's how we're leveraging those technologies that again have really just come to the forefront within the last couple of years, and we want to apply it to a place where it's critically underserved.”
Some tasks are automated, but don’t really deal with handling the product, but rather after it's been packaged or the packaging process, Hu added. Poultry processing plants rely on workers, who typically stand in refrigerator-like temperatures for 8-10 hours a day deboning chickens at a rate of about 35 to 40 a minute. Although it's the most skilled job at the plant, it also has turnover of 50 percent or more annually.
Add to that “no rehire” policies that exist at some facilities, and now some plants are to the point of bussing people in from neighboring counties since they’ve run through everyone nearby, Hu noted.
Georgia Tech has received $2.1 million of the grant to develop the first automated poultry processing lines. “The way we're doing that is we're using machine vision to be able to characterize each unique bird carcass,” Hu said. “From that, we're able to predict where that shoulder joint is to a few millimeters.”
A robotic arm equipped with a knife will then execute a unique knife path that will extract the maximum amount of meat from that unique carcass. Although fixed automation machines do exist, they are limited in settings and take too much of a one-size-fits-most approach, leaving too much meat behind. Automated deboners will leave 16 percent to 17 percent of meat on a carcass, Subbiah said, while human deboners will only leave about 13 percent.
“There have actually been plants that put in fixed automation solutions at really high costs, and they've actually taken it out because they find that they lose too much yield, and they put people back in," Hu said. “We've got a solution where we can adjust to every unique bird because you've got a robot that can move and adjust itself, just like a human arm can."
Profit margins are slim, and the loss of even one percent of yield would translate to around $1.5 million per plant per year, Hu explained. “That's like a couple of nickel's worth of meat per carcass. That really adds up if you're cutting hundreds of birds per minute.”
The team aims to have a plant-ready system that has been tested within a plant for at least six months, to prove that it’s ready for commercialization and can perform at parity or better than human workers.
“We think that with proper programming and learning from human trials that we can actually come up with a system that will exceed what people can do,” Hu added.
Become a Member: How to Join ASME
To further assist with machine learning, the second objective will explore the use of VR to change how labor is performed in chicken processing plants.
“We have an interface that allows a headset wearer to be virtually inside a plant and they'll actually work with the robot to do a task such as picking a bird out of a big pile and then putting it onto an assembly line,” Hu explained. “Because AI is not really 100 percent accurate quite yet, there are still things that a person's able to do better. The idea is collaboration between the robot and that headset. "Once the robot knows where to approach that carcass, it does the rest because it's physically inside the plant.”
This approach would diversify the workforce, making it possible for anyone with access to VR goggles and haptics gloves to, once trained, work in such a facility remotely. It would also allow for plants to be more ideally located to reduce transportation costs and environmental impacts. “The intent is really to help the poultry industry to advance and be more sustainable,” Subbiah added. It could even be applied to other industries once refined.
Although the person helping the robot via VR would slowly work their way out of the job because AI will continue learning, that is the goal. The team hopes to have a proof of concept where the VR robot could at least match human workers’ output. “We also want to have proof of concept that it's actually learning by itself,” Hu said.
Pilot processing plants in Arkansas and Georgia will help the researchers test modules, Subbiah added.
The Arkansas Agricultural Experiment Station, the research arm of the University of Arkansas’ Division of Agriculture, received $2.2 million from the grant to focus on food safety automation.
Among the goals are looking at robotic sanitation, where an automated vehicle with hoses and scrubbers can go around a poultry plant to clean. Another is using a mobile robotic platform that uses a biosensor to “biomap” the facility, highlighting hot and cold spots, where organic material or bacterial populations are high, Subbiah explained. “Then where it seems to be high, the robot takes a swab for a traditional microbial analysis. Then you can see places that need to be cleaned better. So, we’ll automate environmental mapping so that we can proactively improve food safety.”
The team is also working on a hyperspectral imaging system to detect the foreign materials on the processing line, such as pieces of plastic, gloves, or other nonmetallic items that an x-ray would otherwise detect.
A proof-of-concept system with robots cleaning plants is the end goal. “We also think that with an automated solution where the robot can see exactly what places need more attention, you can actually save water [during the sanitation process], so I think there's an environmental component there as well,” Hu added.
Remaining grant funds have been allocated to the University of Nebraska-Lincoln and Fort Valley State University in Georgia. The UNL team is leading the fourth objective, which examines the social components of this entire effort and will be led by Julia McQuillan, Willa Cather professor of sociology.
Manufacturing Blog: How to Identify AI Systems and Realistic Implementation
“They’ll be answering questions such as, if you start introducing robots into these environments that have never seen robots, what is the implication to the people working inside the plant? What is the implication to the whole food chain? All those kinds of not strictly technical problems, but rather the ‘silo’ impact,” Hu explained.
This effort will culminate in a set of guidelines or best practices for how the industry introduces automation and other such technology.
At the end of the four-year process, the Center for Scalable and Intelligent Automation in Poultry Processing will look to license out the resulting technologies for scaling and production at a commercial level.
“I think it's rare in an engineer's career to be able to work on a project that will impact so many people, and where there's such a clear need for it,” Hu said. “I think a lot of times—and I’m guilty of this as well—when you do research projects, oftentimes in a sense, the justification for why it's important is fairly cursory. Here, there's a demonstrated need. I know it's going to have a real-world impact on lots of people from all different strata of the industry.”
Louise Poirier is senior editor.
A four-year $5-million grant from the U.S. Department of Agriculture's National Institute of Food and Agriculture establishes the Center for Scalable and Intelligent Automation in Poultry Processing. Led by the University of Arkansas System Division of Agriculture, this collaborative effort will merge AI, machine learning, and robotics to advance chicken meat processing operations, sanitation, and even the social effects of AI robotics on the industry.
Industry hurdles
Unlike machinery assembly lines, chicken deboning lines face tremendous biological variability, explained project director Jeyam Subbiah, a professor and head of the food science department for the Division of Agriculture and the Dale Bumpers College of Agricultural, Food and Life Sciences at the University of Arkansas.“There are few robotic deboning systems implemented in the industry,” he said. “So, one of the things we are trying to look at is how do we use AI and how do we individualize the cut based on each bird? That's the main objective.”
Raw chickens are slippery and squishy, affecting how they respond to robotic manipulation. Automated robotics has lagged not only in meat processing, but in other processes where there are innumerable variables, such as harvesting fruits and vegetables outdoors.
You Might Also Enjoy: 5 Agricultural Robots Bringing Food to the Table
“Because of AI's ability to use deep learning, where you can give the computer just lots and lots of examples of chickens or lots and lots of examples of peach trees, it'll figure out the patterns that will allow you to make sense of that unstructured environment,” explained Ai-Ping Hu, principal research engineer, Agricultural Technology Research Program, at Georgia Tech. “So that's how we're leveraging those technologies that again have really just come to the forefront within the last couple of years, and we want to apply it to a place where it's critically underserved.”
Some tasks are automated, but don’t really deal with handling the product, but rather after it's been packaged or the packaging process, Hu added. Poultry processing plants rely on workers, who typically stand in refrigerator-like temperatures for 8-10 hours a day deboning chickens at a rate of about 35 to 40 a minute. Although it's the most skilled job at the plant, it also has turnover of 50 percent or more annually.
Add to that “no rehire” policies that exist at some facilities, and now some plants are to the point of bussing people in from neighboring counties since they’ve run through everyone nearby, Hu noted.
Assistance unlocked
Researchers are focusing their efforts on four core objectives. The first two are merging AI and robotics to help the poultry industry achieve better yields at chicken deboning facilities and introducing virtual reality-assisted robotics.Georgia Tech has received $2.1 million of the grant to develop the first automated poultry processing lines. “The way we're doing that is we're using machine vision to be able to characterize each unique bird carcass,” Hu said. “From that, we're able to predict where that shoulder joint is to a few millimeters.”
A robotic arm equipped with a knife will then execute a unique knife path that will extract the maximum amount of meat from that unique carcass. Although fixed automation machines do exist, they are limited in settings and take too much of a one-size-fits-most approach, leaving too much meat behind. Automated deboners will leave 16 percent to 17 percent of meat on a carcass, Subbiah said, while human deboners will only leave about 13 percent.
“There have actually been plants that put in fixed automation solutions at really high costs, and they've actually taken it out because they find that they lose too much yield, and they put people back in," Hu said. “We've got a solution where we can adjust to every unique bird because you've got a robot that can move and adjust itself, just like a human arm can."
Profit margins are slim, and the loss of even one percent of yield would translate to around $1.5 million per plant per year, Hu explained. “That's like a couple of nickel's worth of meat per carcass. That really adds up if you're cutting hundreds of birds per minute.”
The team aims to have a plant-ready system that has been tested within a plant for at least six months, to prove that it’s ready for commercialization and can perform at parity or better than human workers.
“We think that with proper programming and learning from human trials that we can actually come up with a system that will exceed what people can do,” Hu added.
Become a Member: How to Join ASME
To further assist with machine learning, the second objective will explore the use of VR to change how labor is performed in chicken processing plants.
“We have an interface that allows a headset wearer to be virtually inside a plant and they'll actually work with the robot to do a task such as picking a bird out of a big pile and then putting it onto an assembly line,” Hu explained. “Because AI is not really 100 percent accurate quite yet, there are still things that a person's able to do better. The idea is collaboration between the robot and that headset. "Once the robot knows where to approach that carcass, it does the rest because it's physically inside the plant.”
This approach would diversify the workforce, making it possible for anyone with access to VR goggles and haptics gloves to, once trained, work in such a facility remotely. It would also allow for plants to be more ideally located to reduce transportation costs and environmental impacts. “The intent is really to help the poultry industry to advance and be more sustainable,” Subbiah added. It could even be applied to other industries once refined.
Although the person helping the robot via VR would slowly work their way out of the job because AI will continue learning, that is the goal. The team hopes to have a proof of concept where the VR robot could at least match human workers’ output. “We also want to have proof of concept that it's actually learning by itself,” Hu said.
Pilot processing plants in Arkansas and Georgia will help the researchers test modules, Subbiah added.
Broadened scopes
As for the final two objectives, the center will explore robotic and sensor assisted sanitation and determine the social impacts the use of such technology will have on industry and people near to it.The Arkansas Agricultural Experiment Station, the research arm of the University of Arkansas’ Division of Agriculture, received $2.2 million from the grant to focus on food safety automation.
Among the goals are looking at robotic sanitation, where an automated vehicle with hoses and scrubbers can go around a poultry plant to clean. Another is using a mobile robotic platform that uses a biosensor to “biomap” the facility, highlighting hot and cold spots, where organic material or bacterial populations are high, Subbiah explained. “Then where it seems to be high, the robot takes a swab for a traditional microbial analysis. Then you can see places that need to be cleaned better. So, we’ll automate environmental mapping so that we can proactively improve food safety.”
The team is also working on a hyperspectral imaging system to detect the foreign materials on the processing line, such as pieces of plastic, gloves, or other nonmetallic items that an x-ray would otherwise detect.
A proof-of-concept system with robots cleaning plants is the end goal. “We also think that with an automated solution where the robot can see exactly what places need more attention, you can actually save water [during the sanitation process], so I think there's an environmental component there as well,” Hu added.
Remaining grant funds have been allocated to the University of Nebraska-Lincoln and Fort Valley State University in Georgia. The UNL team is leading the fourth objective, which examines the social components of this entire effort and will be led by Julia McQuillan, Willa Cather professor of sociology.
Manufacturing Blog: How to Identify AI Systems and Realistic Implementation
“They’ll be answering questions such as, if you start introducing robots into these environments that have never seen robots, what is the implication to the people working inside the plant? What is the implication to the whole food chain? All those kinds of not strictly technical problems, but rather the ‘silo’ impact,” Hu explained.
This effort will culminate in a set of guidelines or best practices for how the industry introduces automation and other such technology.
At the end of the four-year process, the Center for Scalable and Intelligent Automation in Poultry Processing will look to license out the resulting technologies for scaling and production at a commercial level.
“I think it's rare in an engineer's career to be able to work on a project that will impact so many people, and where there's such a clear need for it,” Hu said. “I think a lot of times—and I’m guilty of this as well—when you do research projects, oftentimes in a sense, the justification for why it's important is fairly cursory. Here, there's a demonstrated need. I know it's going to have a real-world impact on lots of people from all different strata of the industry.”
Louise Poirier is senior editor.
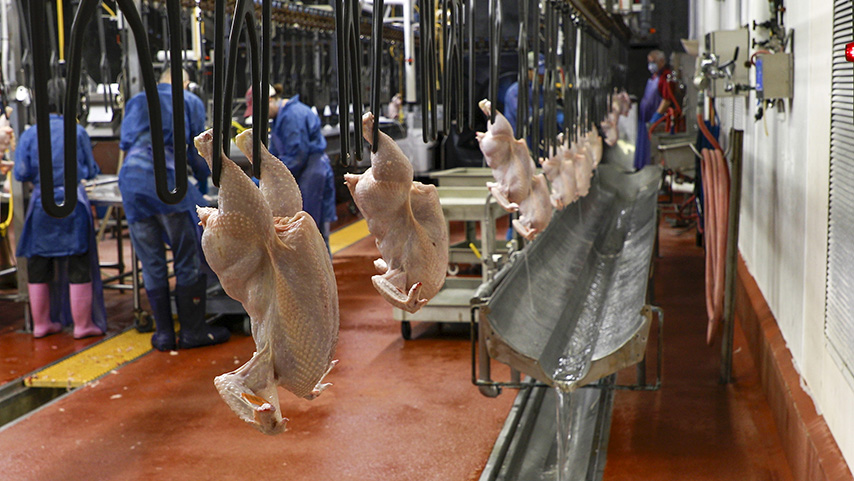
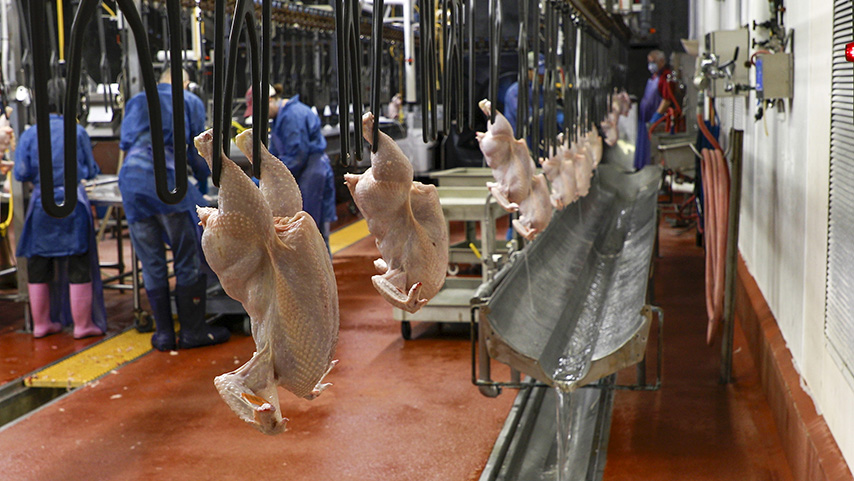