Conflict Isn’t the Problem, Failing to Address It Is
Conflict Isn’t the Problem, Failing to Address It Is
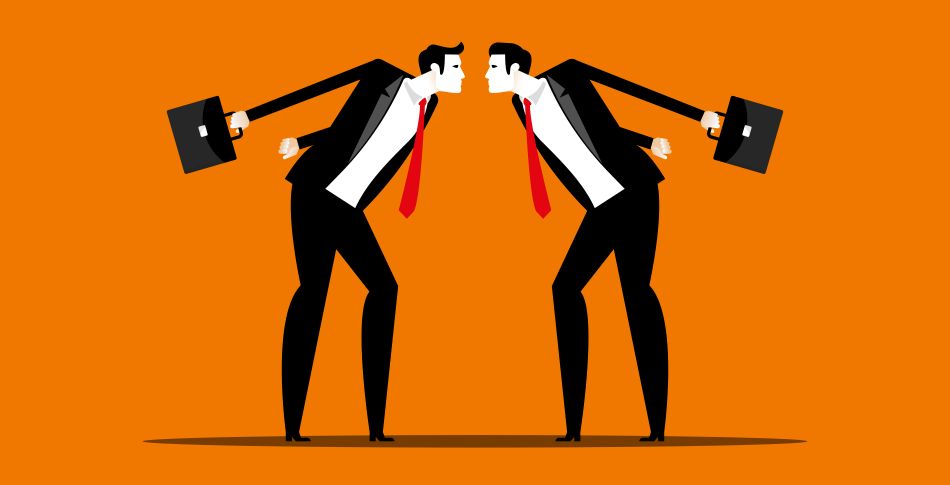
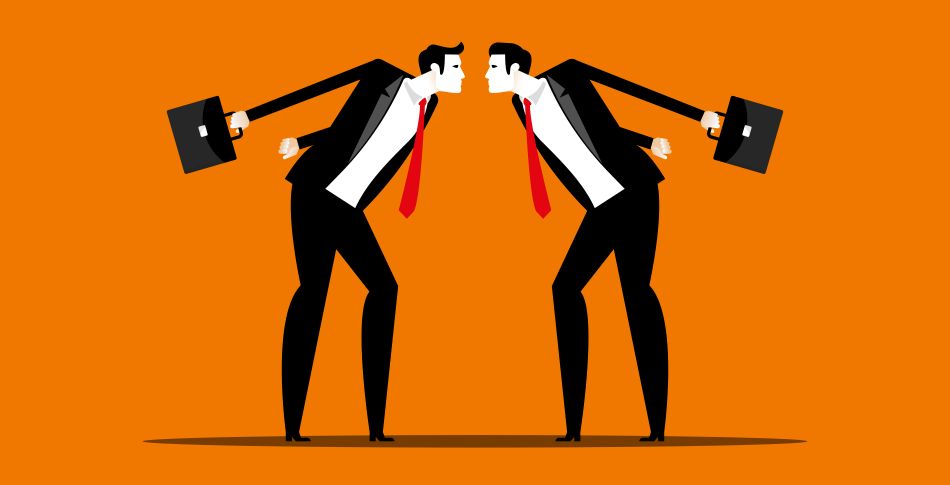
How mechanical engineers can tackle workplace tension without derailing collaboration.
Conflict is a natural byproduct of the work that mechanical engineers do. Disagreements arise over technical decisions, timelines, budgets, personnel, even personalities. Yet engineers often instinctively do all they can to avoid confrontation. This tendency, while understandable and in some ways admirable, can erode team cohesion, hinder project success, and cause stress to silently build.
“The problem isn’t conflict itself; it’s how we handle it,” explained Bobby Bakshi, a workplace alignment expert who has coached leaders in professional services industries. “Avoidance feels safer in the moment, but over time, it costs teams the clarity, accountability, and trust they need to work well together.”
Whether you’re a senior manager or a junior team member, developing conflict resolution skills isn’t just for HR professionals. It’s an essential part of engineering effectiveness. Fortunately, researchers and practitioners alike offer clear and actionable strategies that engineers can use to address conflict before it festers and drags down the team.
At its root, conflict emerges from differences: in goals, communication styles, technical opinions, and perceived responsibilities, to name a few. In a presentation to the American Society for Engineering Education, researchers at the University of Texas at El Paso, who implemented conflict resolution training in engineering capstone teams, categorized conflict in the work environment into three main types:
• Task conflict: Disagreements about technical approaches or project direction.
• Relationship conflict: Personality clashes or interpersonal tension.
• Process conflict: Frustrations over how work is assigned or executed, often linked to social loafing or coordination breakdowns.
According to the University of Texas El Paso (UTEP) study, “Teaching Engineers the Leadership Skill of Conflict Resolution,” task conflict, when managed well, can boost team performance by encouraging critical thinking and better decisions. But if left unchecked, it often spills into relationship conflict, undermining trust, and collaboration. Process conflict, meanwhile, tends to escalate when roles and expectations are unclear or when team members feel, perhaps incorrectly, that contributions are imbalanced.
A common trap in engineering culture is “being nice.” Engineers are wired to focus on data and technical accuracy, but to avoid emotional terrain. Experience shows that avoiding tough conversations doesn’t make the problems go away. It simply pushes the conflict below the surface, where it festers and re-emerges as missed deadlines, siloed work, or passive resistance.
“People say they want accountability, but you can’t get there without learning how to navigate disagreement,” Bakshi said. “We need structure for difficult conversations, especially when stakes are high.”
Bakshi developed the RESPECT Quotient, a seven-step framework to guide professional conflict resolution. While designed primarily for executive leaders, several elements translate well for any engineer facing interpersonal friction.
For instance, three of his core ideas—recognize, empathize and stretch—mirror best practices across the field. These steps encourage people to hear one another’s perspectives fully, stay curious, and expand their ability to see beyond their own assumptions. As Phil Yates, an engineer who writes about team management, notes in his May 2023 article “Best Practices for Managing Conflict in Engineering Management”: “Listen actively. Ask open-ended questions. Try to understand the situation from each person’s perspective.”
This echoes findings from the UTEP program, where engineering students reported that active listening was the most effective technique they used during team conflicts. In fact, students applied it unprompted in real project situations—such as when a team member wasn’t contributing or when assumptions led to early missteps.
Bakshi’s remaining steps—prioritize, empower, commit, and transform—shift the focus to action. Once perspectives are exchanged, team members identify what matters most and where the real disconnect lies (prioritize). Then each person takes ownership of moving forward, not by trying to fix the other person, but by taking responsibility for their own role in the solution with clarity and intention (empower). To make it stick, engineers should agree explicitly on next steps, who’s doing what, by when, and how to follow up (commit). Over time, this kind of sustained, respectful behavior leads to lasting improvements in team culture and performance (transform).
Based on insights from Bakshi, Yates, and the UTEP study, here are six strategies that mechanical engineers can use to resolve conflicts constructively:
1. Create clarity early
Set expectations around roles, timelines, and communication norms at the start of a project. A written team charter, as suggested in UTEP’s teaching modules, can prevent misunderstandings later.
2. Focus on the problem, not the person
When addressing an issue be specific and objective. “The design didn’t meet the load spec” is easier to hear than “You messed up the calculations.”
3. Ask before assuming
Misunderstandings often stem from inaccurate assumptions. One UTEP student shared how their team avoided future issues by simply asking more clarifying questions up front.
4. Don’t wait
As Yates emphasizes, avoiding difficult conversations only makes things worse. Address tensions early while they’re still manageable and before resentment builds.
5. Match assertiveness with cooperation
The Thomas-Kilmann model, a common framework in conflict management, suggests balancing the need to advocate for your perspective (assertiveness) with a willingness to find mutual ground (cooperation).
6. Make follow-up part of the process
A resolution without follow-through is just a polite conversation. Agree on next steps and schedule a check-in to assess progress.
Engineers don’t have to become amateur therapists to resolve conflict, they just need tools, structure, and the willingness to stretch. When managed well, even entrenched disagreements can become opportunities for improved collaboration.
Bakshi shared a story of two senior leaders at a Mountain Region firm who clashed over the direction of a cultural policy. Through structured conversations, they didn’t change their personal beliefs, but they did learn to listen better and co-create a solution that served the entire team. Their improved relationship became a model that others in the firm could follow.
At the end of the day, conflict resolution isn’t about winning an argument or avoiding one. It’s about learning to work better together, even when it’s difficult to do.
Jerry Guerra is an independent writer in Lynnfield, Mass.
“The problem isn’t conflict itself; it’s how we handle it,” explained Bobby Bakshi, a workplace alignment expert who has coached leaders in professional services industries. “Avoidance feels safer in the moment, but over time, it costs teams the clarity, accountability, and trust they need to work well together.”
Whether you’re a senior manager or a junior team member, developing conflict resolution skills isn’t just for HR professionals. It’s an essential part of engineering effectiveness. Fortunately, researchers and practitioners alike offer clear and actionable strategies that engineers can use to address conflict before it festers and drags down the team.
Engineering teams and workplace dynamics
At its root, conflict emerges from differences: in goals, communication styles, technical opinions, and perceived responsibilities, to name a few. In a presentation to the American Society for Engineering Education, researchers at the University of Texas at El Paso, who implemented conflict resolution training in engineering capstone teams, categorized conflict in the work environment into three main types:• Task conflict: Disagreements about technical approaches or project direction.
• Relationship conflict: Personality clashes or interpersonal tension.
• Process conflict: Frustrations over how work is assigned or executed, often linked to social loafing or coordination breakdowns.
According to the University of Texas El Paso (UTEP) study, “Teaching Engineers the Leadership Skill of Conflict Resolution,” task conflict, when managed well, can boost team performance by encouraging critical thinking and better decisions. But if left unchecked, it often spills into relationship conflict, undermining trust, and collaboration. Process conflict, meanwhile, tends to escalate when roles and expectations are unclear or when team members feel, perhaps incorrectly, that contributions are imbalanced.
Effective collaboration begins with conversation
A common trap in engineering culture is “being nice.” Engineers are wired to focus on data and technical accuracy, but to avoid emotional terrain. Experience shows that avoiding tough conversations doesn’t make the problems go away. It simply pushes the conflict below the surface, where it festers and re-emerges as missed deadlines, siloed work, or passive resistance.“People say they want accountability, but you can’t get there without learning how to navigate disagreement,” Bakshi said. “We need structure for difficult conversations, especially when stakes are high.”
Embrace structure methodically
Bakshi developed the RESPECT Quotient, a seven-step framework to guide professional conflict resolution. While designed primarily for executive leaders, several elements translate well for any engineer facing interpersonal friction.For instance, three of his core ideas—recognize, empathize and stretch—mirror best practices across the field. These steps encourage people to hear one another’s perspectives fully, stay curious, and expand their ability to see beyond their own assumptions. As Phil Yates, an engineer who writes about team management, notes in his May 2023 article “Best Practices for Managing Conflict in Engineering Management”: “Listen actively. Ask open-ended questions. Try to understand the situation from each person’s perspective.”
This echoes findings from the UTEP program, where engineering students reported that active listening was the most effective technique they used during team conflicts. In fact, students applied it unprompted in real project situations—such as when a team member wasn’t contributing or when assumptions led to early missteps.
Bakshi’s remaining steps—prioritize, empower, commit, and transform—shift the focus to action. Once perspectives are exchanged, team members identify what matters most and where the real disconnect lies (prioritize). Then each person takes ownership of moving forward, not by trying to fix the other person, but by taking responsibility for their own role in the solution with clarity and intention (empower). To make it stick, engineers should agree explicitly on next steps, who’s doing what, by when, and how to follow up (commit). Over time, this kind of sustained, respectful behavior leads to lasting improvements in team culture and performance (transform).
Resolving conflicts
Based on insights from Bakshi, Yates, and the UTEP study, here are six strategies that mechanical engineers can use to resolve conflicts constructively:1. Create clarity early
Set expectations around roles, timelines, and communication norms at the start of a project. A written team charter, as suggested in UTEP’s teaching modules, can prevent misunderstandings later.
2. Focus on the problem, not the person
When addressing an issue be specific and objective. “The design didn’t meet the load spec” is easier to hear than “You messed up the calculations.”
3. Ask before assuming
Misunderstandings often stem from inaccurate assumptions. One UTEP student shared how their team avoided future issues by simply asking more clarifying questions up front.
4. Don’t wait
As Yates emphasizes, avoiding difficult conversations only makes things worse. Address tensions early while they’re still manageable and before resentment builds.
5. Match assertiveness with cooperation
The Thomas-Kilmann model, a common framework in conflict management, suggests balancing the need to advocate for your perspective (assertiveness) with a willingness to find mutual ground (cooperation).
6. Make follow-up part of the process
A resolution without follow-through is just a polite conversation. Agree on next steps and schedule a check-in to assess progress.
When respect becomes a culture
Engineers don’t have to become amateur therapists to resolve conflict, they just need tools, structure, and the willingness to stretch. When managed well, even entrenched disagreements can become opportunities for improved collaboration.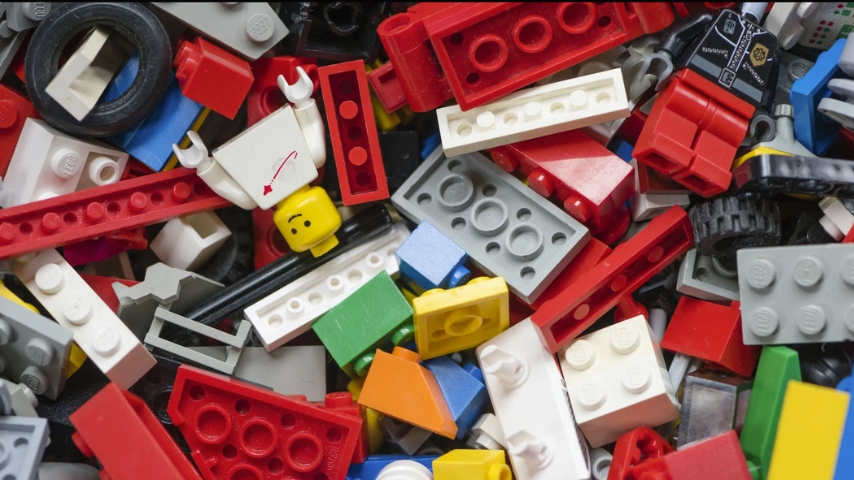
At the end of the day, conflict resolution isn’t about winning an argument or avoiding one. It’s about learning to work better together, even when it’s difficult to do.
Jerry Guerra is an independent writer in Lynnfield, Mass.
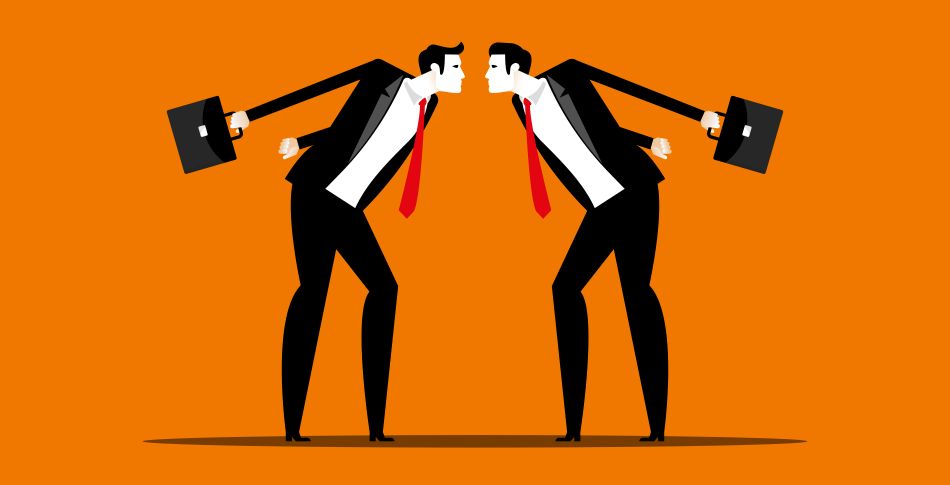
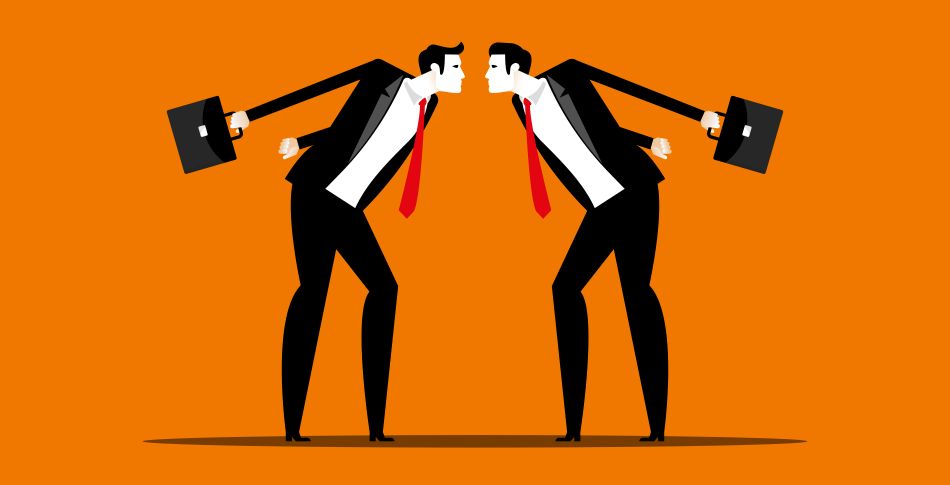