5 Engineering Innovations that Helped Win WWII
5 Engineering Innovations that Helped Win WWII
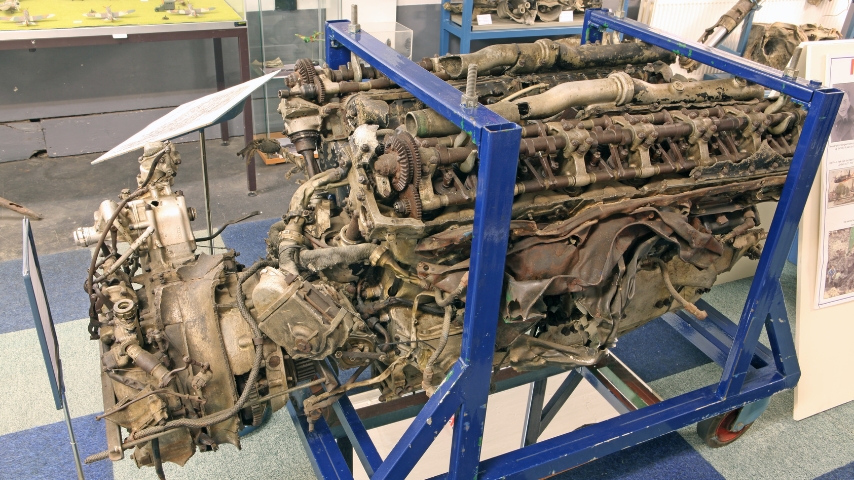
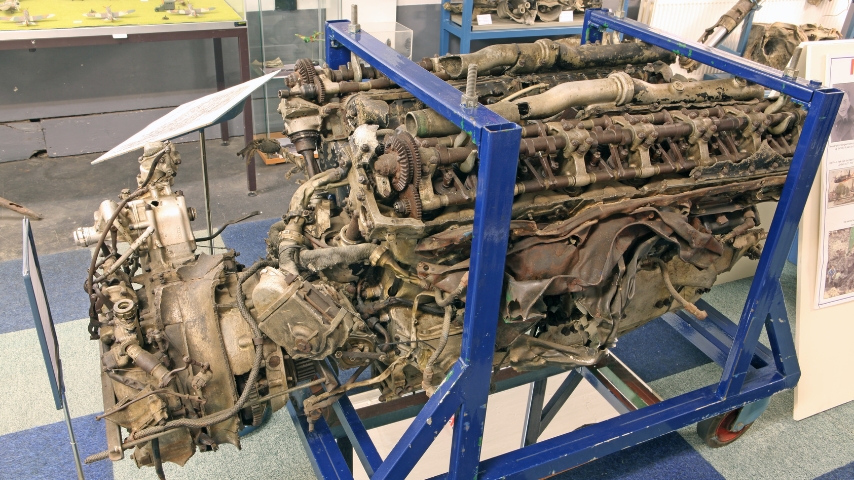
The sheer number of ships and planes that WWII manufacturers produced lead the headlines, but the stories of smaller engineering innovations may actually have tipped the scales toward an Allie win.
The role that engineers played in the Allies’ victory of World War II (WWII) can never be overstated. Much of the fame goes to the number of ships, planes, and other vehicles manufactures produced. And while producing three ships each day with an average time to build them of 42 days nationally and two weeks at Kaiser shipyards, the ultimate story, as it always is, can be found in the details.
With the attack on Pearl Harbor on December 7, 1941, the United States was quickly rushed into war. Getting battle-ready meant a quick ramp up of production especially since the war raged across land, air, and water. Bourne out of necessity, mechanical engineers and others developed machines and equipment involving innovative solutions.
Here are five amazing innovations of the bombers, tanks, and more of the Second World War.
Historians argue that the Rolls-Royce Merlin was the most important WWII engine. This series of 12-cylinder, 60° “V”, 27 L, liquid cooled piston aircraft engines powered both the P-51 Mustang and Spitfire. Manufacturers also used it in tanks, giving the British a powerful and reliable war machine.
Work started on the engine design that would eventually become the Merlin in the early 1930s, after Rolls-Royce leadership realized their successful 21 L 700 hp Kestrel V12 wouldn’t continue to get the job done. The upgraded design, the PV-12, would produce 1,100 hp. It was realized in 1933 and would first fly in a Hawker Hart in 1935.
Next, engineers designed the Supermarine Spitfire and Hawker Hurricane to accommodate the PV-12. With production of both these aircraft awarded in 1936, the PV-12 was also given the green light for large-scale production. It would be named the Merlin, following Roll-Royce’s tradition of naming its engines after birds of prey. The engine was eventually used in 40 different kinds of aircraft.
World War I tanks had a major problem. Their conventional leaf spring suspension systems were limited. The major problem developers faced was the limited vertical space needed for the spring and strut design. For example, for a 25 cm movement they needed up to 75 cm of vertical space.
In the late 1920s J. Walter Christie, an American engineer, introduced the Christie Suspension by adding a bell crank which changed the direction of motion from vertical to horizontal. Moreover, he decided to mount the road wheels individually on a pipe that could move vertically only, at the top of which the bell crank rotated. Springs were mounted on the end of the crank, and could be as long as needed, lying along the inside of the hull. The result was a substantial increase in range of motion.
Another feature of Christie’s designs was the “convertible” drive: the ability to remove the tracks for road travel, allowing for higher speeds and better range, and reducing wear on the track systems. In one public test in 1931 in Linden, N.J., Army officials clocked a Christie M1931 tank and declared it the fastest tank in the world. Genuine Christie suspension systems were used only on a few armed forces vehicles, notably the Soviet BT tanks and T-34, the British Cruiser tanks, including the A13s: Cruiser Mk III, Cruiser Mk IV, Covenanter, Crusader, Cromwell, and the Comet, as well as some experimental designs in Poland and Italy.
A major problem that bomber missions faced, especially during the winter months, was bad weather over England and Europe. To solve the problem, during the aerial war against Germany, the Royal Air Force developed radio beam and radar.
Engineers at Massachusetts Institute of Technology improved this equipment with the H2X Mickey—the AN/APS-15. This device used a rotating antenna within a cupola attached to the belly of a bomber to build up a map of the terrain below. The design allowed for precision bombing and was installed in both the B-17 F and the B-17 G.
The new equipment led to the United States establishing the first United States Army Air Force Pathfinder group stationed in Alconbury, England. In 1943 Major Fred A. Rabo joined the bombardment missions that used the B-17 equipped with the new version of radar. The story goes is when Rabo first saw the hand-built retractable H2X units under the nose of the aircraft he simply said, “that radome looks, Mickey Mouse.”
The nickname stuck and subsequently, it was shortened to “Mickey.” Throughout the remainder of WWII, H2X radar units were commonly referred to as Mickey units and operators were called “Mickey Operators.”
Born just after the automobile was invented, founder of Huck Manufacturing Company, Louis C. Huck, earned a reputation for process improvement and innovation. Known for his Huck Brake (patented in 1926) used in General Motors cars, the carmaker turned to Huck when it looked to improve manufacturing output of Dornier aircraft with its partner Fokker Aircraft.
Production speed was an issue Huck began to look for production bottlenecks. One that he quickly identified was the fastening of the skin of the aircraft to the frame with rivets. This joining process not only required skilled labor, but the process took up to four workers to install one rivet. The process was slow and expensive.
Huck imagined a fastener that was strong enough to withstand the tensile and sheer the airplane would experience but could be installed by a single person from one side of the structure. Even though he never got a chance to bring his innovation to production at Dornier, he never gave up on his idea. He eventually developed a single-sided fastener that could be easily installed with a pneudraulic tool. This Huck structural blind rivet was patented in 1936, and Huck began manufacturing structural blind rivets in 1939.
France may have fallen to Germany before manufacturers could fill that country’s orders for bombers. But the British took its first deliveries, totaling 48 B-24s, in 1941. It may have been the location of Huck’s Detroit factory that got his one-sided structural rivet noticed by the engineers at Ford’s Willow Run plant.
How it happened may have been lost to history, but the Huck blind fastener eventually became a game changer for airplane manufacturing. The first precision-engineered Huck blind rivet was installed on a B-24 Liberator bomber at Willow Run in the summer of 1943 and by the end of that year, they were installed on every B-24 that came off the assembly line.
The Little Ships of Dunkirk were a bit less than 1,000 private boats that sailed from Ramsgate in England to Dunkirk in northern France. The memorable undertaking, immortalized in the 2017 “Dunkirk,” helped rescue more than 336,000 British, French, and other Allied soldiers who would have otherwise perished on the beaches of Dunkirk.
During the evacuation of Dunkirk, codenamed “Operation Dynamo,” the military and others observed that attacking aircraft bullets did not penetrate the boats that were decked with bituminous flooring. In fact, the composite seemed to ensnare the artillery. When examined, the bullets appeared spent, and had arrived at an angle, the deck sheathing pretty much prevented any penetration.
The deck sheathing examined was a form of mastic asphalt, grit added to bitumen and limestone powder. When heated, the soft paste is formed and spread in position. When it cools it hardens. In peacetime the mixture was used mostly for flat roofs, floors, and even road surfacing. It was the work of Britian’s Road Research Laboratory of the Department of Scientific and Industrial Research that came up with “plastic armor” that helped provide an alternative to heavy, often scarce, materials such as concrete and metal.
The final product was a lighter material despite being made up of a packed mass of stone particles held together with bituminous mortar and backed with steel plate. The plastic protective plating (PPA) worked with the stone breaking or turning the bullets so that the metal can stop the slowed projectiles. By the end of 1942 the majority of gun positions were protected by PPP and by May 1943, about 100,000 tons of plastic armor and PPP were being made each year.
Cathy Cecere is membership content program manager.
With the attack on Pearl Harbor on December 7, 1941, the United States was quickly rushed into war. Getting battle-ready meant a quick ramp up of production especially since the war raged across land, air, and water. Bourne out of necessity, mechanical engineers and others developed machines and equipment involving innovative solutions.
Here are five amazing innovations of the bombers, tanks, and more of the Second World War.
Manufacturing the Rolls Royce Merlin
Historians argue that the Rolls-Royce Merlin was the most important WWII engine. This series of 12-cylinder, 60° “V”, 27 L, liquid cooled piston aircraft engines powered both the P-51 Mustang and Spitfire. Manufacturers also used it in tanks, giving the British a powerful and reliable war machine.Work started on the engine design that would eventually become the Merlin in the early 1930s, after Rolls-Royce leadership realized their successful 21 L 700 hp Kestrel V12 wouldn’t continue to get the job done. The upgraded design, the PV-12, would produce 1,100 hp. It was realized in 1933 and would first fly in a Hawker Hart in 1935.
Next, engineers designed the Supermarine Spitfire and Hawker Hurricane to accommodate the PV-12. With production of both these aircraft awarded in 1936, the PV-12 was also given the green light for large-scale production. It would be named the Merlin, following Roll-Royce’s tradition of naming its engines after birds of prey. The engine was eventually used in 40 different kinds of aircraft.
Engineering the Christie Suspension
World War I tanks had a major problem. Their conventional leaf spring suspension systems were limited. The major problem developers faced was the limited vertical space needed for the spring and strut design. For example, for a 25 cm movement they needed up to 75 cm of vertical space.In the late 1920s J. Walter Christie, an American engineer, introduced the Christie Suspension by adding a bell crank which changed the direction of motion from vertical to horizontal. Moreover, he decided to mount the road wheels individually on a pipe that could move vertically only, at the top of which the bell crank rotated. Springs were mounted on the end of the crank, and could be as long as needed, lying along the inside of the hull. The result was a substantial increase in range of motion.
Another feature of Christie’s designs was the “convertible” drive: the ability to remove the tracks for road travel, allowing for higher speeds and better range, and reducing wear on the track systems. In one public test in 1931 in Linden, N.J., Army officials clocked a Christie M1931 tank and declared it the fastest tank in the world. Genuine Christie suspension systems were used only on a few armed forces vehicles, notably the Soviet BT tanks and T-34, the British Cruiser tanks, including the A13s: Cruiser Mk III, Cruiser Mk IV, Covenanter, Crusader, Cromwell, and the Comet, as well as some experimental designs in Poland and Italy.
The H2X Mickey innovation
A major problem that bomber missions faced, especially during the winter months, was bad weather over England and Europe. To solve the problem, during the aerial war against Germany, the Royal Air Force developed radio beam and radar. Engineers at Massachusetts Institute of Technology improved this equipment with the H2X Mickey—the AN/APS-15. This device used a rotating antenna within a cupola attached to the belly of a bomber to build up a map of the terrain below. The design allowed for precision bombing and was installed in both the B-17 F and the B-17 G.
The new equipment led to the United States establishing the first United States Army Air Force Pathfinder group stationed in Alconbury, England. In 1943 Major Fred A. Rabo joined the bombardment missions that used the B-17 equipped with the new version of radar. The story goes is when Rabo first saw the hand-built retractable H2X units under the nose of the aircraft he simply said, “that radome looks, Mickey Mouse.”
The nickname stuck and subsequently, it was shortened to “Mickey.” Throughout the remainder of WWII, H2X radar units were commonly referred to as Mickey units and operators were called “Mickey Operators.”
Huck fasteners of World War II
Born just after the automobile was invented, founder of Huck Manufacturing Company, Louis C. Huck, earned a reputation for process improvement and innovation. Known for his Huck Brake (patented in 1926) used in General Motors cars, the carmaker turned to Huck when it looked to improve manufacturing output of Dornier aircraft with its partner Fokker Aircraft. Production speed was an issue Huck began to look for production bottlenecks. One that he quickly identified was the fastening of the skin of the aircraft to the frame with rivets. This joining process not only required skilled labor, but the process took up to four workers to install one rivet. The process was slow and expensive.
Huck imagined a fastener that was strong enough to withstand the tensile and sheer the airplane would experience but could be installed by a single person from one side of the structure. Even though he never got a chance to bring his innovation to production at Dornier, he never gave up on his idea. He eventually developed a single-sided fastener that could be easily installed with a pneudraulic tool. This Huck structural blind rivet was patented in 1936, and Huck began manufacturing structural blind rivets in 1939.
France may have fallen to Germany before manufacturers could fill that country’s orders for bombers. But the British took its first deliveries, totaling 48 B-24s, in 1941. It may have been the location of Huck’s Detroit factory that got his one-sided structural rivet noticed by the engineers at Ford’s Willow Run plant.
How it happened may have been lost to history, but the Huck blind fastener eventually became a game changer for airplane manufacturing. The first precision-engineered Huck blind rivet was installed on a B-24 Liberator bomber at Willow Run in the summer of 1943 and by the end of that year, they were installed on every B-24 that came off the assembly line.
Engineering Plastic Armor
The Little Ships of Dunkirk were a bit less than 1,000 private boats that sailed from Ramsgate in England to Dunkirk in northern France. The memorable undertaking, immortalized in the 2017 “Dunkirk,” helped rescue more than 336,000 British, French, and other Allied soldiers who would have otherwise perished on the beaches of Dunkirk. During the evacuation of Dunkirk, codenamed “Operation Dynamo,” the military and others observed that attacking aircraft bullets did not penetrate the boats that were decked with bituminous flooring. In fact, the composite seemed to ensnare the artillery. When examined, the bullets appeared spent, and had arrived at an angle, the deck sheathing pretty much prevented any penetration.
The deck sheathing examined was a form of mastic asphalt, grit added to bitumen and limestone powder. When heated, the soft paste is formed and spread in position. When it cools it hardens. In peacetime the mixture was used mostly for flat roofs, floors, and even road surfacing. It was the work of Britian’s Road Research Laboratory of the Department of Scientific and Industrial Research that came up with “plastic armor” that helped provide an alternative to heavy, often scarce, materials such as concrete and metal.
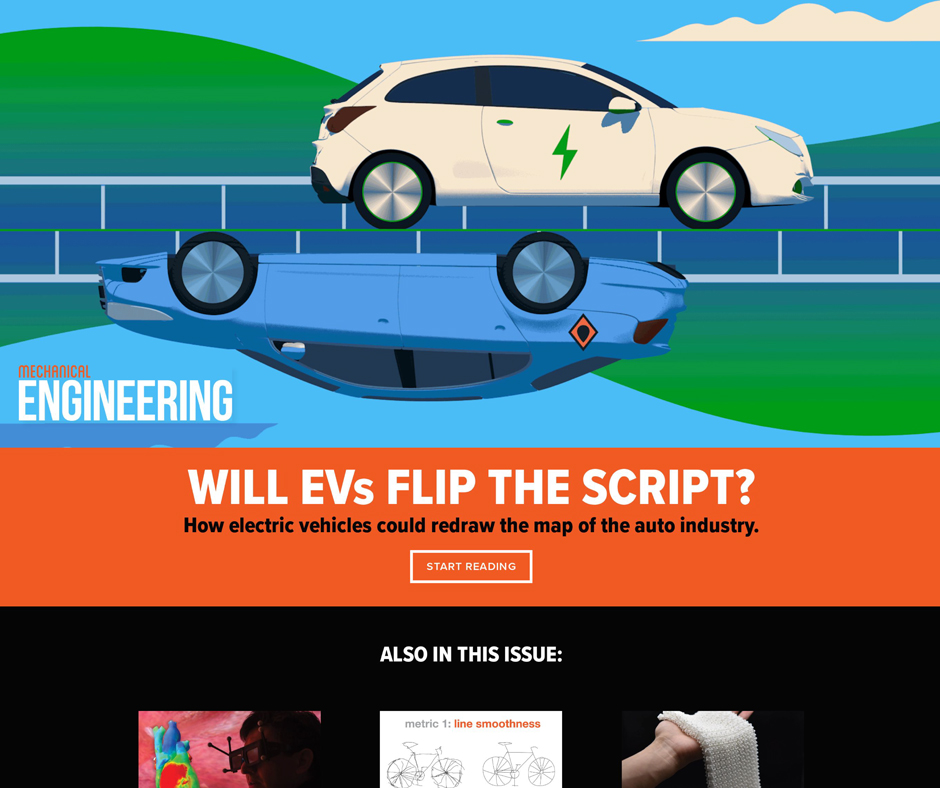
Industry Moves with Electric Shift
By the 1940s, Detroit produced more than half of the world’s vehicles. After car manufacturing took a hit in the 1980s, automakers built new plants in “Auto Alley.” Now, Georgia, Tennessee, and South
Cathy Cecere is membership content program manager.