3D-Printed Sensor Could Serve All of Humanity in Space
3D-Printed Sensor Could Serve All of Humanity in Space
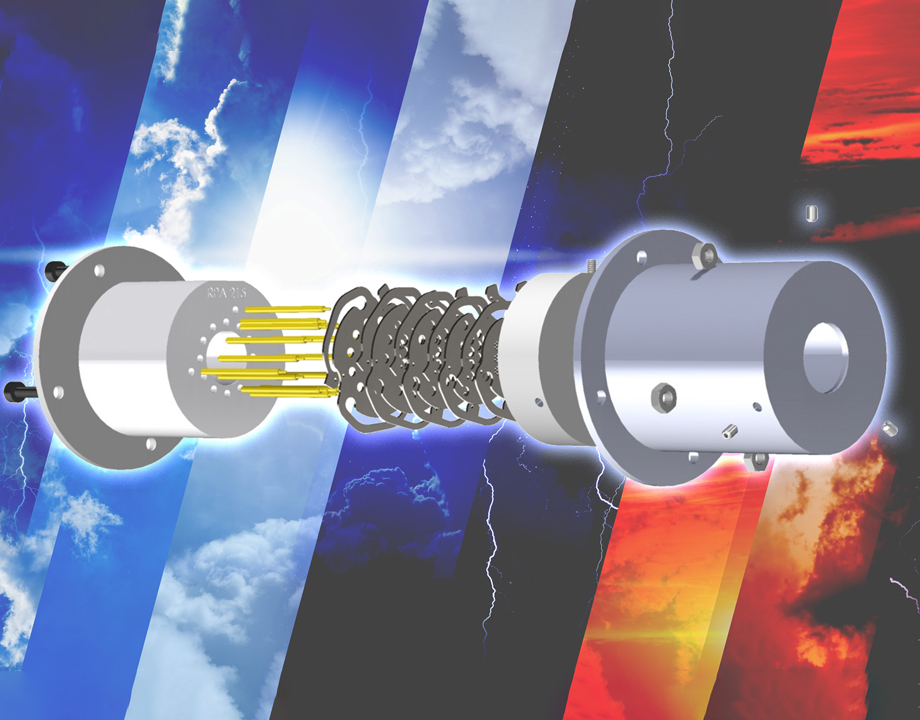
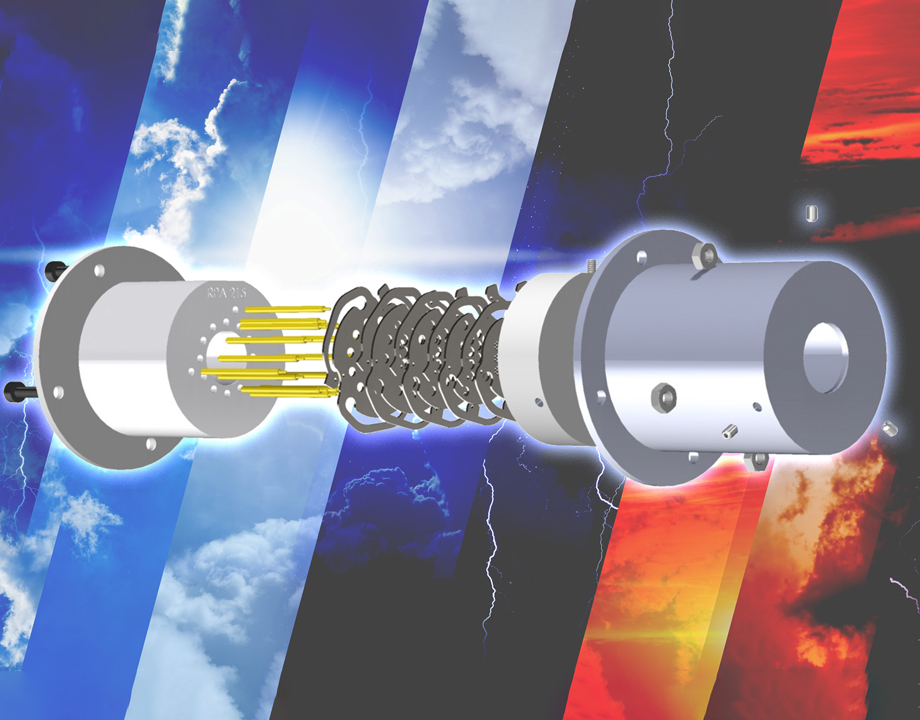
MIT researchers have demonstrated a 3D-printed plasma sensor for orbiting spacecraft that works as well as more expensive, semiconductor sensors. Image: Courtesy of MIT researchers.
The best solution to high shipping prices is to lower the weight of the package and the cost of its contents, especially when shipping can exceed $11,000 per pound.
That was the main concept Luis Fernando Velásquez-García had in mind when his group at MIT’s Microsystems Technology Laboratories set out to develop an inexpensive miniature retarding potential analyzer (RPA), a sensor that can be placed in a mini satellite and used to analyze the composition of plasma gases found in space and other atmospheres. The description and measurements of plasma are important to applications like predicting the weather, analyzing climate change, communications, space travel, supersonic flights, and fusion energy reactors.
“The opportunity here is that the RPAs make it possible at a very low cost to get a better understanding of the problems that affect all of humanity,” Velásquez-García said.
RPAs can measure the electron and ion energy distribution of plasma. The devices typically consist of a series of mesh grids that filter ions, and a collector placed behind the grid stack that detects the ions that go through the electrode stack. The grids and collector must be electrically insulated from each other and the housing.
For the last decade, Velásquez-García’s team of engineers and scientists has used new technologies and methods to produce complex hardware at a fraction of what it once cost. The group’s latest research, recently published in Additive Manufacturing, focuses on 3D-printed RPAs aboard CubeSats, low-powered miniaturized satellites used for low-cost research in low Earth orbit (LEO). They are typically housed in a cube that can measure between 1 to 10 cubic liters and between 2 and 30 pounds.
More on 3D Printing: Racing toward 3D-Printed Electric Motors
“Instead of spending tons of money, you can spend tens of thousands of dollars to launch this little guy into space,” he said. “That would make a tremendous difference. Think of all the different businesses that you can now deploy.”
Payloads aboard LEO flights (the region of space within 1,243 miles of the Earth’s surface) cost roughly $11,650 per pound. Researchers in the past have managed to develop light RPAs for CubeSats, but the sensors are usually manufactured in a cleanroom, an expensive process that takes weeks to fabricate. Most RPAs, according to the researchers, also have unaligned apertures across the grid stack, allowing only a fraction of the ions to pass through the grid. That can cause signal loss and lead to inaccurate measurements due to an effect called space charge. Velásquez-García’s design enforces aperture alignment across the grid stack, maximizing transmission.
“What you want is a device that’s impervious to space charge and transmits as much of the signal as possible,” he said.
In 2015, the Velásquez-García group used silicon microfabrication to build an RPA with a set of deflection springs that helped to better align the grid stack. “It was state of the art, but very expensive and it took a long time to make,” he said. A major problem, however, remained: the thin films used to insulate the electronics could sputter or melt under extreme plasma temperatures.
To solve those problems, the group turned to 3D printing for this project and created the first digitally manufactured RPA, which can be produced for about $10 each in a few days. The process allowed the researchers to build intricate mesh grids with unique laser-cut shapes that aligned perfectly when set inside the housing structure. The team chose to print the structure using Vitrolite, a glass-ceramic material originally called pigmented structural glass when it was first manufactured in 1900. Vitrolite is a great insulator and can withstand temperatures of up to 800° C, while the polymers used in microfabricated RPAs can start to melt at 400° C.
Editor's Pick: 3D-Printed Lattices Optimize Strength-to-Weight Ratios
The next round of research will focus on printing additional parts in metal.
“For this research, we wanted to simplify things and focus on the most important parts, the ceramic parts,” Velásquez-García said. “In the end, we show that we have a very capable sensor. With the current manufacturing limitations, we’re able to be state of the art. But when we get better manufacturing methods, it will be even better and more precise.”
Jeff O’Heir is a science and technology writer in Huntington, N.Y.
That was the main concept Luis Fernando Velásquez-García had in mind when his group at MIT’s Microsystems Technology Laboratories set out to develop an inexpensive miniature retarding potential analyzer (RPA), a sensor that can be placed in a mini satellite and used to analyze the composition of plasma gases found in space and other atmospheres. The description and measurements of plasma are important to applications like predicting the weather, analyzing climate change, communications, space travel, supersonic flights, and fusion energy reactors.
“The opportunity here is that the RPAs make it possible at a very low cost to get a better understanding of the problems that affect all of humanity,” Velásquez-García said.
RPAs can measure the electron and ion energy distribution of plasma. The devices typically consist of a series of mesh grids that filter ions, and a collector placed behind the grid stack that detects the ions that go through the electrode stack. The grids and collector must be electrically insulated from each other and the housing.
For the last decade, Velásquez-García’s team of engineers and scientists has used new technologies and methods to produce complex hardware at a fraction of what it once cost. The group’s latest research, recently published in Additive Manufacturing, focuses on 3D-printed RPAs aboard CubeSats, low-powered miniaturized satellites used for low-cost research in low Earth orbit (LEO). They are typically housed in a cube that can measure between 1 to 10 cubic liters and between 2 and 30 pounds.
More on 3D Printing: Racing toward 3D-Printed Electric Motors
“Instead of spending tons of money, you can spend tens of thousands of dollars to launch this little guy into space,” he said. “That would make a tremendous difference. Think of all the different businesses that you can now deploy.”
Payloads aboard LEO flights (the region of space within 1,243 miles of the Earth’s surface) cost roughly $11,650 per pound. Researchers in the past have managed to develop light RPAs for CubeSats, but the sensors are usually manufactured in a cleanroom, an expensive process that takes weeks to fabricate. Most RPAs, according to the researchers, also have unaligned apertures across the grid stack, allowing only a fraction of the ions to pass through the grid. That can cause signal loss and lead to inaccurate measurements due to an effect called space charge. Velásquez-García’s design enforces aperture alignment across the grid stack, maximizing transmission.
“What you want is a device that’s impervious to space charge and transmits as much of the signal as possible,” he said.
In 2015, the Velásquez-García group used silicon microfabrication to build an RPA with a set of deflection springs that helped to better align the grid stack. “It was state of the art, but very expensive and it took a long time to make,” he said. A major problem, however, remained: the thin films used to insulate the electronics could sputter or melt under extreme plasma temperatures.
To solve those problems, the group turned to 3D printing for this project and created the first digitally manufactured RPA, which can be produced for about $10 each in a few days. The process allowed the researchers to build intricate mesh grids with unique laser-cut shapes that aligned perfectly when set inside the housing structure. The team chose to print the structure using Vitrolite, a glass-ceramic material originally called pigmented structural glass when it was first manufactured in 1900. Vitrolite is a great insulator and can withstand temperatures of up to 800° C, while the polymers used in microfabricated RPAs can start to melt at 400° C.
Editor's Pick: 3D-Printed Lattices Optimize Strength-to-Weight Ratios
The next round of research will focus on printing additional parts in metal.
“For this research, we wanted to simplify things and focus on the most important parts, the ceramic parts,” Velásquez-García said. “In the end, we show that we have a very capable sensor. With the current manufacturing limitations, we’re able to be state of the art. But when we get better manufacturing methods, it will be even better and more precise.”
Jeff O’Heir is a science and technology writer in Huntington, N.Y.