Researcher Focus: Advanced Materials
Researcher Focus: Advanced Materials
Interview conducted by Paul Glanville
Kashif Nawaz, a Research Assistant at the University of Illinois at Urbana-Champaign talks about Silica Aerogels and Metallic Foams for Humidity Control in Energy-Efficient Buildings
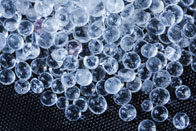
Learn more about this research through the 2013 ASME Congress Proceedings: Effect of Catalyst Used in the Sol-Gel Process on the Microstructure and Adsorption/Desorption Performance of Silica Aerogels.
Tell us about your research on silica aerogels…
The idea is to use the silica aerogels as desiccant for dehumidification applications. There are a number of desiccants available and silica aerogels are one of them.
Silica aerogel’s have been in the industry and they are using them for insulators, because they are really bad conductors of heat transfer. They are using the cryogenic doors and there are some other applications for these materials.
But nobody has really looked at the manufacturing process. This is in fact one part of my research, and what we have done here is to look at the recipe to find out, “what are the different ingredients” and “what’s their role” in determining the final microstructure of the aerogel.
There are three main ingredients; a catalyst, a solvent, and then a precipitator. We conducted a study to see the affect of these three different ingredients. It turned out that the catalyst is probably the most important one, it affects the structure a lot. Normally we use acid catalyst or basic catalysts, and I used a variety of catalysts. In fact, I made an aerogel sample of about 72 aerogel samples using different recipes, but it turned out that when I was preparing the catalyst the microstructure varied from very small, highly porous structure to relatively large pores.
Then because we are interested in using them for the dehumidification application, it’s important to know what the mass transfer characteristics of these materials are. In order to determine the diffusion coefficients we came up with an instrument and automated method. You have to expose your sample to a certain humidity and then you have to wait until the equilibrium is reached.
But when you use the dynamic reabsorption apparatus, which we used, you can actually see the complete process within a few days. And then you can essentially use some kind of modeling to come up with the diffusion coefficient.
For all different types of samples we determined the diffusion coefficient using the dynamic reabsorption technique, and it turned out that the different silica aerogel’s prepared by different catalysts they have different diffusion coefficients, and sometimes it was a difference of order of magnitude. It shows that essentially if you really want to use the silica aerogel’s for a dehumidification application, as a desiccant, you need to use the right recipe. You need to have the right kind of ingredients.
This paper is essentially determining the effective diffusion coefficients for silica aerogel’s and somehow relating it to the recipe which you are using to manufacture them.
Essentially the next step of this research was coating the silica aerogel’s on the metal foams. Previously we conducted a study to determine empirical performance of the metal foams as a heat exchanger.
I have some research experience using those as burners. Well, they are really interesting materials and we got really promising results. In fact, in comparison to the state-of-the-art heat exchanger design - when you use a metal form and you compare the performance you can get up to 150, 200 percent increase in the heat transfer rate with a slight, mild increase in pressure drop, but essentially you can vary the geometry and you can get the desired performance.
The idea of combining these two research programs was to come up with a device which consists of aerogel coated metal foams, and then you can use the device as a mass exchanger, to absorb the moisture. These kinds of devices which will be really compact, and we have been working on some kind of prototype. We have already conducted some modeling of aerogel coated metal forms. They can replace some of the desiccants used for the dehumidification applications, and essentially you will be saving a lot in terms of volume, and the efficiency of mass transfer will be really high.
To let you know why we have chosen the metal foams as a substrate for these silica aerogel’s, they are a very low thermal conductor - they are good insulators. So the metal foams they have a very large surface area to volume ratio. It can go up to 900 to 2,800 meters square per meter cubed depending upon what kind of porosity of the metal foam you are using. They are available in standard, like five pores per inch, 10 pores per inch, 20 pores per inch and 40 pores per inch.
When you have such a large surface area essentially you can have a very thin layer of silica aerogel on the metal foam, 200 microns or 300 microns. The effect of the bad insulator, or being a bad conductor, that effect is diminished when you have a very thin layer. And when you have the substrate - another reason for using the substrate is you basically want to take over the heat of absorption by the coolant flowing through the tubes of the mass exchanger. When you have a very thin layer essentially you can take away the heat of absorption through the coolant flowing through the tubes of the mass exchanger, and when you want to desorb - get rid of the humidity, you can provide the hot fluid on the tube side and it will essentially provide the heat of desorption, it will remove the moisture.
Essentially it’s a cycle, it’s a cyclic process. More like frosting and defrosting in a heat exchanger, you know heat pumps, where you have about one hour of frosting and then you can have a cycle of defrosting for about 15 minutes. And the other reason for which we think that this will work is the diffusion coefficient of absorption is that we found that the heat of the diffusion coefficient under absorption is different than desorption. In fact, when you are desorbing the diffusion coefficient is approximately two times higher than absorption, which happened because of the microstructure change.
And this is really good because essentially for having a larger desorption diffusion coefficient over desorption you can get rid of the moisture which was absorbed on the silica aerogel rather quickly. If you have a device which has a certain type of metal foam, and you have a 100 micron layer of silica aerogel, your absorption time for the 90 percent saturation would be about 45 to 50 minutes. And then because of the better desorption coefficient, mass diffusion coefficient, you can get rid of all that absorbed humidity within 5 to 10 minutes.
It’s more like a frosting/defrosting process, but essentially the idea is that you can have your dehumidifying device really compact, and it has the potential to replace some of the existing technologies.
Do you have a sense for how this technology, aerogel onto a metal foam or just on its own, is going to be utilized in a dehumidification system or something different than that?
When working as a member of the Air-Conditioning and Refrigeration Center we are more interested in the practical side of research. We had this issue, where I had a discussion with many of the sponsors, from industry, who are sponsoring this project, they questioned how suitable, or in terms of economics, how viable this idea is, to have this kind of device.
Right now there are some issues, mainly because of the cost of the metal foams, because they are really expensive. Actually, there are only a few manufacturers in the US, or even in the world, but there are only two or three major manufacturers. They are more like a monopoly so they can always sell at their own price. But once the use of this kind of material is more common, essentially, we’re talking about 10 years from now, I am quite sure that the price for the metal foam will go down and we will be able to sort of beat the criteria in terms of economics as well.
But right now for specialized applications, the wait is really a critical issue. These things are definitely a better option than the existing technologies. I’m quite hopeful that this technology has some potential.
Your field of research relates to energy and that’s one of ASME’s three strategic areas in the HVAC/humidity control side of things. Are there ways in which you feel that you tailored your work towards ASME’s goals or is it just a happy coincidence? Well essentially - my project is related to energy efficiency, and we are building devices that can work to save energy. We want to perform the same sort of work at the minimum cost in terms of energy fuel. I am also kind of interested in renewable energy. I’m quite near the completion of my Masters in nuclear engineering.
Reading conference papers and attending ASME conferences, has helped me to tailor my ideas. If I want to do some kind of contribution in the renewable area, where should I go? But, I think my work relates to both. I’m also looking at the broader prospect of when you have really the big renewable energy projects such as wind energy or solar energy.
What has it been like becoming the engineer that you are right now?
Well to be honest after my high school, I thought that when you are essentially in a specific area, let’s say if you are an electrical engineer, or you are a mechanical engineer, your area of focus will be just limited to that specific divisions. But it turned out that things can go much beyond that.
And when you talk about mechanical engineering and ASME is not like somehow exclusive to mechanical engineers. Essentially, ASME has helped me to realize that in order to come up with some kind of fabrication you need to know more than the mechanical engineering, hard-core mechanical engineering.
On my own research, well it’s essentially a dehumidifying application. I started the analysis of these devices, which is essentially a role of mechanical engineering, but I also did some material characterization. When I was preparing the samples, mine was more like a chemist, you know I was dealing with different catalysts. And when I was studying the material imagery of these materials it was more like a material scientist.
What sort of advice would you give to early career engineers in terms of using ASME, or other avenues for mentoring, or finding ways to get involved? You have to essentially get involved. Working on your own [independently] there’s a good chance that you might get stuck, or you might develop a habit of going in a specific direction. But when you interact with people and you go to the organizations like ASME, ASHRAE, you broaden your knowledge about the research. You can get a broader view of the different technical skills, the people involved, that’s a very important.
There are different ways to tackle the same problem. You can actually talk to the people, you let them know about your research, you learn about their research, you get a broader idea of the research even if you’re talking about the same specific area.
Research Assistant, Kashif Nawaz has published papers on The ASME Digital Collection, including the following from the 2013 ASME Congress Proceedings (IMECE2013): Effect of Catalyst Used in the Sol-Gel Process on the Microstructure and Adsorption/Desorption Performance of Silica Aerogels.