Automation of Production Optimization
Automation of Production Optimization
An opportunity for future engineers by Frederick M Proctor, NIST and Ritesh Lakhkar, Senior Development Engineer, Corning Incorporated
Over the past 5-10 years, manufacturing has evolved to be very highly automated, at least for the routine tasks, making the benefits of countries with low manual labor costs less significant for manufacturing. There has been a much higher integration of information throughout manufacturing enterprises due to the Internet, i.e., "shop floor to top floor" connectivity. The future is hard to predict, but the phrase "agile manufacturing" has persisted, and this is where automation of the non-routine tasks will be very important.
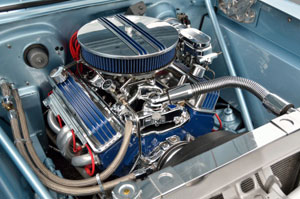
In the years to come manufacturing will be highly diverse, highly automated, with less emphasis on mass production of identical items, and more customization of the product. This is referred to as "mass customization," supported by "reconfigurable manufacturing". Automobile production is a good example: think of a line where every car is different in some way (color, trim, options), decisions on when to make which car are made as late as possible, perhaps on the day the car is ordered, and where automation of difficult tasks (assembly of flexible material in unconstrained environments) means that people will no longer be working directly on the product, but will be called on to provide experience and expertise solving more difficult problems. There are many good reports on this subject, covering a much wider swath of manufacturing. The question remains, what can enable mass customization and agile innovation processes?
In the manufacturing environment there is and will be a constant need for monitoring the current processes and make changes to them to increase efficiency, reduce cost and optimization. Much of the information needed to optimize production today is manually collected by people on the shop floor, who are otherwise occupied with the production itself. It's tedious, time consuming, and error prone. The sources of this information vary greatly, and include lots of legacy equipment possibly decades old that don't have modern network interfaces that could help automate the data collection. There is a big need to bring all this equipment and sensors into a common networked environment so that optimization applications can work on good data.
Production optimization is using information from sensors and equipment to understand current conditions in a factory or facility, and applying models to determine how to adapt future actions to reduce time and cost to make the product. It is one of the critical components for mass customization and agile innovation.
The concept of production optimization is being applied across a broad range of manufacturing activities – discrete parts production such as aerospace and automotive, continuous processes like oil refineries and chemical plants, and batch production for food and medicine. Mostly it's being done by larger companies, and small to medium enterprises (SMEs) with small lot sizes can't spend the time to optimize these small lots. If it were easier and automated, there could be big improvements in these SMEs and thus enable mass customization and agile innovation.
A research group led by Frederick M. Proctor at NIST has been working on 'Automation of Production Optimization' in association with his colleagues John Michaloski at NIST, Jorge Arinez at General Motors and Jonatan Berglund at Chalmers University of Technology, Sweden. Mr. Proctor is the Group Leader of the Networked Control Systems group at the U.S. National Institute of Standards and Technology (NIST) in Gaithersburg, Maryland, and manages the Smart Manufacturing Control Systems Program of NIST's Engineering Laboratory.
A case study on automating the data collection used to drive a discrete event simulation (DES) application for modeling and improving automotive engine block casting lines was covered in the ASME 2013 IMECE paper presented by Mr. Proctor. DES applications are widely used to answer “what if” questions on throughput, cycle times, energy costs, and other key performance indicators that vary when equipment is placed in different configurations, or used at different times. The problem is that much of the data that is used to set up DES studies is manually collected. This takes time and is prone to errors, and these errors may contribute to faulty conclusions. It’s important to make it as easy and accurate as possible to collect data for DES, because bad data can lead to bad decisions.
According to Mr. Proctor, at NIST, his group is looking at two aspects of production optimization scenario that could be greatly improved with automation. The first concerns the data collection. Depending on the vintage of the sensors and equipment in a facility, and the degree of network connectivity, this can be a completely manual process where people walk around with clipboards and stopwatches, and observe and record the activities in the facility over long periods of time, often months. Even when the equipment is networked, the communication may be done using proprietary protocols or information models that differ between vendors. Automating this data collections means point-to-point software applications that are not portable, and need to be written for each new type of equipment that comes in. Happily, standards for automating this data collection are available and getting better. One that his group has looked at is MTConnect, from the Association for Manufacturing Technology (AMT), an open, royalty-free standard that defines a wide range of information that is encountered on the factory floor. MTConnect-enabled equipment such as machine tools and robots serve up real-time status information, and client applications will run with any mix of vendor equipment that supports MTConnect.
The second aspect that can be automated relates to the DES application itself, and the need to share information between modeling, simulation, and analysis activities. Here Mr. Proctor's group looked at the Core Manufacturing Simulation Data (CMSD) standard for representing typical DES parameters like mean time between failure (MTBF), mean time to repair (MTTR), cycle time, throughput, and other information commonly encountered in manufacturing operations. Using CMSD, it is possible to automate the exchange of this information, rather than having people assist in point-to-point translations.
For people who are interested in participating in this type of research work or adapting this work in the industry, Mr. Proctor suggests that domain knowledge of the particular production application is certainly required; for example, when optimizing oil refinery activities, one would be expected to have skills in petroleum engineering. As is true for many engineering activities today, a good grasp of modern networked computing is needed: how to hook up computers and devices to wired and wireless networks, how to analyze files of computer data, and to some extent how to write computer applications. The effort can involve students, early career engineers, and late career engineers. The idea of automating data collection is simple, and indeed, many early career engineers get job training by doing this sort of ad hoc data collection that gets them exposure to the company's production details. Young engineers also have experience and familiarity with computers, networks, and moving information around in different formats, so they are a good fit for the problem. Late career engineers presumably know all the ins and outs of production, and can be indispensable when deciding what information to collect, how to analyze it, and how to interpret the results.
Engineering or computer science degrees are typical for people working in this area. Engineering degrees would include mechanical, electrical, or industrial engineering. Some background in a manufacturing environment is helpful. Bachelor's degrees are sufficient, but many people pursue a Master's degree while employed, with a thesis covering a particular practical application.
People from diverse backgrounds participated in this research work on production optimization at NIST that was presented at 2013 ASME IMECE. One was a high-volume production end user in the automotive industry, General Motors, and plant personnel who were able to conduct tests, collect data, and provide sanity checks on analyses. Mr. Proctor's group partnered with Chalmers University in Sweden, who is doing research on discrete event simulation and optimization algorithms. NIST, a measurement and standards organization helped define the tests, and determined what changes were needed to CMSD as a result. The ideal project involves a mix of a good end user who can articulate requirements and who will directly benefit from the results, a research organization who can develop new technology to solve the problem, and vendors who will ultimately deliver products that the end user will buy to get the benefits.
In order to facilitate implementation of new technologies such as production optimization techniques, early career engineers should cultivate relationships with the later-career engineers who have a lot of practical experience, and who will need to be sold on the value of new technologies. The problem to be solved, and the solution to do it, both need buy-in from established engineers for a new technology roll-out to be successful. It is also important to manage expectations and not over-sell new technology.
For successful and deployable new technology solutions, academia and research community need to hear from industry on what problem they need solved, what the time frame is, what the environment is in which the technology has to work, any requirements for compatibility with legacy systems, and what sort of continued engineering support and training will be required once the technology is in place. Graduate students and early career engineers have a much more current view of what technology is available, and can provide unique and innovative solutions or use cases that established manufacturing engineers may overlook.
For future or early career engineers with keen interest in connected networks, automation, industrial and mechanical engineering, ideas such as automated production optimization can definitely help in developing solutions for the modern age 21st century agile manufacturing.
NIST has several programs for students ranging from summer internships to post-doctoral research positions. Undergraduate students can apply for the Summer Undergraduate Research Fellowship (SURF) program, a NIST/National Science Foundation partnership that teams outstanding undergraduate students with NIST mentors on cutting-edge research projects; SURF-Boulder and SURF-Gaithersburg. NIST also sponsors grants to universities, through an annual call for proposals that is published through grants.gov. NIST collaborates with industry quite a lot. Typically NIST involves industry so that NIST understands industry requirements, the constraints on deployment, and how to measure the benefits to their organization. NIST works with academia to develop the new technology, and with third-party technology providers who can commercialize the resulting work.