Additive Manufacturing with In Situ Resource Utilization on Extra-Terrestrial Bodies
Additive Manufacturing with In Situ Resource Utilization on Extra-Terrestrial Bodies
2018 Arthur L. Williston Medal Winning Paper Abstract
By Noah M. Purdy
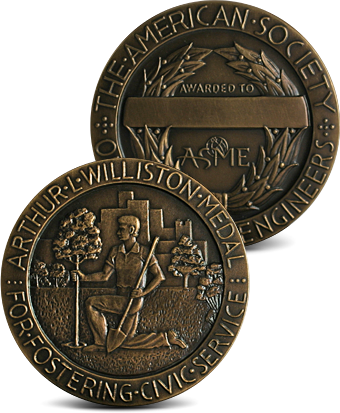
Crewed exploration of space is moving beyond low Earth orbit towards the exploration of the Moon, Mars and beyond 1. However, space exploration is expensive, especially deep space missions. Despite dropping launch costs and the introduction of reusable boosters, transporting massive, bulky supplies and equipment to the Moon, Mars, or beyond is a huge obstacle to the future of spaceflight. One way to bridge this obstacle is In Situ Resource Utilization (ISRU), which makes use of material already at or near the destination to reduce the amount of material and supplies that need to be taken from Earth. Additive Manufacturing (AM) is a likely way in which in situ resources will be used. By looking at current academic research and industrial development, this paper explores how additive manufacturing using in situ resources may be the key to unlocking the next stage of human space exploration.
In theory, ISRU is simple enough, instead of bringing supplies with you to your destination, use what is already there. But when it comes time to determine the logistics and technical details, it can quickly turn into a complex challenge. Therefore, the simplest ISRU systems should be the first to be employed. These will likely harvest water and fuel by collecting regolith with a rover and heating it to extract the water, which can then be converted to hydrogen, oxygen, and even Methane 2,3. However, for long term exploration, more complex ISRU systems must be developed, to allow for the construction of infrastructure, such as habitats, solar collection, greenhouses, vehicles, and workstations. These structures are made up of many different materials, so for an extra-terrestrial manufacturing system to be practical, it would need to produce components in a wide range of materials for various applications. The best technique that allows for the efficient manufacturing of components from a wide range of materials is Additive Manufacturing (AM), also known as 3D printing, where components are constructed layer by layer. Of the seven main types of AM, Powder Bed Fusion (PBF) and Material Extrusion (ME) appear to be the best methods for use on extra-terrestrial bodies 4.
PBF consists of a focused energy beam that selectively heats up areas of a thin layer of powered material, to either melt, fuse, or sinter the material together. It can use a very wide range of materials, including plastics, metals, and some ceramics. Precision and surface finish are dependent on layer thickness, energy beam thickness, and energy beam accuracy, but generally very detailed parts can be produced, with respectable material properties and a fine surface finish 5. In extra-terrestrial environments, there are several potential materials that could be used with PBF. One of the simplest is to use the Lunar or Martian regolith itself with no modification 6. For more detailed components, metals such as aluminum and iron could be used, as they could be refined out of the regolith on both the Moon and Mars 7.
The second method of AM that has potential is ME, which consists of a gantry mounted nozzle that extrudes material to create each layer. It can function with most materials that are softened when heated, such as thermoplastics, or any fluid material that cures or hardens over time, such as concrete. A potential material for ME manufacturing on Mars is polyethylene, either in the form of high density polyethylene (HDPE) or low-density polyethylene (LDPE), which can be produced from carbon dioxide on the Marian surface using the Sabatier and the modified Fischer-Tropsch reactions 8. Lunar and Martian regolith might also be able to be used directly as a building material for ME, with the addition of a binding agent 9.
A potential problem with relying on additive manufacturing for a significant portion of the infrastructure of an extra-terrestrial mission is the long cycle times. Even with the fastest AM techniques, printing a significant quantity of material could take a significant portion of the 12 to 18-month duration of a mission 10. In addition to this, if the infrastructure is intended to be built prior to crew arrival, it must operate independent of humans. However, most current or proposed AM architectures are based around a human user. To truly develop useful AM technology on extra-terrestrial bodies, full automation is necessary to both increase efficiency and to allow the fabrication of components in the absence of humans.
There are several companies currently pursuing Earth-bound automated AM systems. Voodoo manufacturing, which operates over 160 off the shelf, ME desktop 3D printers, has recently begun the task of automating some of their processes, with the desire to eventually automate their whole factory 11. They purchased and integrated a robotic arm to reduce human bottlenecks, which increased productivity threefold 12. Another company, Formlabs is working on a similar setup, but taking it a step further. They are creating an automated work cell that consists of five, off the shelf, desktop 3D printers, a robotic gantry manipulator, and a post-processing station, which promises to produce finished parts with no human interaction13. NextgenAM Project, a joint venture between AEROTEC, EOS, and Daimler AG, are taking a slightly different approach. Instead of trying to automate an AM machine designed for human operators, they are working to integrate the automation and AM into one system14. While Voodoo Manufacturing and Formlabs are focused on ME AM processes, designed to mass produce plastic components, NextgenAM is looking to produce anywhere from single prototypes to medium batches of PBF metal alloy parts. To create an effective AM system on an extra-terrestrial body, both methods should be included, ME for plastics and polymers as well as PBF for metal alloys.
References:
Additive Manufacturing Research Group, Loughborough University. (2018).
Powder Bed Fusion
Retrieved 28 February 2018,
From http://www.lboro.ac.uk/research/amrg/ about/the7categoriesofadditivemanufacturing/powderbedfusion/
Bibring, J., Langevin, Y., Poulet, F., Gendrin, A., Gondet, B., & Berth é, M. et al. (2004).
Perennial water ice identified in the south polar cap of Mars. Nature, 428(6983), 627-630.
http://dx.doi.org/10.1038/nature02461
Deckers, J., Vleugels, J., & Kruth, J. (2014).
Additive Manufacturing of Ceramics: A Review. Journal Of Ceramic Science And Technology, 5(4), 245-256.
EOS 400-4: Ultra-fast quad-laser system for industrial 3D printing. (2018).
Eos.info.
Retrieved 27 February 2018,
From http://www.eos.info/systems_solutions/eos-m-400-4
Feldman, W., Maurice, S., Lawrence, D., Little, R., Lawson, S., & Gasnault, O. et al. (2001).
Evidence for water ice near the lunar poles.
Journal Of Geophysical Research: Planets, 106(E10), 23231-23251.
http://dx.doi.org/10.1029/2000je001444
Flynn, M., & Rosenberg, S. (2005).
In Situ Production of High Density Polyethylene and Other Useful Materials on Mars. SAE Technical Papers, 1.
https://doi.org/10.4271/2005-01-2776
Formlabs. (2018).
Form Cell: Automated 3D Printing Solutions.
Retrieved 24 February 2018,
From https://formlabs.com/3d-printers/form-cell/
Goulas, A., Binner, J., Harris, R., & Friel, R. (2017).
Assessing extraterrestrial regolith material simulants for in-situ resource utilisation based 3D printing. Applied Materials Today, 6, 54-61.
http://dx.doi.org/10.1016/j.apmt.2016.11.004
Goulas, A., & Friel, R. (2016).
3D printing with Moondust. Rapid Prototyping Journal, 22(6), 864-870.
http://dx.doi.org/10.1108/rpj-02-2015-0022
Jakus, A., Koube, K., Geisendorfer, N., & Shah, R. (2017).
Robust and Elastic Lunar and Martian Structures from 3D-Printed Regolith Inks. Scientific Reports, 7, 44931.
http://dx.doi.org/10.1038/srep44931
Schwartz, J. (2017).
How We’re Building a Robotic 3D Printing Factory. The Voodoo Manufacturing Blog.
Retrieved 25 February 2018
From http://blog.voodoomfg.com/2017/03/17/building-a-robotic-3d-printing-factory/
Sanders, J. (2016).
Johnson Space Center Engineering Directorate L-8: In-Situ Resource Utilization (ISRU) Capabilities.
National Aeronautics and Space Administration.
Retrieved from https://www.nasa.gov/sites/default/files/atoms/files/scp07-sanders_isru.pdf
Saunders, S. (2017).
Collaborative NextGenAM Project Aims to Speed Up Automation of the Industrial 3D Printing Process. 3DPrint.com.
Retrieved 25 February 2018,
From https://3dprint.com/171727/nextgenam-automation-project/
Young, J. (2016).
How a NASA Supplier & Thermoplastic Firm’s Material Allow 3D Printing in Space. 3DPrint.com.
Retrieved 25 February 2018,
From https://3dprint.com/158277/green-pe-3d-printing-in-space/