Using Micro 3D Printing for Short-Run Production
Using Micro 3D Printing for Short-Run Production
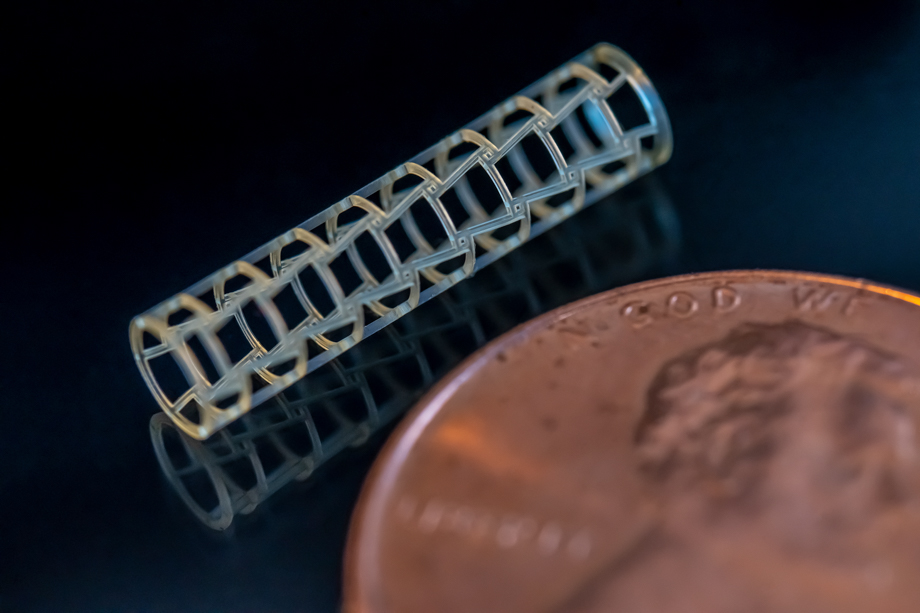
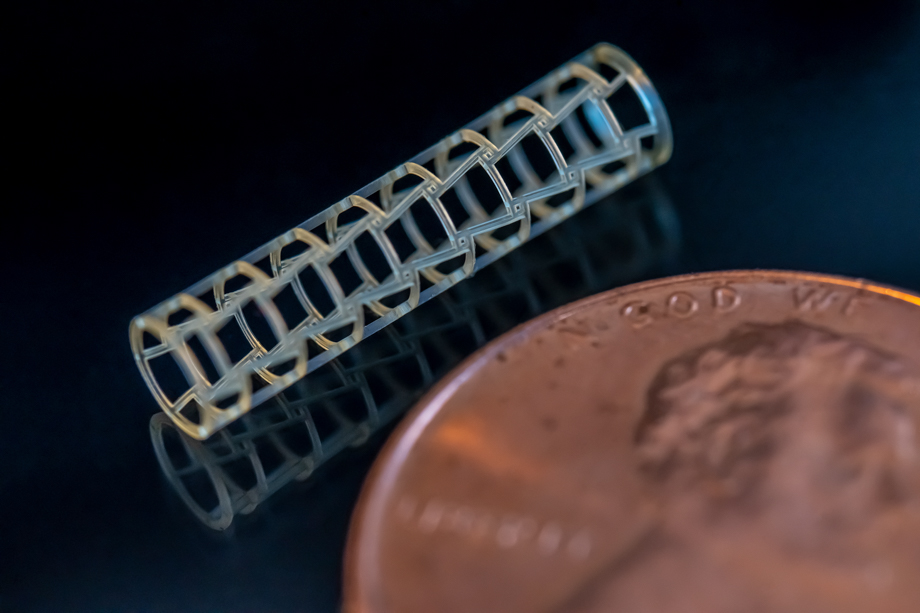
Additive manufacturing processes can make such small parts that it is revolutionizing miniaturization in manufacturing and will expand innovation in product design.
There is considerable R&D focus on how to make parts bigger with additive manufacturing or 3D printing. At the same time, engineers are designing smaller and more complex products, especially in the medical-device and electronics fields. This trend toward miniaturization also requires that the components and assemblies inside these products are also smaller, and often more complex. Smaller parts at the micro-scale are difficult to prototype with conventional manufacturing methods, such as injection molding and CNC machining, and take more time and money.
Now, however, AM technologies have advanced to the point where they can make small, high-resolution parts with incredibly tight tolerances. Led by software and hardware advancements, “micro 3D printing” equipment enables manufacturers to make AM parts that are millimeters in size and smaller, at tolerances in the micron range.
Several AM platforms have been modified to achieve micron-level resolution. These include micro stereolithography, selective laser sintering (for metals), and directed energy deposition. Another variation of stereolithography is multiphoton lithography (MPL), which can have resolutions of up to 50 nanometers, far smaller than can be seen with the naked eye.
A leader in micro 3D printing is Boston Micro Fabrication. Its platforms utilize a proprietary projection micro stereolithography (PµSL) technology, a vat polymerization process that has been upgraded with the latest technologies for control resolution and dimensional accuracy. This allows for rapid photopolymerization of a layer of liquid polymer using a flash of UV light at micro-scale resolution, with a larger build volume (50 x 50 x 50 mm). The printer is compatible with a growing portfolio of engineering and ceramic resins suitable for end-use parts.
Resolution ranges from two microns to 25 microns. “Resolution is the size of the light voxel that is being projected onto the resin bath,” said John Kawola, CEO for Boston Micro Fabrication. “With this size projection, we can typically achieve features such as posts, walls, and holes that are five times the voxel size. So, for a 10-micron system, we can create a 50-micron feature.”
Dimensional tolerance is another consideration. Some industries are more focused on resolution and less on dimensional accuracy. A good example is the jewelry industry. These manufacturers care about very crisp features/edges and surface finish, but they are usually not measuring their product. “In the more industrial applications such as electronics, medical devices, sensors, and microfluidics, product designers care about both resolution and tolerance,” said Kawola.
Although micro 3D printing is often used for prototyping and pre-production testing, some companies seek it out for production-ready parts or short-volume orders. “For short-medium run production—say, 50,000 parts or fewer—micro 3D printing is often cost-effective and provides shorter time to production,” Kawola said. “This trend is occurring across a range of industries including optics/photonics, microfluidics, and medical device, displacing traditional manufacturing methods, especially injection molding. Sometimes optimizing a part for greater performance can only be done through the geometric design freedom that comes with additive manufacturing.”
The pace of miniaturization will quicken as advances continue to be made in micro 3D printing, especially with new materials.
A big strength of additive manufacturing is the ability to design and manufacture parts with high complexity, without being constrained by the limitations of conventional manufacturing processes, such as injection molding, machining, stamping, or casting. “Mechanical engineers need to recognize that, thanks to micro 3D printing, they can now create very small parts that were perhaps very costly or impossible to make before,” Kawola said.
Potential applications using micro 3D printing abound, including next-generation medical devices and implants, 3D scaffolds for stem cell differentiation, high-performance cameras and optics, and advanced, lightweight, wearable or embedded sensors, leading the way to an explosion of Internet of Things-enabled products.
“Miniaturization is happening all around us,” Kawola said. “As our micro 3D printing technologies converge with other inputs, like software/artificial intelligence and materials science, high-value, end-parts made with AM will revolutionize our manufacturing sectors.”
Mark Crawford is a technology writer based in Corrales, N.M.
Now, however, AM technologies have advanced to the point where they can make small, high-resolution parts with incredibly tight tolerances. Led by software and hardware advancements, “micro 3D printing” equipment enables manufacturers to make AM parts that are millimeters in size and smaller, at tolerances in the micron range.
Several AM platforms have been modified to achieve micron-level resolution. These include micro stereolithography, selective laser sintering (for metals), and directed energy deposition. Another variation of stereolithography is multiphoton lithography (MPL), which can have resolutions of up to 50 nanometers, far smaller than can be seen with the naked eye.
Resolution and Dimensional Accuracy
A leader in micro 3D printing is Boston Micro Fabrication. Its platforms utilize a proprietary projection micro stereolithography (PµSL) technology, a vat polymerization process that has been upgraded with the latest technologies for control resolution and dimensional accuracy. This allows for rapid photopolymerization of a layer of liquid polymer using a flash of UV light at micro-scale resolution, with a larger build volume (50 x 50 x 50 mm). The printer is compatible with a growing portfolio of engineering and ceramic resins suitable for end-use parts.
Resolution ranges from two microns to 25 microns. “Resolution is the size of the light voxel that is being projected onto the resin bath,” said John Kawola, CEO for Boston Micro Fabrication. “With this size projection, we can typically achieve features such as posts, walls, and holes that are five times the voxel size. So, for a 10-micron system, we can create a 50-micron feature.”
Dimensional tolerance is another consideration. Some industries are more focused on resolution and less on dimensional accuracy. A good example is the jewelry industry. These manufacturers care about very crisp features/edges and surface finish, but they are usually not measuring their product. “In the more industrial applications such as electronics, medical devices, sensors, and microfluidics, product designers care about both resolution and tolerance,” said Kawola.
Although micro 3D printing is often used for prototyping and pre-production testing, some companies seek it out for production-ready parts or short-volume orders. “For short-medium run production—say, 50,000 parts or fewer—micro 3D printing is often cost-effective and provides shorter time to production,” Kawola said. “This trend is occurring across a range of industries including optics/photonics, microfluidics, and medical device, displacing traditional manufacturing methods, especially injection molding. Sometimes optimizing a part for greater performance can only be done through the geometric design freedom that comes with additive manufacturing.”
Future Trends
The pace of miniaturization will quicken as advances continue to be made in micro 3D printing, especially with new materials.
A big strength of additive manufacturing is the ability to design and manufacture parts with high complexity, without being constrained by the limitations of conventional manufacturing processes, such as injection molding, machining, stamping, or casting. “Mechanical engineers need to recognize that, thanks to micro 3D printing, they can now create very small parts that were perhaps very costly or impossible to make before,” Kawola said.
Potential applications using micro 3D printing abound, including next-generation medical devices and implants, 3D scaffolds for stem cell differentiation, high-performance cameras and optics, and advanced, lightweight, wearable or embedded sensors, leading the way to an explosion of Internet of Things-enabled products.
“Miniaturization is happening all around us,” Kawola said. “As our micro 3D printing technologies converge with other inputs, like software/artificial intelligence and materials science, high-value, end-parts made with AM will revolutionize our manufacturing sectors.”
Mark Crawford is a technology writer based in Corrales, N.M.
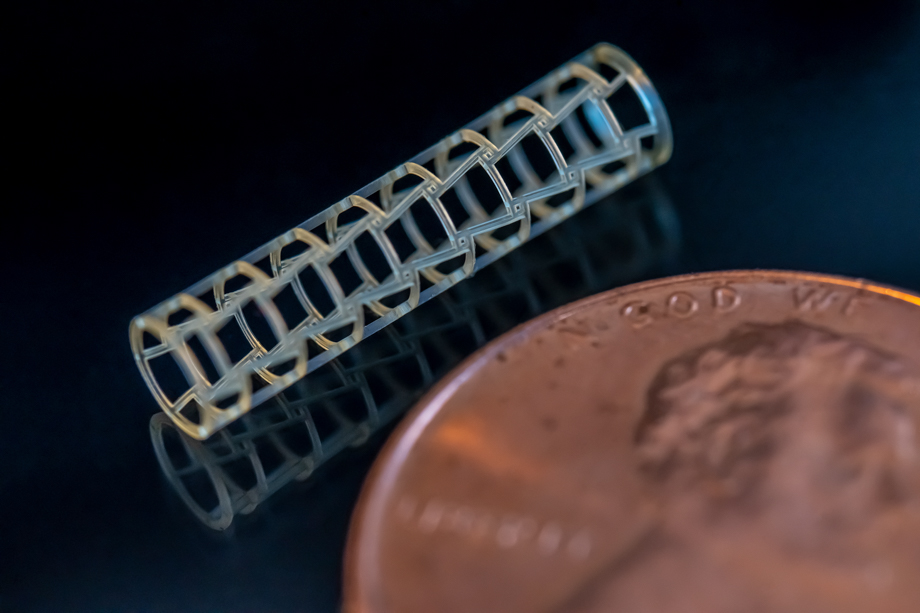
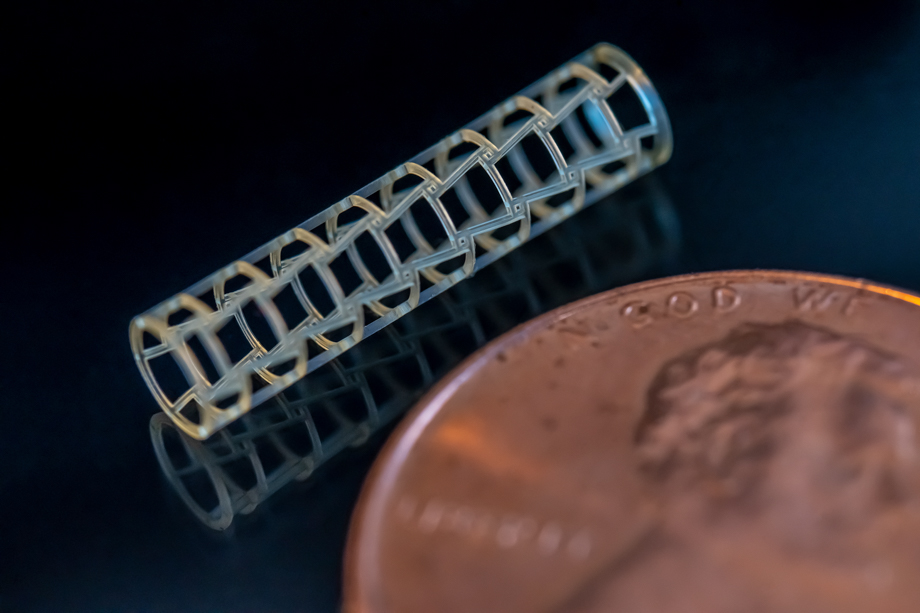