Top 10 Materials for 3D Printing
Top 10 Materials for 3D Printing
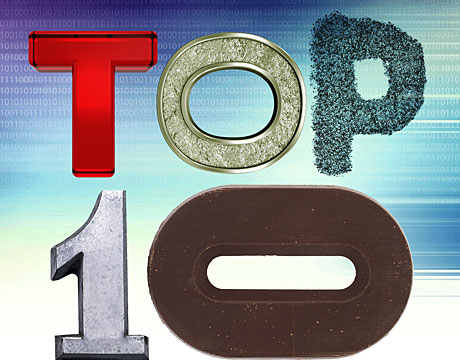
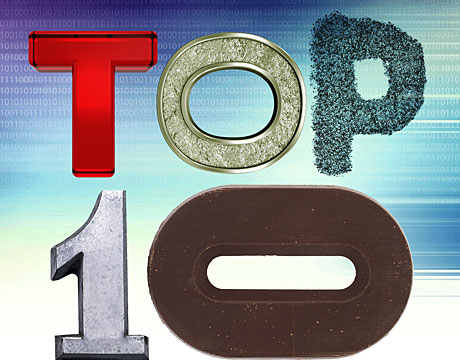
The excitement around the promise of 3D printing has opened the floodgates. New printers are being developed every day to print all sorts of materials from plastics, metals, composites, and concrete, to organic materials, paper, and food.
“It shows what a hot and exciting field it is,” says Jesse Darley, director of mechanical engineering for Design Concepts, a Madison, WI-based product design and innovation consultancy.
Darley’s favorites as a product developer begin with those currently in use and those undergoing testing and are followed up by materials of interest in other fields. Below are his top 10 favorite materials for 3D printing (beyond common and improved plastics), starting with current ones.
1. Sintered powdered metal
Used for “printing” injection molds and sacrificial fixtures that accelerate the design process for traditional manufacturing methods like injection molding, casting, and lay-up. “One of the cooler applications is for carbon fiber lay-up,” Darley says. “You print the lattice and lay out the carbon fiber [around the mold]. Then you put it in a bath, and the support material melts away.”
2. Metals, such as stainless, bronze, steel, gold, nickel steel, aluminum, and titanium
These are printed directly by binding metal dust and firing it to become a hard part. This process can replace casting and post-processing and turn material directly into a functional metal part that can be electropolished or machined to finish the items. Prototyping is the best example of this application, but it is also being used for medical devices, jewelry and other custom items, according to Darley.
3. Carbon fiber and other composites
A 3D machine first prints a plastic, like ABS, and then prints carbon fibers on top. “This is a more cost-effective and quicker way to print something as strong as or stronger than metal,” Darley says. “If it can be scaled up (right now the printers are fairly small), I see it replacing carbon fiber lay-up, a slow and time-consuming process.” This material is used in the bicycle and aeronautics industries.
4. Carbon nanotubes and graphene embedded in plastics
“The most awesome is graphene,” says Darley. “There is all this promise of graphene, its amazing strength, conductivity instead of connectivity, its size. You could make things like flexible touchscreens, solar panels, and building circuits made of extremely tough materials; that’s the only material I’ve seen where you create totally new technology, not just being able to do stuff faster or easier; this is something totally new.”
5. Nitinol
Nitinol is an alloy of nickel and titanium used in a lot of medical implants. Darley notes that this metal has two “amazing” properties: its superelasticity and the ability to change shapes. For catheter wires and stents, nitinol can bend further than anything else, he explains. “You can fold it in half and it will come back into its original shape.” Darley adds that because the metal is not an easy material to machine or create in a lot of different forms, 3D printing allows you to do things with medical products you couldn’t do before.
6. Water-absorbing plastic
Water-absorbing plastic is printed using a 4D printing process. The fourth dimension refers to a form an object can take after it is printed that is a different shape, possibly leading to self-assembly. For example, if something is being inserted into the body (or sea, or space), in a narrow tube but the end product needs to be a different shape, the object can transform itself after it is inserted.
7. Stem cells
Being able to print organs to replace an ear, a blood vessel, or a piece of the heart with such an implant is pretty amazing, Darley says.
8. Conductive carbomorph (carbon black plus plastic)
3D printing allows circuits and batteries to be built into plastic parts used to make devices. This could eliminate some assembly, leading to having additive manufacturing replacing most, if not all, other manufacturing processes. “There are very few plain plastics or mechanical parts these days; everything is electromechanical,” Darley says.
9. Paper
3D printed paper results in a full color model; one produced very inexpensively compared to traditional visual models that take hours of work for a realistic look and are used for client approval of a design prior to final engineering, Darley says. The printer glues together and trims layers of paper to create the shape and has the capability of adding color as well.
10. Concrete, food, yarn
In China, pieces of houses have been printed and then assembled. Food has been printed in all different shapes, and yarn has produced many soft materials. When you think about it, you can manipulate with the computer anything that can be squirted out, Darley adds.
Nancy S. Giges is an independent writer.
Participate in ASME's Advanced Design & Manufacturing Impact Forum, focusing on the intersection of advanced design and manufacturing in industrial and consumer applications.
When you think about it, you can manipulate with the computer anything that can be squirted out.Jesse Darley, Design Concepts
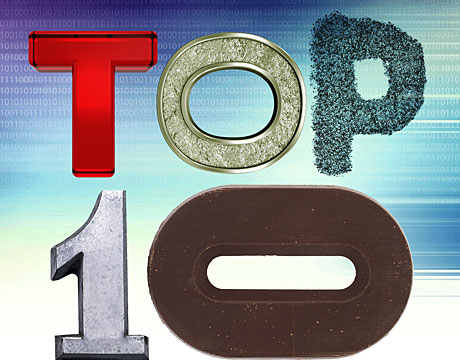
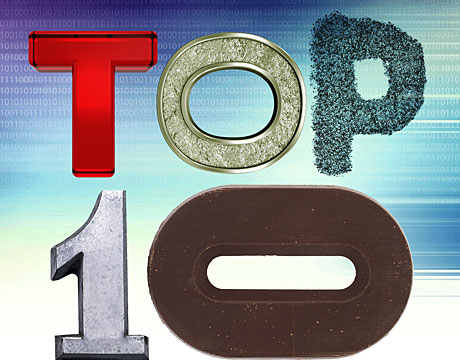