Taking the Noise Out of Expansion
Taking the Noise Out of Expansion
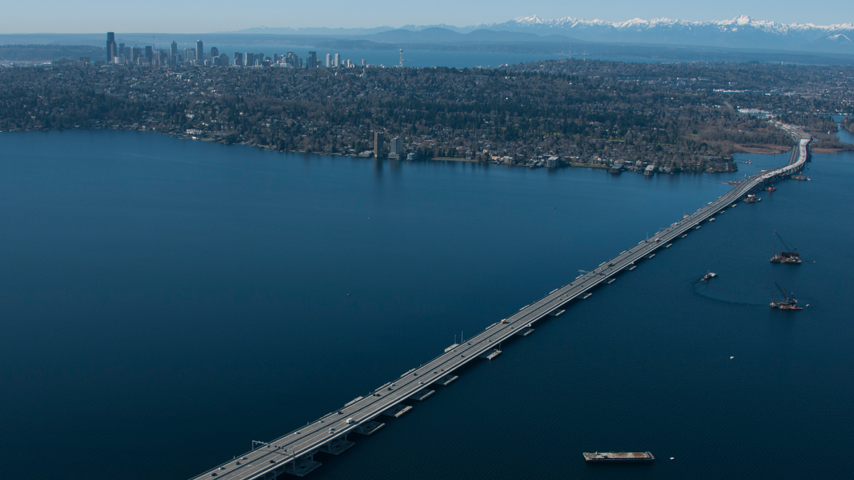
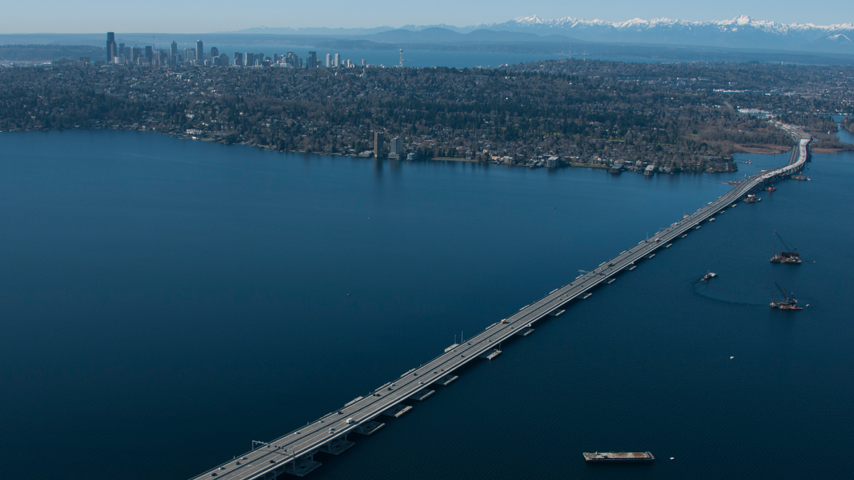
Researchers designed, tested, and recommended strategies that successfully reduced the noise caused by noisy floating bridge expansion joints.
Four of the world’s five longest floating bridges are located in Washington State. This is because of the deep bodies of water with soft foundations, making conventional bridges more expensive to build. On each end of the bridge, where the floating segments meet the fixed sections, there are large expansion joints to accommodate changes in the water surface, wind, and thermal expansion. As cars drive across the expansion joints they generate significant noise that is heard up to a mile away.
A team of researchers at the University of Washington, in consultation with the Washington Department of Transportation, have developed a solution to quiet noisy expansion joints on the Evergreen Point (SR 520) floating bridge connecting Seattle and Bellevue over Lake Washington. The team 3D printed initial models, but these weren’t scalable for durable samples. Outsourcing to a manufacturing facility, they made a prototype from a material resembling a car tire.
The polymer is very strong and durable to support the weight of a car, but still flexible enough to expand and contract with the bridge. The team installed the prototype and then collected audio samples. At the expansion joint, the team measured a 56 percent reduction in audible noise over the sounds of traffic. At 160 feet away, they measured a 70 percent reduction. The noise reduction was so significant it was hard to distinguish between the expansion joint noise and regular traffic sounds.
Joint noise
The expansion joints consist of 15 steel I-beams running perpendicular to the flow of traffic, a neoprene seal between each beam below the road surface to prevent runoff from entering Lake Washington, and a concrete cavity below to mitigate noise and provide access for servicing. During normal operation, the gaps between the I-beams range from 0.84 inches to three inches and up to 9 degrees of rotation. In some cases, during extreme weather, the gaps may fully close, meaning the team needed to design a prototype to fail under these conditions, allowing closure and protecting the bridge structure.
As cars drive across the expansion joints three main mechanisms occur. The I-beams vibrate from the impact of the car tire, this compresses the air inside the expansion joint and the sound, and the tires themselves create noise. All the sound is generated as the tire deforms into the gap between each of the expansion joints I-beams. The goal of the prototype is to fill the gap between the expansion joints to limit pressure spikes in the beam, tire, and cavity, while not interrupting traffic, and still allowing the joints to expand and contract with movement from the bridge.
The tire is excited by the edge of the beams, the beams are shaken by the tire, and more significantly the air is compressed into the expansion joint cavity. "It's all about filling this gap with something strong enough to support the vehicle," Per Reinhall explained. As a mechanical engineering professor at the University of Washington and expert in acoustics and biomechanics, Reinhall has worked with the Washington Department of Transportation on previous projects to reduce acoustic impacts on marine life. "The problem is when the gap gets smaller the beams push on the material it expands. We had to come up with a zero Poisson’s ratio structure, meaning if you compress the structure one way, it does not expand in another direction,” he explained.
Become a Member: How to Join ASME
Poisson’s ratio, a measure of the Poisson effect, is when a material expands in the direction perpendicular to compression. In the context of the bridge expansion joints, when the material between the I-beams is compressed as the beams move in and out, the material expands up and out of the expansion joint and impacts traffic on the roadway. To prevent upward expansion, the prototype uses a flexible chevron pattern with no height change from compression along the length of the gap.
Reduced noise
Constructed in 2016, the Evergreen Point floating bridge replaced the original 1963 bridge of the same name. To reduce traffic noise in the surrounding neighborhoods, when constructing the new bridge builders incorporated 1,600 feet of noise walls into the north and south sides of the bridge’s east end. The roadway surface also features quieter concrete, which includes grooves in the pavement to further reduce traffic noise. “They made the road surface quieter compared to the old bridge but then noise from the expansion joints stood out more than the rest of the bridge” Reinhall noted.
More for You: Engineers Work to Quiet the Ocean
The prototype was successful at reducing noise as cars rolled over the expansion joint. The research team used convenient fabrication processes and low run production, allowing them to access the prototype quickly and cost effectively to start testing. With a successful prototype design, the team is looking at options for more durable material, better manufacturing, and mass production to develop a prototype lasting at least three years or more, since engineers need to close the bridge to install the product.
The chevron zero Poisson’s ratio protype was successfully able to reduce the noise emanating from the large expansion joints on Seattle’s newest floating bridge. The solution could benefit all types of bridges, not just floating ones. “The justification of getting funding for this project was not just addressing a problem for one bridge, we're addressing a problem for hundreds of bridges in Washington State,” Reinhall explained.
Nicole Imeson is an engineer and writer in Calgary, Alberta.
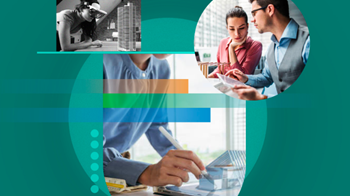
Pulse of the Profession: CAD in 2023
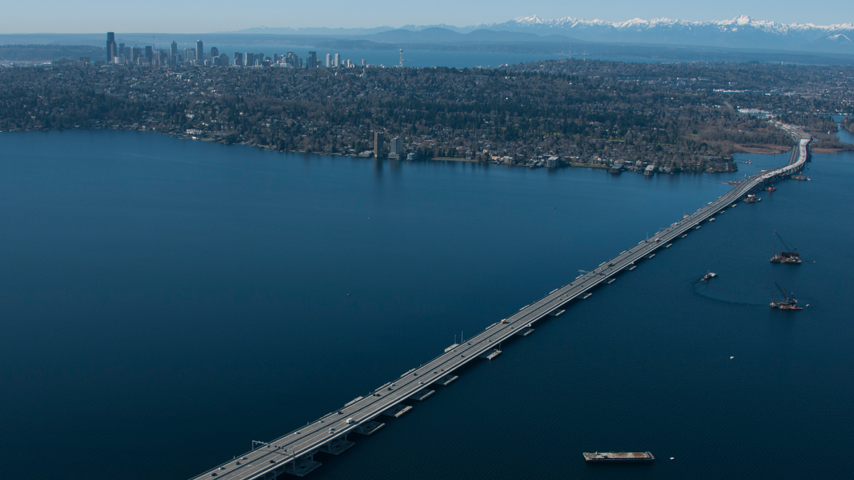
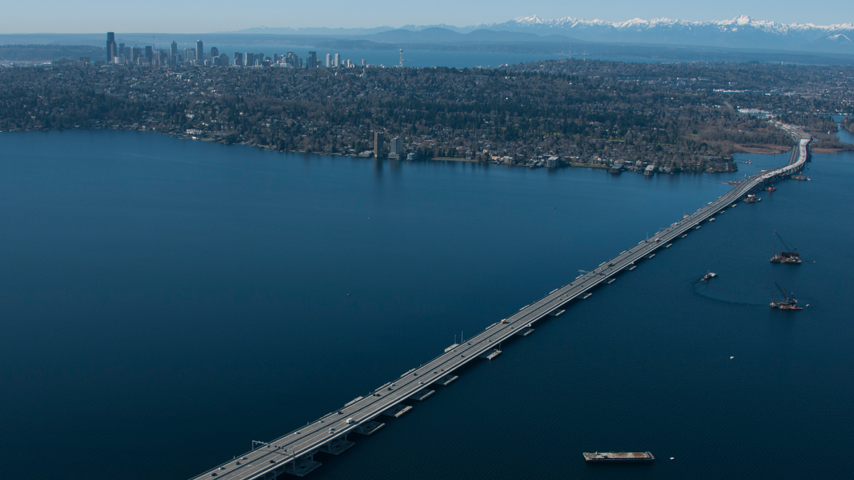