Sensing 3D Printing Flaws Can Make AM More Accepted
Sensing 3D Printing Flaws Can Make AM More Accepted
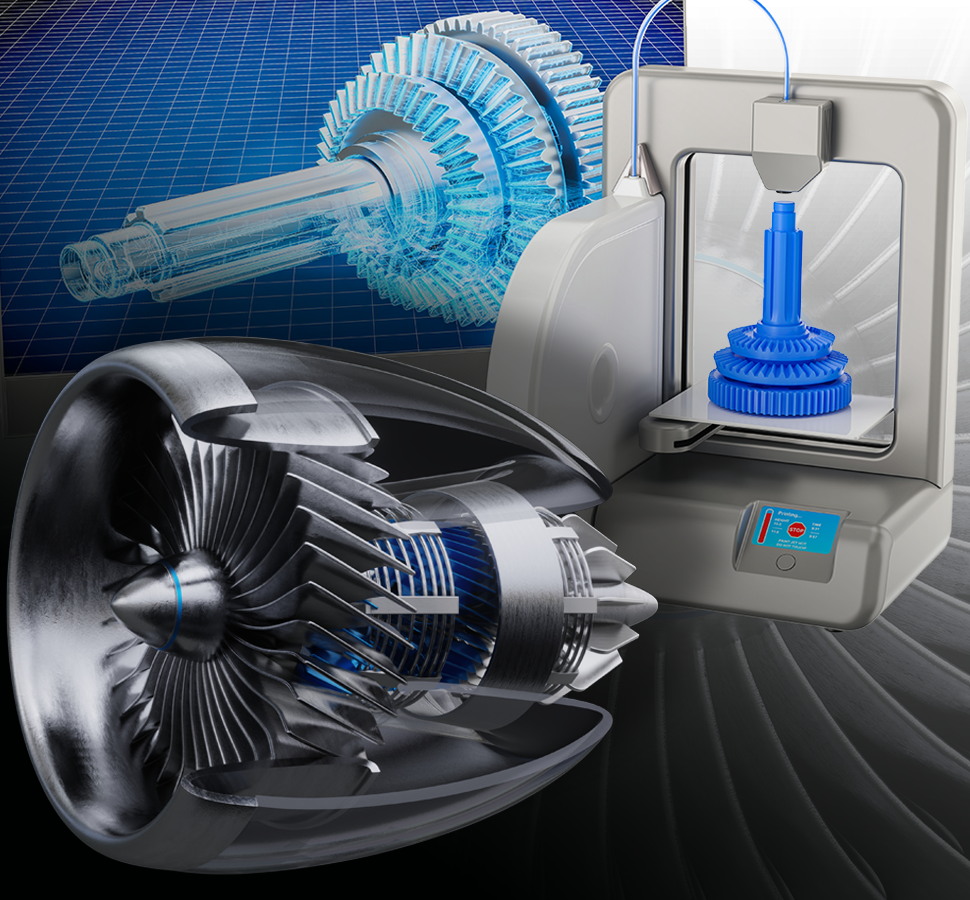
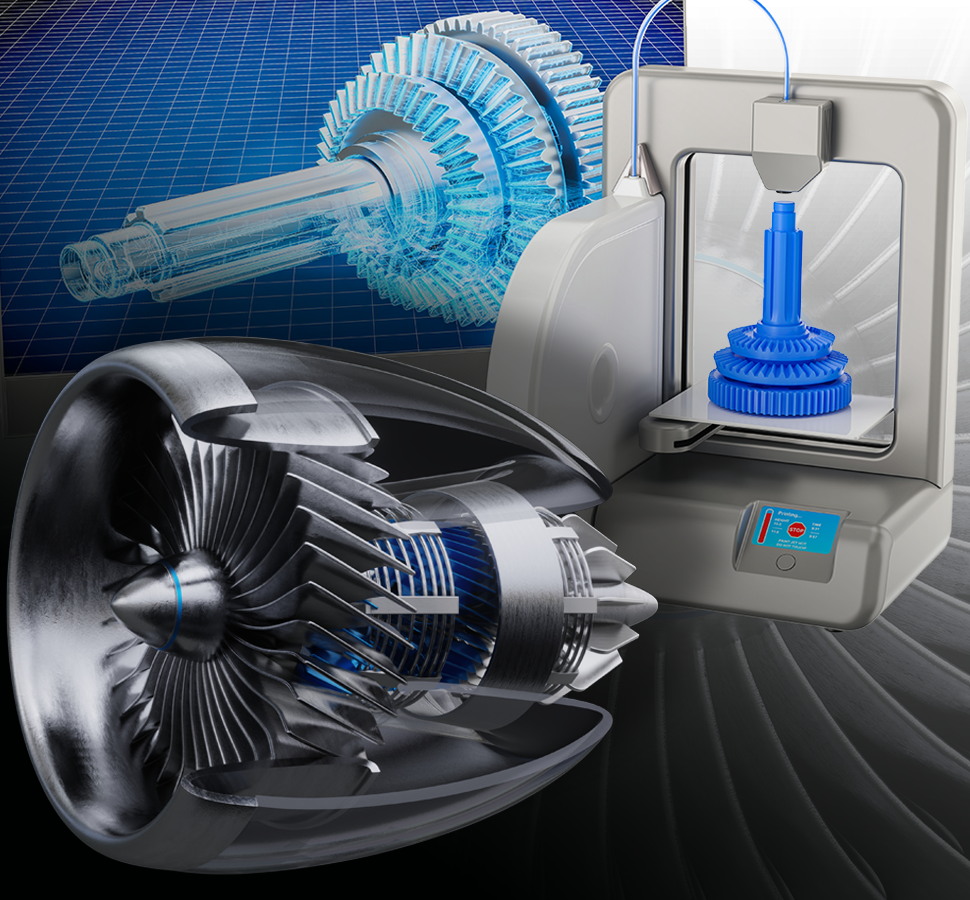
3D printing aircraft parts could dramatically reduce the amount of material used, and a reliable process could save even more.
One drawback to 3D printing for industries such as aerospace, automotive, or medicine is that there simply is no inexpensive way to ensure that the parts can meet the necessary standard of quality. A project led by Andrew Wessman and Mohammed Shafae with the University of Arizona’s College of Engineering, funded by NASA, aims to address this issue.
In collaboration with Open Additive LLC and CompuTherm LLC, their goal is to set up a suite of sensors, as well as thermal imaging and high-speed cameras, that will monitor the printing process in situ and detect when and where problems may occur. This technology suite will help improve the 3D printing process—making it a cost-effective option for producing intricate parts, specifically for jet engines.
“These are very complex geometries that are difficult to inspect,” Wessman said. “We’re going to come up with a way to detect anomalies that occur during the process so we can start to analyze and classify them into different categories based on the information we get from the sensors.”
More on This Topic: Rethinking and Redesigning Heat Exchangers
There are many ways that anomalies can occur. Some of these can be mistakes in how the products are modeled. Some of them can be random variation with the materials such as vaporization or cracking. The goal is to shore up these issues so that the part is in near-flawless condition.
“You’re never going to make a perfect part,” Wessman explained. “But in the aviation industry, we must understand the levels of imperfection that we can tolerate within the material.”
Traditionally, jet engine parts are made in a variety of ways, but all involve castings, casings, or molds. Compressor discs, for example, must be in mint condition as these parts endure extremely high pressure and any cracking could quickly turn into terminal fractures once in operation. The discs are formed in a process called powder metallurgy that involves vacuum packing a fine metallic powder into a casing that is then put under intense heat and pressure to fuse the powder into a disc. Other parts like compressor blades are cast by pouring an alloy into a ceramic mold and cooling it. Regardless of how the parts are made, they all must be shaped and cut down to size. This creates a lot of waste.
Shafae said 3D printing the parts could dramatically reduce the amount of material used, and a reliable process could save even more.
“If we can get a good handle on the process, minimize the amount of postproduction vetting and inspection, and shorten the time that it takes to develop the process, it would help a lot with the economics,” he said.
Also, analysis must occur at the microscopic level. Imagine taking the highest resolution image and zooming all the way in.
Once the researchers crack the code, they believe they will be one step closer to ensuring that the part is to spec. The next phase in development for the team will be to apply machine learning methods that not only detect an issue but predict it. Ideally, this would mean that they can put a stop to the process should some kind of damage occur, so as not to waste additional time and material.
“So for instance, say I have a lack-of-fusion defect,” Shafae said. “Can I change something when I make the next layer that helps to correct that defect? Can I add more energy on the next layer to melt a little bit deeper and fill in the hole, or should I terminate the process altogether? This kind of ‘correction mode’ is the long-term goal.”
At the end of the program, the team will run a demonstration at Lockheed Martin Space, another partner in the work, to prove the system’s effectiveness in an industrial environment.
Test Your Knowledge: How 3D Printing is Advancing in Automotive
The results from this research will no doubt be widely useful to many industries. As Wessman said, they’d like to make the system universal so that it may be adopted by developers of precision parts for medical implants or even semiconductors; any area where very high confidence in the part is needed. The main advantage they have is that their team is multidisciplinary and is working with individuals in all areas of their mechanical engineering program as well as individuals in data science who they say are the experts at working with very large data sets.
“This program provides a great framework for a lot of different disciplines to come together,” Wessman said. “We’re working on different aspects of additive manufacturing that go from design all the way through production, post-processing, and lifecycle management. So it’s a great opportunity for a lot of us from diverse backgrounds to work together on some very interesting problems.”
Cassandra Martindell is a science and technology writer based in Columbus, Ohio.
In collaboration with Open Additive LLC and CompuTherm LLC, their goal is to set up a suite of sensors, as well as thermal imaging and high-speed cameras, that will monitor the printing process in situ and detect when and where problems may occur. This technology suite will help improve the 3D printing process—making it a cost-effective option for producing intricate parts, specifically for jet engines.
“These are very complex geometries that are difficult to inspect,” Wessman said. “We’re going to come up with a way to detect anomalies that occur during the process so we can start to analyze and classify them into different categories based on the information we get from the sensors.”
More on This Topic: Rethinking and Redesigning Heat Exchangers
There are many ways that anomalies can occur. Some of these can be mistakes in how the products are modeled. Some of them can be random variation with the materials such as vaporization or cracking. The goal is to shore up these issues so that the part is in near-flawless condition.
“You’re never going to make a perfect part,” Wessman explained. “But in the aviation industry, we must understand the levels of imperfection that we can tolerate within the material.”
Traditionally, jet engine parts are made in a variety of ways, but all involve castings, casings, or molds. Compressor discs, for example, must be in mint condition as these parts endure extremely high pressure and any cracking could quickly turn into terminal fractures once in operation. The discs are formed in a process called powder metallurgy that involves vacuum packing a fine metallic powder into a casing that is then put under intense heat and pressure to fuse the powder into a disc. Other parts like compressor blades are cast by pouring an alloy into a ceramic mold and cooling it. Regardless of how the parts are made, they all must be shaped and cut down to size. This creates a lot of waste.
Shafae said 3D printing the parts could dramatically reduce the amount of material used, and a reliable process could save even more.
“If we can get a good handle on the process, minimize the amount of postproduction vetting and inspection, and shorten the time that it takes to develop the process, it would help a lot with the economics,” he said.
Selected for You: Additive Manufacturing Trends: Looking Back at 2021 and Ahead on 2022
The main challenge for Wessman and Shafae is how to create a system that can digest all of the data required to properly detect anomalies. Manufacturing just one item can take several hours and all of the imaging data that the cameras collect, combined with data from the sensors, gives their system a lot to sort through.Also, analysis must occur at the microscopic level. Imagine taking the highest resolution image and zooming all the way in.
Once the researchers crack the code, they believe they will be one step closer to ensuring that the part is to spec. The next phase in development for the team will be to apply machine learning methods that not only detect an issue but predict it. Ideally, this would mean that they can put a stop to the process should some kind of damage occur, so as not to waste additional time and material.
“So for instance, say I have a lack-of-fusion defect,” Shafae said. “Can I change something when I make the next layer that helps to correct that defect? Can I add more energy on the next layer to melt a little bit deeper and fill in the hole, or should I terminate the process altogether? This kind of ‘correction mode’ is the long-term goal.”
At the end of the program, the team will run a demonstration at Lockheed Martin Space, another partner in the work, to prove the system’s effectiveness in an industrial environment.
Test Your Knowledge: How 3D Printing is Advancing in Automotive
The results from this research will no doubt be widely useful to many industries. As Wessman said, they’d like to make the system universal so that it may be adopted by developers of precision parts for medical implants or even semiconductors; any area where very high confidence in the part is needed. The main advantage they have is that their team is multidisciplinary and is working with individuals in all areas of their mechanical engineering program as well as individuals in data science who they say are the experts at working with very large data sets.
“This program provides a great framework for a lot of different disciplines to come together,” Wessman said. “We’re working on different aspects of additive manufacturing that go from design all the way through production, post-processing, and lifecycle management. So it’s a great opportunity for a lot of us from diverse backgrounds to work together on some very interesting problems.”
Cassandra Martindell is a science and technology writer based in Columbus, Ohio.
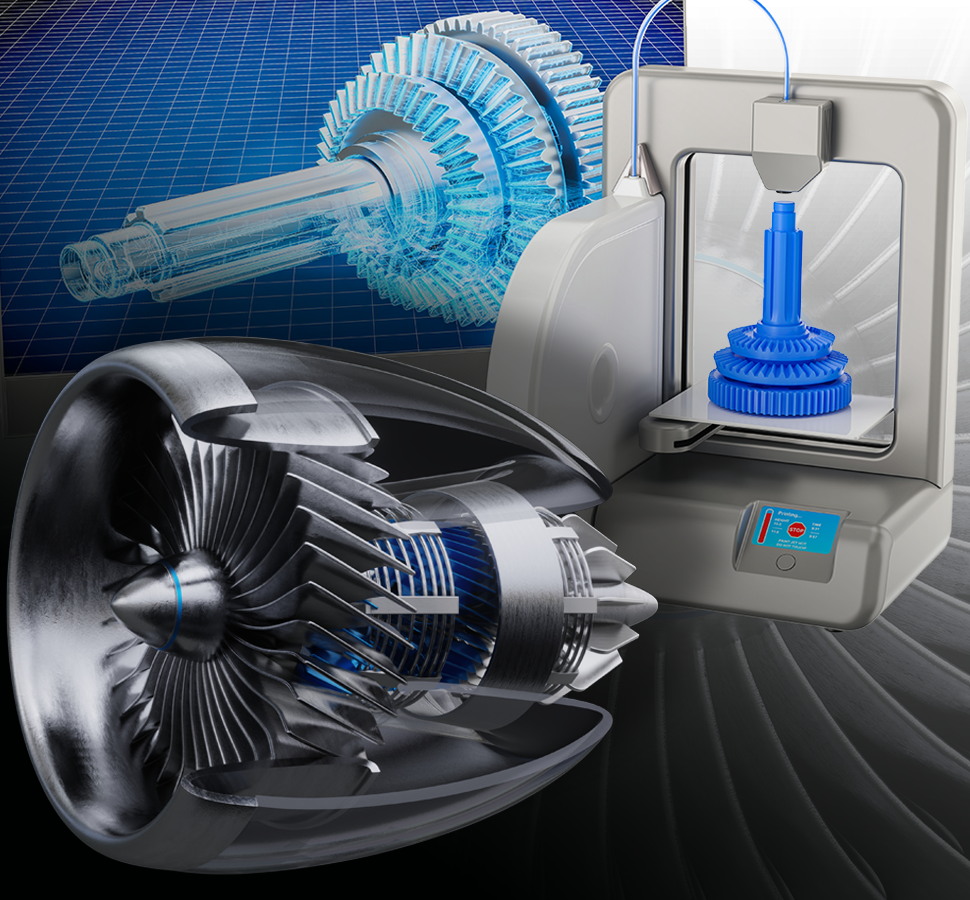
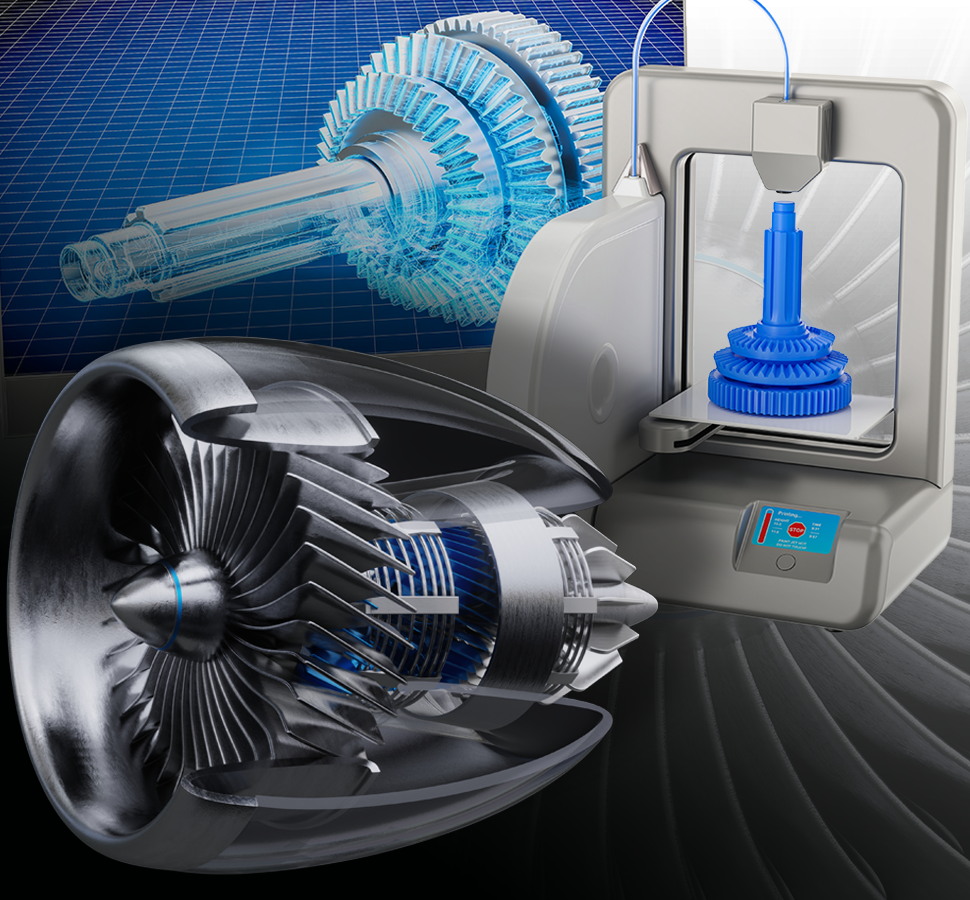