Pressurized Haptic Sleeve Breaks New Ground in Wearables
Pressurized Haptic Sleeve Breaks New Ground in Wearables
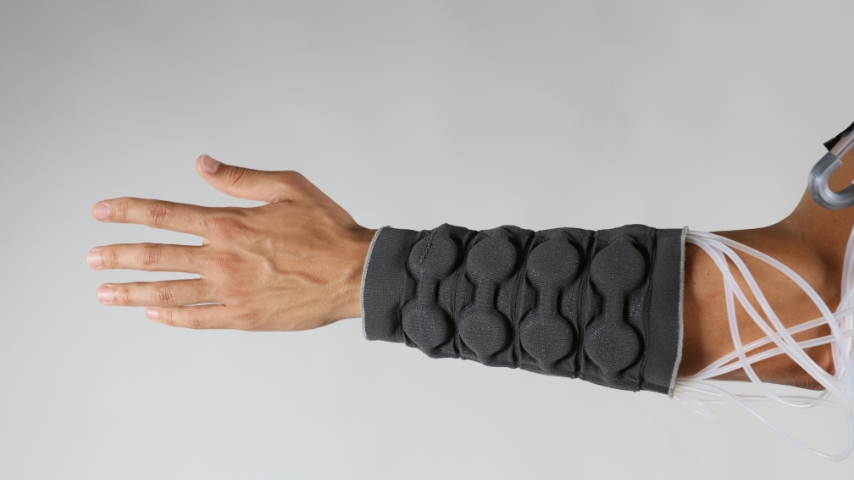
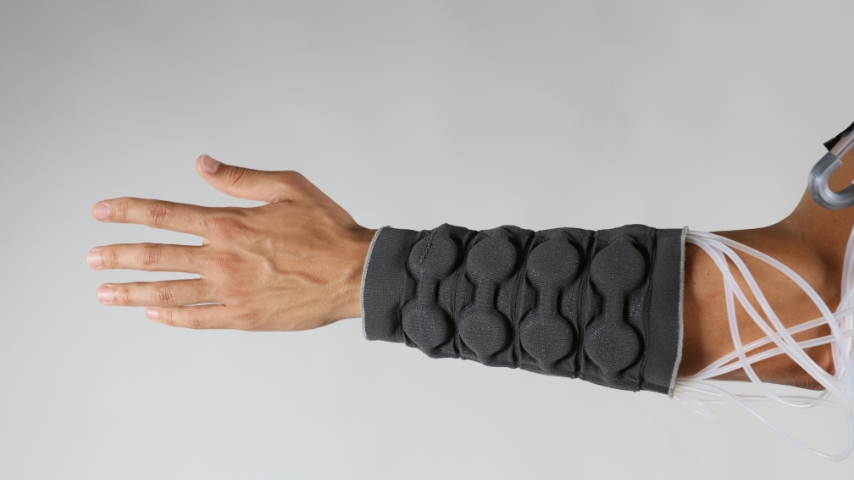
New wearable technology has implications for both social and medical applications as the knitted sleeve allows wearers to interact with the world through pressure-based haptics.
A new knitted sleeve that mimics human touch gives the wearer a new way to interact with the world, opening possibilities for social and medical applications. Unlike current modern wearable technology that uses vibration for haptic response, the researchers explored pressure as a means to mimic touch.
“One of the things that moved us to do this project was the role of touch in remote interactions, especially during the pandemic,” shared Allison Okamura, professor of engineering at Stanford University and senior author of the article published in Science Robotics, “Haptiknit: Distributed stiffness knitting for wearable haptics.”
As Okamura explained, we’re fairly used to vibration feedback now—think about your cell phone or gaming device. “It’s become a non-auditory way of communicating,” she said. “Vibration is usually used to bring your attention to something, or to say that there’s been an event, but it can’t communicate a lot of detailed information.”
The research team builds on the knowledge that mechanoreceptors—sensory receptors in our skin—can be very non-specific. You can feel the vibrating sensation in your hand, but that sensation is not localized. As Okamura explained it, our perception of vibration is “diffused.”
So, to replicate human touch as realistically as possible with the sleeve, Okamura teamed up with Cosima du Pasquier, a postdoctoral researcher and first author of the article. Together, they created a “haptic illusion” using a pressurized system that tricks the user into believing they are being touched.
To do this, they designed a knitted structure that is embedded with small pneumatic actuators to enable a programmable haptic display. A high-stiffness outer layer grounds the force and a lower stiffness inner layer transfers that force to the wearer. Their design is not only effective, but also comfortable, versatile, and even washable. This strategy represents a major advancement when compared to other modern wearable designs, which often have a rigid structure that sacrifices comfort for power.
“Comfort was always at the forefront of the design process,” du Pasquier said. “Existing haptic devices tend to be pretty big and bulky, and electric motors dissipate a lot of heat, requiring an external system. So the wearer often has to stay near where the system is stationed.”
Du Pasquier has been working with textiles for some time and was looking at how knitting could be used in soft robotics and inflatables. It was during her post-doctoral research work at Stanford that she learned how to use an industrial knitting machine and began working with patterns that had been previously used in the lab for other haptics.
Du Pasquier and Okamura decided to collaborate with a group at MIT’s Self Assembly Lab that had extensive expertise in industrial knitting. “We worked with Lavender Tessmer and Skylar Tibbits at MIT to think through the structure,” Okamura explained. “They do amazing things with knits and fabrics and other novel engineering materials. They’re a very creative group.”
Creating the design came with its challenges. First, it was difficult to source parts. There’s not much in the way of application for very small pneumatic devices, so they were limited in their options for valves and pressure systems.
Resolution was another challenge. Du Pasquier initially envisioned a design that had little bubbles all over and quickly realized that wouldn’t be feasible, because, as Okamura knew from her own expertise in haptics, there isn’t enough sensation—or resolution—in the forearm.
“We have very high resolution and a very good haptic perception in our fingertips, but not so much in other parts of our body,” Okamura said. “So on one hand, we have this unused ‘skin real estate,’ but the amount of force that we need to apply is larger on the arm than if we had the device mounted on the fingertips.”
Understanding this, du Pasquier knew that the dense bubble design wouldn’t be able to pack as much power. So they came up with a pattern that has space for a total of eight actuators arranged in two rows. Putting together their skills and experience allowed them to come up with a highly effective model for a pressurized wearable.
“Our different domains of expertise converged to create something that worked, and worked well,” du Pasquier explained. “We were able to bring them together pretty seamlessly.”
The team tested the wearable with 32 participants, and what they found was that the users were able to distinguish touch at a much higher resolution, which isn’t something that typically happens with vibrational devices.
Through the results from this research, and the research Okamura has been a part of for the past 10 years, they created their own kind of “touch language.”
“In earlier studies, we were collaborating with psychologists and taking cues from people in other fields about how people communicate through social touches,” Okamura explained.
“We would give them a prompt like, ‘you're sitting next to your friend, you just had this amazing day, you won a hundred dollars,’ and then you reach out and touch your friend to tell them what an awesome day you're having, and then we would actually have the partner wearing a sleeve with sensors in it and we were able to record that social touch,” she said.
They recorded the sensations for all kinds of social touches from positive to negative and were able to characterize them—giving Okamura and du Pasquier a great foundation for setting up communication with their own device. Now, the goal is to characterize these “touch languages” from many diverse backgrounds.
“Everything we build is going to be colored by the perspective and the context in which we get that data,” Okamura said. “So one of the things that we want to do next is allow people to design their own touch communications.”
They also have ideas for how to create a dual system, one where the user is able to teleoperate a robot and that same system can provide haptic feedback to the user, or where two users can interact through the system. Further, making the device easy to take on and off, which will be especially important for users who may have mobility impairments, is also a consideration.
Overall, they imagine applications for this device in virtual reality, medicine, and rehabilitation, and even dog training. “I actually used the system to train my friend’s dog,” du Pasquier explained. “He learned how to sit and lie down on command in about five minutes.”
This design represents a significant leap forward in the field of human-computer interaction. By moving beyond the limitations of vibrational haptics, the researchers have unlocked a richer and more intuitive way for users to experience virtual and remote environments, fundamentally changing how we connect with technology and each other.
Cassandra Kelly is a technology writer in Columbus, Ohio.
“One of the things that moved us to do this project was the role of touch in remote interactions, especially during the pandemic,” shared Allison Okamura, professor of engineering at Stanford University and senior author of the article published in Science Robotics, “Haptiknit: Distributed stiffness knitting for wearable haptics.”
As Okamura explained, we’re fairly used to vibration feedback now—think about your cell phone or gaming device. “It’s become a non-auditory way of communicating,” she said. “Vibration is usually used to bring your attention to something, or to say that there’s been an event, but it can’t communicate a lot of detailed information.”
Replicating human touch
The research team builds on the knowledge that mechanoreceptors—sensory receptors in our skin—can be very non-specific. You can feel the vibrating sensation in your hand, but that sensation is not localized. As Okamura explained it, our perception of vibration is “diffused.” So, to replicate human touch as realistically as possible with the sleeve, Okamura teamed up with Cosima du Pasquier, a postdoctoral researcher and first author of the article. Together, they created a “haptic illusion” using a pressurized system that tricks the user into believing they are being touched.
To do this, they designed a knitted structure that is embedded with small pneumatic actuators to enable a programmable haptic display. A high-stiffness outer layer grounds the force and a lower stiffness inner layer transfers that force to the wearer. Their design is not only effective, but also comfortable, versatile, and even washable. This strategy represents a major advancement when compared to other modern wearable designs, which often have a rigid structure that sacrifices comfort for power.
“Comfort was always at the forefront of the design process,” du Pasquier said. “Existing haptic devices tend to be pretty big and bulky, and electric motors dissipate a lot of heat, requiring an external system. So the wearer often has to stay near where the system is stationed.”
Du Pasquier has been working with textiles for some time and was looking at how knitting could be used in soft robotics and inflatables. It was during her post-doctoral research work at Stanford that she learned how to use an industrial knitting machine and began working with patterns that had been previously used in the lab for other haptics.
Du Pasquier and Okamura decided to collaborate with a group at MIT’s Self Assembly Lab that had extensive expertise in industrial knitting. “We worked with Lavender Tessmer and Skylar Tibbits at MIT to think through the structure,” Okamura explained. “They do amazing things with knits and fabrics and other novel engineering materials. They’re a very creative group.”
Design challenges of wearable devices
Creating the design came with its challenges. First, it was difficult to source parts. There’s not much in the way of application for very small pneumatic devices, so they were limited in their options for valves and pressure systems. Resolution was another challenge. Du Pasquier initially envisioned a design that had little bubbles all over and quickly realized that wouldn’t be feasible, because, as Okamura knew from her own expertise in haptics, there isn’t enough sensation—or resolution—in the forearm.
“We have very high resolution and a very good haptic perception in our fingertips, but not so much in other parts of our body,” Okamura said. “So on one hand, we have this unused ‘skin real estate,’ but the amount of force that we need to apply is larger on the arm than if we had the device mounted on the fingertips.”
Understanding this, du Pasquier knew that the dense bubble design wouldn’t be able to pack as much power. So they came up with a pattern that has space for a total of eight actuators arranged in two rows. Putting together their skills and experience allowed them to come up with a highly effective model for a pressurized wearable.
“Our different domains of expertise converged to create something that worked, and worked well,” du Pasquier explained. “We were able to bring them together pretty seamlessly.”
Communication through social touch
The team tested the wearable with 32 participants, and what they found was that the users were able to distinguish touch at a much higher resolution, which isn’t something that typically happens with vibrational devices. Through the results from this research, and the research Okamura has been a part of for the past 10 years, they created their own kind of “touch language.”
“In earlier studies, we were collaborating with psychologists and taking cues from people in other fields about how people communicate through social touches,” Okamura explained.
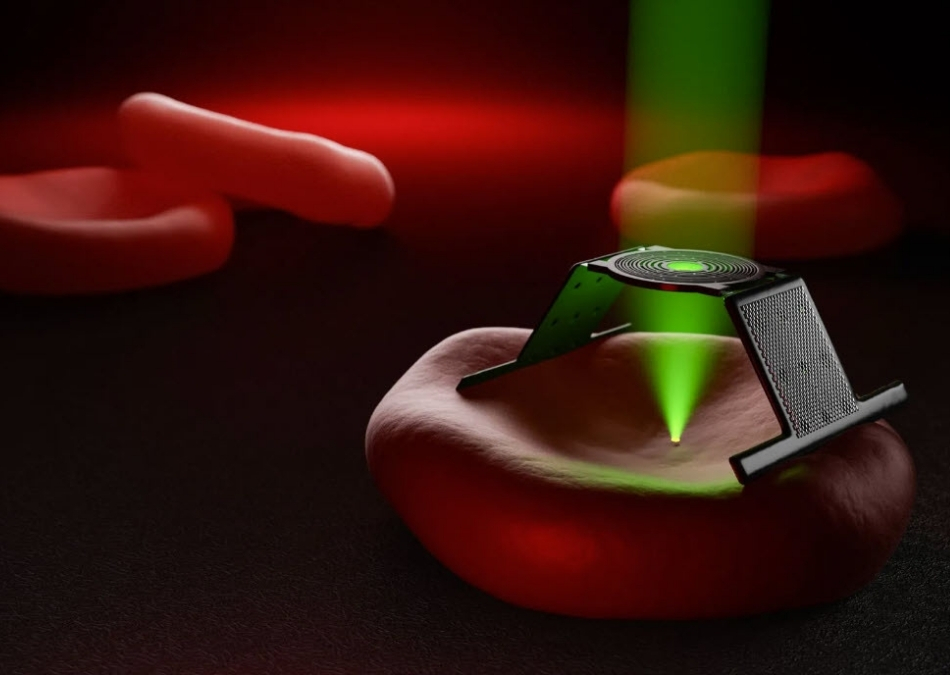
They recorded the sensations for all kinds of social touches from positive to negative and were able to characterize them—giving Okamura and du Pasquier a great foundation for setting up communication with their own device. Now, the goal is to characterize these “touch languages” from many diverse backgrounds.
“Everything we build is going to be colored by the perspective and the context in which we get that data,” Okamura said. “So one of the things that we want to do next is allow people to design their own touch communications.”
They also have ideas for how to create a dual system, one where the user is able to teleoperate a robot and that same system can provide haptic feedback to the user, or where two users can interact through the system. Further, making the device easy to take on and off, which will be especially important for users who may have mobility impairments, is also a consideration.
Overall, they imagine applications for this device in virtual reality, medicine, and rehabilitation, and even dog training. “I actually used the system to train my friend’s dog,” du Pasquier explained. “He learned how to sit and lie down on command in about five minutes.”
This design represents a significant leap forward in the field of human-computer interaction. By moving beyond the limitations of vibrational haptics, the researchers have unlocked a richer and more intuitive way for users to experience virtual and remote environments, fundamentally changing how we connect with technology and each other.
Cassandra Kelly is a technology writer in Columbus, Ohio.
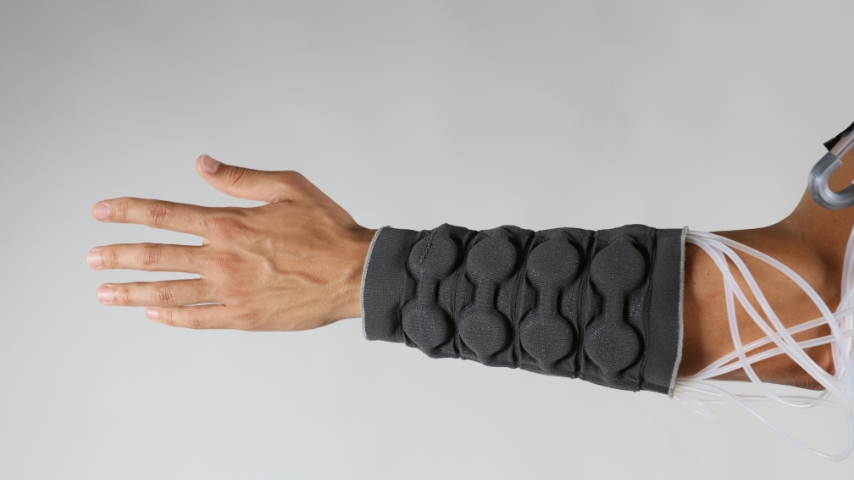
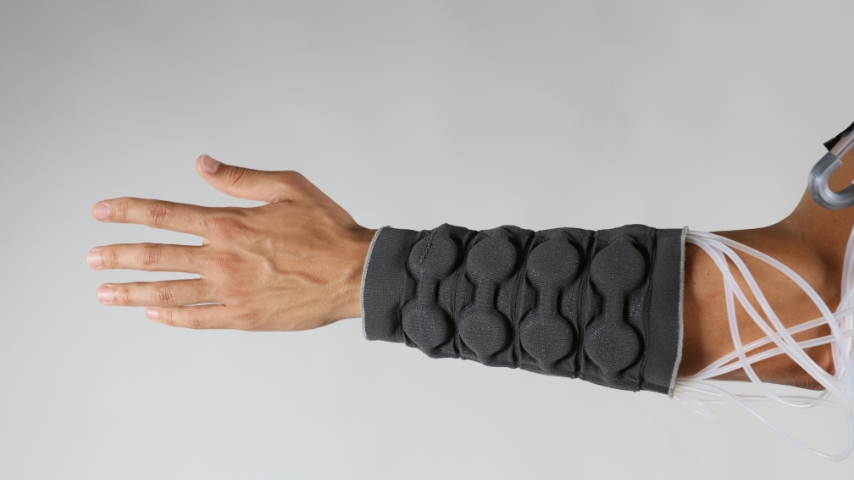