New Skills for the New World of Engineering
New Skills for the New World of Engineering
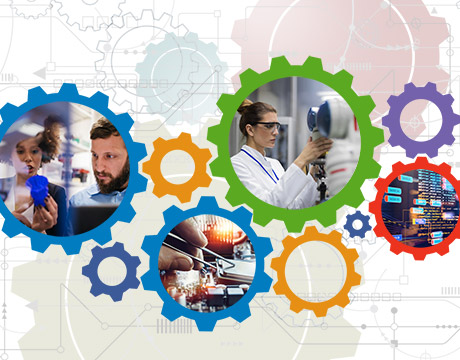
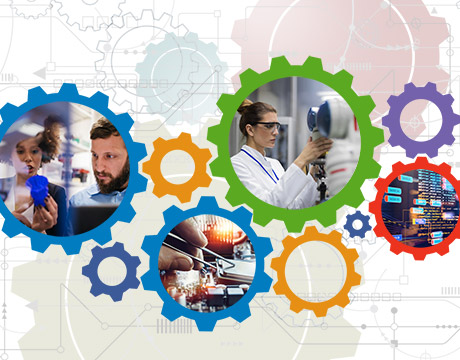
Because many of today’s devices and products designed by today’s mechanical engineers incorporate electronics and other non-mechanical components, companies want mechanical engineers with experience in additive manufacturing, robotics, computer and electrical engineering, mechatronics, system networking, and the Internet of Things.
As a modern-day mechanical engineer, you’re expected to know or at least understand disciplines and skills you weren’t taught in college. Unfortunately, many employers don’t offer the continued, cross-functional engineering training you need to keep up with the job. While some companies offer programs and training to bring their engineers up to speed, engineers without access to these resources must either fight to bring them in-house or access them through off-site education to stay fresh and advance their careers.
For You: 12 Skills You Need to Advance an Engineering Career
Nearly 40 percent of manufacturers polled for a recent survey said the evolving and changing engineering skillset needed for systems-driven product development is one of their biggest workforce challenges, according to research firm Tech Clarity.
The survey also found that 70 percent of the top-performing engineering companies polled expect the balance of engineering disciplines to continue to change over the next decade.
“Engineers who have been exposed to other engineering disciplines and have experience working on multi-discipline teams will be more prepared to participate in today's product development teams,” according to the survey.
Many divisions of the engineering software maker Siemens PLM use training to ensure employees are up-to-speed on the company’s software offerings. The training serves a dual purpose, as Siemens PLM users are also testing the training technology called Siemens Learning as a Service, says Beat Neuhaus, Siemens PLM vice president of educational services.
Sometimes customers ask: ‘What happens if I train my employees and then they leave because they get a better offer?’ I answer, ‘What happens if you don’t train them and they stay? Beat Neuhaus, Siemens PLM
The training is available to engineers under the “perform” membership, which is designed to support life-long learning and to help engineers and other users of the company’s digital enterprise software suite keep their knowledge up-to-date with the latest developments in digitalization. It offers engineers’ “point of need” about specific bits and pieces of information.
Siemens PLM has seen cost savings, faster time to market, high employee engagement, and long-term employee satisfaction as a result of the online training systems, Neuhaus says..
“This leads to faster and deeper user adoption and productivity and avoids underutilization of the purchased tools and systems,” he adds.
Training Against a Shortage of Engineers
Admittedly the Siemens program, like others from the makers of engineering technology, focuses on how to best use that company’s tools.
Surveys and articles dot the Internet about the need for continued training, but examples of companies that put that into place are rare. Their rationale is often misplaced, Nehaus says.
“Sometimes customers ask: What happens if I train my employees and then they leave because they get a better offer? I answer, What happens if you don’t train them and they stay?” he says.
“The Skills Gap in U.S. Manufacturing,” a 2016 study by Deloitte, cites that employers need to provide training for their existing workforce to ensure that a skills gap doesn’t develop that can’t be filled by hiring.
The Deloitte study also found that involvement with local schools and community colleges can ensure a future supply of engaged, skilled professionals for manufacturers.
Looking further at the issue, a 2016 Deloitte article titled “A 3D Opportunity for the Talent Gap” looked at how manufacturers can address the shortage of engineers and other technical employees with additive knowledge. It too called for continued training.
It’s unclear if engineering firm are heeding that call. What is clear, however, is that they’ll soon have to be to remain competitive.
Ongoing learning in engineering and design is the only solution for keeping up-to-date with rapidly evolving technology in the emerging knowledge economy, says Tony Glockler, the chief executive officer of Solid Professor, which provides online and mobile training tools for engineers.
“Smart investment in ongoing training is the hallmark of successful engineers and high-growth companies,” he says.
But what to do if you work for a company—and there seem to be many—that doesn’t offer cross-functional engineering training?
Ask your managers to make training available. Arm yourself with the studies cited here as well as other statistics and training options available.
Be aware that your higher-ups may fear engineers will leave for other opportunities after they have education and experience in new areas like additive manufacturing or robotics. For this, be ready to reiterate the quote from Neuhaus and cite the way your company can continue to succeed with well-rounded engineers on board.
Jean Thilmany is an independent writer.
Read More:
Freelance Engineering? There’s a Site for That
The Rise of the Master of Engineering Management Degree
Measuring Motivation
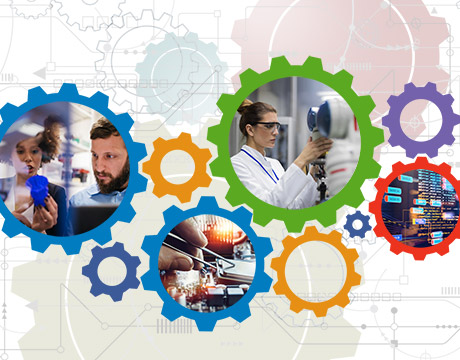
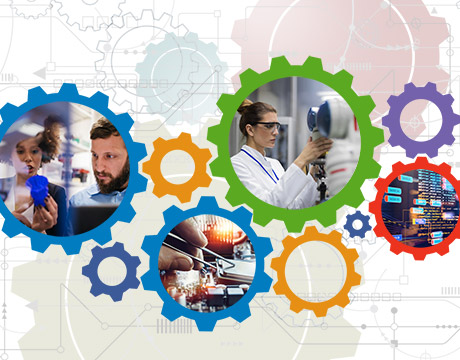