Engineering Jobs that are Both Ordinary and Extraordinary
Engineering Jobs that are Both Ordinary and Extraordinary
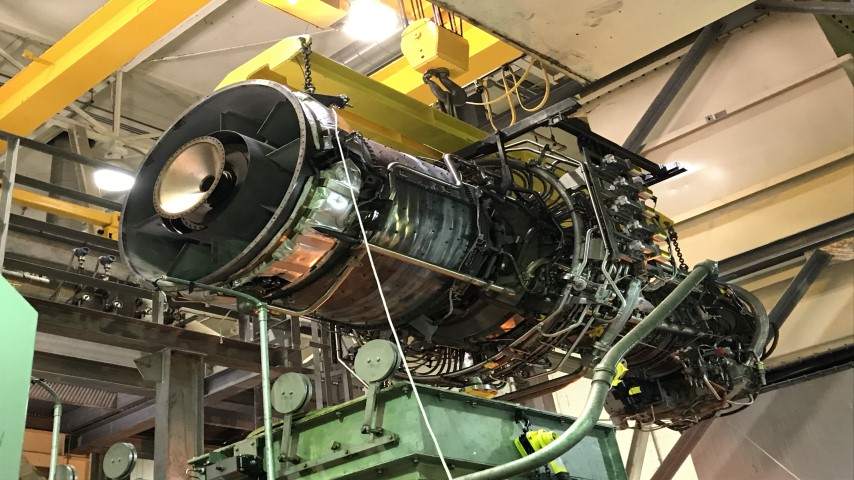
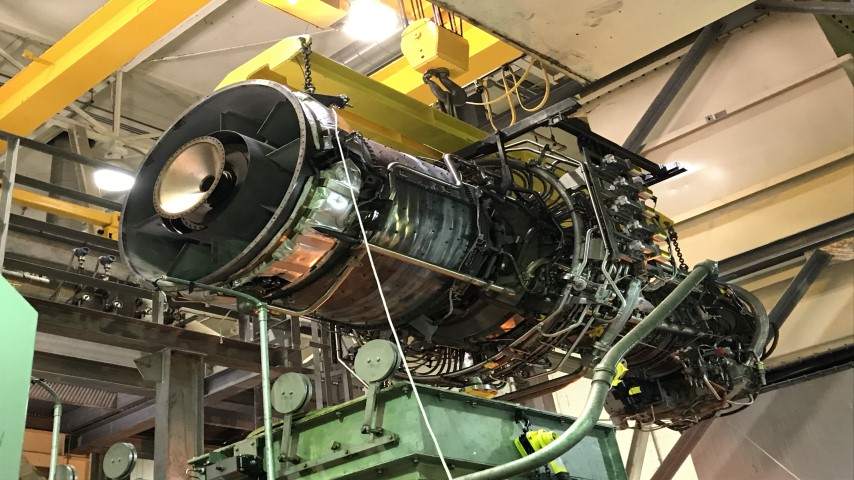
Because of their unique abilities and skills, mechanical engineers work in exclusive and often dangerous situations.
It often seems like the options available to mechanical engineers when selecting careers are endless. MEs design and develop, maintain and optimize, and because of their experience, skills, and expertise, they work in situations that many in the general public will never have a chance to see or experience.
The following are five examples of engineers going to places that few of us will ever be allowed to witness.
Watching a video on YouTube is nothing like working aboard an underground tunnel boring machine (TBM). Amid the noise of flint hitting slurry pumps, return line hydraulics, powerful electric motors, and metal gates and stairs, a three-engineer team works with miners above and below ground to drive the TBM forward, construct tunnels, and remove waste materials. The engineers are there to adjust parameters and steer the underground “factory” from the operation cabin equipment using multiple monitors that display camera views, sensor readings, and other critical information.
HS2 TBM tunneling engineers are aboard a 170-meter-long machine as it excavates a 10-mile-long tunnel. Seventeen miners work up on land and with the engineers of “Cecilia” to direct multi-service vehicles, cranes, feeders, erectors, and robots. This operation is all part of the TBM that moves rings in place that are made up of seven 8.5-ton segments. Amid the boring activity, a huge screw moves the material from the borer head (powered by 10 strong motors) to the back of the machine, where rocks and dirt mix with water. Slurry pumps then move this material out of the tunnel. Engineers also monitor the atmospheric pressure of the excavation chamber as they “drive” the machine slowly forward.
Engineers at the University of Texas Austin Carl J. Eckhardt Combined Heat and Power Plant (CHP) ensure that the plant remains capable of generating 138 MW of power (62 MW peak) and 1.2 million pounds per hour of steam safely. Most students don't have a second thought about a system that, for example, provides more than 60,000 tons of chilled water. Every day, mechanical engineers help maintain central heating and cooling for airports, universities, and healthcare complexes. Large plants, like that at Pittsburgh International Airport (PIA) generate their own power. PIA generates the energy it needs with five natural gas generators and a solar field of 10,000 panels.
The public doesn’t get the chance to step inside a power plant where engineers maintain heavy-duty machines such as boilers, turbines, pumps, compressors, and blowers. MEs follow the internal pressure and temperature of boilers via dashboards on computer screens or tablets, yet they know every remote corner or dark space of the plant they maintain. They often must climb and crawl to examine parts of heat distribution systems and can to tell you the unique noise that every pump in the plant makes. Quiet shifts are the norm as these engineers work to avoid emergencies.
Engineers who evaluate jet engineers at GE Aerospace's test site in Peebles, Ohio, get to throw chunks of dust, dirt, and ice at the monster machines. Mechanical engineers run prototype engines through their paces to make sure they can withstand real-world challenges. GE recently released information on the GE9X. It tells the tale of MEs on scaffolds using hoses and pumps to produce clouds of powder and grit and evaluates how well the engine will react when powering a Boeing 777X in desert situations.
We are talking over 12,000 hours of endurance and flight test—more than any other GE Aerospace commercial aircraft engine has undergone before entry into service. The work is in anticipation of fulfilling an order of 460 units for the United Arab Emirates. The engine is a colossal, 11 feet in diameter, and holds the world record for highest thrust—134,300 pounds. It is the most efficient wide-body engine in its thrust class. Through all the ice and water (and iterations and analysis) they make improvements that not only help ensure reliability but also establish that the engine can reach up to 10 percent lower fuel consumption than the engine that came before it, the GE90-115B.
Wind energy engineers spend their time in offices and laboratories to design and optimize wind energy systems. When they are out in the field, often in remote, windy locations, they may be in charge of a team of professionals that take care of the "farm" of turbines. According to the Office of Energy Efficiency & Renewable Energy, engineers might design and implement lifting plans for cranes, conduct transportation studies for component delivery, perform verification of the installation of turbine components, and test installation equipment. During the operational phase, engineers oversee wind technicians to complete repairs and maintenance to resolve concerns from both manufacturers and customers.
They also create quality control procedures for the installation of turbine components in coordination with the original equipment manufacturer. When issues arise, mechanical engineers may investigate the issue, troubleshoot, and identify the root cause of the problem on structures that can be as high as 350 feet. Inside the shaft of the turbine, there is a ladder that leads up to the top and offers critical access to the gearbox, blades, and rotor. It is a dizzying height, and engineers work with wind technicians who are often rock climbers and feel comfortable working with harnesses and rope since the blades can need attention after weather-related damage.
During normal operation of a nuclear power plant, engineers experience what few people ever have a chance to see—walking above a cooling tower's expansive water spray zone. All thermoelectric power plants that use heat to make steam need a way
to cool the water the system uses. With more than 250 cooling towers in the United States, engineers are the professionals that oversee the systems in these huge buildings that take warm water and cool it down.
One example of a natural draft tower is located in Raleigh, N.C., as part of Duke Energy’s Harris Nuclear Plant. The 532-foot-tall tower’s discharge pipe sends the water that falls into the basin of the tower to nearby 4,100-acre Harris Lake. The engineers ensure that valves and nozzles continually spray water into the tower’s hollow core. The process is as simple as it is endless. The “cloud” leaving the top of a cooling tower—which is often visible from miles away and can create a trail up to two miles long from taller towers—is harmless, clean water vapor.
Cathy Cecere is membership content program manager.
The following are five examples of engineers going to places that few of us will ever be allowed to witness.
Aboard a TBM
Watching a video on YouTube is nothing like working aboard an underground tunnel boring machine (TBM). Amid the noise of flint hitting slurry pumps, return line hydraulics, powerful electric motors, and metal gates and stairs, a three-engineer team works with miners above and below ground to drive the TBM forward, construct tunnels, and remove waste materials. The engineers are there to adjust parameters and steer the underground “factory” from the operation cabin equipment using multiple monitors that display camera views, sensor readings, and other critical information.
HS2 TBM tunneling engineers are aboard a 170-meter-long machine as it excavates a 10-mile-long tunnel. Seventeen miners work up on land and with the engineers of “Cecilia” to direct multi-service vehicles, cranes, feeders, erectors, and robots. This operation is all part of the TBM that moves rings in place that are made up of seven 8.5-ton segments. Amid the boring activity, a huge screw moves the material from the borer head (powered by 10 strong motors) to the back of the machine, where rocks and dirt mix with water. Slurry pumps then move this material out of the tunnel. Engineers also monitor the atmospheric pressure of the excavation chamber as they “drive” the machine slowly forward.
Heat and power plant
Engineers at the University of Texas Austin Carl J. Eckhardt Combined Heat and Power Plant (CHP) ensure that the plant remains capable of generating 138 MW of power (62 MW peak) and 1.2 million pounds per hour of steam safely. Most students don't have a second thought about a system that, for example, provides more than 60,000 tons of chilled water. Every day, mechanical engineers help maintain central heating and cooling for airports, universities, and healthcare complexes. Large plants, like that at Pittsburgh International Airport (PIA) generate their own power. PIA generates the energy it needs with five natural gas generators and a solar field of 10,000 panels.
The public doesn’t get the chance to step inside a power plant where engineers maintain heavy-duty machines such as boilers, turbines, pumps, compressors, and blowers. MEs follow the internal pressure and temperature of boilers via dashboards on computer screens or tablets, yet they know every remote corner or dark space of the plant they maintain. They often must climb and crawl to examine parts of heat distribution systems and can to tell you the unique noise that every pump in the plant makes. Quiet shifts are the norm as these engineers work to avoid emergencies.
Testing jet engines
Engineers who evaluate jet engineers at GE Aerospace's test site in Peebles, Ohio, get to throw chunks of dust, dirt, and ice at the monster machines. Mechanical engineers run prototype engines through their paces to make sure they can withstand real-world challenges. GE recently released information on the GE9X. It tells the tale of MEs on scaffolds using hoses and pumps to produce clouds of powder and grit and evaluates how well the engine will react when powering a Boeing 777X in desert situations.
We are talking over 12,000 hours of endurance and flight test—more than any other GE Aerospace commercial aircraft engine has undergone before entry into service. The work is in anticipation of fulfilling an order of 460 units for the United Arab Emirates. The engine is a colossal, 11 feet in diameter, and holds the world record for highest thrust—134,300 pounds. It is the most efficient wide-body engine in its thrust class. Through all the ice and water (and iterations and analysis) they make improvements that not only help ensure reliability but also establish that the engine can reach up to 10 percent lower fuel consumption than the engine that came before it, the GE90-115B.
Atop turbines
Wind energy engineers spend their time in offices and laboratories to design and optimize wind energy systems. When they are out in the field, often in remote, windy locations, they may be in charge of a team of professionals that take care of the "farm" of turbines. According to the Office of Energy Efficiency & Renewable Energy, engineers might design and implement lifting plans for cranes, conduct transportation studies for component delivery, perform verification of the installation of turbine components, and test installation equipment. During the operational phase, engineers oversee wind technicians to complete repairs and maintenance to resolve concerns from both manufacturers and customers.
They also create quality control procedures for the installation of turbine components in coordination with the original equipment manufacturer. When issues arise, mechanical engineers may investigate the issue, troubleshoot, and identify the root cause of the problem on structures that can be as high as 350 feet. Inside the shaft of the turbine, there is a ladder that leads up to the top and offers critical access to the gearbox, blades, and rotor. It is a dizzying height, and engineers work with wind technicians who are often rock climbers and feel comfortable working with harnesses and rope since the blades can need attention after weather-related damage.
In a cooling tower
During normal operation of a nuclear power plant, engineers experience what few people ever have a chance to see—walking above a cooling tower's expansive water spray zone. All thermoelectric power plants that use heat to make steam need a way
to cool the water the system uses. With more than 250 cooling towers in the United States, engineers are the professionals that oversee the systems in these huge buildings that take warm water and cool it down.
One example of a natural draft tower is located in Raleigh, N.C., as part of Duke Energy’s Harris Nuclear Plant. The 532-foot-tall tower’s discharge pipe sends the water that falls into the basin of the tower to nearby 4,100-acre Harris Lake. The engineers ensure that valves and nozzles continually spray water into the tower’s hollow core. The process is as simple as it is endless. The “cloud” leaving the top of a cooling tower—which is often visible from miles away and can create a trail up to two miles long from taller towers—is harmless, clean water vapor.
Cathy Cecere is membership content program manager.
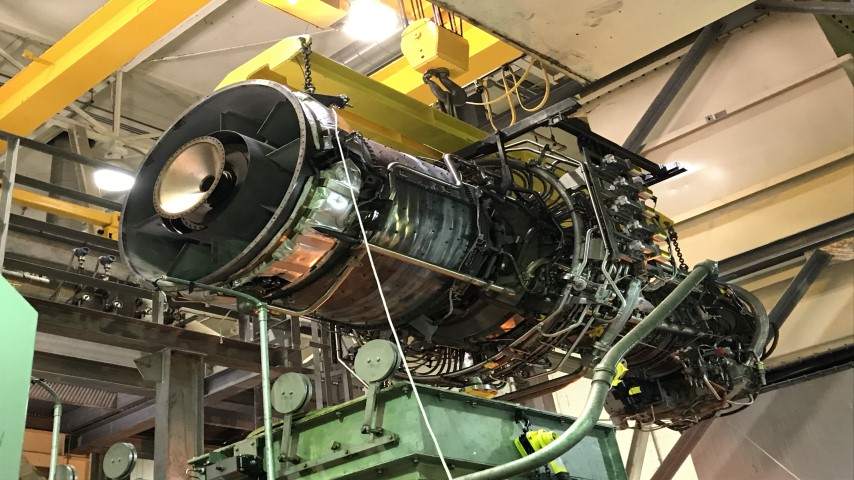
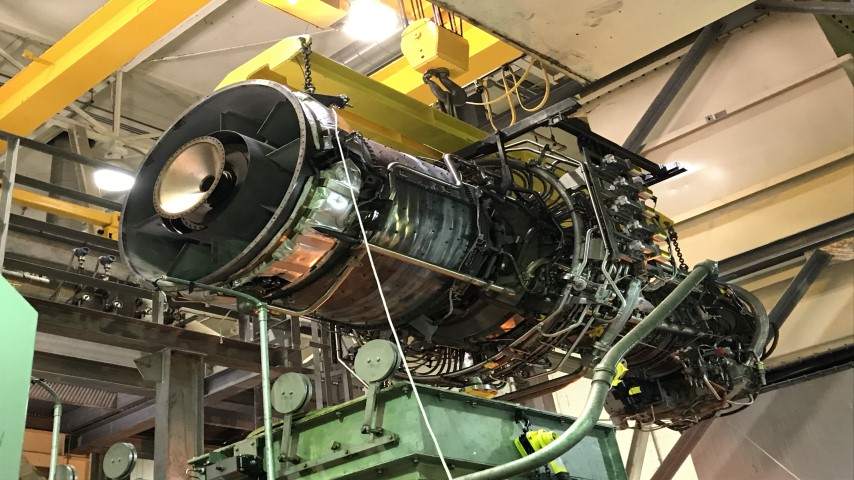