Manufacturing Blog: How the Marriage of Digital Systems is the Future of Manufacturing
Manufacturing Blog: How the Marriage of Digital Systems is the Future of Manufacturing
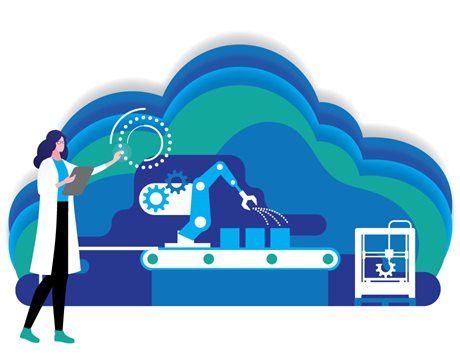
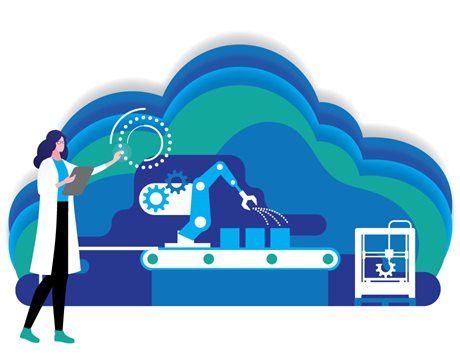
Adopting digital technology is no longer the standard in manufacturing. Organizations need to begin to merge these systems into one larger ecosystem.
If the current COVID-19 pandemic has taught those working in manufacturing anything, it is that digital manufacturing is essential to their survival. Those organizations that had Internet of Things systems and technologies in place were able to survive and even thrive during the onset of the pandemic. And the evidence is clear that companies need not only ramp up the adoption of digital manufacturing but also integrate these digital systems into a larger framework.
The latest research from the McKinsey Group points to how early adopters of IoT or Industry 4.0 technologies could ride out the early months of the pandemic and continued to perform well throughout 2020. These organizations were able to curtail supply chain disruptions and keep their manufacturing operations going.
Since 2017, the McKinsey Group has tracked the progress of 400 companies worldwide through their annual Industry 4.0 survey. The companies that have participated in the study reflect the major manufacturing hubs of the world—Asia-Pacific, Europe, and the Americas—and represent significant industries including advanced manufacturing, energy, materials, medical and pharmaceuticals, consumer tech, travel, and logistics.
Overall, 94 percent of companies responded that Industry 4.0 technologies helped them operate during the coronavirus crisis, and 56 percent said that Industry 4.0 systems were critical to their crisis response. For example, a company in Asia that focuses on consumer-packaged goods used a digital twin of its supply chain to run multiple scenarios during the pandemic and was able to prepare itself for sudden shutdowns or supply chain disruptions. Another company in North America specializing in personal protective equipment increased capacity by commissioning a new manufacturing line by using augmented reality remote assistance for project execution.
Read Our Latest Infographic: Hyperautomation—The Next Phase of Automated Systems
Within the companies surveyed by the McKinsey Group in 2020, 26 percent were unable to scale their Industry 4.0 projects successfully. McKinsey noticed a significant drop—more than 40 percent—in Industry 4.0 technologies’ maturity level compared to last year. This is below the level recorded in 2017 at the very beginning of McKinsey’s survey.
Several companies pointed to travel restrictions and remote work as the major hurdle in Industry 4.0 adoption, followed by cash and team-capacity constraints—essentially, it’s too little, too late. The research points out that the bar of Industry 4.0 adoption rose in 2020. The measure is no longer about adding value during normal business operations but instead how well digital technologies can help companies during crises, like the coronavirus pandemic.
The benchmark for progress has moved significantly. Many companies realized that they were not as far along the adoption curve as they initially thought. In the race to adopt Industry 4.0 tools, many organizations implemented information and operational technology infrastructure workarounds during initial rollouts rather than a complete and structured infrastructure improvement. In total, 56 percent of respondents who had no Industry 4.0 systems in place prior to the pandemic, found themselves limited, constrained, and unable to respond successfully to COVID-19.
Industry 4.0 has reached the point of maturity that merely having digital tools in place is not enough. Manufacturing is at the tipping point and what is crucial now is how these digital tools are integrated within the infrastructure of manufacturing.
The next phase of manufacturing is about the ecosystem of digital technologies. Gartner Research has labeled this as Hyperautomation—the idea automation rules all, and any system that can be automated should. Hyperautomation combines several advanced automated systems to create a unique ecosystem of processes. It brings together robotic process automation, intelligent business management software, artificial intelligence, machine learning, and advanced IoT analytics. AI is integrated at every level. This includes physical systems like robots and automated lines and drives data collection and business process systems.
Another advanced ecosystem merging is Industry X.0, established by Accenture. According to Accenture Labs’ recent paper Industry X.0: Get Ready for the Future of Product Engineering, Industry X.0 is “the convergence of multiple technologies—including artificial intelligence, edge intelligence, analytics and extended reality—[and] is driving a new era of manufacturing.”
The key to Industry X.0 is integrating advanced digital technologies at every step of the design and manufacturing process. The digital plant uses IoT and edge computing to connect machines, enabling networks to ‘talk’ with each other. Engineers and manufacturers become extensions of the digital design process via augmented and virtual reality equipment. AI and ML turn raw data into fundamental insight that aids every engineer’s decision, creating a more efficient workflow. Rockwell Automation has partnered with Accenture to implement Industry X.0 practices for its industrial clients.
Watch our Video: Augmented and Virtual Reality Advancements in 2021
For both Hyperautomation and Industry X.0, the goal is to create more flexible manufacturing lines and supply chains. Automation and advanced manufacturing help lift the profile of local manufacturing. Customers can turn to their local supplier for rapid part production that uses AI-driven robots and additive manufacturing. Workers are protected as automation increases by creating socially distant manufacturing environments. The supply chain becomes more diversified as more manufacturers become capable of flexible manufacturing and digital ecosystems connect more creators and manufacturers.
Ultimately, the COVID-19 pandemic has shown us that advanced digital automated ecosystems will become the future of manufacturing—and it is closer than we think.
Carlos M. González is special projects manager.
Companies Pull Ahead with Industry 4.0
The latest research from the McKinsey Group points to how early adopters of IoT or Industry 4.0 technologies could ride out the early months of the pandemic and continued to perform well throughout 2020. These organizations were able to curtail supply chain disruptions and keep their manufacturing operations going.
Since 2017, the McKinsey Group has tracked the progress of 400 companies worldwide through their annual Industry 4.0 survey. The companies that have participated in the study reflect the major manufacturing hubs of the world—Asia-Pacific, Europe, and the Americas—and represent significant industries including advanced manufacturing, energy, materials, medical and pharmaceuticals, consumer tech, travel, and logistics.
Overall, 94 percent of companies responded that Industry 4.0 technologies helped them operate during the coronavirus crisis, and 56 percent said that Industry 4.0 systems were critical to their crisis response. For example, a company in Asia that focuses on consumer-packaged goods used a digital twin of its supply chain to run multiple scenarios during the pandemic and was able to prepare itself for sudden shutdowns or supply chain disruptions. Another company in North America specializing in personal protective equipment increased capacity by commissioning a new manufacturing line by using augmented reality remote assistance for project execution.
Read Our Latest Infographic: Hyperautomation—The Next Phase of Automated Systems
Within the companies surveyed by the McKinsey Group in 2020, 26 percent were unable to scale their Industry 4.0 projects successfully. McKinsey noticed a significant drop—more than 40 percent—in Industry 4.0 technologies’ maturity level compared to last year. This is below the level recorded in 2017 at the very beginning of McKinsey’s survey.
Several companies pointed to travel restrictions and remote work as the major hurdle in Industry 4.0 adoption, followed by cash and team-capacity constraints—essentially, it’s too little, too late. The research points out that the bar of Industry 4.0 adoption rose in 2020. The measure is no longer about adding value during normal business operations but instead how well digital technologies can help companies during crises, like the coronavirus pandemic.
The benchmark for progress has moved significantly. Many companies realized that they were not as far along the adoption curve as they initially thought. In the race to adopt Industry 4.0 tools, many organizations implemented information and operational technology infrastructure workarounds during initial rollouts rather than a complete and structured infrastructure improvement. In total, 56 percent of respondents who had no Industry 4.0 systems in place prior to the pandemic, found themselves limited, constrained, and unable to respond successfully to COVID-19.
Digital Ecosystems are the Future of Manufacturing
Industry 4.0 has reached the point of maturity that merely having digital tools in place is not enough. Manufacturing is at the tipping point and what is crucial now is how these digital tools are integrated within the infrastructure of manufacturing.
The next phase of manufacturing is about the ecosystem of digital technologies. Gartner Research has labeled this as Hyperautomation—the idea automation rules all, and any system that can be automated should. Hyperautomation combines several advanced automated systems to create a unique ecosystem of processes. It brings together robotic process automation, intelligent business management software, artificial intelligence, machine learning, and advanced IoT analytics. AI is integrated at every level. This includes physical systems like robots and automated lines and drives data collection and business process systems.
Another advanced ecosystem merging is Industry X.0, established by Accenture. According to Accenture Labs’ recent paper Industry X.0: Get Ready for the Future of Product Engineering, Industry X.0 is “the convergence of multiple technologies—including artificial intelligence, edge intelligence, analytics and extended reality—[and] is driving a new era of manufacturing.”
The key to Industry X.0 is integrating advanced digital technologies at every step of the design and manufacturing process. The digital plant uses IoT and edge computing to connect machines, enabling networks to ‘talk’ with each other. Engineers and manufacturers become extensions of the digital design process via augmented and virtual reality equipment. AI and ML turn raw data into fundamental insight that aids every engineer’s decision, creating a more efficient workflow. Rockwell Automation has partnered with Accenture to implement Industry X.0 practices for its industrial clients.
Watch our Video: Augmented and Virtual Reality Advancements in 2021
For both Hyperautomation and Industry X.0, the goal is to create more flexible manufacturing lines and supply chains. Automation and advanced manufacturing help lift the profile of local manufacturing. Customers can turn to their local supplier for rapid part production that uses AI-driven robots and additive manufacturing. Workers are protected as automation increases by creating socially distant manufacturing environments. The supply chain becomes more diversified as more manufacturers become capable of flexible manufacturing and digital ecosystems connect more creators and manufacturers.
Ultimately, the COVID-19 pandemic has shown us that advanced digital automated ecosystems will become the future of manufacturing—and it is closer than we think.
Carlos M. González is special projects manager.
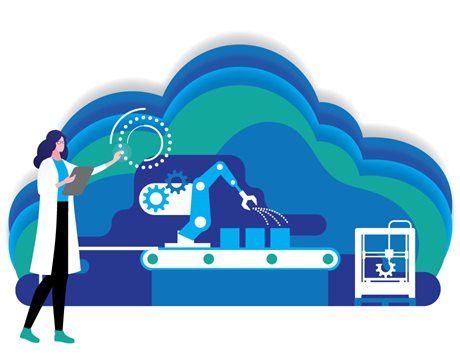
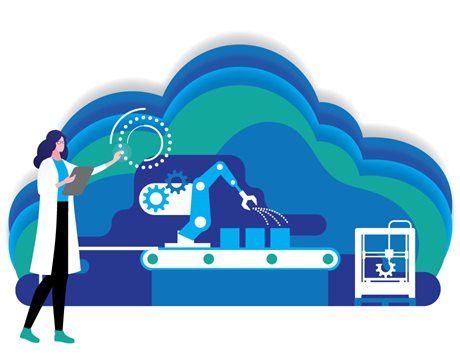